Process flow of mechanical alloying 3D printing metal powder
Table of Contents
Imagine holding the future in your hands. A revolutionary technology, 3D printing, allows us to create complex objects directly from digital models. But what about the building blocks for these marvels? Enter mechanical alloying, a game-changing process for crafting high-performance metal powders specifically designed for 3D printing.
This comprehensive guide delves into the intricate world of mechanical alloying, exploring its process flow, key parameters, influential factors, and real-world applications. We’ll also unveil a diverse range of metal powder models, empowering you with the knowledge to unlock the full potential of this transformative technology.
Production Process of Mechanical Alloying
Mechanical alloying (MA) is a solid-state powder processing technique that utilizes high-energy milling to achieve two primary objectives:
- Intimately mix elemental powders or pre-alloyed powders: Imagine meticulously folding and mixing various powders, like flour and cocoa, to create a uniform dough. MA replicates this process at an intense level, ensuring a homogeneous blend of different elements.
- Refine the microstructure of the powder particles: The vigorous milling process breaks down the powder particles, leading to a finer and more uniform size distribution. This, in turn, significantly influences the flowability, packing density, and ultimately, the printability of the powder.
The process flow of mechanical alloying for 3D printing metal powders can be broadly divided into five key stages:
- Powder selection and pre-processing: Choosing the right combination of elemental or pre-alloyed powders forms the foundation. Factors like desired final composition, particle size, and purity play a crucial role in selection. Pre-processing steps like drying and sieving may be necessary to ensure optimal performance during milling.
- Milling: This is the heart of the process. Powders are loaded into a high-energy ball mill, where they are subjected to intense collisions with grinding media (balls) for a predetermined duration. The energy from these collisions breaks down the powder particles and promotes intimate mixing at the atomic level.
- Classification and sieving: After milling, the powder mixture undergoes classification and sieving to achieve the desired particle size distribution. This ensures optimal flowability and packing density, crucial for successful 3D printing.
- Powder analysis and characterization: The final powder is meticulously analyzed using various techniques like X-ray diffraction (XRD) and scanning electron microscopy (SEM). These analyses verify the final composition, microstructure, and flowability characteristics, ensuring they meet the stringent requirements for 3D printing.
- Packaging and storage: Finally, the qualified powder is carefully packaged and stored under controlled conditions to maintain its quality and prevent degradation.
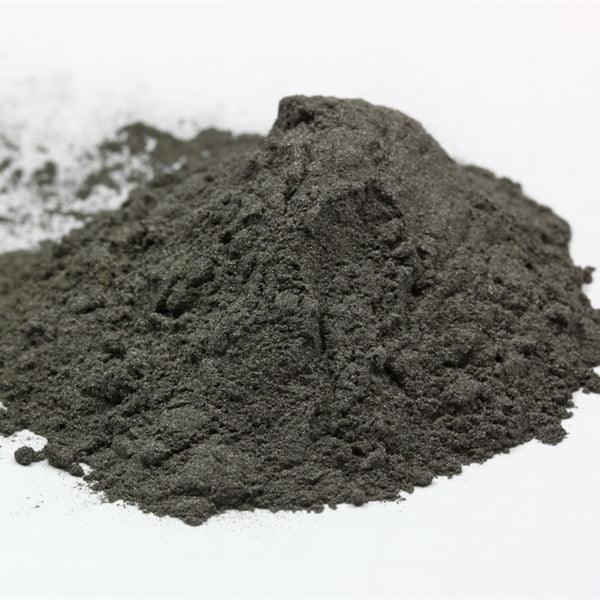
Explain the Key Parameters for Each Step
Each stage in the mechanical alloying process is influenced by several critical parameters that directly impact the final powder quality. Understanding and controlling these parameters is essential for achieving consistent and desirable outcomes:
- Powder selection: Particle size, purity, and chemical composition of the starting powders significantly affect the milling efficiency and final microstructure.
- Milling parameters: Milling duration, speed, and the type of grinding media all play a crucial role in achieving the desired level of refinement and avoiding excessive contamination.
- Classification and sieving parameters: Mesh size and sieving techniques influence the final particle size distribution, impacting flowability and packing density.
The Influence of Key Parameters on the Final Powder Quality
The interplay of various parameters throughout the process significantly influences the final powder quality:
- Particle size and distribution: Finer and more uniform particle size distributions generally lead to better flowability, packing density, and ultimately, improved printability.
- Microstructure: The milling process alters the microstructure of the powder particles, influencing their mechanical and physical properties. For instance, finer particles typically exhibit higher strength and hardness.
- Chemical composition: Mechanical alloying allows for precise control over the final composition of the powder, enabling the creation of novel alloys with tailored properties.
Exploring the Diverse Landscape of Metal Powder Models for 3D Printing
The world of 3D printing metal powders boasts a diverse range of options, each catering to specific needs and applications. Here’s an exploration of ten popular metal powder models:
Model: 316L Stainless Steel
Description: A versatile and widely used austenitic stainless steel powder known for its excellent corrosion resistance, formability, and biocompatibility.
Applications: Aerospace components, medical implants, and general-purpose structural parts.
Model: Inconel 625
Description: A high-performance nickel-chromium-based superalloy powder offering exceptional strength, high-temperature resistance, and good oxidation resistance.
Model: Titanium 6Al-4V
Description: A widely used titanium alloy powder known for its high strength-to-weight ratio, excellent biocompatibility, and good corrosion resistance.
Applications: Aerospace components, medical implants, and high-performance sporting goods.
Model: Inconel 718
Description: Another high-performance nickel-chromium-based superalloy powder offering superior strength, creep resistance at elevated temperatures, and good oxidation resistance compared to Inconel 625.
Applications: Aerospace components, turbine blades, and demanding structural applications.
Model: Aluminum Si10Mg
Description: A popular aluminum alloy powder containing silicon and magnesium, known for its good castability, weldability, and improved strength compared to pure aluminum.
Applications: Automotive components, architectural components, and general-purpose parts requiring good strength and weight savings.
Model: Copper
Description: A pure copper powder offering excellent electrical conductivity and thermal conductivity.
Applications: Heat exchangers, electrical components, and applications requiring high thermal and electrical conductivity.
Model: CoCrMo
Description: A cobalt-chromium-molybdenum alloy powder known for its excellent wear resistance, biocompatibility, and high strength.
Applications: Medical implants, orthopedic devices, and wear-resistant components.
Model: Nickel
Description: A pure nickel powder offering good corrosion resistance, ductility, and electrical conductivity.
Applications: Electrodes for battery production, chemical processing equipment, and electronic components.
Model: Maraging Steel
Description: A family of high-strength, low-carbon steel powders that can be age-hardened to achieve exceptional strength and toughness.
Applications: Aerospace components, critical structural parts requiring high strength and toughness.
Model: Hastelloy C-276
Description: A nickel-chromium-molybdenum-tungsten alloy powder offering exceptional corrosion resistance to a wide range of chemicals and high-temperature environments.
Applications: Chemical processing equipment, pollution control equipment, and components exposed to harsh chemical environments.
Comparing Metal Powder Models: A Buyer’s Guide
Choosing the right metal powder for your 3D printing project is crucial for success. Here’s a breakdown of key factors to consider when comparing different models:
- Desired properties: Identify the critical properties your final product needs, such as strength, corrosion resistance, and thermal conductivity.
- Application: Different applications have varying requirements. Consider the specific demands of your project when selecting a powder.
- Printability: Ensure the chosen powder offers good flowability and packing density for optimal printing performance with your chosen 3D printing technology.
- Cost: Metal powders can vary significantly in price. Evaluate your budget and choose a cost-effective option that meets your project requirements.
Advantages and Limitations of Mechanical Alloying
Advantages:
- Versatility: Allows for the creation of a wide range of metal powder compositions, including novel alloys with tailored properties.
- Precise control: Enables precise control over the final powder composition and microstructure, leading to consistent and predictable results.
- Scalability: The process can be scaled up or down to meet various production needs.
Limitations:
- Cost: Compared to other powder production methods, mechanical alloying can be more expensive, especially for large-scale production.
- Process complexity: Requires careful control of various parameters to ensure consistent and desirable powder quality.
- Potential contamination: The milling process can introduce contaminants from the grinding media, necessitating strict control measures.
Conclusion
Mechanical alloying presents a powerful technique for crafting high-performance metal powders specifically designed for 3D printing. By understanding the process flow, key parameters, and diverse range of available metal powder models, you can harness the potential of this technology to create innovative and functional objects. As 3D printing technology continues to evolve, mechanical alloying will undoubtedly play a vital role in pushing the boundaries of what’s possible.
FAQ
Q: What are the benefits of using metal powders produced by mechanical alloying?
A: Metal powders produced by mechanical alloying offer several benefits, including:
- Tailored properties: Precise control over the composition and microstructure allows for the creation of powders with specific properties desired for the application.
- Improved printability: Finer and more uniform particle size distributions often lead to better flowability and packing density, enhancing printability.
- Novel alloys: The ability to mix elements at the atomic level enables the creation of novel alloys with unique properties not achievable with traditional methods.
Q: What are the limitations of mechanical alloying compared to other powder production methods?
A: While offering several advantages, mechanical alloying also has some limitations:
- Higher cost: Compared to techniques like atomization, mechanical alloying can be more expensive, especially for large-scale production.
- Process complexity: The process requires careful control of various parameters, such as milling duration, speed, and media selection, to achieve consistent and high-quality powder.
- Potential contamination: The milling process can introduce contaminants from the grinding media, necessitating strict control measures and potentially impacting the final powder properties.
Q: What are some emerging trends in the field of mechanical alloying for 3D printing metal powders?
A: The field of mechanical alloying for 3D printing metal powders is constantly evolving, with several exciting trends emerging:
- Development of new alloys: Researchers are continuously exploring the creation of novel alloys with improved properties like higher strength, better corrosion resistance, and lighter weight, specifically tailored for 3D printing applications.
- Advanced characterization techniques: New techniques are being developed to analyze and characterize metal powders with greater accuracy and detail, allowing for a deeper understanding of the relationship between processing parameters, microstructure, and final powder properties.
- Integration with automation: The integration of automation and machine learning into the mechanical alloying process is being explored to improve process control, consistency, and efficiency.
Q: How does the choice of metal powder impact the final product in 3D printing?
A: The selection of metal powder plays a crucial role in determining the final properties and quality of the 3D printed product. Here’s how:
- Material properties: The inherent properties of the chosen metal powder, such as its strength, ductility, and thermal conductivity, directly translate to the final product.
- Microstructure: The microstructure of the powder, influenced by the mechanical alloying process, impacts the final product’s mechanical properties like strength and fatigue resistance.
- Printability: The flowability and packing density of the powder significantly affect the printability and surface quality of the final product.
Therefore, careful consideration of the desired properties, application requirements, and printing technology compatibility is essential when selecting a metal powder for 3D printing.
By understanding the intricacies of mechanical alloying, the diverse landscape of metal powder models, and the crucial factors influencing powder selection, you can leverage this transformative technology to unlock the full potential of 3D printing and create objects that redefine the boundaries of design and functionality.
Share On
MET3DP Technology Co., LTD is a leading provider of additive manufacturing solutions headquartered in Qingdao, China. Our company specializes in 3D printing equipment and high-performance metal powders for industrial applications.
Inquiry to get best price and customized Solution for your business!
Related Articles
About Met3DP
Recent Update
Our Product
CONTACT US
Any questions? Send us message now! We’ll serve your request with a whole team after receiving your message.
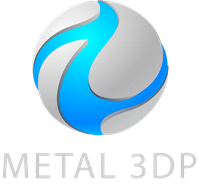
Metal Powders for 3D Printing and Additive Manufacturing
COMPANY
PRODUCT
cONTACT INFO
- Qingdao City, Shandong, China
- [email protected]
- [email protected]
- +86 19116340731