Laser Rapid Prototyping
Table of Contents
Overview of Laser Rapid Prototyping
Laser Rapid Prototyping (LRP) has revolutionized the way we approach manufacturing and design. Imagine a world where you can create a physical object directly from a digital model, almost like magic. That’s the power of LRP. This technology uses high-powered lasers to selectively fuse or melt materials, layer by layer, to create intricate and precise prototypes. Whether you’re in aerospace, automotive, or medical industries, LRP offers a fast, efficient, and versatile solution for prototyping and small-scale production.
But what makes LRP so special? It’s all about precision, speed, and material flexibility. Unlike traditional manufacturing methods that often require molds or multiple machining steps, LRP can create complex geometries with minimal material waste and reduced lead times. This guide dives deep into the world of Laser Rapid Prototyping, exploring its types, applications, advantages, limitations, and much more.
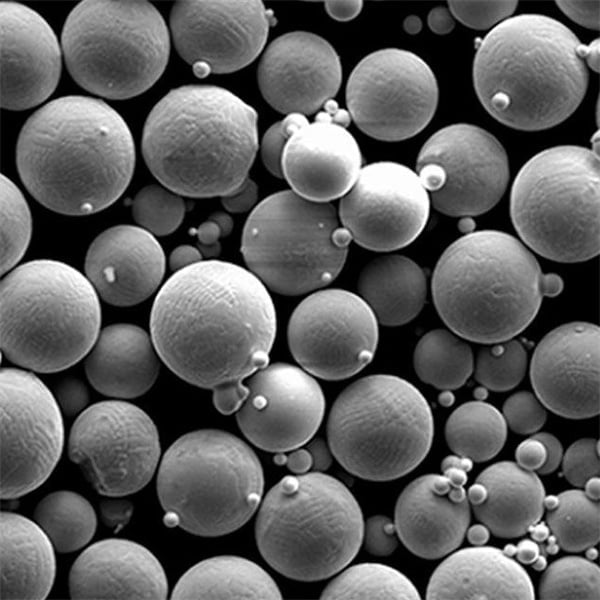
Types of Laser Rapid Prototyping
LRP encompasses several technologies, each with its unique process and applications. Let’s break them down:
1. Selective Laser Sintering (SLS)
SLS uses a high-powered laser to sinter powdered material, typically nylon or polyamide, to create solid structures. It’s excellent for producing durable prototypes and functional parts.
2. Direct Metal Laser Sintering (DMLS)
DMLS operates similarly to SLS but uses metal powders. It’s ideal for creating robust metal parts and is widely used in aerospace and medical industries.
3. Stereolithography (SLA)
SLA uses a UV laser to cure photopolymer resin layer by layer. This method is known for its high resolution and smooth surface finish, making it suitable for detailed prototypes.
4. Laser Engineered Net Shaping (LENS)
LENS involves melting metal powder using a high-powered laser to create or repair metal components. It’s highly versatile and can work with a variety of metals, including titanium and stainless steel.
5. Selective Laser Melting (SLM)
SLM fully melts metal powders to create parts with high density and mechanical properties. It’s often used for critical components in high-stress applications.
6. Electron Beam Melting (EBM)
EBM uses an electron beam instead of a laser to melt metal powder. It’s typically used for high-performance materials like titanium alloys.
7. Laser Cladding
Laser cladding involves depositing a coating of material onto a substrate using a laser. It’s used for surface modifications and repairs.
8. Laser Additive Manufacturing (LAM)
LAM is a broad term that covers various laser-based additive manufacturing processes, including those listed above.
9. Continuous Liquid Interface Production (CLIP)
CLIP uses a UV light projector to cure a photopolymer resin continuously, creating parts with excellent mechanical properties and surface finish.
10. Hybrid Manufacturing
Hybrid manufacturing combines LRP with traditional subtractive methods, offering the best of both worlds for complex part production.
Detailed Breakdown of Metal Powder Models for LRP
Let’s delve into specific metal powders used in Laser Rapid Prototyping. Each powder type has unique properties and applications.
Metal Powder Model | Composition | Properties | Applications | Suppliers & Pricing |
---|---|---|---|---|
Titanium (Ti64) | Ti-6Al-4V | High strength-to-weight ratio, biocompatibility | Aerospace, medical implants | $300-$400/kg |
Stainless Steel (316L) | Fe-Cr-Ni-Mo | Corrosion resistance, good mechanical properties | Automotive, food processing | $80-$120/kg |
Aluminum (AlSi10Mg) | Al-Si-Mg | Lightweight, good thermal properties | Aerospace, automotive | $60-$90/kg |
Inconel (718) | Ni-Cr-Fe-Mo | High temperature and corrosion resistance | Turbine blades, aerospace | $400-$600/kg |
Cobalt-Chrome (CoCr) | Co-Cr-Mo | High wear resistance, biocompatibility | Dental, orthopedic implants | $350-$500/kg |
Copper (Cu) | Pure Cu | High conductivity, good mechanical properties | Electronics, heat exchangers | $30-$50/kg |
Tool Steel (H13) | Fe-Cr-Mo-V | High hardness, thermal fatigue resistance | Tooling, molds | $50-$70/kg |
Nickel Alloy (625) | Ni-Cr-Mo-Nb | Oxidation resistance, good weldability | Chemical processing, marine | $350-$500/kg |
Maraging Steel (MS1) | Fe-Ni-Co-Mo | High strength, toughness | Aerospace, tooling | $80-$120/kg |
Tungsten (W) | Pure W | High density, melting point | Radiation shielding, aerospace | $500-$800/kg |
Applications of Laser Rapid Prototyping
Laser Rapid Prototyping has found its way into various industries, thanks to its versatility and efficiency. Here are some key applications:
Industry | Application | Benefits |
---|---|---|
Aerospace | Engine components, structural parts | Lightweight, high strength, design freedom |
Automotive | Prototypes, end-use parts | Reduced lead times, complex geometries |
Medical | Implants, surgical tools | Biocompatibility, patient-specific designs |
Electronics | Heat sinks, connectors | High conductivity, precision |
Dental | Crowns, bridges | Customization, accuracy |
Tooling | Molds, jigs | Durability, quick turnaround |
Consumer Goods | Custom products, accessories | Customization, fast prototyping |
Specifications, Sizes, Grades, Standards
When selecting materials and processes for LRP, it’s essential to understand the specifications, sizes, grades, and standards associated with each. Here’s a breakdown:
Material | Specifications | Sizes | Grades | Standards |
---|---|---|---|---|
Titanium (Ti64) | ASTM F1472, ISO 5832-3 | 15-45 µm powder | Grade 5 | AMS 4911, MIL-T-9046 |
Stainless Steel (316L) | ASTM A240, ISO 4954 | 20-50 µm powder | Marine Grade | ASTM A276, AMS 5653 |
Aluminum (AlSi10Mg) | ISO 3522 | 20-63 µm powder | Cast | EN 1706 |
Inconel (718) | ASTM B637, AMS 5662 | 15-45 µm powder | Nickel-Chromium | AMS 5663 |
Cobalt-Chrome (CoCr) | ASTM F75 | 20-53 µm powder | F75 | ISO 5832-4 |
Copper (Cu) | ASTM B124 | 15-45 µm powder | Oxygen-free | ASTM B152 |
Tool Steel (H13) | ASTM A681 | 15-53 µm powder | H13 | ASTM A681 |
Nickel Alloy (625) | ASTM B443 | 15-45 µm powder | NiCr22Mo9Nb | AMS 5666 |
Maraging Steel (MS1) | ASTM A579 | 15-53 µm powder | 18Ni(300) | AMS 6520 |
Tungsten (W) | ASTM B777 | 15-45 µm powder | Pure W | ASTM F288 |
Suppliers and Pricing Details
Finding the right supplier is crucial for ensuring material quality and availability. Here’s a list of suppliers and pricing for various metal powders:
Supplier | Material | Price (per kg) | Notes |
---|---|---|---|
EOS GmbH | Titanium (Ti64) | $300-$400 | High-quality powders for LRP |
GKN Hoeganaes | Stainless Steel (316L) | $80-$120 | Extensive range of metal powders |
Renishaw | Aluminum (AlSi10Mg) | $60-$90 | Precision-engineered powders |
Carpenter Technology | Inconel (718) | $400-$600 | Specialty alloys for high-performance applications |
Sandvik | Cobalt-Chrome (CoCr) | $350-$500 | Medical-grade powders |
Praxair Surface Technologies | Copper (Cu) | $30-$50 | High-purity copper powders |
Höganäs AB | Tool Steel (H13) | $50-$70 | Consistent quality and performance |
Oerlikon Metco | Nickel Alloy (625) | $350-$500 | Advanced powders for aerospace |
LPW Technology | Maraging Steel (MS1) | $80-$120 | High-strength steel powders |
H.C. Starck | Tungsten (W) | $500-$800 | High-density tungsten powders |
Advantages of Laser Rapid Prototyping
Laser Rapid Prototyping offers numerous advantages, making it a popular choice across various industries. Here’s a detailed look at the benefits:
Speed and Efficiency
LRP significantly reduces the time from design to prototype, allowing for faster iterations and quicker time-to-market.
Complex Geometries
Unlike traditional methods, LRP can create intricate and complex shapes that would be impossible or very costly to produce otherwise.
Material Versatility
LRP works with a wide range of materials, from metals to polymers, providing flexibility in material choice based on application needs.
Reduced Waste
LRP is an
additive process, meaning it only uses the material needed for the part, leading to minimal waste and more sustainable manufacturing.
Customization
The ability to produce customized parts, especially in medical and dental fields, is a significant advantage of LRP.
Strong and Lightweight Parts
Many LRP processes can produce parts with excellent mechanical properties, essential for industries like aerospace and automotive.
Disadvantages of Laser Rapid Prototyping
Despite its many advantages, LRP also has some limitations and challenges:
High Initial Costs
The equipment and materials for LRP can be expensive, making it a significant investment.
Limited Material Properties
While LRP can work with many materials, some materials may not have the same properties as those produced by traditional methods.
Surface Finish
Parts produced by LRP may require additional finishing processes to achieve the desired surface quality.
Size Limitations
The build size in LRP is often limited by the machine’s capabilities, which can be a constraint for larger parts.
Post-Processing
Some LRP parts may need post-processing steps, such as heat treatment or machining, to meet final specifications.
Knowledge and Expertise
Successfully implementing LRP requires a good understanding of the technology and materials, which can be a barrier for some companies.
Comparing Laser Rapid Prototyping to Traditional Manufacturing
Let’s compare LRP to traditional manufacturing methods to see how it stacks up:
Parameter | Laser Rapid Prototyping | Traditional Manufacturing |
---|---|---|
Speed | Faster, especially for complex parts | Slower, multiple steps involved |
Cost | Higher initial cost, lower per-part cost | Lower initial cost, higher per-part cost |
Complexity | Can handle complex geometries easily | Limited by machining capabilities |
Waste | Minimal waste | More waste due to subtractive processes |
Customization | High degree of customization | Limited customization options |
Material Variety | Wide range of materials | Depends on machining and tooling capabilities |
Surface Finish | May require post-processing | Often better surface finish without additional steps |
Size Limitations | Limited by machine size | Can handle larger parts with appropriate equipment |
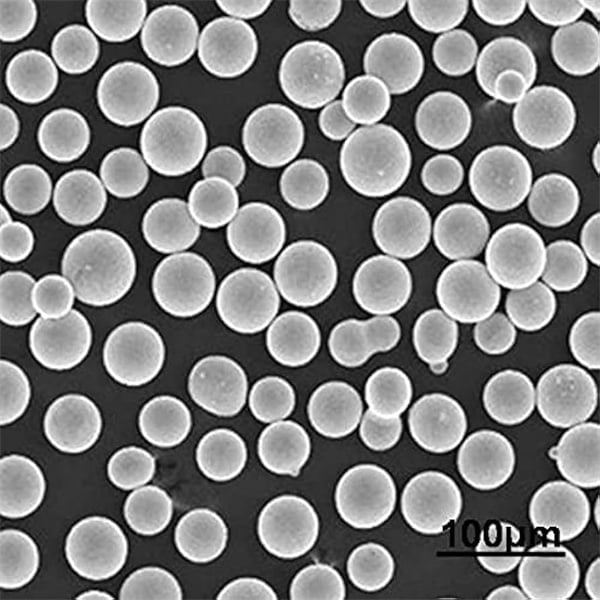
FAQ
To help you better understand Laser Rapid Prototyping, here are some frequently asked questions:
Question | Answer |
---|---|
What is Laser Rapid Prototyping? | LRP is a manufacturing process that uses lasers to create prototypes or end-use parts from digital models. |
Which industries use LRP? | Aerospace, automotive, medical, electronics, dental, tooling, and consumer goods industries. |
What materials can be used in LRP? | Metals, polymers, ceramics, and composites. |
How does LRP compare to traditional manufacturing? | LRP offers faster production, reduced waste, and the ability to create complex geometries, but has higher initial costs and potential size limitations. |
What are the common types of LRP? | SLS, DMLS, SLA, LENS, SLM, EBM, Laser Cladding, LAM, CLIP, Hybrid Manufacturing. |
What are the advantages of LRP? | Speed, efficiency, complex geometries, material versatility, reduced waste, customization, and strong, lightweight parts. |
What are the disadvantages of LRP? | High initial costs, limited material properties, surface finish, size limitations, post-processing needs, and required expertise. |
What is the cost of LRP materials? | Prices vary by material, ranging from $30/kg for copper to $800/kg for tungsten. |
What is the typical lead time for LRP parts? | Lead times can vary from a few hours to several days, depending on part complexity and size. |
Can LRP be used for mass production? | LRP is typically used for prototyping and small-scale production, but advancements are being made towards mass production capabilities. |
Conclusion
Laser Rapid Prototyping is a game-changing technology in the manufacturing world. Its ability to produce complex, customized parts quickly and efficiently opens up new possibilities across various industries. By understanding the different types of LRP, the materials used, and the advantages and limitations, you can make informed decisions about incorporating this technology into your processes. Whether you’re looking to speed up prototyping, reduce waste, or create intricate designs, LRP offers a versatile and powerful solution.
Share On
MET3DP Technology Co., LTD is a leading provider of additive manufacturing solutions headquartered in Qingdao, China. Our company specializes in 3D printing equipment and high-performance metal powders for industrial applications.
Inquiry to get best price and customized Solution for your business!
Related Articles
About Met3DP
Recent Update
Our Product
CONTACT US
Any questions? Send us message now! We’ll serve your request with a whole team after receiving your message.
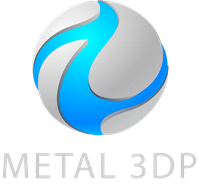
Metal Powders for 3D Printing and Additive Manufacturing