HIP Technology
Table of Contents
HIP technology or Hot Isostatic Pressing is an advanced manufacturing process to eliminate porosity, increase density, and improve mechanical properties of parts produced via additive manufacturing, casting, powder metallurgy and other techniques.
HIP technology Process
Table 1: Summary of The Hot Isostatic Pressing Process
Parameters | Details |
---|---|
Principle | High temperature + High isostatic gas/liquid pressure to consolidate part |
Process Steps | 1) Load parts into HIP container <br>2) Seal container under vacuum <br>3) Heat to treatment temperature <br> 4) Apply isostatic pressure through gas/fluid <br>5) Cool under pressure <br>6) Release pressure and unpack parts |
Typical Conditions | Pressure: 100 to 300 MPa <br> Temperature: 0.6 to 0.9 x Melting T <br> Cycle Times: 3 to 10 hours |
Effect | Porosity reduction, densification, microstructure, properties enhanced |
The combination of high heat and uniform force from all directions compacts internal pores via diffusion bonding to give fully dense, isotropic components.
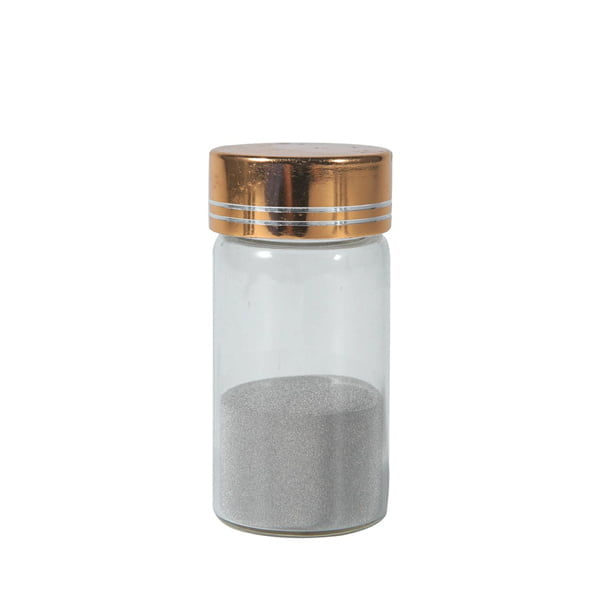
HIP technology Applications
Table 2: Applications where HIP post-treatment is vital
Application Area | Specific Uses |
---|---|
Additive Manufacturing | HIP 3D printed aerospace, dental, medical parts in Ti, CoCr, Inconels, etc for full density |
Investment Castings | HIP turbine blades, airfoils for IGT, car turbochargers to meet densification and strength specs |
Powder Metallurgy | HIP sintered connecting rods, gears, bearings to maximize consolidation and fatigue strength |
Electronics Packaging | HIP ceramic or kovar IC packages to seal lids and ensure hermeticity |
Hard Metals | HIP WC-Co cutting tools and die punches to reduce remaining porosity and cracks |
HIP finds extensive application for post-consolidation across additive, casting, P/M and ceramic manufacturing industries.
Benefits of HIP technology
Table 3: Advantages and Value Addition Due to HIP
Parameters | Benefits |
---|---|
Densification | Achieve full theoretical density; reduce defects |
Mechanical Strength | Increase tensile strength by 20% or more |
Fatigue Strength | 40-50% higher fatigue strength and life |
Fracture Toughness | 25-30% improvement in toughness possible |
Leak and Creep Resistance | Hermetic sealing improves working life |
Dimensional Precision | Size variation within 0.1%; isotropic shrinkage |
Microstructure | Refinement and homogeneity leads to consistency |
HIP expands capabilities for finished or semi-finished components across performance metrics. It is a vital complement for metal AM in industry.
Pros vs Cons
Table 4: Advantages and Limitations of HIP Technology
Pros | Cons |
---|---|
Maximizes density and eliminates porosity defects | High equipment and operation cost limits adoption |
Complex, near-net shape capability | Design compensation vital; may affect as-built tolerances |
Applicable to range of materials like metals, composites, ceramics | Large HIP vessels needed for industrial components |
Environment-friendly with gas reuse, part encapsulation | Special handling of highly pressurized gas systems required |
Despite the challenges posed due to high capital and running expenses, HIP holds future potential to become a mainstream process where consistent material quality and precision at scale matters greatly.
FAQs
Q: For which additive manufacturing metals is HIP treatment most critical?
A: Titanium and nickel alloys used in aerospace AM. Eliminating residual stresses and pores by HIPping improves the fatigue performance and surface quality expected from these printed parts in long run.
Q: Can the HIP process be used on plastic and polymer parts?
A: Challenging for regular thermoplastics as the high temperature will simply melt the plastics. Some thermosets like carbon fiber composites can experience moderate HIP responses. Speciality polymers may work under highly specific HIP conditions after careful evaluation.
Q: What are typical HIP vessel sizes for industrial applications?
A: Most common are HIP chamber diameters from 1 to 4 meters which can process industrial parts used in sectors like aerospace, automotive and general engineering. Large vessels are also being developed by HIP companies for more volume capacity.
Q: Does HIP affect the surface finish of additive manufactured components?
A: HIP can moderately improve surface roughness by offsetting warpage effects and reducing satellite particles. But finish machining post-HIP is often still required, especially for critical components used in industries like aerospace with stringent texture expectations.
Share On
MET3DP Technology Co., LTD is a leading provider of additive manufacturing solutions headquartered in Qingdao, China. Our company specializes in 3D printing equipment and high-performance metal powders for industrial applications.
Inquiry to get best price and customized Solution for your business!
Related Articles
About Met3DP
Recent Update
Our Product
CONTACT US
Any questions? Send us message now! We’ll serve your request with a whole team after receiving your message.
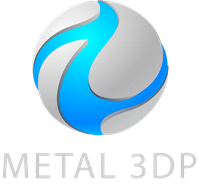
Metal Powders for 3D Printing and Additive Manufacturing