Inconel Powder
Table of Contents
Inconel powder refers to nickel-chromium-based superalloys that are corrosion and heat resistant. This guide provides a comprehensive overview of inconel powder, its properties, applications, specifications, pricing, and more.
Overview of Inconel Powder
Inconel is a family of nickel-chromium-based superalloys known for their strength, heat resistance, and corrosion resistance properties. Inconel powders are used across industries like aerospace, oil and gas, chemical processing, power generation, and more.
Some key properties and characteristics of inconel powder:
Composition
Type | Nickel Content | Chromium Content | Iron Content | Other Alloying Elements |
---|---|---|---|---|
Inconel 600 | 72% | 14-17% | 6-10% | Cobalt, carbon |
Inconel 625 | 58% min | 20-23% | 5% max | Molybdenum, niobium |
Inconel 718 | 50-55% | 17-21% | Balance | Niobium, molybdenum, aluminium, titanium |
High Temperature Strength – Retains strength and resist creep deformation up to 700°C. Specific grades can withstand even higher temperatures exceeding 1000°C.
Oxidation and Corrosion Resistance – Forms protective chromia layer making it resistant to pitting and corrosion by acids, salts etc.
Easy Weldability and Machinability – Readily fabricated and machined into complex shapes. Requires post-weld heat treatment.
High Fatigue Strength – Withstand repeated stress cycles without failure making it suitable for dynamic load-bearing applications.
Compare the properties of common inconel powder grades:
Properties | Inconel 600 | Inconel 625 | Inconel 718 |
---|---|---|---|
Melting Point | 1350-1413°C | 1260-1350°C | 1260-1336°C |
Density | 8.47 g/cm3 | 8.44 g/cm3 | 8.19 g/cm3 |
Tensile Strength | 485-860 MPa | 760 MPa | 1275 MPa |
Elongation | 30-35% | 35% | 19% |
Thermal Expansion | 16.0×10−6/°C | 13.0×10−6/°C | 13.0×10−6/°C |
Thermal Conductivity | 9.8-10.4 W/m.K | 9.8 W/m.K | 11.4 W/m.K |
Table 1: Comparison of key inconel grades
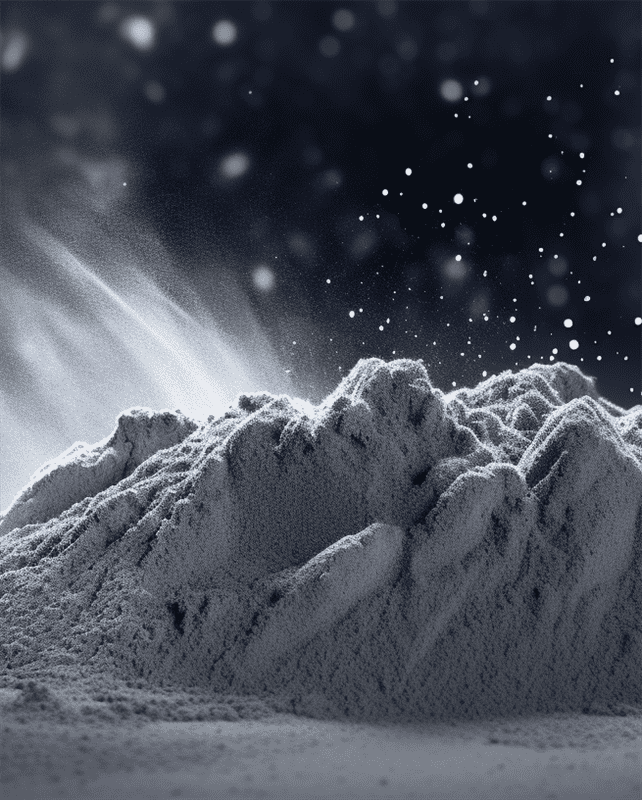
Applications of Inconel Powder
Thanks to its unique material properties, inconel finds extensive use across industries like:
Industry | Applications | Powder Products Used |
---|---|---|
Aerospace | Turbocharger exhaust cases, thrust reverser systems, turbine blades | Inconel 718, Inconel 625 |
Oil and Gas | Wellhead systems, rupture discs, downhole tools | Inconel 718, Inconel 625, Inconel 600 |
Chemical Processing | Heat exchangers, reaction vessels, conveyor components | Inconel 600, Inconel 625 |
Power Generation | Heat exchanger tubing, coal gasification systems | Inconel 617, Inconel 625, Inconel 740 |
Automotive | Valve components, exhaust gas recirculation systems | Inconel 718, Inconel 600 |
Key Applications of Inconel Powder:
- High temperature strength allows use in gas turbine blades, rocket motor casings, nuclear fuel cladding etc.
- Corrosion resistance enables use in acid production systems, sea water applications etc.
- Oxidation resistance makes it suitable for aircraft exhaust systems, industrial furnace components etc.
- Easy fabrication into complex shapes through 3D printing or other methods.
Industry Trends Driving Adoption:
- Aerospace sector growth leading to increasing use in aeroengine components.
- Demand from chemical plants, oil refineries, LNG carriers due to high temperature and pressure needs.
- Growth in metal additive manufacturing for prototyping and production applications.
Table 2: Overview of inconel powder applications by industry
Inconel Powder Specifications
Inconel powder is available in various size ranges, shapes, and compositions to suit different applications:
Size Range | Common Shape | Typical Uses |
---|---|---|
15-45 microns | Spheroidal | Metal injection molding feedstock |
45-106 microns | Irregular, spherical | Additive manufacturing, HIP applications |
150-250 microns | Spherical, agglomerated | Thermal spray coatings |
-140/+325 mesh | Irregular | Press and sinter process |
Based on application needs, users can choose from ASTM, ASME, AWS, AMS, UNS, etc. grade specifications:
Specification | Common Grades |
---|---|
ASTM B168 | Inconel 600, Inconel 601, Inconel 625, Inconel 718, Inconel X-750 |
ASME SB443 | Inconel 82, Inconel 625, Inconel 718 |
AWS A5.14 | Inconel 52, Inconel 152, Inconel 625 |
AMS Specs | Inconel 718 (AMS 5662), Inconel X-750 (AMS 5754) |
Table 3: Overview of common inconel powder specifications
Characteristics Evaluated as per Standards
- Chemical composition – Ni, Cr, Fe, Nb, Ti, Al contents
- Particle size distribution, flow rates
- Microstructure – Gamma prime content, grain size
- Impurity levels – C, S, Si, Mn
- Mechanical properties – hardness, tensile and yield strength
Choosing the right specification grade ensures the powder meets design needs.
Suppliers and Pricing
Most nickel and superalloy powder manufacturers supply various inconel grades. Buyers can select suppliers based on factors like:
- Capability to manufacture different compositions and particle size distributions
- Quality certifications – AS9100, ISO 9001
- Customization options – ability to tailor powders
- Production capacity, lead times, minimum order quantities
Indicative Pricing Range
Inconel Grade | Price Per Kg |
---|---|
Inconel 600 | $50 – $120 |
Inconel 625 | $50 – $150 |
Inconel 718 | $80 – $220 |
Prices vary based on:
- Purity levels, impurity limits
- Particle shape and size distribution
- Purchase volumes and production process used
- Level of customization for properties
Leading Inconel Powder Manufacturers
Company | Locations | Grades Offered |
---|---|---|
Sandvik | Europe, Asia | Inconel 718, Inconel 625 |
Praxair | US | Inconel 600, Inconel 625, Inconel 718 |
Hoganas | Europe | Inconel 718 |
Carpenter Technology | US | Inconel 600, Inconel 718 |
Erasteel | Europe | Inconel 718 |
Table 4: Indicative pricing range and major inconel powder suppliers
Pros and Cons of Inconel Powder
Advantages
- Extreme temperature resistance – can operate up to 1000°C
- Withstands thermal fatigue and dynamic loads without failure
- High corrosion and oxidation resistance protects surface
- Tailorable mechanical properties by adjusting composition
- Easy to fabricate into complex shapes
Limitations
- Very expensive compared to steel, titanium alloys
- Lower thermal conductivity than aluminium, copper
- Susceptible to grain boundary cracking if improperly processed
- Difficult to fully recycle and reuse after service life
- Requires post-weld heat treatment for optimal properties
Carefully weigh the unique performance benefits with higher costs compared to alternatives when choosing inconel.
Comparison to Key Alternatives
How does inconel fare compared against other high temperature alloys?
Parameter | Inconel | Stainless Steel | Hastelloy | Haynes Alloys |
---|---|---|---|---|
Oxidation Resistance | Excellent | Moderate | Excellent | Excellent |
Corrosion Resistance | Excellent | Good | Excellent | Excellent |
Thermal Conductivity | Moderate | Low | Low | Moderate |
Thermal Expansion | Low | High | Moderate | Moderate |
Common Applications | Aerospace, oil and gas | Industrial equipment | Chemical processing | Aerospace |
Key Takeaways
- Inconel offers the best high temperature performance but at very high cost
- Stainless steel is cheaper but has much lower temperature limits
- Hastelloy and Haynes alloys rival inconel but have higher material costs
- Consider actual operating conditions, cost constraints before choosing
Carefully evaluate application needs before paying the price premium for inconel over other alternatives.
Table 5: Comparison of key properties between inconel and alternative alloys
FAQ
Q: What is inconel powder used for?
A: Inconel powder is used to manufacture high performance components for extreme environments in aerospace, oil and gas, chemical processing and power generation requiring good mechanical strength and corrosion resistance at high temperatures above 1000°C.
Q: What is the difference between inconel 600, 625 and 718?
A: The main differences are – Inconel 600 offers the best high temperature corrosion resistance but lower strength, while Inconel 718 provides the highest strength but lower oxidation and chemical resistance compared to Inconel 625 which provides the best balanced properties.
Q: Does inconel contain nickel?
A: Yes, inconel is a nickel-chromium-iron based superalloy. Most inconel grades have at least 50% nickel along with 14-23% chromium which gives inconel its excellent high temperature performance.
Q: What powder size is used in additive manufacturing?
A: Inconel powders ranging from 15 microns to 150 microns with spherical morphology are commonly used in laser powder bed fusion, direct energy deposition additive manufacturing processes used to produce metal components across industries.
Q: Is inconel hazardous?
A: Inconel powders are generally considered non-hazardous and safe for handling with standard protective equipment. However, the fine nickel and chromium components pose irritation issues and it is recommended to take precautions and prevent excessive skin contact or inhalation.
Share On
MET3DP Technology Co., LTD is a leading provider of additive manufacturing solutions headquartered in Qingdao, China. Our company specializes in 3D printing equipment and high-performance metal powders for industrial applications.
Inquiry to get best price and customized Solution for your business!
Related Articles
About Met3DP
Recent Update
Our Product
CONTACT US
Any questions? Send us message now! We’ll serve your request with a whole team after receiving your message.
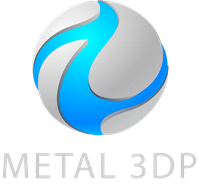
Metal Powders for 3D Printing and Additive Manufacturing