Metal Alloy Powders
Table of Contents
Metal alloy powders comprise diverse precise blends of metal elements produced through atomization processing into fine spherical particles ideal for advanced fabrication techniques. This guide serves technical professionals a comprehensive reference on metal powder alloy grades spanning typical compositions, mechanical properties data, manufacturing methods, key applications, and leading global suppliers.
Overview of Metal Alloy Powders
Metal powders produced from alloys of iron, nickel, cobalt, aluminum, titanium, copper, and other base metals represent versatile engineering materials conferring tailored properties from their controlled compositions.
Common Metal Powder Types
Alloy System | Description |
---|---|
Stainless steels | Corrosion resistant, high strength |
Tool and low alloy steels | Hardened, temperature resistant |
Nickel superalloys | Extreme heat/chemical resistance |
Cobalt superalloys | Biocompatible, wear resistant |
Titanium alloys | Lightweight, strong for aerospace |
Copper and bronzes | Electrical/thermal conductivity |
Precious metal alloys | Pure, inert, specialized applications |
Balancing constituents enables optimizing for key requirements like hardness, strength, durability, conductivity, magnetism or cost targets.
Typical Composition Ranges
Alloying Element | Role | Wt% Range |
---|---|---|
Iron, Cobalt, Nickel | Base metal matrix | 50-99% |
Chromium | Corrosion + oxidation resistance | 5-35% |
Molybdenum | Strength, creep resistance | 0-30% |
Tungsten | Heat resistance, density | 0-18% |
Manganese | Deoxidizer, strength | 0-15% |
Carbon | Hardening, wear resistance | 0-6% |
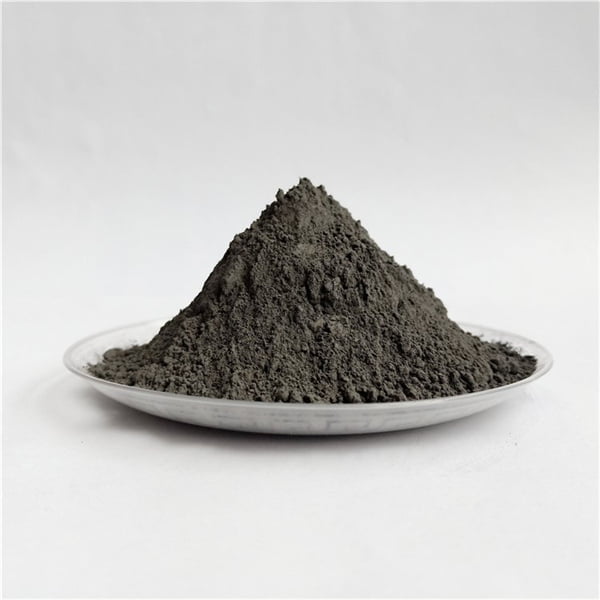
Metal Alloy Powder Specifications
Size Distributions
Mesh Size | Micrometers |
---|---|
-325 | <45 μm |
-100/+325 | 45-150 μm |
+100 | >150 μm |
Morphology and Flow Characteristics
Attribute | Typical Range |
---|---|
Particle shape | Spherical |
Apparent density | 2 – 6 g/cm3 |
Tap density | 4 – 8 g/cm3 |
Hausner ratio | <1.25 |
Flow rate | 20-35 s/50g |
Friction coefficient | 0.4-0.9 |
Chemistry and Contamination Levels
Element | Max ppm |
---|---|
Oxygen | 1000 |
Nitrogen | 150 |
Carbon | 3000 |
Sulfur | 100 |
Metal Powder Production Methods
Water Atomization
- High purity inert gas atomization
- Protects reactive alloy chemistries
- Enables small size distributions
Gas Atomization
- Air melt spinning
- Narrowest size distributions
- Spheroidal particle shapes
Plasma Rotating Electrode Process (PREP)
- Custom alloys, research quantities
- Controlled microstructures
- Rapid solidification rates
Mechanical Alloying
- Ball milling elemental blends
- Lower cost than atomization
- Broad size distributions
Other Methods
- Electrolysis
- Chemical reduction
Properties of Metal Alloy Powders
Balancing key attributes determines suitable applications:
Mechanical Properties
Alloy System | Yield Strength | Tensile Strength | Elongation |
---|---|---|---|
Stainless Steels | 200-1400 MPa | 500-1600 MPa | 10-50% |
Tool Steels | 600-1900 MPa | 1000-2100 MPa | 5-15% |
Nickel Superalloys | 500-1400 MPa | 700-1700 MPa | 10-50% |
Titanium Alloys | 750-1100 MPa | 900-1200 MPa | 15-25% |
Copper/Bronzes | 70-450 MPa | 200-600 MPa | 5-60% |
Thermal Properties
Alloy System | Melting Point | Thermal Conductivity |
---|---|---|
Stainless Steels | 1400-1500°C | 10-30 W/m-°K |
Tool Steels | 1350-1450°C | 20-35 W/m-°K |
Nickel Superalloys | 1200-1400°C | 5-50 W/m-°K |
Titanium Alloys | 1600-1700°C | 5-20 W/m-°K |
Copper/Bronzes | 900-1300°C | 50-400 W/m-°K |
Metal Alloy Powder Applications
Additive Manufacturing
- Aerospace components
- Medical implants
- Automotive hardware
- Tooling and molds
- Exotic architecture
Powder Metallurgy
- Oil and gas bearings
- Automotive bushings
- Appliance hardware
- Cost-effective net shapes
Thermal Spray Coatings
- Corrosion resistant overlays
- Friction reducing films
- Dimensional restoration
Electronics and Magnetics
- Conductive adhesives
- Inductor cores
- Thermal management
- Surface mount devices
Emerging Applications
- Batteries and energy storage
- 3D printed electronics
- Exotic alloys and prototypes
- Micro-scale components
Leading Metal Alloy Powder Manufacturers
Company | Location |
---|---|
Sandvik Osprey | United Kingdom |
Carpenter Powder Products | United States |
Praxair Surface Technologies | United States |
Höganäs | Sweden |
Rio Tinto Metal Powders | Canada |
ATI Powder Metals | United States |
Custom Toll Processing Partners
- Extensive alloy development expertise
- Specialize in research scale production
- Shorten development timelines
- Protect intellectual property
Cost Estimates
Stainless Steel Powders
Alloy Grade | Cost Per Kg |
---|---|
304, 316, 303 | $12-30 |
17-4PH, 15-5PH | $40-90 |
Custom duplex/superaustentics | $70-150 |
Tool and High Alloy Steel Powders
Alloy Grade | Cost Per Kg |
---|---|
H13, M2, M4 | $20-45 |
Custom PM tool steel | $45-100 |
Nickel Superalloy Powders
Alloy Grade | Cost Per Kg |
---|---|
Inconel 718 | $90-180 |
Custom Waspaloy, Rene alloys | $250-1000+ |
Titanium and Exotic Alloy Powders
Alloy Grade | Cost Per Kg |
---|---|
Ti-6Al-4V | $270-450 |
Custom titanium | $450-1000+ |
Pros vs Cons
Advantages | Challenges |
---|---|
Properties surpassing wrought alloys | Requires protective processing |
Custom alloys and microstructures | Limited size capabilities |
Complex geometry enabled | Needs post-consolidation |
Lower buy-to-fly ratios | Qualification testing |
Reduced production lead times | Handling and storage precautions |
Weigh trade-offs carefully against performance targets and budgets when selecting specialized grades.
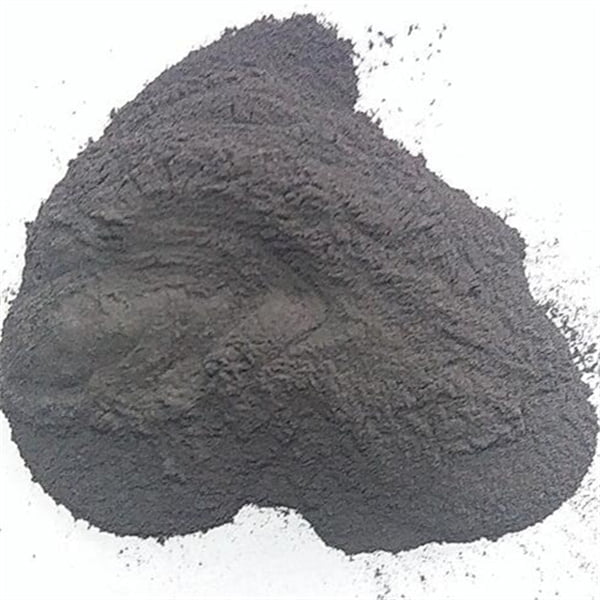
FAQs
Q: What is the benefit of metal alloy over pure elemental powders?
A: Alloying enables significantly enhancing key attributes like strength, corrosion resistance, hardness, conductivity etc over any single element’s intrinsic limitations through metallurgical mechanisms and Second Phase control.
Q: How small can metal alloy powder sizes get produced?
A: Inert gas atomization can generate nano-scale metal powders down below 10 nanometers at the leading edge of current commercial capabilities. Chemistries and morphologies remain an intense R&D area as new methods get pioneered.
Q: Is post-processing of powders mandatory before part fabrication?
A: Besides sieving into precise size fractions, additional conditioning like deoxidation, annealing, coating and blending can get utilized to modify powder characteristics assisting fabrication process performance, densification behavior and final component property targets.
Q: What dictates the cost difference between grades?
A: Processing intricacy, alloying elements pricing, R&D investments, production volume and specification requirements control pricing – exotic highly engineered powders prove far more expensive than common workhorse varieties.
Conclusion
This guide presented a holistic overview of metal alloy powder engineering materials capable of realizing next generation component performance far surpassing conventional metallurgical constraints through tailored chemistry and optimized processing. Please connect with an industry expert to discuss aligning specialized grades’ unique advantages to your targeted application requirements.
Share On
MET3DP Technology Co., LTD is a leading provider of additive manufacturing solutions headquartered in Qingdao, China. Our company specializes in 3D printing equipment and high-performance metal powders for industrial applications.
Inquiry to get best price and customized Solution for your business!
Related Articles
About Met3DP
Recent Update
Our Product
CONTACT US
Any questions? Send us message now! We’ll serve your request with a whole team after receiving your message.
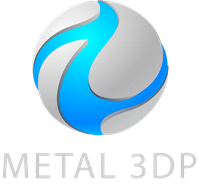
Metal Powders for 3D Printing and Additive Manufacturing