In-Situ Alloying: Revolutionizing Material Science
Table of Contents
Welcome to the fascinating world of in-situ alloying! If you’re scratching your head wondering what in-situ alloying is, don’t worry—I’ve got you covered. In this extensive guide, we’re diving deep into everything you need to know about this groundbreaking process. By the end, you’ll be an in-situ alloying aficionado!
Overview of In-Situ Alloying
In-situ alloying is a sophisticated manufacturing process where two or more different metal powders are mixed and alloyed during the manufacturing process itself, rather than combining pre-alloyed powders. This method allows for the creation of custom alloys with unique properties tailored to specific applications. Think of it like baking a cake from scratch instead of using a premade mix—you get to control every ingredient and tweak the recipe to perfection.
Why In-Situ Alloying?
Why has in-situ alloying gained so much traction in recent years? The answer lies in its numerous benefits, including the ability to produce highly customized materials with superior properties. Whether it’s creating lightweight yet strong components for aerospace or producing corrosion-resistant parts for marine applications, in-situ alloying offers unparalleled flexibility and precision.
Key Benefits of In-Situ Alloying
- Customization: Tailor the composition to meet specific needs.
- Efficiency: Combine multiple steps into one streamlined process.
- Quality: Achieve superior material properties compared to traditional methods.
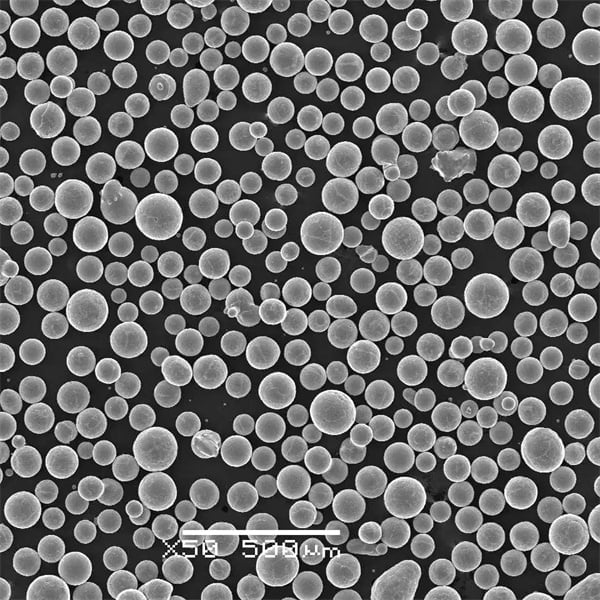
Specific Metal Powder Models in In-Situ Alloying
Now, let’s get into the nitty-gritty of metal powders used in in-situ alloying. Here’s a rundown of some specific metal powder models and their unique characteristics.
1. Aluminum (Al) Powder
- Description: Light, corrosion-resistant, and highly conductive.
- Applications: Aerospace, automotive, and electronics.
- Properties: High strength-to-weight ratio, excellent thermal and electrical conductivity.
2. Titanium (Ti) Powder
- Description: Known for its strength, lightweight, and biocompatibility.
- Applications: Medical implants, aerospace components.
- Properties: High tensile strength, corrosion resistance, biocompatibility.
3. Nickel (Ni) Powder
- Description: Excellent resistance to corrosion and high temperatures.
- Applications: Turbine blades, nuclear reactors.
- Properties: High melting point, corrosion resistance, good mechanical properties.
4. Copper (Cu) Powder
- Description: Highly conductive and malleable.
- Applications: Electrical components, heat exchangers.
- Properties: High electrical and thermal conductivity, good ductility.
5. Iron (Fe) Powder
- Description: Versatile and widely used in various industries.
- Applications: Automotive, construction, machinery.
- Properties: Good magnetic properties, strength, and ductility.
6. Stainless Steel (SS) Powder
- Description: Corrosion-resistant and strong.
- Applications: Medical devices, food processing equipment.
- Properties: High corrosion resistance, good strength, and durability.
7. Cobalt (Co) Powder
- Description: Excellent wear resistance and high-temperature stability.
- Applications: Cutting tools, aerospace engines.
- Properties: High hardness, wear resistance, thermal stability.
8. Magnesium (Mg) Powder
- Description: Extremely lightweight and strong.
- Applications: Automotive, aerospace, electronics.
- Properties: High strength-to-weight ratio, good machinability.
9. Tungsten (W) Powder
- Description: Extremely dense and heat-resistant.
- Applications: Radiation shielding, electrical contacts.
- Properties: High density, high melting point, good thermal conductivity.
10. Molybdenum (Mo) Powder
- Description: Excellent strength and stability at high temperatures.
- Applications: Furnace components, aerospace parts.
- Properties: High melting point, good thermal and electrical conductivity.
The Science Behind In-Situ Alloying
Understanding the science behind in-situ alloying requires a bit of a deep dive into material science and engineering. When different metal powders are combined and subjected to high temperatures and pressures, they form a solid solution or a new phase with distinct properties. This process can be fine-tuned to achieve the desired microstructure and properties of the final alloy.
Properties and Characteristics of In-Situ Alloys
The properties of in-situ alloys depend on the specific metal powders used and the processing conditions. Here’s a handy table summarizing the properties of some common in-situ alloys:
Metal Powder | Composition | Properties | Characteristics |
---|---|---|---|
Aluminum (Al) | Pure Al or Al alloys | High strength-to-weight ratio, conductivity | Lightweight, corrosion-resistant |
Titanium (Ti) | Pure Ti or Ti alloys | High tensile strength, biocompatibility | Strong, lightweight, corrosion-resistant |
Nickel (Ni) | Pure Ni or Ni alloys | High melting point, corrosion resistance | Durable, high-temperature stability |
Copper (Cu) | Pure Cu or Cu alloys | High electrical and thermal conductivity | Malleable, conductive |
Iron (Fe) | Pure Fe or Fe alloys | Good magnetic properties, strength | Versatile, strong |
Stainless Steel (SS) | Various SS grades | Corrosion resistance, durability | Strong, corrosion-resistant |
Cobalt (Co) | Pure Co or Co alloys | High hardness, thermal stability | Wear-resistant, heat-stable |
Magnesium (Mg) | Pure Mg or Mg alloys | High strength-to-weight ratio, machinability | Lightweight, strong |
Tungsten (W) | Pure W or W alloys | High density, thermal conductivity | Dense, heat-resistant |
Molybdenum (Mo) | Pure Mo or Mo alloys | High melting point, conductivity | Heat-resistant, conductive |
Applications of In-Situ Alloying
In-situ alloying is used across various industries, from aerospace to medical devices. Here are some of the key applications:
Application | Description | Examples |
---|---|---|
Aerospace | Lightweight, strong components | Turbine blades, structural parts |
Automotive | High-strength, lightweight materials | Engine parts, chassis components |
Medical Devices | Biocompatible, corrosion-resistant materials | Implants, surgical tools |
Electronics | Conductive, heat-resistant materials | Circuit boards, connectors |
Construction | Durable, strong materials | Structural components, tools |
Energy | Heat-resistant, conductive materials | Turbine components, reactors |
Tooling | Hard, wear-resistant materials | Cutting tools, molds |
Marine | Corrosion-resistant, durable materials | Ship components, offshore structures |
Specifications, Sizes, Grades, Standards
When it comes to specifications, sizes, grades, and standards, in-situ alloying materials are highly varied. Here’s a table detailing some of these aspects for a few common alloys:
Metal Powder | Specifications | Sizes | Grades | Standards |
---|---|---|---|---|
Aluminum (Al) | ASTM B221, ASTM B483 | Various diameters | 1100, 2024, 6061 | ASTM, ISO, SAE |
Titanium (Ti) | ASTM B348, ASTM F67 | Rods, sheets, wires | Grade 1-5, 23 | ASTM, ISO, AMS |
Nickel (Ni) | ASTM B160, ASTM B161 | Various diameters | 200, 201, 400 | ASTM, SAE, AMS |
Copper (Cu) | ASTM B187, ASTM B152 | Sheets, rods, wires | C10100, C11000, C12200 | ASTM, SAE, EN |
Iron (Fe) | ASTM A36, ASTM A123 | Various forms | Various steel grades | ASTM, ISO, SAE |
Stainless Steel (SS) | ASTM A276, ASTM A240 | Rods, sheets, tubes | 304, 316, 410 | ASTM, SAE, ISO |
Cobalt (Co) | ASTM F75, ASTM F1537 | Powder, rods | F75, F799, F1537 | ASTM, ISO |
Magnesium (Mg) | ASTM B107, ASTM B91 | Sheets, rods, tubes | AZ31B, AZ91D, WE43 | ASTM, SAE, ISO |
Tungsten (W) | ASTM B760, ASTM B777 | Rods, sheets | W1, W2, WHA | ASTM, MIL |
Molybdenum (Mo) | ASTM B386, ASTM B387 | Rods, sheets, wires | Mo1, Mo2 | ASTM, ISO |
Suppliers and Pricing Details
Finding the right supplier for in-situ alloying materials can be crucial for your project’s success. Here’s a list of some reputable suppliers along with a rough idea of pricing:
Supplier | Materials Supplied | Price Range (per kg) | Contact Details |
---|---|---|---|
Metal Powder Company | Stainless Steel, Copper, Iron | $30 – $150 | www.metalpowdercompany.com |
Alloy Innovations | Titanium, Nickel, Cobalt | $80 – $300 | www.alloyinnovations.com |
Precision Alloys Inc. | Aluminum, Magnesium, Tungsten | $50 – $250 | www.precisionalloysinc.com |
Tech Metals Corporation | Nickel, Copper, Stainless Steel | $40 – $200 | www.techmetalscorp.com |
Global Alloy Solutions | Cobalt, Titanium, Molybdenum | $100 – $400 | www.globalalloysolutions.com |
Comparing Pros and Cons of In-Situ Alloying
Let’s weigh the advantages and limitations of in-situ alloying to give you a clear picture:
Advantages | Limitations |
---|---|
Highly customizable alloys | Requires precise control over processing conditions |
Enhanced material properties | Initial setup costs can be higher |
Streamlined manufacturing process | Complexity in alloy design |
Reduced material waste | Limited to certain compositions |
Cost-effective for small batch production | Potential for intermetallic phases |
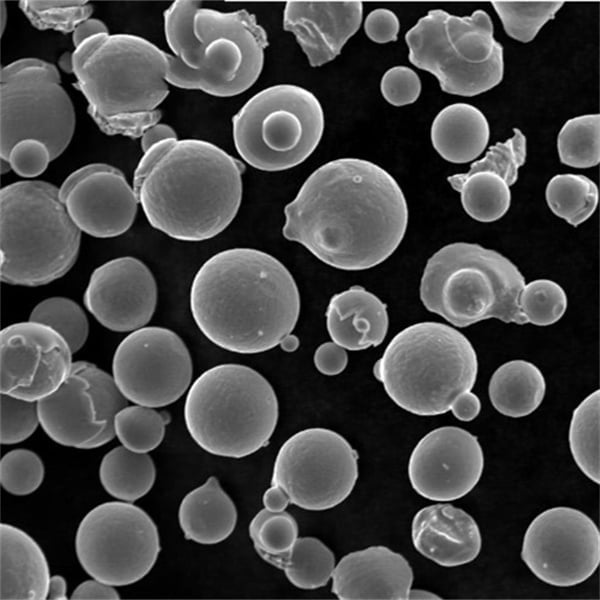
FAQs
Here are some common questions answered concisely to help you understand in-situ alloying better:
Question | Answer |
---|---|
What is in-situ alloying? | In-situ alloying is a manufacturing process where different metal powders are mixed during production to create alloys. |
What are the advantages of in-situ alloying? | It allows for custom alloys, better material properties, and reduced waste. |
Where is in-situ alloying used? | It’s used in aerospace, automotive, medical, and other industries requiring specialized materials. |
How does in-situ alloying compare to traditional methods? | It offers more flexibility and precise control over alloy composition compared to pre-alloyed materials. |
What are the challenges of in-situ alloying? | It requires expertise to control alloy composition and may have higher initial setup costs. |
Conclusion
In conclusion, in-situ alloying is a game-changer in material science, offering unparalleled flexibility and precision in creating customized alloys with superior properties. Whether you’re in aerospace, automotive, or medical industries, understanding the nuances of in-situ alloying can lead to innovative advancements and cost-effective solutions. With the right knowledge and materials, the possibilities are endless!
Now that you’ve explored the world of in-situ alloying, feel free to delve deeper into specific applications or reach out to suppliers to kickstart your next project. Remember, the key lies in harnessing the power of metals to transform ideas into reality.
Share On
MET3DP Technology Co., LTD is a leading provider of additive manufacturing solutions headquartered in Qingdao, China. Our company specializes in 3D printing equipment and high-performance metal powders for industrial applications.
Inquiry to get best price and customized Solution for your business!
Related Articles
About Met3DP
Recent Update
Our Product
CONTACT US
Any questions? Send us message now! We’ll serve your request with a whole team after receiving your message.
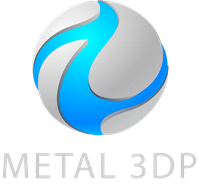
Metal Powders for 3D Printing and Additive Manufacturing