Inconel 625 Powder
Table of Contents
Inconel 625 is a nickel-chromium-molybdenum alloy with excellent corrosion and high temperature resistance. This guide provides an in-depth look at Inconel 625 powder for additive manufacturing and other powder metallurgy applications.
Overview of Inconel 625 Powder
Inconel 625 powder is made of a nickel-chromium-molybdenum alloy with additions of niobium, iron, titanium and aluminum. Here are its key characteristics:
Property | Details |
---|---|
Composition | Nickel-chromium-molybdenum alloy |
Nickel Content | 58-63% |
Density | 8.4 g/cm3 |
Melting Point | 1260-1350°C |
Color | Gray metallic |
Key properties like strength, corrosion resistance, and weldability make Inconel 625 suitable for demanding applications.
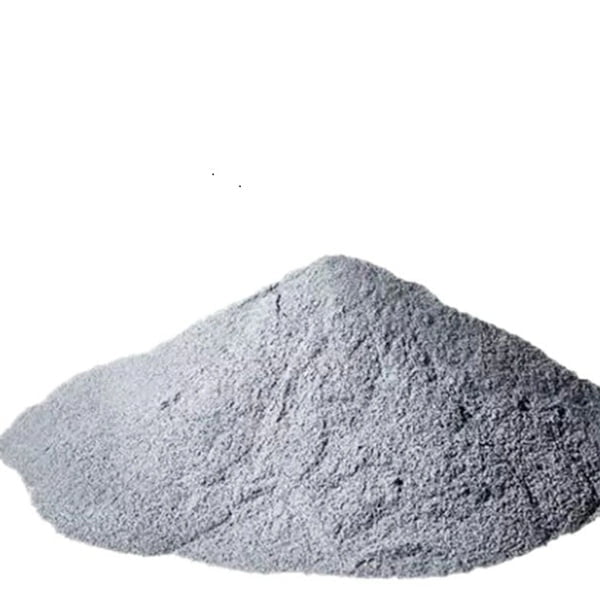
Production Methods
Common techniques to produce Inconel 625 powder include:
- Gas Atomization – High pressure inert gas disintegrates molten Inconel 625 into fine droplets that solidify into powder. This produces spherical powders ideal for additive manufacturing.
- Plasma Rotating Electrode Process (PREP) – Electrode of Inconel 625 is melted using a plasma arc and spun at high speeds to disperse molten material into powder using centrifugal force.
- Water Atomization – Similar to gas atomization but water is used instead of gas to break up the molten metal stream into fine particles.
- Mechanical Alloying – Elemental metal powders are blended and ball milled to synthesize Inconel 625 alloy powder through powder mixing.
Proper control of the process parameters results in powder with flowability, packing density and microstructure suitable for the intended application.
Powder Characteristics
Inconel 625 powder can be customized in terms of:
Characteristic | Details |
---|---|
Particle size distribution | Commonly 10-45 microns |
Particle morphology | Spherical, granular or irregular |
Apparent density | Typically 3-5 g/cc |
Flow rate | Measured in s/50g, typically 20-30 s/50g |
Oxygen content | <300 ppm oxygen content |
The powder characteristics dictate performance in additive manufacturing or other powder consolidation processes.
Applications of Inconel 625 Powder
Key application areas for Inconel 625 powder include:
- Aerospace – Turbine engine components, rocket motor casings, valves and pumps for corrosive propellants.
- Oil and Gas – Downhole tools, wellhead valves, subsea components exposed to corrosive well fluids.
- Chemical Processing – Heat exchangers, reaction vessels, pipe fittings handling corrosive chemicals.
- Medical – Dental implants, prosthetics, surgical instruments requiring biocompatibility.
- Automotive – Valve parts, fuel system components, turbocharger rotors.
- Additive Manufacturing – Complex metal parts exposed to high temperatures and corrosive atmospheres.
Its strength and corrosion resistance make Inconel 625 suitable for demanding applications across industries.
Specifications and Standards
Key standards for Inconel 625 powder:
- ASTM B214 – Standard specification for Ni-Cr-Mo-Cb alloy powder and products
- AMS 5666 – Nickel alloy powder and consolidated material specification
- ASME SB214 – Ni-Cr-Mo-Cb alloy pipe specification
- AMS 5837 – Specification for additive manufacturing nickel alloy
- ISO 21809-2 – Specification for Ni-Cr-Mo alloy for additive manufacturing
Chemistry, mechanical properties, microstructure requirements are outlined for quality control.
Printing Parameters for Inconel 625
Typical Inconel 625 printing parameters:
Parameter | Range |
---|---|
Layer thickness | 20-100 microns |
Laser power | 195-350 W |
Scan speed | 700-850 mm/s |
Hatch spacing | 0.1-0.17 mm |
Beam size | 50-150 μm |
These parameters are optimized based on part geometry, build time, and desired material properties.
Post-Processing
Common post-processing steps for Inconel 625 parts:
- Stress Relief – Annealing heat treatment to relieve residual stresses and prevent distortion/cracking.
- Surface Machining – CNC machining to achieve dimensional accuracy and good surface finish.
- Hot Isostatic Pressing – Eliminates internal voids and porosity by applying high pressure at elevated temperatures.
- Heat Treatment – Solution annealing and aging to enhance strength and hardness.
- Surface Treatments – Electroplating, anodizing, or powder coating may be applied for corrosion protection and wear resistance.
Proper post-processing is vital to achieve the required material performance.
Mechanical Properties
Inconel 625 properties:
Property | Value |
---|---|
Density | 8.4 g/cm3 |
Ultimate Tensile Strength | 1025 MPa |
Yield Strength | 550 MPa |
Elongation | 35% |
Hardness | 35 HRC |
Properties depend on build parameters and post-processing treatments applied. Values approach wrought Inconel 625.
Applications of Printed Inconel 625 Parts
Industry applications of additively manufactured Inconel 625 components:
Aerospace
- Combustor liners, engine blades – high temperature resistance
Oil and Gas
- Valves, pumps for corrosive drilling fluids
Marine
- Pump impellers, propeller shafts – corrosion resistance
Medicine
- Dental crowns, implants – biocompatibility
Automotive
- Turbocharger rotors, fuel system parts – high temperature strength
3D printing enables complex Inconel 625 parts with significant lead time and cost savings versus machining.
Global Suppliers
Leading global suppliers of Inconel 625 powder include:
Company | Location |
---|---|
Sandvik Osprey | UK |
Praxair | USA |
Carpenter Additive | USA |
AP&C | Canada |
Erasteel | Sweden |
These companies can supply Inconel 625 powder tailored for additive manufacturing and other metallurgy applications.
Cost Analysis
Inconel 625 powder costs around $50-100/kg. Cost depends on:
- Purity levels
- Particle size distribution
- Powder morphology – spherical is costlier
- Purchase volumes
- Additional powder characterization testing
Economies of scale apply for bulk orders of over 100kg.
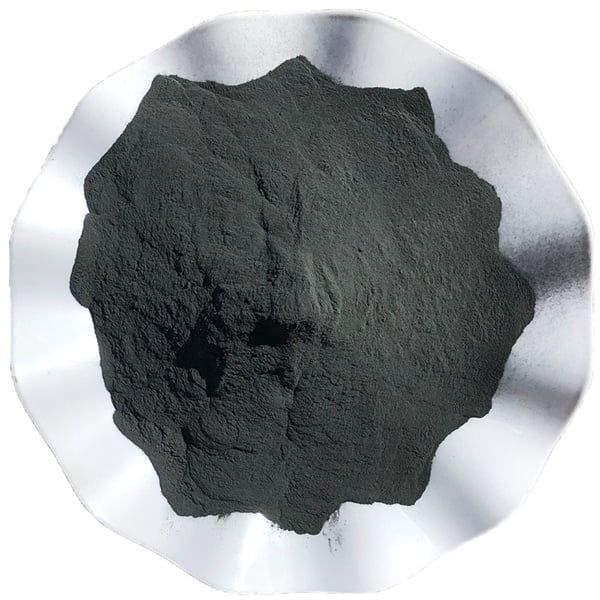
Choosing a Reliable Supplier
Here are key factors when selecting an Inconel 625 powder supplier:
- Technical expertise in nickel alloy powder manufacture
- Quality management certifications like ISO 9001
- Testing capabilities for powder characterization
- Range of purities and particle size distributions
- Lot traceability and consistent quality
- Competitive pricing and minimum order quantities
- Quick turnaround on small/prototype orders
- Reputation for product quality and service
Choosing an established supplier reduces risks and ensures optimal powder quality.
Storage and Handling
Best practices for Inconel 625 powder storage:
- Store sealed containers in a cool, dry area away from moisture
- Use inert gas purging when storing opened powder
- Avoid accumulation of oxygen, which degrades the powder over time
- Follow safety precautions – nickel powder may be flammable
- Refer to manufacturer’s Safety Data Sheet for proper handling
Proper storage maximizes the shelf life and preserves the powder characteristics.
Advantages of Inconel 625 Powder
- Withstands high temperatures up to 1000°C
- Excellent corrosion resistance in acidic and marine environments
- Good weldability using conventional welding methods
- Retains strength after prolonged exposure to elevated temperatures
- More fabricable than other nickel alloys
- Can be thermally sprayed onto metal substrates
- Can be hot-formed using powder forging techniques
- Used for cladding other metals to provide corrosion protection
Inconel 625 delivers performance advantages making it the material of choice for harsh conditions across industries.
Limitations and Disadvantages
- Less strong compared to other superalloys like Waspaloy or Hastelloy
- Subject to corrosion in alkaline environments and chloride solutions
- Requires controlled atmosphere during heat treatment and welding
- Difficult to cut and machine – abrasive-based methods required
- Relatively heavy compared to aluminum or titanium alloys
- More expensive than carbon steels and stainless steels
- Limited high temperature creep rupture strength
Inconel 625 has some drawbacks that must be designed around for high performance applications.
Health and Safety Considerations
Key health and safety notes when handling Inconel 625 powder:
- Contains nickel which can cause skin sensitization through contact
- Eye and respiratory tract irritant especially at fine particle sizes
- As a combustible metal, it presents fire and explosion risks
- Follow recommended precautions in the Safety Data Sheet
- Use appropriate PPE – gloves, goggles, respirator mask
- Avoid inhalation and ingestion of particles
- Ensure proper ventilation and point-of-use dust collection
- Inert gas storage is recommended to prevent oxidation
Applying sound safety practices when using Inconel 625 powder is important.
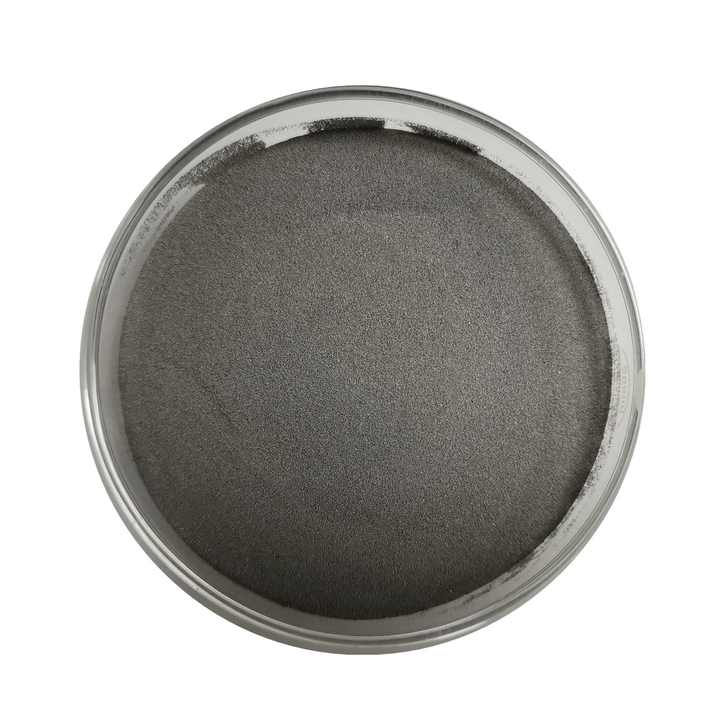
FAQs
Question | Answer |
---|---|
What is Inconel 625 used for? | Aerospace, oil and gas, chemical processing, automotive applications needing corrosion resistance. |
What is the difference between Inconel 625 and 718? | Inconel 718 offers higher tensile strength while 625 provides better corrosion resistance. |
What is the typical size of Inconel 625 powder? | 10-45 microns for additive manufacturing, but sizes up to 150 microns are available. |
What are the contents of Inconel 625 alloy? | Nickel, chromium, molybdenum, niobium, iron, titanium and aluminum. |
Does Inconel 625 require heat treatment? | Solution annealing and aging can be done to enhance strength and ductility. |
Conclusion
Inconel 625 powder provides an exceptional combination of high temperature strength, corrosion resistance, and fabricability for demanding applications across aerospace, oil and gas, chemical processing, and other industries. Advances in additive manufacturing are enabling Inconel 625 to be used in complex component designs not possible with traditional methods. With proper handling and processing, Inconel 625 powder can enable high-performance metal parts for next-generation technologies.
Share On
MET3DP Technology Co., LTD is a leading provider of additive manufacturing solutions headquartered in Qingdao, China. Our company specializes in 3D printing equipment and high-performance metal powders for industrial applications.
Inquiry to get best price and customized Solution for your business!
Related Articles
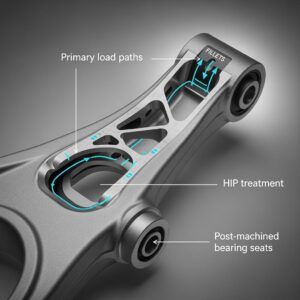
Metal 3D Printing for U.S. Automotive Lightweight Structural Brackets and Suspension Components
Read More »About Met3DP
Recent Update
Our Product
CONTACT US
Any questions? Send us message now! We’ll serve your request with a whole team after receiving your message.