Introduction to Metal Powders
Table of Contents
Metal powders are fine metal particles used in various manufacturing processes to create metal parts and products. This article provides an in-depth guide on metal powders covering their key properties, production methods, applications, suppliers, costs, and more.
Overview of Metal Powders
Metal powders are composed of fine particles of metal materials that can be used to manufacture dense and intricate parts for a variety of industries. Here is a brief overview:
Metal Powder Properties
- Particle size range: 1 micron to 1000 microns
- Morphology: Spherical, irregular, flakes, fibers
- Common materials: Iron, copper, aluminum, titanium, nickel, cobalt
- Key characteristics: Flowability, compactability, sinterability
Production Methods
- Atomization
- Electrolysis
- Carbonyl decomposition
- Milling
Main Applications
- Powder metallurgy
- Metal injection molding
- Additive manufacturing
- Welding
- Brazing and soldering
Suppliers and Costs
- Major global suppliers
- Cost depends on material, purity, production method
- Range from $5/kg to $500/kg
Advantages Over Wrought Metal
- Intricate and complex shapes
- High dimensional precision
- Near net-shape fabrication
- Novel material properties
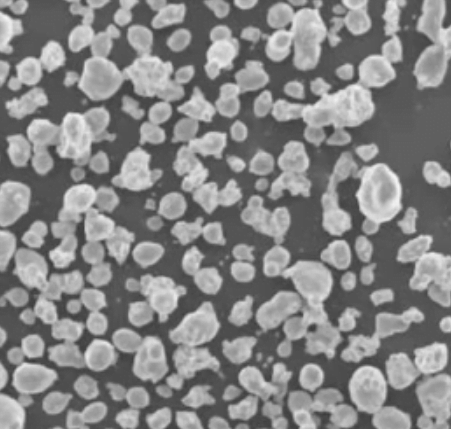
Types of Metal Powders
There are various ways to categorize metal powders based on composition, production method, morphology, and particle size.
Table 1: Metal Powder Types
Type | Characteristics | Common Materials | Typical Size Range |
---|---|---|---|
Elemental | Single metal, high purity | Iron, copper, nickel, cobalt | 1-150 microns |
Alloys | Mixtures of metals | Stainless steels, tool steels, superalloys | 10-1000 microns |
Composites | Mixtures with other powders | WC-Co, Cu-Diamond | 1-500 microns |
By Production Method | Unique size and morphology based on production process | See next section | Depends on process |
Spherical | Smooth, rounded particles | Gas or water atomization | 5-150 microns |
Irregular | Jagged, uneven shapes | Mechanical comminution | 1-1000 microns |
The choice of metal powder type depends on the specific application and desired final properties. The powder metallurgy process allows a wide range of combinations.
Production Methods for Metal Powders
There are several well-established production methods, each resulting in powders with unique characteristics optimized for certain applications:
Table 2: Metal Powder Production Methods
Method | Process Description | Particle Morphology | Typical Size Range |
---|---|---|---|
Gas Atomization | Molten metal stream disintegrated by high pressure gas jets | Highly spherical | 5-150 microns |
Water Atomization | Uses water stream instead of gas | Irregular shapes | 10-300 microns |
Electrolysis | Metal ions in solution deposited at cathode | Dendritic, spiky | 1-100 microns |
Carbonyl Decomposition | Thermal decomposition of volatile metal carbonyls | Spherical, smooth | 1-10 microns |
Mechanical Milling | Ball mills or attritors used to comminute metal particles | Flattened, irregular | 1-300 microns |
Each process results in powders suited for certain applications depending on their characteristics. For example, gas atomized powders with smooth, spherical particles allow excellent packing density and sinterability. While mechanically milled particles provide higher green strength.
Applications of Metal Powders
The major applications taking advantage of the unique properties of metal powders include:
Table 3: Metal Powder Applications
Application | Description | Typical Materials Used |
---|---|---|
Powder Metallurgy | Press and sinter process to create net shape parts | Iron, steel, copper, aluminum |
Metal Injection Molding | Mix powders with binders, inject into molds | Stainless steels, tool steels, tungsten heavy alloys |
Additive Manufacturing | 3D printing of complex parts from metal powders | Titanium alloys, cobalt chrome, nickel superalloys |
Welding | Deposition of metal powders in welding zone | Stainless steel, nickel, cobalt alloys |
Brazing and Soldering | Bonding of metal joints using powder interlayers | Silver, copper, aluminum alloys |
The flexibility of properties achieved through different powder compositions and post-processing allows metal powders to be adapted to these critical manufacturing industries.
Global Suppliers of Metal Powders
There are a number of large global suppliers as well as smaller regional powder producers:
Table 4: Major Metal Powder Companies
Company | Headquarters | Materials Offered |
---|---|---|
Höganäs | Sweden | Iron, steel, alloy steels |
GKN | UK | Stainless steels, tool steels, superalloys |
Sandvik | Sweden | Stainless steels, high alloy steels, titanium alloys |
Praxair (Carpenter Powder) | USA | Tool steels, stainless steels, superalloys |
Rio Tinto Metal Powders | Canada | Aluminum, aluminum alloys, iron |
In addition, there are many other smaller companies scattered globally that offer specialty metal powders. When selecting a supplier, it is important to consider factors like:
- Powder composition and particle characteristics
- Quality standards and consistency
- Production capacity and lead times
- Pricing
- Technical support
Cost Analysis of Metal Powders
The costs of metal powders depend heavily on the base material, purity, particle size, and powder shape:
Table 5: Metal Powder Cost Overview
Material | Price Range |
---|---|
Iron and steel | $2-10 per kg |
Copper and aluminum | $5-30 per kg |
Nickel alloys | $10-50 per kg |
Cobalt alloys | $50-150 per kg |
Titanium alloys | $100-500 per kg |
In general, higher purity, finer sizes, and ability to flow pack tightly result in higher costs. There are also added costs for atomization and special handling of reactive powders.
When budgeting for a metal powder project, it is important to work closely with suppliers to understand impact of material choices, buy-to-fly ratios, recycling options, and inventory management on overall costs.
Installing and Operating Metal Powder Production Equipment
For companies looking to bring metal powder production in-house, there are important considerations for installing and operating the equipment:
Table 6: Metal Powder Production Setup
Parameter | Details |
---|---|
Plant Layout and Flow | – Logical separation of processes; material transport and powder handling |
Services and Utilities | – Electricity, cooling water, gas supplies |
Commissioning and Training | – Verify correct installation and functionality; train employees on operating procedures |
Safety | – Explosion prevention and containment; robust ventilation; PPE protocols |
Process Monitoring | – Data collection and analysis on key parameters like size, shape, purity |
Maintenance and Upkeep | – Regular inspections, replacement of wear components |
Quality Control | – Sampling and testing methods; statistical control; customer requirements |
Having technical experts for supervision during ramp-up and dedicated personnel for production is highly recommended. Most critical powder characteristics should be continually measured to ensure consistency.
Choosing Between Outsourcing vs In-house Production
Companies need to weigh the pros and cons of outsourcing metal powder manufacturing vs creating internal production capacity:
Table 7: Outsourcing vs In-house Production Comparison
Considerations | Outsourcing | In-house |
---|---|---|
Upfront Capital Costs | Low | Very high for equipment purchase and plant construction |
Operating Costs | Higher unit prices | Lower unit costs but have to account for labor, utilities, maintenance |
Control and Customization | Limited influence; depend on supplier capabilities | Full control over materials, parameters, schedule, quantities |
Quality and Consistency | Varies greatly; dependent on supplier | Can implement rigorous standards and control |
Technical Expertise | Supplied by vendor | Need to recruit and train specialized personnel |
Inventory and Lead Times | Need to carry buffer inventory; longer lead times | Better planning and flexibility; minimize inventory |
In summary, outsourcing benefits from lower investments but higher ongoing costs, while in-house production requires heavy upfront capital expenditure but gives greater flexibility and control during daily operations.
Advantages of Metal Powders vs Wrought Metals
Despite higher costs, metal powders offer certain advantages over traditional wrought metal processing:
Table 8: Metal Powder vs Wrought Metal Comparison
Parameter | Metal Powders | Wrought Metals |
---|---|---|
Shape Complexity | Can produce intricate, complex shapes using powder processing paths | Limited in terms of manufacturable shapes and features |
Dimensional Precision | Consistent tolerances down to ±0.1% using net shape powder capabilities | More variation; additional machining required |
Material Options | Custom alloys and microstructures tailored to application requirements | Restricted to available sheet, plate, extruded profiles |
Mechanical Properties | Favorable strength, hardness, ductility combinations | Vary based on mechanical working and thermal history |
Assembly Consolidation | Simplify assemblies by reducing part count | Additional assembly steps required |
The powder state offers unique advantages that warrant consideration where existing manufacturing techniques fall short. Continued development in advanced powder processes are enhancing the competitiveness.
FAQ
Here are some frequently asked questions about metal powders:
Table 9: Metal Powder FAQs
Question | Answer |
---|---|
How are metal powders made? | Major methods include gas/water atomization, electrolysis, milling – molten metal or bulk metals are reduced into fine powder form through mechanical and chemical processes |
What is the typical size range? | Most common is 1 micron to 1000 microns, but some specialty nano-powders and large particles used in thermal spraying go outside this range |
What is powder morphology and why is it important? | Morphology refers to powder shape/texture – smooth, spherical powders provide better packing density and flow whereas irregular, dendritic shapes improve green strength |
How are metal powders used? | Main applications include powder metallurgy press-and-sinter, metal injection molding, additive manufacturing, welding, brazing/soldering |
How much do metal powders cost? | Price depends heavily on base material, purity, particle characteristics with range spanning $5/kg to $500/kg |
Why use metal powders instead of wrought metals? | Advantages include shape complexity, dimensional precision, tailored compositions, novel properties, consolidated assemblies |
What should I look for in a metal powder supplier? | Key supplier attributes involve consistent quality, stringent testing, customized offerings, responsive lead times, technical expertise in powder production and applications |
Share On
MET3DP Technology Co., LTD is a leading provider of additive manufacturing solutions headquartered in Qingdao, China. Our company specializes in 3D printing equipment and high-performance metal powders for industrial applications.
Inquiry to get best price and customized Solution for your business!
Related Articles
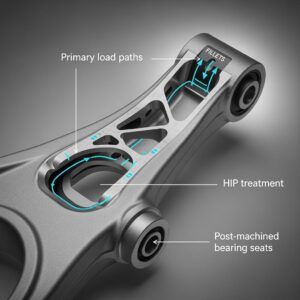
Metal 3D Printing for U.S. Automotive Lightweight Structural Brackets and Suspension Components
Read More »About Met3DP
Recent Update
Our Product
CONTACT US
Any questions? Send us message now! We’ll serve your request with a whole team after receiving your message.