Mold Steel 3D Printing Metal Powder
Table of Contents
The world of manufacturing is undergoing a significant transformation, and at the heart of this change lies the remarkable technology of 3D printing. But 3D printing isn’t just for creating plastic trinkets anymore. It’s rapidly making inroads into the realm of metalworking, particularly with mold steel 3D printing metal powder. This innovative material is opening doors for designers and engineers, enabling the creation of complex, high-performance molds with unprecedented flexibility and efficiency.
the Power of Mold Steel 3D Printing Metal Powder
Imagine a scenario where you can design a mold with intricate features, internal channels, and geometries that would be impossible or incredibly expensive to achieve with traditional machining techniques. Mold steel 3D printing metal powder makes this a reality. It’s a revolutionary material specifically formulated for use in 3D printing processes like Selective Laser Melting (SLM) and Electron Beam Melting (EBM). These processes use a high-powered laser or electron beam to selectively melt and fuse layers of metal powder, building the mold layer by layer according to a digital design.
The benefits of using mold steel 3D printing metal powder are numerous:
- Unmatched Design Freedom: Unlike traditional subtractive manufacturing methods like CNC machining, 3D printing allows for the creation of highly complex mold geometries with internal channels, conformal cooling passages, and intricate details. This opens doors for innovative mold designs that enhance performance and efficiency.
- Reduced Lead Times: 3D printing eliminates the need for complex tooling and lengthy machining processes. This translates to significantly faster lead times for mold production, allowing you to get your product to market quicker.
- Cost-Effectiveness for Low-Volume Production: For low-volume production runs, 3D printing molds can be a more cost-effective option compared to traditional methods. The elimination of expensive tooling and the ability to iterate on designs rapidly contribute to overall cost savings.
- Lightweight Molds: Mold steel 3D printing powders can be formulated to create lighter weight molds compared to their traditionally machined counterparts. This can be advantageous for applications where weight reduction is crucial.
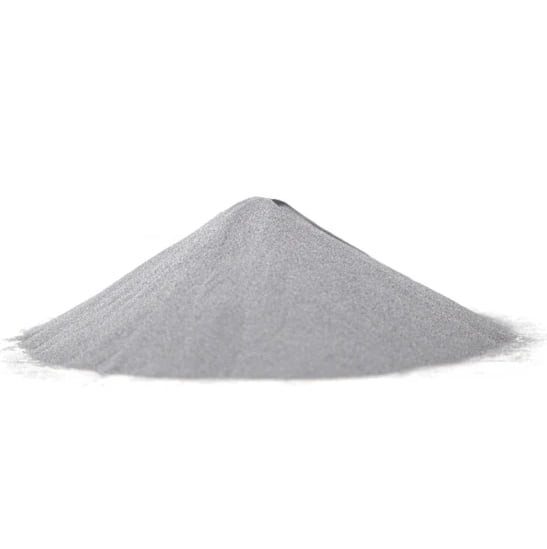
Here’s a table summarizing the key characteristics of mold steel 3D printing metal powder:
Property | Description |
---|---|
Material Type | Metal powder specifically formulated for 3D printing processes like SLM and EBM |
Composition | Primarily consists of iron with varying amounts of other elements like chromium, nickel, molybdenum, and others depending on the specific type of mold steel |
Properties | High strength, good ductility, excellent wear resistance, thermal stability |
Benefits | Enables creation of complex mold geometries, reduces lead times, cost-effective for low-volume production, lightweight molds |
Various Mold Steel 3D Printing Metal Powder Options
With the growing popularity of mold steel 3D printing, a diverse range of metal powders are available to cater to specific application needs. Here’s a closer look at ten prominent options:
1. 17-4 PH Stainless Steel (UNS 17400):
This precipitation-hardening stainless steel powder offers a good balance of strength, ductility, and corrosion resistance. It’s a popular choice for molds used in applications like injection molding of plastic parts and low-pressure casting of aluminum.
2. 316L Stainless Steel (UNS 31603):
This widely used stainless steel powder boasts excellent corrosion resistance and good weldability. It’s suitable for molds used in applications requiring high chemical resistance, such as food and medical applications.
3. Maraging Steel (UNS 1.2709):
Known for its exceptional strength and toughness, maraging steel powder is ideal for molds used in demanding applications like die casting and high-pressure molding. Maraging steels achieve high strength through a precipitation hardening process that allows for near net shape printing with minimal distortion.
4. H13 Tool Steel (AISI H13):
A popular choice for hot work tooling applications, H13 tool steel powder offers excellent hot hardness, wear resistance, and dimensional stability. It’s well-suited for molds used in processes like die casting and injection molding of high-temperature thermoplastics.
5. A2 Tool Steel (AISI A2):
This air-hardening tool steel powder exhibits good wear resistance and toughness. It’s a versatile option for molds used in cold work applications like punching, shearing, and bending.
6. D2 Tool Steel (AISI D2):
Offering exceptional wear resistance and high hardness, D2 tool steel powder is ideal for molds used in cold work applications that require sharp cutting edges, such as blanking dies and cold forming
A2 Tool Steel (AISI A2) vs. D2 Tool Steel (AISI D2)
While both A2 and D2 tool steel powders are suitable for cold work applications, they have some key differences:
- Hardness: D2 tool steel powder boasts a higher achievable hardness compared to A2. This translates to better wear resistance for applications involving abrasive materials or high contact pressures.
- Toughness: A2 tool steel powder offers superior toughness compared to D2. This makes it a better choice for applications where the mold may experience shock loads or impacts.
- Machinability: A2 tool steel powder is generally easier to machine after printing compared to D2. This can be beneficial for applications requiring post-processing to achieve tighter tolerances or finer surface finishes.
Choosing between A2 and D2 tool steel powders depends on the specific application requirements. If wear resistance is the top priority, D2 might be the better option. However, if toughness or machinability are crucial factors, A2 could be a more suitable choice.
Here’s a table summarizing the key differences between A2 and D2 tool steel powders:
Property | A2 Tool Steel (AISI A2) | D2 Tool Steel (AISI D2) |
---|---|---|
Hardness (HRC) | 58-62 | 60-64 |
Toughness | Higher | Lower |
Wear Resistance | Good | Excellent |
Machinability | Easier | More Difficult |
Applications | Punching, shearing, bending | Blanking dies, cold forming |
7. Copper Alloys:
Copper alloys like CuCr1Zr (copper-chromium-zirconium) offer excellent thermal conductivity, making them ideal for molds requiring efficient heat transfer. This is particularly beneficial for applications involving fast cycle times or materials with high melting points.
8. Nickel Alloys:
Nickel alloys like Inconel 625 are known for their exceptional high-temperature strength, corrosion resistance, and oxidation resistance. These properties make them suitable for molds used in demanding applications like investment casting and high-temperature molding processes.
9. Titanium Alloys:
Titanium alloys like Ti6Al4V offer a unique combination of high strength, low weight, and excellent corrosion resistance. These attributes make them ideal for applications where weight reduction and chemical resistance are critical, such as aerospace and medical applications.
10. Custom Formulations:
Several manufacturers offer custom formulations of mold steel 3D printing metal powders tailored to specific application requirements. These custom powders can be formulated to achieve a unique balance of properties like strength, ductility, wear resistance, and thermal conductivity.
The choice of mold steel 3D printing metal powder depends on various factors, including the intended application, required properties, post-processing considerations, and budget.
Applications of Mold Steel 3D Printing Metal Powder
The applications of mold steel 3D printing metal powder are vast and continue to expand as the technology matures. Here’s a table showcasing some prominent applications:
Application | Benefits of Using Mold Steel 3D Printing Metal Powder |
---|---|
Injection Molding | Enables creation of complex mold geometries with conformal cooling channels for improved cycle times. |
Die Casting | Allows for the production of high-strength, wear-resistant molds for demanding applications. |
Blow Molding | Facilitates the creation of lightweight molds for efficient blow molding processes. |
Investment Casting | Enables the production of intricate molds for high-quality investment castings. |
Prototyping and Low-Volume Production | Offers a rapid and cost-effective way to create functional prototypes and molds for low-volume production runs. |
Medical and Dental Applications | Provides the ability to create biocompatible molds for medical implants and dental prosthetics. |
The potential applications of mold steel 3D printing metal powder are virtually limitless. As the technology evolves and the cost of materials and equipment decreases, we can expect to see even wider adoption across various industries.
Specifications, Sizes, Grades, and Standards
Here’s a table outlining the specifications, sizes, grades, and standards typically associated with mold steel 3D printing metal powder:
Property | Description |
---|---|
Particle Size | Typically ranges from 15 to 100 micrometers |
Sphericity | Spherical or near-spherical particles are preferred for optimal flow and packing during the printing process. |
Apparent Density | Varies depending on the specific material but typically falls between 4.0 and 7.0 g/cm³ |
Flowability | Measured by standardized tests to ensure consistent powder flow during printing. |
Moisture | Low moisture content is crucial to prevent spatter and ensure consistent printing quality. |
Oxygen Content | Minimized oxygen content helps to minimize oxidation during the printing process and maintain material properties. |
Grades | Available in various grades depending on the specific material and desired properties. Common standards include ASTM International (ASTM) and American Iron and Steel Institute (AISI). |
Standards | Conforms to relevant industry standards for metal powder used in additive manufacturing, such as ASTM F3049 for stainless steel powders and ASTM B330 for AM powders in general. |
Pricing for mold steel 3D printing metal powder can vary depending on the specific material, particle size, quantity, and supplier. Generally, expect to pay a premium compared to bulk metal powders used in traditional manufacturing techniques. However, the benefits of 3D printing, such as design flexibility and reduced lead times, can often offset the higher material cost.
Advantages and Limitations of Mold Steel 3D Printing Metal Powder
Here’s a table contrasting the advantages and limitations of mold steel 3D printing metal powder:
Advantages | Limitations |
---|---|
Unmatched Design Freedom | Higher material cost compared to traditional mold making methods. |
Reduced Lead Times | Requires specialized 3D printing equipment and expertise. |
Cost-Effective for Low-Volume Production | Surface finish of printed molds might require post-processing for some applications. |
Lightweight Molds | Limited selection of materials compared to traditional methods. |
Improved Mold Performance | Evolving technology with ongoing research and development. |
Despite the limitations, the advantages of mold steel 3D printing metal powder are significant. As the technology matures and the cost of materials and equipment comes down, we can expect to see even wider adoption across various industries.
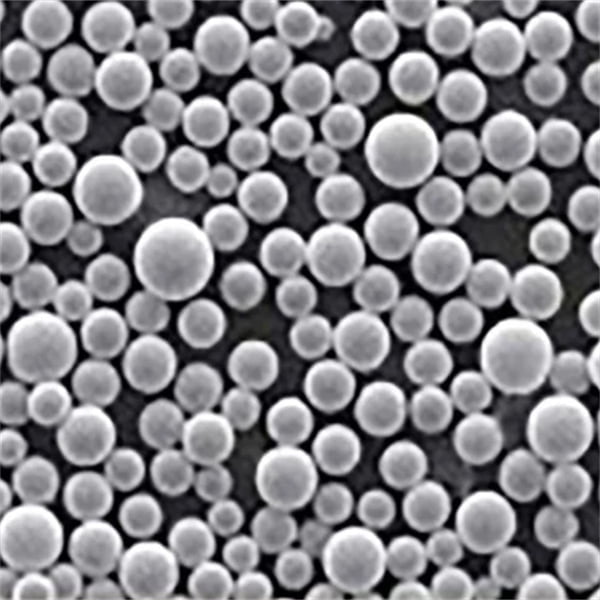
FAQ
Q: What are the benefits of using mold steel 3D printing metal powder compared to traditional mold making methods?
A: Mold steel 3D printing metal powder offers several advantages, including:
- Unmatched design freedom: Enables the creation of complex mold geometries that would be difficult or impossible to achieve with traditional machining techniques.
- Reduced lead times: Eliminates the need for complex tooling and lengthy machining processes, allowing for faster mold production.
- Cost-effective for low-volume production: Can be a more cost-effective option for low-volume production runs compared to traditional methods.
- Lightweight molds: Can create lighter weight molds compared to traditionally machined counterparts.
- Improved mold performance: Can potentially lead to improved mold performance through features like conformal cooling channels.
Q: What are some of the limitations of using mold steel 3D printing metal powder?
A: Some limitations of using mold steel 3D printing metal powder include:
- Higher material cost: The cost of mold steel 3D printing metal powder can be higher compared to bulk metal powders used in traditional methods.
- Specialized equipment: Requires specialized 3D printing equipment and expertise to operate effectively.
- Surface finish: The surface finish of printed molds might require post-processing for some applications.
- Limited material selection: Currently, the selection of mold steel 3D printing metal powders is more limited compared to traditional mold making materials.
Q: What are some typical applications for mold steel 3D printing metal powder?
A: Some typical applications for mold steel 3D printing metal powder include:
- Injection Molding: This is a prominent application where mold steel 3D printing powder shines. The ability to create complex geometries with conformal cooling channels allows for faster cycle times, improved part quality, and reduced energy consumption.
- Die Casting: Molds produced with mold steel 3D printing powder can handle the demanding requirements of die casting, including high pressures and molten metal temperatures. This is particularly beneficial for applications requiring high-strength, wear-resistant molds.
- Blow Molding: The lightweight nature of molds created with mold steel 3D printing powder is advantageous for blow molding processes. This can lead to improved energy efficiency and faster cycle times.
- Investment Casting: The intricate details achievable with 3D printing translate well to investment casting. Mold steel 3D printing powder allows for the creation of complex molds for high-quality investment castings.
- Prototyping and Low-Volume Production: This is a sweet spot for mold steel 3D printing powder. The technology enables rapid creation of functional prototypes and molds for low-volume production runs, reducing costs and accelerating time to market.
- Medical and Dental Applications: The biocompatible nature of some mold steel 3D printing powders allows for the creation of molds for medical implants and dental prosthetics. This opens doors for customization and potentially improved patient outcomes.
The potential applications of mold steel 3D printing metal powder are constantly expanding. As the technology evolves and becomes more accessible, we can expect to see its adoption in various industries, including aerospace, automotive, and consumer goods.
Conclusion
Mold steel 3D printing metal powder represents a significant advancement in the realm of mold making. It empowers designers and engineers with unprecedented design freedom, enabling the creation of complex, high-performance molds that were previously unimaginable. While some limitations exist, the advantages of faster lead times, potential cost-effectiveness for low-volume production, and the ability to create lightweight molds with improved performance are undeniable. As the technology matures and the cost of materials and equipment comes down, mold steel 3D printing metal powder is poised to revolutionize the way we design and manufacture molds across various industries.
Share On
MET3DP Technology Co., LTD is a leading provider of additive manufacturing solutions headquartered in Qingdao, China. Our company specializes in 3D printing equipment and high-performance metal powders for industrial applications.
Inquiry to get best price and customized Solution for your business!
Related Articles
About Met3DP
Recent Update
Our Product
CONTACT US
Any questions? Send us message now! We’ll serve your request with a whole team after receiving your message.
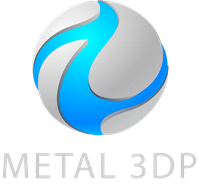
Metal Powders for 3D Printing and Additive Manufacturing