Molybdenum Disilicide Powder
Table of Contents
Molybdenum disilicide (MoSi2) is an intermetallic compound valued for high temperature stability, oxidation resistance, and thermal shock characteristics. As a powder, it serves thermal spray, sintering, and composite markets. This guide reviews MoSi2 powder specifications, manufacturing methods, usage examples, vendors, costs, limitations and alternatives to inform materials engineers.
Molybdenum Disilicide Powder Overview
Combining silicon with refractory molybdenum metal produces MoSi2 retaining strength beyond 1300°C without melting or oxidizing. Converting to powder form enables:
- Thermal spray coatings on turbine blades and tools
- Adding particulate reinforcement improving ceramic matrix composites
- Powder metallurgy consolidation into net shape heat exchangers
Key attributes:
- Melting point of 2030°C offers high temperature stability
- Forms protective SiO2 oxide layer resisting oxidation in air to 1500°C
- Low density of 6.2 g/cm2 eases component light weighting
- Very low coefficient of thermal expansion avoids cracking under rapid ΔT gradients
Withstanding extreme environments far above nickel and cobalt superalloys makes this silicide indispensable in thermal protection systems ranging from furnace components to aerospace engines and hypersonic vehicle leading edges.
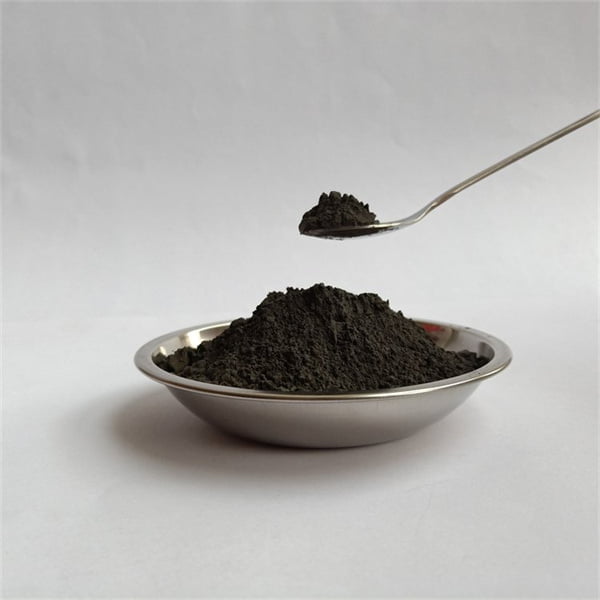
Molybdenum Disilicide Powder Compositions
MoSi2 powders span from relatively pure formulations with minor residual carbon and oxygen contamination to customized compositions alloying or adding particulate reinforcement:
Type | Description | Composition |
---|---|---|
Pure MoSi2 | Binary blend of molybdenum + silicon | 99% MoSi2 + <1% C, O |
Alloyed Compounds | Elements like boron, chromium, aluminum added forming Mo-Si-X ternaries/quaternaries | MoSi2 + 5% Cr + 2% B |
Composites | Particulate oxides or carbides blended with MoSi2 powder | MoSi2 + 20% SiC |
Table 1. Primary categories of molybdenum disilicide powder compositions including commodity binary blends and customized alloys/composites
Augmenting with elements like chromium, aluminum, carbon or reinforcing with stable ceramics expands capabilities tuning CTE, oxidation resistance and rheology matching final sintered product designs.
Characteristics and Properties of MoSi2 Powder
- Appearance – Gray powder with crystalline or angular morphology
- Melting Point – 2030°C enables molten state sintering without component melting
- Density – 6.2 g/cm3, 50% the density of tungsten
- Oxidation Resistance – Up to pressures of 0.9 atm, resists oxidation in air up to 1500°C via protective silica layer
- Poisson’s Ratio – 0.18-0.28 akin to steels
- CTE – 7.8 μm/m°C from 20-1000°C provides excellent thermal shock resistance
- Electrical Resistivity – 150-190 μΩ-cm must consider alongside thermal conductivity for component cooling
The properties ensure dimensional stability across rapid and cyclical firing thermal loads above superalloy limitations. Ductile phase additions expand brittle silicide ductility.
MoSi2 Powder Particle Size Specifications
Industry grades classify powders based on distribution cutoffs:
Grade | Micron Size | Typical Use |
---|---|---|
-140 Mesh | <106 μm | Thermal spray coatings |
-325 Mesh | <44 μm | Powder injection molding feedstock |
-400 Mesh | <38 μm | CMC reinforcement, pressed/sintered parts |
Table 2. Common molybdenum disilicide powder size classifications by mesh ranging from thermal spray down to sub 10 micron additions for sintered silicon carbides
Specifying powder distributions ensures alignment to particle size limitations and rheology needs of thermal spray nozzles versus tightly packed pressing and sintering demands.
Production Processes for MoSi2 Powder
Reduction & Silicidation – Molybdenum trioxide powders reduced under hydrogen atmosphere with silicon powder creates MoSi2 above 1200°C ultimately ball milled into distributions. Lower purity and irregular particles suit thermal spray deposition best.
Gas Atomization – Induction melted ingots in inert gas atomized into powder manages oxidation and controls particle sizes well. Spherical shapes improve powder bed packing and sintering behavior. But lower yields and higher powder price points verses chemical production.
Plasma Spheroidization – Instead of fully melting, induction heated feed stock injected into plasma torches rounds irregular reduced/silicided particles improving flow and packing while minimizing material loss to drain melt purification. Offers a midpoint powder quality and cost profile between the other methods.
Evaluating tradeoffs between purity, powder characteristics and price determines best value production method matching application requirements.
Industry Standards and Specifications
Governments and trade associations issue various MoSi2 powder standards:
Entity | Standard Number | Description |
---|---|---|
Fédération des Techniques de la Pulvérisation | FS-150 | Thermal spray grade |
DIN Deutsches Institut fur Normung | DIN17742 | Powder metallurgy grade |
ASTM International | C1765 | Testing methodology standards |
ISO International Standards Organization | ISO 21825 | Mechanical and physical testing methods |
Table 3. Leading international quality and testing standards applicable to molybdenum disilicide powders
Reviewing required chemistry, particle sizes, typical impurity thresholds and critically end application mechanical testing protocols ensures properly specifying and qualifying procured MoSi2 lots against certification guidelines covering usage scenarios – avoiding over or under specifying raw material inputs.
MoSi2 Powder Applications
Non-exhaustive uses benefiting from extreme thermal stability and oxidation resistance include:
Thermal Spray Coatings
- Furnace muffle tubes, fixtures and trays
- Refractory metal processing crucibles
- Aircraft turbine blade erosion + thermal protection
Sintering
- Electric heating element contacts and supports
- High temp gas seals and electrodes in glass manufacturing
- Molten metal immersion hardware like ladles
Composites
- Reinforcing additive in silicon nitrides and carbides
- Thermal management electronic substrate fillers
Any sintering, coating or composite manufacturing process needing dimensional stability across >1000°C temperature fluctuations free of oxidation considers molybdenum disilicide powders.
Molybdenum Disilicide Powder Manufacturers & Vendors
Reputable merchants producing and supplying MoSi2 powders include:
Supplier | Location | Production Method |
---|---|---|
Thermo Fisher Scientific | United States | Reduction & silicidation |
Atlantic Equipment Engineers | United States | Gas atomization |
Phoenix Scientific | United States | Plasma spheroidization |
China Molybdenum | China | Reduction & silicidation |
Japan New Metals | Japan | Gas atomization |
Table 4. Notable companies providing moly-silicon powders suiting either high purity or high volume industrial applications
Secondary distributors also sell commercially but best practice sources small lots directly from primary mills for best price and traceability.
MoSi2 Powder Cost Factors
Driver | Impact |
---|---|
Production method | Gas atomization costs 5-10x chemical production |
Material purity | Trace element and particle size controls increase price |
Purchase volume | Ton+ quantity discounts up to 30% possible |
Powder geometry | High sphericity consistency adds 25-50% |
Application spec | Tighter distributions and verifications raise price |
Table 5. Supply channel dynamics influencing molybdenum disilicide powder pricing
Expect $50/kg for common silicidation grades up to $300/kg for high purity plasma spheroidized fractions – although pricing not linear based on subtle quality variances.
Pros and Cons of MoSi2 Powder
Advantages | Disadvantages |
---|---|
2030°C melting point sustains mechanical properties at extreme temperatures | Brittle intermetallic prone to cracking under strain once fully densified |
Resists surface oxidation up to 1500°C via SiO2 layer | Poorer thermal conductivity than graphite must consider for heating element contacts |
Lower density than tungsten alternatives | Manufacturing challenges fully densifying without high hot press pressures |
Table 6. Tradeoffs to factor when considering molybdenum disilicide powder applications
MoSi2 serves uniquely solving extreme thermal stability needs despite processing and brittleness challenges unmatched by alternative 316 stainless or superalloy candidates also costing five times less even before densification complexity considerations also considered.
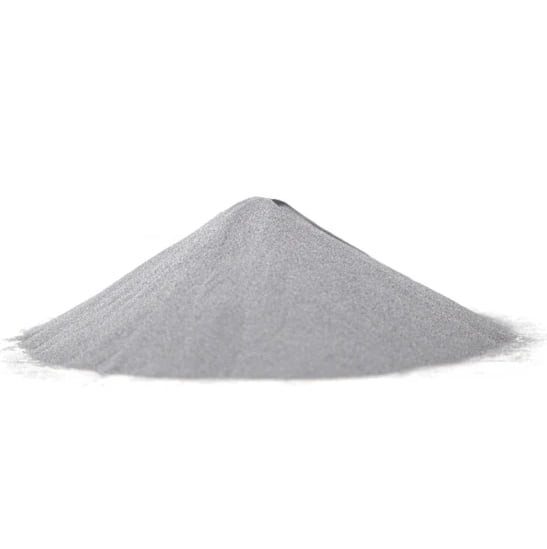
Comparing MoSi2 Powder to Alternatives
Parameter | MoSi2 | W | Ta | Re | Hf |
---|---|---|---|---|---|
Melting Point | 2030°C | 3410°C | 2996°C | 3180°C | 2230°C |
Oxidation Resistance | Up to 1500°C | Poor | Poor | Poor | Poor |
Density | 6.2 g/cm^3 | 19 g/cm^3 | 16 g/cm^3 | 21 g/cm^3 | 13 g/cm^3 |
Thermal Conductivity | Low | High | Medium | Medium | Medium |
Electric Resistivity | High | Low | Medium | ||
Cost | $$$$ | $$$$$ | $$$$$ | $$$$$ | $$$$$ |
Table 7. Qualitatively contrasting molybdenum disilicide powder against alternative refractory metal powders
Weigh composite requirements balancing thermal performance limits against manufacturability and lifecycle cost drivers steering engineers towards the right ultra-high temperature materials.
Frequently Asked Questions
Q: Does MoSi2 oxidize in air above 1500°C?
A: Yes, above 1500°C under 0.9 atm pressure, crystalline SiO2 surface layer grows more porous losing protection.
Q: What colors are available with MoSi2 coatings?
A: Natural gray but coloring via fine dispersions of oxides possible for higher emissivity thermal management.
Q: Does MoSi2 powder require hot isostatic pressing when sintering?
A: Yes, HIP densification minimizes residual porosity and maximizes mechanical strength after initial pressureless sintering stages.
Q: What applications use pure molybdenum disilicide with no alloying?
A: Pure MoSi2 suffices for furnace fixtures, trays, muffles seeing primarily uniform oxidation/corrosion without mechanical loads.
Share On
MET3DP Technology Co., LTD is a leading provider of additive manufacturing solutions headquartered in Qingdao, China. Our company specializes in 3D printing equipment and high-performance metal powders for industrial applications.
Inquiry to get best price and customized Solution for your business!
Related Articles
About Met3DP
Recent Update
Our Product
CONTACT US
Any questions? Send us message now! We’ll serve your request with a whole team after receiving your message.
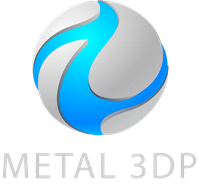
Metal Powders for 3D Printing and Additive Manufacturing