Metal Powder 3D Printers
Table of Contents
Overview
Metal powder 3D printers use a laser or electron beam to selectively melt and fuse metallic powder into a solid 3D object. This additive manufacturing technology enables complex geometries and lightweight parts to be created directly from 3D CAD data.
Compared to traditional subtractive methods like CNC machining, metal 3D printing can construct intricate designs without the typical constraints of tool access or high part counts from assembly. It provides design freedom and reduced time-to-market for lightweight components across aerospace, automotive, medical, and general industrial applications.
However, the process can be slower and more expensive per part depending on volume requirements. Achieving dense, void-free components with the desired mechanical properties requires optimizing multiple printing parameters and post-processing steps.
Types of Metal Powder 3D Printers
There are two main technologies used in metal powder bed fusion – Direct Metal Laser Sintering (DMLS) and Electron Beam Melting (EBM). The key differences lie in the heat source, atmospheric conditions, powder options, and applications:
Parameter | DMLS | EBM |
---|---|---|
Heat Source | Fiber laser | Electron beam |
Atmosphere | Inert argon | Vacuum |
Materials | Al, Ti, Ni alloys, tool steels | Ti alloys, some Ni alloys |
Resolution | Higher, thin walls down to 0.3mm | Moderate, minimum wall 0.8mm |
Accuracy | ± 0.1-0.2% with 20-50 micron detail | ± 0.2% with 50-200 micron detail |
Surface Finish | Smooth as-printed surface | Comparatively rough surface |
Speed | Moderate build rates | Very fast build rates |
Applications | Dental, medical, aerospace components | Orthopedic implants, aerospace structures |
DMLS Printers use a high power fiber laser precisely controlled by galvo scanners or mirrors to selectively melt microscopic layers of metallic powder in an inert argon atmosphere. Complex and delicate structures with finer details can be produced to a high accuracy and smooth surface finish.
Popular DMLS systems include the EOS M series, GE Additive Concept Laser machines, Renishaw RenAM 500 quad laser printer, and the open-source Lulzbot TAZ Pro.
EBM Printers harness an electron beam as the high intensity heat source to fully melt metal powder layers in a vacuum. The fast scanning beam enables very high build rates, but coarser resolution around 100 microns.
EBM can efficiently print porous structures used as bone implants. Leading EBM systems are manufactured by ARCAM, now a GE Additive brand, which builds the Arcam EBM Spectra H, Q10plus, and Q20plus printers.
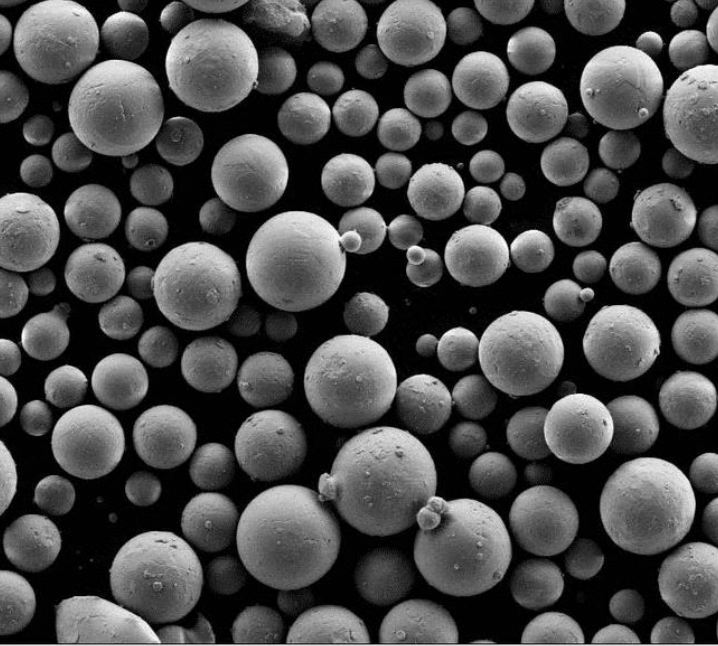
Metal Powder Materials
Most commercial metal powders for powder bed 3D printing meet the following specifications:
Parameter | Typical Range |
---|---|
Particle size | 10 – 45 microns |
Flowability | Suitable for layer deposition |
Purity | >99.5% |
Shape | Spherical, Satellite, Irregular |
Apparent density | 60-80% of solid density |
Tap density | Up to 98% solid density after compaction |
Common alloys used are titanium, aluminum, stainless steel, nickel superalloys, and cobalt-chrome. Many are customized for AM processes and optimized after repeated recycling.
Grade 5 titanium Ti6Al4V is popular for its strength-to-weight ratio and biocompatibility. Aluminum AlSi10Mg alloy and maraging steel components have high strength. Cobalt chrome is used extensively for dental and medical implants.
Nickel superalloys like Inconel 718 and 625 offer excellent heat and corrosion resistance at high temperatures. Tool steels can be hardened after printing to 60 HRC for extreme wear resistance.
Exotic metal powders are being qualified as the technology expands – aluminum-magnesium-scandium, copper-nickel-tin, precious metals like gold, platinum and silver have been printed.
Printing Process
Though DMLS and EBM vary in hardware, the generic metal powder bed fusion steps are:
- 3D CAD model designed accounting for AM design principles
- STL file processed through slicing software
- Powder deposition mechanism spreads measured layer
- Laser or ebeam scans slice pattern according to file
- Process repeats until full object is built on a baseplate
- Excess powder supports part and absorbs stresses
- Printer recovers unmelted powder for reuse after filtration
- Completed 3D printed build removed from machine
For metals, the following post-processing is critical prior to putting a part in service:
- Support removal via cutting, blasting, or chemical dissolution
- Hot isostatic pressing to eliminate internal voids
- Heat treatments for altering microstructure
- Surface finishing – bead blasting, grinding, polishing
- Precision machining to meet tolerance requirements
- Quality checks per application – dimensional accuracy, density, mechanical properties, microstructure, surface defects
3D printing metals opens up key applications due to:
Design Complexity – intricate cooling channels, lattices, bionic shapes
Customization – patient-specific implants, tailored alloys
Weight Reduction – lighter aero and auto components
Part Consolidation – integrated assemblies printed as one part
Rapid Prototyping – faster iteration of designs
Pros and Cons of Metal 3D Printing
Advantages | Disadvantages |
---|---|
Design freedom for complex, organic shapes | Relatively slow build speeds |
Lightweighting by optimizing mass distribution | Limitations on part size based on printer model |
Faster time-to-market of products | Currently expensive technology for production |
Customization and personalization | Extensive post-processing required |
High strength and hardness attainable | Anisotropic material properties |
Intricate lattice and foam structures | Must design to accommodate AM principles |
Buyers Guide – Metal Powder Bed 3D Printers
Choosing the best metal powder bed fusion 3D printing system for industrial manufacturing depends on:
1) Build Envelope: Maximum part dimensions – popular sizes from 100-500mm cubes
2) Laser / Electron Beam: Power rating from 50W-5kW; higher power enables faster builds
3) Materials: Cost, mechanical requirements, ease of post-processing, certification levels
4) Accuracy/Surface Finish: Dimensional precision and tolerances achievable; target roughness
5) Automation: Powder handling systems, sieving, recycling, and controls software
6) Price: Equipment cost ranging from $100k to over $1M; consider operating costs
7) Lead Time + Service: Install schedules from vendors; access to applications expertise
Specification | Beginner | Professional | Industrial |
---|---|---|---|
Build Volume | 5 x 5 x 5 inches | 10 x 10 x 12 inches | 750 x 380 x 380 mm |
Laser Power | 100-200 W | 400-500 W | 1 kW |
Layer Height | 20-50 μm | 20-30 μm | 20-50 μm |
Materials | stainless steels | ~10 metal options | Ti, Al, Ni alloys, more |
Accuracy | ± 0.5-1 mm | ± 0.1-0.2 mm | ± 0.075-0.2 mm |
Surface Roughness | 15 μm Ra | 7-10 μm | 5-15 μm |
Automation | Manual powder handling | Automated depowdering | Closed-loop powder processing |
Price Range | $100-250K | $300-750K | Over $1 million |
Applications of Metal 3D Printing
Aerospace
- Lightweighted aerostructures and components – titanium and aluminum alloys
- Integrated assemblies consolidated into one printed part
- Complex engine sections with conformal cooling channels
- Quick prototypes for design validation
Medical Devices
- Custom cranial, spinal, and orthopedic implants – titanium and cobalt chrome
- Bio-models for surgical planning and guides
- Patient matching implants and instrumentation
Automotive
- Lightweight chassis and structural parts in aluminum and steel
- Personalized automotive components
- Complex parts consolidation – engine blocks with cooling
Industrial Manufacturing
- Lightweighting components and structural optimization
- Part consolidation to improve functionality
- On-demand spare parts with reduced lead times
- Metal injection molding tooling inserts with conformal cooling
Suppliers of Metal Powder Bed 3D Printers
Manufacturer | Models | Description |
---|---|---|
GE Additive | Concept Laser M2, Mlab, Xline 2000R | Laser powder bed printers acquired from Concept Laser |
3D Systems | DMP Flex 350, Factory 500 | Laser melting printers for metals with dual lasers |
Renishaw | RenAM 500M | Modular laser system with quad laser configuration |
SLM Solutions | SLM 280 2.0, SLM 500 HL | Selective laser melting machines, pioneers in powder bed fusion |
Trumpf | TruPrint 3000 | Automated laser metal 3D printer series made in Germany |
AddUp | FormUp 350 | Modular, double laser printer targeting aerospace |
Sisma | Sisma MYSINT100 | Low-cost introductory metal laser melting system |
Additive Industries | MetalFAB1 | High productivity metal AM system for series production |
OR Laser / Matsuura | LUMEX Avance-25 | Hybrid subtractive + laser metal 3D printer |
Mazak | INTEGREX i-AM | Done-in-one hybrid metal 3D printer with milling |
DMG Mori | Lasertec 12 SLM | Powder nozzle + Laser metal 3D printer + 5 axis milling |
ARCAM / GE Additive | Arcam Q20plus | EBM technology printer for orthopedic implants |
Velo3D | Sapphire | SupportFree metal printer for low angle features |
Desktop Metal | Production System | Binder jetting + sintering workflow for metal 3D printing |
Markforged | Metal X | Bound metal deposition printer affordable for workshops |
Tiertime | UP300M | Laser powder bed fusion machine ‘made in China’ |
Farsoon | FS721M | Industrial grade metal powder bed system |
3DGence | DOUBLE P255 | Laser & EBM metal printer combo hybrid system |
Aidro | hydrim M3 | Multi-laser metal printer focused on hydraulics |
Aurora Labs | RMP-1 | Multi-laser printer targeting high throughput |
Metal Powder for 3D Printing – Suppliers
Company | Products | Description |
---|---|---|
AP&C | Titanium, nickel, cobalt alloys | Powders for aerospace and medical |
Carpenter Additive | 17-4PH, 316L, cobalt chrome, Inconel | Broad portfolio of 3D printing alloys |
Sandvik Osprey | Ti6Al4V, stainless steels, Ni alloys | Spherical powders customized for AM |
Praxair | Titanium, nickel, tool steel alloys | High purity reactive and refractory metals |
LPW Technology | Aluminum alloy powders | Specialists in aluminum materials |
Höganäs | Stainless steels, soft magnetic alloys | Shaped metal powders from atomization |
EOS | EOS MaragingSteel MS1, StainlessSteel 316L | Materials and parameters from system OEM |
Cost Analysis
Like most additive technologies, metal powder bed fusion is currently more expensive for individual parts produced compared to conventional mass manufacturing.
However, it offers cost savings from part consolidation, lightweighting, and accelerated time-to-market during product development.
Cost Factor | Relative magnitude |
---|---|
Metal powder material cost | $100-$500/kg |
Printer equipment amortized cost | ~$50/build hour |
Labor for preprocessing | ~2-5 hrs per 20 parts |
Post processing operations | 5X – 10X material cost |
Total part cost today | $100-$2000 per kg |
CNC machined part cost | $50-$500 per kg |
Future production part cost | ~$20-50 per kg |
With ongoing developments in automation, faster build rates, and batch production, metal AM part costs are projected to become cost competitive with machined components in high value industries.
Future Outlook
Metal powder bed fusion will continue gaining adoption for small to medium sized parts that push the limits of conventional manufacturing constraints.
Ongoing trends in metal powder 3D printing include:
- Larger build envelopes above 500mm cubes
- Additional validated alloys like copper, gold, aluminum
- Enhanced material properties and surface finishes
- Faster laser scanning up to 10 m/s for higher volume
- More repeatable mechanical performance across machines
- Expanded range of material grades on a single system
- Improved powder handling and closed-loop processing
- Additional hybrid systems with integrated machining
- High quality inline monitoring and metrology
- Industry specific printer variants and process parameters
- Additional high productivity systems for series production
As the technology proliferates and becomes more cost competitive despite its complexity, AM will transform manufacturing across sectors enabling the mass customization of end-use metal parts on demand.
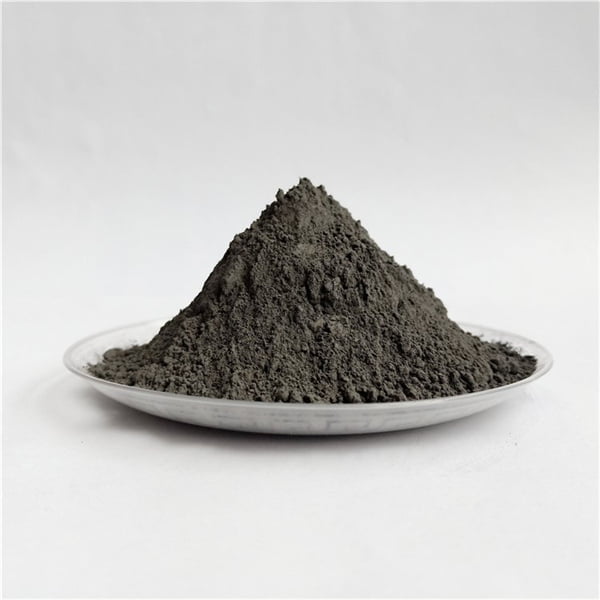
FAQ
Q: How expensive are metal powder 3D printers and associated operating costs?
A: Industrial metal printing systems range from $100,000 to $1M+. Operating costs the highest among AM processes – powder materials, inert atmospheres, and finishing account for bulk of spending.
Q: What size metal parts can be 3D printed today?
A: Dimensions up to 500 x 500 x 500 mm are possible, though ~300 mm per side is average. Many industrial components fall within this range. Larger systems above a meter long also exist.
Q: What materials advanced metals are being developed for AM beyond conventional steels and titanium?
A: Metal AM development is expanding into refractory metals like tungsten, molybdenum, tantalum as well as precious metals used in jewelry including gold, silver and platinum alloys.
Q: How good is the accuracy and surface finish coming off a metal powder bed 3D printer?
A: Dimensional accuracy after post-processing is around ±0.1-0.3% while tolerances of ±0.05mm are achievable. Vertical surfaces exhibit surface roughness of 5-15 microns initially. Higher surface quality involves additional milling/polishing.
Q: What temperatures and pressures are used in sintering metal powder prints to full density?
A: Depends on alloy, but common HIP and sinter parameters are: 1100-1300°C temperature at 100-200 MPa for 2-4 hrs to achieve >99% solid metal density. SLM parts have reached 99.9% solidity.
Q: Which metal 3D printing process is fastest for series production?
A: In terms of build rate speed, electron beam melting (EBM) systems produce parts over four times faster than laser based processes, making them attractive for metal part manufacturing. Laser systems are working to catch up.
Q: Does metal powder bed 3D printing produce isotropic or anisotropic material parts?
A: Due to extreme thermal gradients between melted powder and surrounding areas, metals made by powder bed exhibit anisotropic properties where horizontal tensile figures differ from vertical ones by ~30% typically.
Q: Is heat treating required for DMLS and EBM metal printed parts?
A: Yes, heat treatments are necessary to relieve internal stresses from the layer-by-layer construction and bring alloys to target mechanical specifications regarding hardness, ductility etc.
Q: How sustainable is powder bed metal 3D printing compared to traditional metal fabrication?
A: AM systems reuse over 90% of metal powder excess during builds. And printed components require 25-50% less base material weight due to lightweight, optimized designs – significant sustainability benefits.
Share On
MET3DP Technology Co., LTD is a leading provider of additive manufacturing solutions headquartered in Qingdao, China. Our company specializes in 3D printing equipment and high-performance metal powders for industrial applications.
Inquiry to get best price and customized Solution for your business!
Related Articles
About Met3DP
Recent Update
Our Product
CONTACT US
Any questions? Send us message now! We’ll serve your request with a whole team after receiving your message.
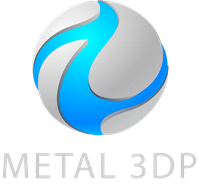
Metal Powders for 3D Printing and Additive Manufacturing