Metal Atomization Systems
Table of Contents
Metal atomization is a manufacturing process where metal is turned into powder form by breaking up molten metal into tiny droplets. This powder can then be used to manufacture parts through methods like metal injection molding, hot isostatic pressing, additive manufacturing, and more. Metal atomization systems are the equipment used to carry out this process.
Overview of Metal Atomization Systems
Metal atomization systems consist of mechanisms to melt metal stock, deliver the molten metal to an atomization area, break up the metal into fine droplets, and collect the solidified powder. Key components include furnaces, tundishes, delivery mechanisms, atomizers, cooling chambers, cyclone separators, bag filters, and powder collection systems.
There are two main types of atomization systems:
- Gas atomization – uses high pressure gas to break up the molten metal stream
- Water atomization – uses high pressure water to break up the molten metal
Gas atomization produces finer powders on average while water atomization offers higher production rates. Both methods can achieve reasonably high yields depending on the design and operating parameters.
metal atomization systems Composition
Component | Description |
---|---|
Furnace | Melts metal stock into liquid state through induction, combustion, etc. Common types are induction furnaces, electric arc furnaces. |
Tundish | Acts as a reservoir to hold the molten metal after it leaves the furnace. Provides continuous flow of metal to delivery system. |
Delivery system | Transfers molten metal from tundish to atomizer. Often uses pouring funnel, heated launder, or pressurized nozzle. |
Atomizer | Breaks up molten metal into droplets using gas or water jets. Various designs and number of jets. |
Cooling section | Allows powder to solidify after atomization before collection. Air or inert gas used as cooling media. |
Separation system | Captures fine powder particles while allowing cooling media to be recirculated. Uses cyclones, bag filters. |
Powder collection | Collects atomized powder for retrieval. Often drum or box containers, glove boxes, or conveyor belts leading to containers. |
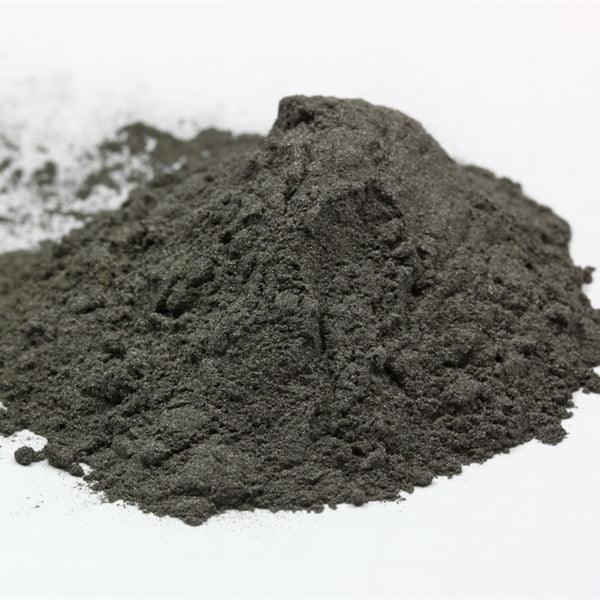
metal atomization systems Types
There are a few common atomizer designs used in commercial metal powder production:
Gas Atomizers
- Supersonic Gas Atomizer – Laval nozzles accelerate inert gas up to sonic velocities.
- Close-Coupled Gas Atomizer – Multiple gas jets impinging on molten metal stream.
- Free Fall Gas Atomizer – Molten metal stream falls freely through high velocity inert gas.
Water Atomizers
- Pressure Water Atomizer – High pressure water jets hit molten metal stream.
- Rotating Water Atomizer – Molten metal stream contacts spinning water jets.
- Submerged Water Atomizer – Water jets placed under molten metal stream surface.
Metal Atomizer Attributes
Attribute | Description |
---|---|
Gas type | Inert gases like nitrogen, argon used to prevent oxidation. Nitrogen most economical. |
Water pressure | 30-150 MPa pressure needed to properly atomize metals. |
Number of jets | More jets increases metal breakup but can reduce yield. Around 4-8 common. |
Jet arrangement | Round or rectangular jet patterns covering metal stream. Rectangular more uniform powder. |
Jet velocity | Faster inert gas velocities make finer powders. Optimal gas speed varies for each metal. |
Drop height | Height molten metal stream falls before hitting jets. Affects particle size distribution. |
Flow design | Smooth, laminar metal flow preferred to prevent splashing into droplets early. |
Nozzle design | Precisely machined nozzles in gas atomizers are crucial for performance. |
Cooling rate | Faster cooling makes finer powders. Depends on gas/water temperature and chamber. |
Separation efficiency | Higher separation rates increase yield. Self-inerting cyclones work well. |
Collection method | Closed systems prevent powder oxidation. Automated drum conveyors common. |
Metal Powder Characteristics
The properties of metal powder produced depends heavily on the atomization process parameters and conditions.
Powder Attributes
Attribute | Typical Range |
---|---|
Particle shape | Irregular, spherical, satellite structures |
Particle size | 1 micron to 1000 micron |
Particle size distribution | Gaussian, log-normal common |
Apparent density | Generally 30-80% of true density |
Tap density | Around 60-95% of true density |
Flow rate | Varies greatly with shape, size distribution |
Purity | 93-99.5% target range |
Oxygen content | 300-3000 ppm range |
Nitrogen content | 75-1500 ppm range |
Effect on Part Properties
Powder Attribute | Effect on Sintered/Printed Parts |
---|---|
Particle size | Finer powders increase density, reduce pores |
Size distribution | Wider distribution gives better packing density |
Particle shape | Spherical particles have better flow and packing |
Apparent density | Higher density increases green strength for handling |
Tap density | Higher density gives fewer shrinkage voids after sintering |
Purity | Higher purity reduces defects like inclusions |
Oxygen content | Above 3000 ppm can cause porosity issues |
metal atomization systems Applications
The fine metallic powders made via atomization are used across many industries to manufacture high performance parts.
Industry | Application Examples |
---|---|
Automotive | Engine components, gears, fasteners |
Aerospace | Turbine blades, airfoil components |
Biomedical | Orthopedic implants, surgical tools |
Electronics | Shielding, connectors, contacts |
Energy | Nuclear & turbine parts subjected to extreme environments |
Additive manufacturing | 3D printed final parts across all industries |
Popular metal atomization systems Used
Many alloys are atomized into powder form for part manufacturing. Here are some common metals and alloys atomized:
Material | Key Properties |
---|---|
Titanium alloys | High strength, low weight ratio. Biocompatibility. |
Nickel alloys | Retains properties at high temperatures. Corrosion resistance. |
Cobalt alloys | Biocompatibility. Wear resistance properties. |
Tool steels | High hardness levels after heat treatment. |
Stainless steels | Excellent corrosion resistance. |
Aluminum alloys | Light weight. Good thermal conductivity. |
Copper alloys | High thermal & electrical conductivity. |
Magnetic alloys | High permeabilities for magnetic applications. |
Metal Powder Suppliers & Pricing
There are a number of reputable suppliers that manufacture & distribute metal powders worldwide. Prices depend on alloy, particle size range, and quantity ordered.
Supplier | Price Ranges |
---|---|
AP&C | $50 – $1500 per kg |
Sandvik Osprey | $100 – $2000 per kg |
Carpenter Powder Products | $75 – $1800 per kg |
Praxair Surface Technologies | $250 – $2500 per kg |
Höganäs | $45 – $1600 per kg |
ECKA Granules | $80 – $1200 per kg |
Higher performing alloys or finer control over powder size distribution demands higher prices, while more common metals and alloys are more economical at production volumes.
Metal Atomization vs Other Methods
Method | Advantages | Limitations |
---|---|---|
Metal atomization | – Finer powders – Higher purity – Range of alloys | – High capital costs – Requires significant processing expertise |
Electrolytic process | – Very fine & clean powders | – Limited to conductive alloys – Expensive |
Mechanical attrition | – Simple & inexpensive – Wide range of metals | – Lower achievable fineness – Higher oxidation |
Chemical precipitation | – Pure elemental & alloyed powders | – Powder agglomeration issues – Potential contamination |
Thermal spraying | – Can produce spherical powder | – Oxide inclusions- Broad size distributions |
Atomization offers reasonably fine and clean powders across a wide range of alloys at good production volumes. Safety precautions are necessary when handling fine metallic powders.
Key Considerations for Selection
Important factors guiding metal atomization system selection include:
Factor | Description |
---|---|
Production rate | Required powder output in kg/hr. Defines capacity. |
Target particle size | Needs defined fineness, distribution. Impacts yield, cost. |
Alloy composition | Most systems handle a range of alloys. May influence choice of melting method, atomizer, gas/water pressures. |
Product quality | Purity levels, oxygen pickup limits, size consistency requirements dictate parameters. |
Handling considerations | Closed powder handling preferred. Some metals pose health risks. |
Powder end use | Part property requirements – density/porosity, fluidity, shape factors. |
Operating costs | Utility inputs for melting, gases, water. Labor, maintenance expenses. |
Safety | Pressure vessels for liquids/gases require specific regulation compliance. |
Environmental impact | Gas emissions, water use/disposal considerations apply. |
Careful determination of throughput requirements, quality metrics, operating conditions, safety parameters, and costs based on end part requirements is necessary.
metal atomization systems Maintenance
Proper maintenance is required to keep atomization equipment performing optimally.
Component | Maintenance Activities | Frequency |
---|---|---|
Furnace | Inspect refractory & heating elements. Replace as needed. | 6-12 months |
Nozzles | Inspect nozzle jet openings for wear/clogs. | Monthly |
Water filters & lines | Flush lines & replace filters regularly. | 2-4 weeks |
Gas lines & valves | Check for leaks, blockages. Confirm pressures. | 2-4 weeks |
Separators | Inspect filter medium condition & seals. | 4-6 months |
Controls & sensors | Check calibration. Test interlocks & responses. | 6-12 months |
Powder collector | Inspect container condition & seals. Confirm inert gas levels for closed systems. | Monthly |
System interiors | Clean built-up metal dusts throughout. More frequent closer to metal stream paths. | Monthly |
Detailed equipment monitoring, preventive & predictive maintenance minimizes unexpected interruptions in production.
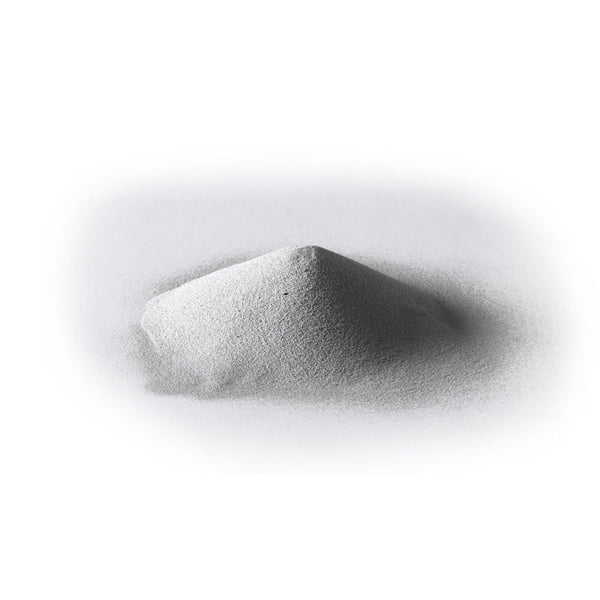
FAQs
Q: What is an appropriate level of automation & control for metal atomization systems?
A: A high degree of automation in material feed, process monitoring and control is recommended for consistent powder production and safety. Key process variables like temperatures, pressures, gas flows should have automatic feedback control. System oversight, parameter tuning and manual operation mode is still prudent.
Q: How to determine if gas atomization or water atomization is preferred for an application?
A: Water atomization offers much higher metal throughput rates compared to gas atomization. But gas atomization can achieve finer average powder sizes suitable for microstructured parts. For typical MIM powders above 15 microns, water atomization is preferred for economy.
Q: What safety measures are recommended for operating atomization systems?
A: Proper personnel protective equipment for handling high pressure systems and fine powders is mandatory. Water atomization systems should have splash guards. Closed powder handling with inert gas glove boxes, automated powder collectors improves safety. Lockouts, access restrictions, emergency stops critical.
Q: What causes common powder production problems in atomization?
A: Irregular powder sizes & satellite particles often stem from uncontrolled metal stream flows. Contamination can result from nozzle wear, degraded filter media or leaks. Chamber & separator fouling from overflows reduces yield over time. Monitoring & optimizing flow parameters is key.
Q: What expertise is required to effectively operate atomization systems?
A: While controls automation reduces manual burden, trained metallurgical or materials science engineers familiar with powder production are ideal to oversee equipment. Mechanical & electrical engineers needed for maintenance & troubleshooting. Operators should receive proper metal powder handling training.
Share On
MET3DP Technology Co., LTD is a leading provider of additive manufacturing solutions headquartered in Qingdao, China. Our company specializes in 3D printing equipment and high-performance metal powders for industrial applications.
Inquiry to get best price and customized Solution for your business!
Related Articles
About Met3DP
Recent Update
Our Product
CONTACT US
Any questions? Send us message now! We’ll serve your request with a whole team after receiving your message.
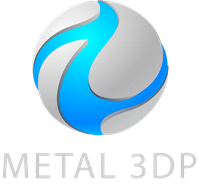
Metal Powders for 3D Printing and Additive Manufacturing