Metal Powder Atomization
Table of Contents
Metal powder atomization is a critical technology for producing fine metallic powders with specialized characteristics. This guide covers the fundamentals, methods, applications and commercial landscape of metal powder atomization.
What is Metal Powder Atomization?
Metal powder atomization refers to industrial processes that turn molten metal alloys into fine liquid droplets, rapidly solidifying them into powder particles.
It involves:
- Melting metals into a liquid state
- Generating a molten metal stream
- Breaking up the metal into discrete droplets
- Solidifying the droplets into powder
- Collecting and sieving the powder
Atomization is used to produce metal powders with unique compositions, sizes, shapes and microstructures suitable for advanced applications.
Key Atomization Benefits
- Custom alloy compositions
- Controlled particle sizes
- Spherical powder shapes
- Defect-free powder metallurgy
- Novel microstructures
- Custom powder properties
Common materials made through atomization include various alloy systems:
- Stainless steels
- Tool steels
- Cobalt alloys
- Nickel alloys
- Titanium alloys
- Tungsten alloys
- Precious metals
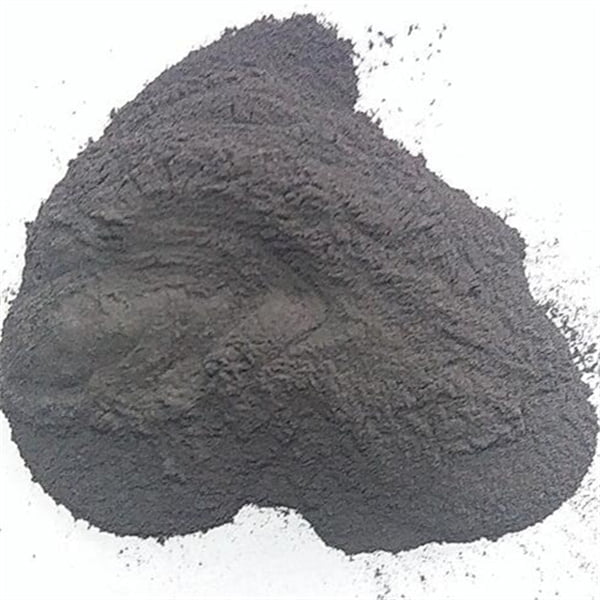
Metal Powder Atomization Methods
There are 5 main commercial atomization techniques:
Gas Atomization
- Uses pressurized inert gas jets
- Common gases: Nitrogen, Argon, Helium
- Produces spherical, smooth powders
Water Atomization
- Uses high pressure water jets
- Lower cooling rates than gas
- Irregular powder shapes
Centrifugal Atomization
- Molten metal poured on spinning disc
- Economical powder production
- Medium cooling rates
Ultrasonic Atomization
- Uses ultrasonic vibrations
- Specialized lab-scale method
- Nanoparticle production
Electrode Induction Melting
- Electrode vaporization in inert gas
- Limited niche applications
- Lower productivity
Atomization Method Comparison
Method | Particle Shape | Size Range | Productivity | Cost |
---|---|---|---|---|
Gas Atomization | Spherical | 10-150 μm | High | High |
Water Atomization | Irregular | 20-400 μm | Very High | Low |
Centrifugal Atomization | Semi-spherical | 20-250 μm | Medium | Medium |
Ultrasonic Atomization | Spherical | 1-100 nm | Very Low | High |
Electrode Induction Melting | Mixed | 10-100 μm | Low | Medium |
Metal Powder Atomization Process
Commercial metal powder atomization involves a series of tightly controlled steps under inert atmosphere:
1. Raw Material Selection
- Pure metals or master alloys
2. Melting
- Vacuum induction melting up to 2000°C
- Precise alloy chemistry inputs
3. Atomization
- Pouring molten metal into atomizing zone
- Breaking up metal stream into droplets
- Quenching and solidifying droplets
4. Powder Collection
- Settling chamber to collect powder
- Cyclone separators
5. Sieving
- Classifying powder into size fractions
- Further annealing if needed
6. Quality Control
- Sampling and testing per standards
- Packaging and shipment
The production environment must have no oxygen or moisture contamination. Operational parameters like temperature profiles, gas pressures and flow dynamics are closely monitored.
Metal Powder Atomization Applications
Some major applications taking advantage of atomized metal powder include:
Additive Manufacturing
- Selective laser melting
- Binder jetting
- Electron beam melting
Metal Injection Molding
Thermal Spray Coatings
Hot Isostatic Pressing
Brazing Materials
Catalysts
Powder Metallurgy
- Press and sinter tooling
- High performance parts
- Porous structures
- Soft magnetic composites
Atomized powder enables emerging technologies like additive manufacturing across industries:
Industry | Applications | Benefits |
---|---|---|
Aerospace | Turbine blades, impellers, airframe components | High strength-to-weight ratio |
Automotive | Gears, connecting rods, chassis parts | Increased efficiency |
Medical | Joint replacements, implants, precision tools | Biocompatibility |
Electronics | Shielding, contacts, sensors | Enhanced performance |
Oil & Gas | Downhole tools, valves | Wear and corrosion resistance |
Metal Powder Atomization Materials
Many alloy systems and material types are processed through atomization:
Stainless Steels
- Austenitic grades like 304, 316, 317
- Ferritic and martensitic grades
- Custom compositions available
Tool Steels
- H13, P20, D2, M2 grades
- High wear resistance
- High hardness after heat treatment
Cobalt Alloys
- Biomedical CoCrMo alloys
- Wear resistant StelliteTM alloys
Nickel Alloys
- Corrosion resistant alloys like Inconel 625
- Heat resistant superalloys
Titanium Alloys
- Ti6Al4V grade 5 titanium
- Commercially pure titanium
Refractory Metals
- Niobium, molybdenum, tungsten
- Very high melting points
Metal Powder Atomization: Specifications
Critical specifications for atomized metal powders include:
Particle Size Distribution
- Typically 10 to 150 microns
- Application method dictates ideal size
- Sieving classifies desired fractions
Particle Shape
- Spherical, smooth morphologies
- Impact compaction, flowability
Chemistry
- Precisely blended compositions
- Custom alloys designed for properties
Density
- Up to 98% theoretical density
- Density optimization modeling
Surface Area
- Relatively high surface area
- Impacts reactivity, solubility
Microstructure
- Controlled grain sizes and phases
- Rapid solidification dynamics
Parameter | Significance | Measurement Technique |
---|---|---|
Particle Size Distribution | Controls downstream processability | Laser diffraction particle size analyzer |
Particle Shape | Impacts density and flow behavior | Scanning electron microscopy |
Chemistry | Achieves target material performance | Optical emission spectrometry, ICP mass spectroscopy |
Density | Related to achievable properties | Gas pycnometry, apparent density tester |
Surface Area | Affects reactivity and solubility | Gas absorption surface area analyzer |
Microstructure | Determines mechanical properties | X-ray diffraction, metallography |
Metal Powder Atomization Cost Analysis
Atomized metal powder is more expensive than conventional raw materials due to specialized processing:
- Small batch production
- Complex quality control
- Manual handling steps
- Equipment maintenance
- Consumables and energy
- R&D expense recovery
Cost Drivers:
- Feedstock metal costs
- Quality conformance
- Order size
- Particle size
- Exotic alloys
Economics:
- Raw materials: 30% of total cost
- Processing: 70% of total cost
Price Ranges:
Material | Price per kg |
---|---|
Stainless Steels | $20-$250 |
Tool Steels | $25-$150 |
Titanium Alloys | $70-$1000 |
Cobalt Alloys | $100-$500 |
Nickel Alloys | $100-$2000 |
Tungsten Alloys | $800-$5000 |
Business viability relies on maximizing production capacity utilization and end-to-end yield.
Metal Powder Atomization: Pros vs Cons
Benefits of Metal Powder Atomization
- Excellent flow characteristics
- Narrow particle size distribution
- Customizable alloy compositions
- Spherical powder shape possible
- Controlled microstructures
- Enables emerging technologies
Challenges of Metal Powder Atomization
- High production cost
- Limited batch sizes
- Stringent safety precautions
- Complex quality conformance
- Qualified operator experience vital
- Costly trial-and-error development
- Handling fine reactive powders
Advancements continue expanding the horizons for specialty materials made via atomization.
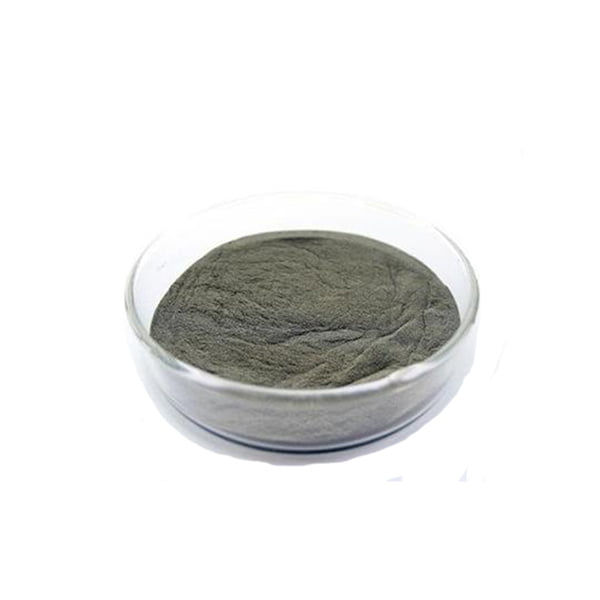
FAQs
Q: How are metal powders atomized?
A: Metal powders are atomized by breaking up a molten metal stream into fine droplets using gas jets, water jets or centrifugal forces, rapidly solidifying them into powder.
Q: What is water atomization?
A: In water atomization, a thin stream of molten metal alloy is struck by high-pressure water jets which break it up into small droplets. The droplets solidify into irregularly shaped powder particles as they fall through the water.
Q: What metals can be atomized into powders?
A: Many engineering metals like tool steels, stainless steels, nickel alloys, titanium alloys, tungsten alloys and precious metals can be atomized into fine spherical powders or irregular powders using appropriate techniques.
Q: What particle sizes can metal powder atomization achieve?
A: Conventional metal powder atomization can produce powders from around 10 microns to over 150 microns. Specialized nozzles and processing conditions allow particle sizes below 5 microns.
Q: How much does metal powder atomization cost?
A: Due to small volumes and specialized equipment, atomized metal powder costs between 5x to 10x more than standard raw metal stock per unit weight, with pricing ranging from $50 per kg to over $2000 per kg depending on composition and quality.
Q: Can you atomize multiple metals simultaneously into an alloy?
A: Yes, atomization allows melting and alloying various metals into customized compositions which solidify into an alloy powder with the desired elemental ratios and advanced metallurgical properties.
Q: What hazards are associated with metal powder atomization?
A: Fine metal powders may spontaneously combust, explode or be toxic if inhaled. Strict safety protocols for inert gas purging, explosion proof electrical equipment, pressurized nozzles, emergency ventilation and operator PPE are enforced.
Q: What machines are used in metal powder atomization?
A: The main metal powder atomization equipment includes vacuum induction furnaces, tundish pouring systems, gas and water jet nozzles, atomizing towers, cyclone separators, screening machines, powder drying ovens and sieving station.
Conclusion
Metal powder atomization is an intricate, multi-faceted manufacturing technique essential for new material development crossing industry boundaries. Persistent metallurgical challenges continue driving process refinements through extensive tribology research and plant trials. With broader collaboration across the metal powder value chain harnessing latest automation technologies, atomization promises to elevate manufacturing—not eliminate it.
Share On
MET3DP Technology Co., LTD is a leading provider of additive manufacturing solutions headquartered in Qingdao, China. Our company specializes in 3D printing equipment and high-performance metal powders for industrial applications.
Inquiry to get best price and customized Solution for your business!
Related Articles
About Met3DP
Recent Update
Our Product
CONTACT US
Any questions? Send us message now! We’ll serve your request with a whole team after receiving your message.
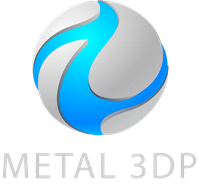
Metal Powders for 3D Printing and Additive Manufacturing