Introduction to spherical titanium powder
Table of Contents
spherical titanium powder with controlled particle sizes enables manufacturing of strong, lightweight titanium metal parts using additive manufacturing or powder metallurgy pressing. Its high strength-to-weight ratio, corrosion resistance and biocompatibility make titanium an attractive engineering material across aerospace, medical, automotive and other demanding applications.
This guide covers compositions, production methods, specifications, uses, pricing and sourcing considerations for spherical titanium powder for metal AM or press-and-sinter fabrication.
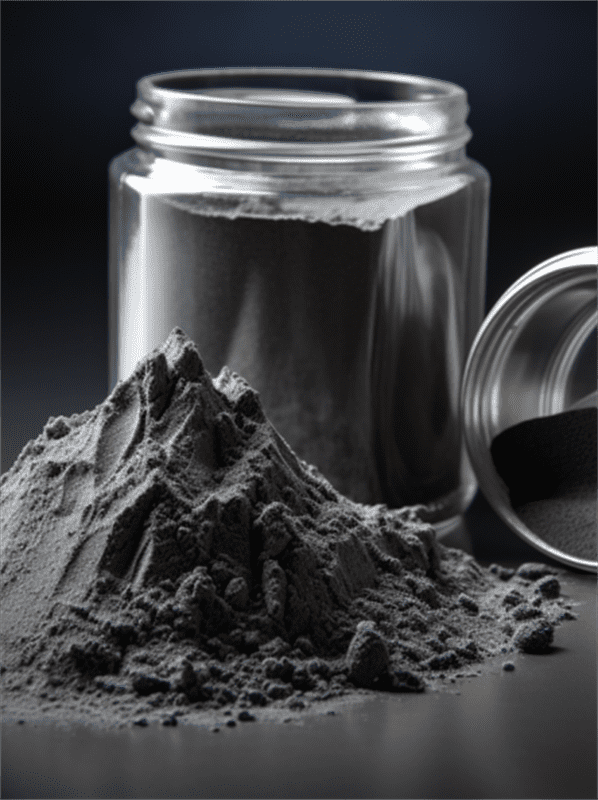
Types of spherical titanium powder
Based on composition and processing, spherical titanium powders are categorized as:
Type | Description |
---|---|
CP (Commercially Pure) Titanium | 99.5% and above pure titanium with low interstitial elemental impurities |
Ti-6Al-4V | Titanium alloy with 6% aluminum and 4% vanadium additions for strength |
Pre-alloyed Powder | Solid spherical particles with homogenous Ti-6-4 composition |
Blended Elemental | Mixture of pure titanium, aluminum and vanadium powders |
Match grade to mechanical properties, corrosion resistance and budget needs of finished titanium part applications.
Production Methods
- Plasma Atomization – High energy plasma torch melts feedstock. Powerful induction coils generate droplet spray that solidify into titanium spheroids. Narrowest particle distribution with good powder flow and packing density.
- Gas Atomization – Similar process using pressurized inert gas jets instead of plasma energy to atomize molten titanium stream into fine droplets. Lower power process but wider particle sizes.
- Rotating Electrode Process – Centrifugal forces from spinning electrodes disintegrate molten titanium into droplets. Achieves small particle sizes. High rate production with narrow distributions.
Controlling process parameters like temperature, pressure and gas flow results in spherical non-porous powders preferred for titanium metal fabrication.
Composition of spherical titanium powder
Grade | Titanium (Ti) | Aluminum (Al) | Vanadium (V) | Iron (Fe) | Oxygen (O) |
---|---|---|---|---|---|
CP Grade 1 | 98.9% min | 0.3% max | 0.2% max | 0.3% max | 0.18% max |
CP Grade 2 | 98.6% min | 0.3% max | 0.1% max | 0.3% max | 0.25% max |
CP Grade 4 | 97.5% min | 0.3% max | 0.1% max | 0.5% max | 0.40% max |
Ti-6Al-4V | Base | 5.5-6.75% | 3.5-4.5% | 0.3% max | 0.13% max |
Tight controls on low oxygen and nitrogen with carbon, iron and chromium limits preserves corrosion resistance and ductility. Grade selection balances required properties with alloy costs for different applications.
Typical Specifications
Parameter | Value | Test Method |
---|---|---|
Purity | >99% titanium | ASTM E2371, ICP analysis |
Particle shape | Spherical >92% | Microscopy |
Tap density | 2.7-3.7 g/cc | Hall flowmeter |
Particle size | 15-45 μm | Laser diffraction |
Oxygen(O) | <2000 ppm | Inert gas fusion |
Nitrogen(N) | <400 ppm | Inert gas fusion |
Hydrogen(H) | <150 ppm | Inert gas fusion |
Flow rates | >95% for 50 μm | Hall flowmeter |
Review statistical batch certification from suppliers confirming standard grade requirements and consistency performance across these metrics before purchase.
Mechanical Properties
Alloy | Ultimate Tensile Strength (ksi) | Yield Strength (ksi) | Elongation (%) |
---|---|---|---|
CP Grade 1 | 130 | 120 | 20% |
CP Grade 2 | 150 | 140 | 18% |
Ti-6Al-4V | 160 | 150 | 10% |
Achieving target material strengths requires optimized thermal post-processing like hot isostatic pressing and heat treatment. Match grade to needed properties.
Metal AM Applications
Key metal additive parts using spherical titanium powders:
- Aerospace: Airframe brackets, wing ribs, engine mounts – high strength, low weight
- Medical & Dental: Hip, knee & spine implants; surgical tools – bio-compatible
- Automotive: Connecting rods, turbocharger components- heat and corrosion resistance
- Consumer: Eyeglass frames, sports gear, watch bodies – aesthetic qualities
- Industrial: Fluid handling parts like valves, pumps; marine hardware; heat exchangers
Leverage high specific strength and tailor alloys like Ti6-4 for demanding production environments across industries.
Industry Specifications
- ASTM F1580 – Wrought titanium 6-aluminum 4-vanadium alloy for surgical implants
- ASTM B348 – Titanium and titanium alloy bars, wire, powder and forging stock specifications
- AMS 4999 – Composition limits for titanium alloy powder production
- ISO 23304 – Metal powders used for additive manufacturing processes
Review statistically validated batch certificates ensuring powder lot quality meets certifications.
Quality Considerations
Metric | Acceptable | Test Method |
---|---|---|
Tap Density | ≥2.7 g/cc | Hall Flowmeter |
Flow Rates | ≥95% for 45 μm sieve | Hall Flowmeter |
Particle Shape | ≥92% spherical | Microscopy |
Particle Size Distribution | Per ASTM B348 | Laser Diffraction |
Major Interstitials (O, H, N) | <2000; <150; <400 ppm resp. | Inert Gas Fusion |
Powder quality attributes directly correlate to final sintered part material strengths, surface finish and defect rates.
Price Range
Grade | Particle Size | Price per kg |
---|---|---|
CP Grade 1 | 15-45 microns | $50-$150 |
Ti-6Al-4V | 15-45 microns | $55-$200 |
Ti-6Al-4V ELI | 10-75 microns | $250-$750 |
Pricing depends on purity, powder sizes, production volumes and regional factors. Get firm budgetary quotes from shortlisted vendors specific to your application.
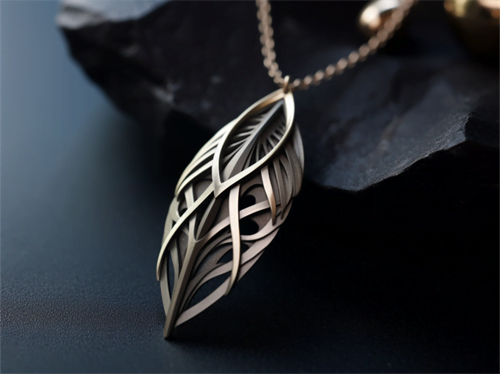
Buying Considerations
Parameter | Importance |
---|---|
Quality Certifications | High |
Consistency | High |
Part Qualification Data | Medium |
Technical Support | Medium |
Sampling Availability | Low |
Price Factors | Low |
FAQs
Q: What is caking in titanium powder and how to prevent it?
A: Powder particle clustering together into partially sintered agglomerates is called caking. It disrupts flow and packing density. Store in air-tight containers with dessicants to prevent moisture and oxygen absorption side reactions that enable caking between titanium particles over time.
Q: Are there health hazards associated with titanium powders?
A: Like most fine metallic powders, avoid inhalation during handling. Other than sensitivity issues, titanium powder is relatively inert and considered non-toxic with low risk for external contact or ingestion incidents. Use adequate protective equipment and procedures during storage, transport or processing.
Q: How to store titanium powder properly?
A: Seal containers air-tight with dessicant bags to prevent oxidation. Limit temperature variation between 10-30°C. Discard if color changes from shiny gray indicating deterioration like hydrogen embrittlement. Shelf life over 5 years if properly stored.
Q: Does titanium powder require special shipping and handling?
A: Classified as non-hazardous, non-flammable. Avoid transport during extreme heat or cold. Secure packages firmly to prevent leakage or contamination. Special cold shippers with gel packs available for high purity research grades.
Share On
MET3DP Technology Co., LTD is a leading provider of additive manufacturing solutions headquartered in Qingdao, China. Our company specializes in 3D printing equipment and high-performance metal powders for industrial applications.
Inquiry to get best price and customized Solution for your business!
Related Articles
About Met3DP
Recent Update
Our Product
CONTACT US
Any questions? Send us message now! We’ll serve your request with a whole team after receiving your message.
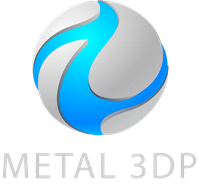
Metal Powders for 3D Printing and Additive Manufacturing