Understanding the LPBF Process
Table of Contents
Overview
Laser Powder Bed Fusion (LPBF) is a revolutionary additive manufacturing technology that uses a high-powered laser to fuse metal powders into precise, high-performance components. It’s a game-changer in industries ranging from aerospace to medical devices, where intricate designs and material properties are paramount. But what exactly is the LPBF process? Let’s delve into the nitty-gritty details, explore various metal powders used, and see how LPBF stacks up against traditional manufacturing methods.
Introduction to LPBF
Laser Powder Bed Fusion (LPBF) is a subset of additive manufacturing (AM) that focuses on creating objects by fusing powdered materials layer by layer. This process leverages a high-intensity laser that selectively melts metal powders based on a 3D model, creating intricate geometries with exceptional accuracy and material properties.
How LPBF Works
LPBF begins with spreading a thin layer of metal powder over the build platform. A laser beam, guided by computer-aided design (CAD) data, selectively fuses the powder into a solid layer. The platform then lowers, and another layer of powder is spread. This process repeats until the entire part is formed. Post-processing steps, such as removing excess powder and heat treatment, finalize the product.
Key Steps in LPBF:
- Powder Spreading: A recoater spreads a thin layer of metal powder on the build platform.
- Laser Melting: The laser selectively melts and fuses the powder according to the CAD model.
- Layer Building: The platform lowers, and the next layer of powder is applied and melted.
- Post-Processing: Excess powder is removed, and the part undergoes further treatments if necessary.
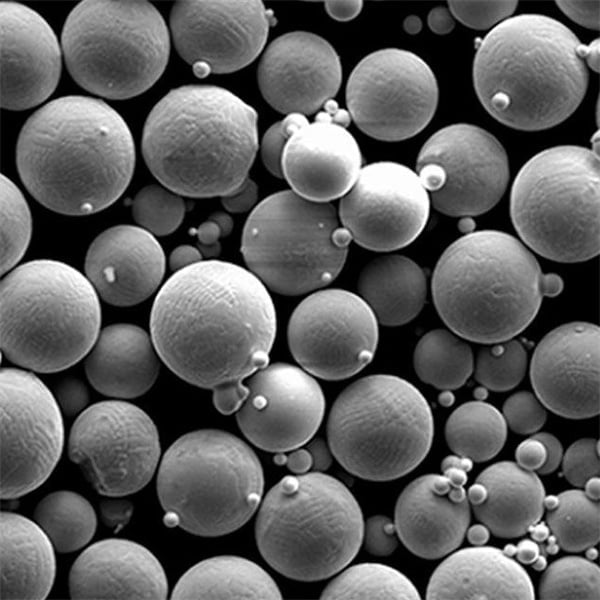
Types of Metal Powders in LPBF
Different applications require different materials. Below are some of the specific metal powders commonly used in LPBF:
Common Metal Powders:
Metal Powder | Composition | Properties |
---|---|---|
Stainless Steel | Fe, Cr, Ni | High corrosion resistance, strength, ductility |
Titanium Alloy | Ti-6Al-4V | High strength-to-weight ratio, biocompatibility |
Aluminum Alloy | AlSi10Mg | Lightweight, good thermal and electrical conductivity |
Inconel 718 | Ni, Cr, Fe, Nb | High temperature resistance, corrosion resistance |
Cobalt-Chrome | Co, Cr, Mo | Wear resistance, strength, biocompatibility |
Maraging Steel | Fe, Ni, Mo, Co | High strength, toughness, good machinability |
Copper Alloy | Cu, with minor additions of other elements | Excellent thermal and electrical conductivity, good mechanical properties |
Tool Steel | Fe, C, Cr, V | High hardness, wear resistance, good machinability |
Hastelloy X | Ni, Cr, Fe, Mo | High strength, oxidation resistance, good formability |
Nickel Alloy | Ni, Cr, Mo | Corrosion resistance, high-temperature performance |
Applications of LPBF
LPBF is versatile, finding applications across numerous industries due to its ability to produce complex geometries and custom parts.
Industry Applications:
Industry | Application Examples |
---|---|
Aerospace | Turbine blades, fuel nozzles, structural components |
Medical | Implants, prosthetics, surgical instruments |
Automotive | Engine components, transmission parts, custom tools |
Energy | Heat exchangers, turbine parts, piping components |
Jewelry | Custom designs, intricate pieces, prototypes |
Tooling | Molds, dies, custom tooling |
Advantages of LPBF
Why is LPBF such a hot topic? Let’s explore some of its key advantages.
Key Advantages:
- Complex Geometries: LPBF allows for the creation of intricate and complex designs that are difficult or impossible with traditional methods.
- Material Efficiency: Minimal waste since only the required amount of powder is used.
- Customization: Easily produce custom or one-off parts tailored to specific needs.
- Strength and Performance: High material density and superior mechanical properties.
- Reduction in Lead Times: Faster production times compared to conventional manufacturing.
Disadvantages of LPBF
Like any technology, LPBF has its downsides. It’s important to weigh these against the advantages.
Key Disadvantages:
- High Costs: Equipment and material costs are high, making it less suitable for low-budget projects.
- Build Size Limitations: Restricted to the build volume of the machine.
- Post-Processing Requirements: Often requires significant post-processing, adding to time and cost.
- Powder Handling: Metal powders can be hazardous, requiring careful handling and storage.
- Surface Finish: May require additional finishing processes to achieve the desired surface quality.
Technical Specifications of Metal Powders
Different metal powders come with varying specifications that are crucial for their performance in LPBF.
Technical Specifications:
Metal Powder | Particle Size | Density (g/cm³) | Melting Point (°C) | Tensile Strength (MPa) | Elongation (%) |
---|---|---|---|---|---|
Stainless Steel | 15-45 µm | 7.9 | 1450 | 600 | 40 |
Titanium Alloy | 20-45 µm | 4.43 | 1660 | 900 | 10 |
Aluminum Alloy | 20-63 µm | 2.7 | 660 | 400 | 10 |
Inconel 718 | 15-53 µm | 8.19 | 1300 | 1250 | 20 |
Cobalt-Chrome | 15-45 µm | 8.4 | 1330 | 1100 | 15 |
Maraging Steel | 10-45 µm | 8.0 | 1413 | 2000 | 12 |
Copper Alloy | 15-45 µm | 8.96 | 1083 | 210 | 40 |
Tool Steel | 10-45 µm | 7.8 | 1420 | 2000 | 5 |
Hastelloy X | 15-53 µm | 8.22 | 1330 | 780 | 40 |
Nickel Alloy | 15-45 µm | 8.44 | 1440 | 690 | 25 |
Suppliers and Pricing
Where can you get these metal powders, and how much will they set you back? Here’s a breakdown.
Suppliers and Pricing:
Supplier | Metal Powders Offered | Price Range (per kg) |
---|---|---|
EOS GmbH | Stainless Steel, Titanium, Aluminum | $300 – $600 |
GE Additive | Inconel, Cobalt-Chrome, Maraging Steel | $500 – $1000 |
3D Systems | Copper Alloy, Tool Steel, Hastelloy | $400 – $900 |
Carpenter Technology | Nickel Alloy, Stainless Steel | $350 – $800 |
Sandvik | Titanium Alloy, Aluminum | $300 – $700 |
AP&C (GE Additive) | Various metal powders | $400 – $950 |
Pros and Cons Comparison
How does LPBF compare to other manufacturing processes? Let’s break it down.
LPBF vs. Traditional Manufacturing:
Factor | LPBF | Traditional Manufacturing |
---|---|---|
Complexity | High (can produce intricate designs) | Moderate to Low |
Material Waste | Low (only needed powder used) | High (excess material often wasted) |
Customization | High (easy to customize) | Low to Moderate |
Speed | Moderate (fast for prototypes) | Varies (often longer for custom parts) |
Cost | High (expensive equipment/materials) | Moderate to Low |
Surface Finish | Moderate (may need post-processing) | High (depending on method used) |
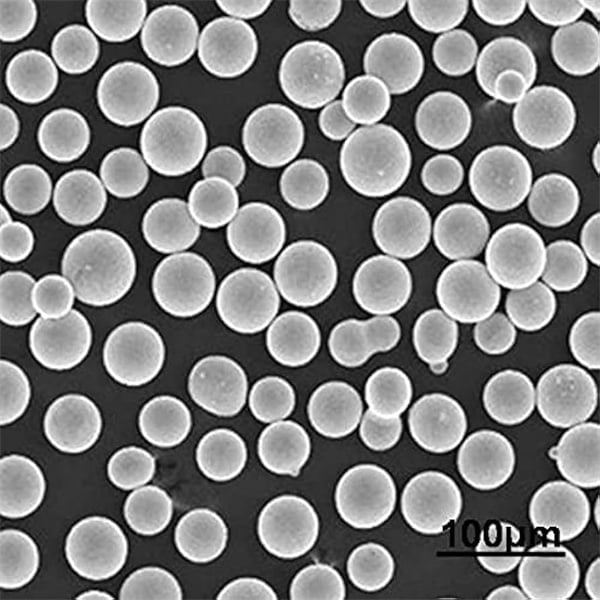
FAQ
1. What is Laser Powder Bed Fusion (LPBF)? Laser Powder Bed Fusion (LPBF) is an additive manufacturing (AM) technique that uses a high-powered laser to fuse powdered material layer by layer to create a solid, three-dimensional object.
2. What materials can be used in LPBF? LPBF can process a wide range of materials including metals (e.g., titanium, aluminum, stainless steel, cobalt-chrome), ceramics, and some polymers. The choice of material depends on the application requirements.
3. What industries use LPBF? LPBF is used in various industries such as aerospace, medical (for implants and prosthetics), automotive, and tool manufacturing due to its ability to produce complex, high-precision parts.
4. What are the key parameters in LPBF? Key parameters include laser power, scan speed, layer thickness, hatch spacing, and powder characteristics. These parameters need to be optimized for each material and part design to ensure quality and performance.
5. How do you ensure the quality of LPBF parts? Quality is ensured through a combination of process control, real-time monitoring, post-process inspection (such as X-ray computed tomography or metallography), and adherence to industry standards.
Share On
MET3DP Technology Co., LTD is a leading provider of additive manufacturing solutions headquartered in Qingdao, China. Our company specializes in 3D printing equipment and high-performance metal powders for industrial applications.
Inquiry to get best price and customized Solution for your business!
Related Articles
About Met3DP
Recent Update
Our Product
CONTACT US
Any questions? Send us message now! We’ll serve your request with a whole team after receiving your message.
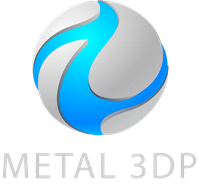
Metal Powders for 3D Printing and Additive Manufacturing