Molybdenum Powder
Table of Contents
Overview of molybdenum powder
Molybdenum powder refers to fine molybdenum particles in powder form used in various metallurgical, electronic, chemical, and industrial applications. Molybdenum has unique properties like high melting point, strength at high temperatures, corrosion resistance, thermal conductivity etc. that make it suitable for specialized uses.
Key details about molybdenum powder:
- Pure molybdenum or molybdenum alloys with other metals
- Main applications are metallurgy, electronics, chemicals, lubricants
- High purity levels from 99.5% to 99.9999% based on process
- Particle sizes ranging from 1 micron to 150 microns
- Multiple manufacturing methods yield different characteristics
- Properties like thermal conductivity leveraged across industries
- Pricing varies based on purity, size specs and purchase volumes
Molybdenum powder possesses properties that provide performance benefits making it a critical material in metal alloys, electronics, chemicals, lubricants and pigments globally.
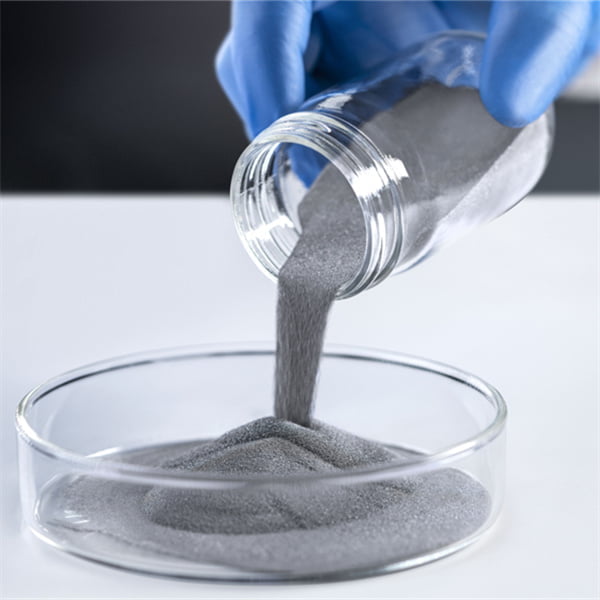
Molybdenum Powder Compositions
Molybdenum powder is available in various compositions ranging from pure molybdenum to combinations with other elements to form alloy powders.
Pure Molybdenum Powder
Molybdenum content above 99.5% purity, with low level impurities.
Molybdenum Alloy Powders
Alloy | Typical Composition |
---|---|
Mo-Cu | Mo 97%, Cu 3% |
Mo-La2O3 | Mo 60-70%, La2O3 30-40% |
Mo-Ni | Mo 40-60%, Ni 40-60% |
Mo-TiC | Mo 70-80%, TiC 20-30% |
Mo-TiB2 | Mo 60-80%, TiB2 20-40% |
Mo-W | Mo 40-60%, W 40-60% |
These powder alloys leverage combined properties of molybdenum with other elements for enhanced performance in specific applications like electronics.
Molybdenum Powder Properties
Molybdenum powder offers a unique combination of chemical, electrical, thermal, and mechanical properties:
Property | Typical Values |
---|---|
Density | 10.2 g/cc |
Melting Point | 2,623°C |
Thermal Conductivity | 138 W/m-K |
Electrical Resistivity | 5.5 μΩ-cm |
coefficient of Thermal Expansion | 5.3 μm/m-°C |
Maximum Working Temp | 1,600-2,000°C |
Its high temperature strength, corrosion resistance, thermal conductivity and other attributes provide advantages where performance under extreme conditions is necessary.
Key factors influencing molybdenum powder properties include:
- Purity Grade – directly impacts electrical, chemical and mechanical characteristics
- Particle Size – smaller size increases surface area to volume ratio enhancing chemical reactivity
- Manufacturing Process – determines morphology, internal porosity and microstructure
- Alloying Elements – tailored to achieve specific thermal, electrical or rheological properties
Property optimization and customization is possible for client applications through control of molybdenum powder composition and powder metallurgy techniques.
Applications of Molybdenum Powder
Some major application areas of molybdenum metal powders across industrial sectors include:
Metallurgical Additive
- Alloying element in stainless steels for corrosion resistance and high strength
- Improves hardenability, toughness and strength in tool steels
- Added to nickel and chromium superalloys for aircraft engines
Electronics & Electrical
- High current carrying capacity utilized in electron emitters and cathodes
- Component in advanced ceramic capacitors, ferroalloys and solar cell contacts
Pigments, Catalysts & Chemicals
- Precursor for molybdenum oxides used as pigments and catalysts
- Reagent in lubricant additives, dyes, organic synthesis, desulfurization etc.
Coatings & Joining
- Used as brazing alloy filler metal for high service temperature welding
- Applied in thermal spray protective coatings and metallization layers
The heat resistance, electrical conductivity and other useful characteristics make molybdenum indispensable across high performance products and advanced technologies.
Molybdenum Powder Specifications
Commercial molybdenum powders for industrial uses are available under different specification grades classified according to:
Parameter | Typical Range |
---|---|
Purity | 99.5% to 99.9999% |
Particle Size | 1 to 150 microns |
Shape | Irregular, spherical |
Apparent Density | 2 to 6 g/cc |
Tap Density | 4 to 10 g/cc |
American Society for Testing and Materials (ASTM) has defined reference standards for additive manufacturing use:
Standard | Item | Criteria |
---|---|---|
ASTM B781 | Chemical composition | Elemental content percentages |
ASTM B783 | Particle size classification | Micron and mesh range |
ASTM B809 | Spherical powder specification | Purity, particle size distribution, apparent density |
These help define quality metrics and ensure buyers get molybdenum powder suitable for mission-critical applications. Custom particle dimensions, size distribution yields, shape uniformity, surface area, bulk densities, and impurity grades are possible through agreement with reputable manufacturers.
Molybdenum Powder Manufacturers and Prices
There are several global specialty metals producers providing pure molybdenum and molybdenum alloy powders for commercial uses. Some of the major suppliers are:
Company | Headquarters |
---|---|
H.C. Starck | Germany |
Plansee Group | Austria |
Exploiter Molybdenum | China |
China Molybdenum Co. | China |
Molymet | Chile |
JDC Moly | Korea |
Some Molybdenum Powder Cost Indications
Purity | Mesh Size | Price per kg |
---|---|---|
99% | -325 Mesh | $40 – $55 |
99.5% | 1-5 Microns | $70 – $90 |
99.9% | 10-50 Microns | $100 – $140 |
99.95% | Spherical <45 μm | $140 – $170 |
Final pricing depends on exact material grade, particle characteristics, order volumes, supply chain logistics and market conditions. Powder metallurgy grade spherical molybdenum with high purity and controlled particle size distribution necessary for critical applications demands premiums.
Pros and Cons of Using Molybdenum Powder
Here is a comparative look at some of the advantages and disadvantages associated with molybdenum powder:
Advantages
- Excellent high temperature strength for service over 2000°C
- Low coefficient of thermal expansion for dimensional stability
- High thermal and electrical conductivity for heat sinks
- Extremely corrosion resistant nature
- Tailor mechanical properties through alloy combinations
- Net-shape part fabrication simplicity with press and sinter
Disadvantages
- Relatively more expensive than substitute options
- Lower hardness and wear/abrasion resistance needing surface treatments in friction contacts
- Susceptible to oxygen contamination at higher processing temperatures
- Requires inert atmospheres or vacuum for metallurgical consolidation
- Exhibits poorer machinability relative to steels
- Lacks ductility for extensive cold forming operations
For niche applications where thermal stability, chemical resistance and electrical characteristics matter, molybdenum outperforms alternatives like tungsten or tantalum, offsetting higher base price for its differentiated performance.
Molybdenum Powder vs. Molybdenum Sheet
Molybdenum powder provides specific advantages in manufacturing and properties relative to molybdenum sheet, rod or wire forms:
Key Differences
Parameter | Molybdenum Powder | Molybdenum Sheet/Rod |
---|---|---|
Manufacturing Method | Atomization and milling | Casting and rolling |
Size and Shape Control | Excellent | Limited |
Dimensional Tolerance | Tighter | Wider |
Surface Finishes | Fine matte | Smooth lustrous |
Mechanical Properties | Isotropic fine grained | Anisotropic coarse |
Net Shape Capability | Very good sintered parts | Extensive machining needed |
Economics | Lower material utilization | Higher raw material efficiency |
The ability to press and sinter molybdenum powder into high performance parts very close to final dimensions + the flexibility around customized powder characteristics makes it attractive for numerous functional and structural component needs.
Thermal Spray with Molybdenum Powder
Thermal spray techniques like high velocity oxy-fuel (HVOF), plasma or arc spray are used to deposit molten or semi-molten molybdenum powder onto components to form highly adherent protective coatings.
Benefits of molybdenum metal spray:
- Wear resistance for friction and load bearing surfaces
- Electrical and thermal conductive surface layers
- Corrosion protection in chemical processing equipment
- Dimensional restoration of worn-out parts through build up
Common spray parameters for molybdenum powder:
Parameter | Typical Range |
---|---|
Particle Size | 10 – 45 microns |
Deposition Efficiency | 50 – 70% |
Coating Thickness | 50 – 500 microns |
Microhardnes | 350 – 600 HV |
Bond Strength | > 69 MPa |
Operating Temperature | 120°C to 260°C |
Molybdenum coatings are widely leveraged across oil & gas valves, aerospace seals, automotive bearings, plastic extrusion barrels, and electrical contacts in connectors owing to exceptional tribological characteristics.
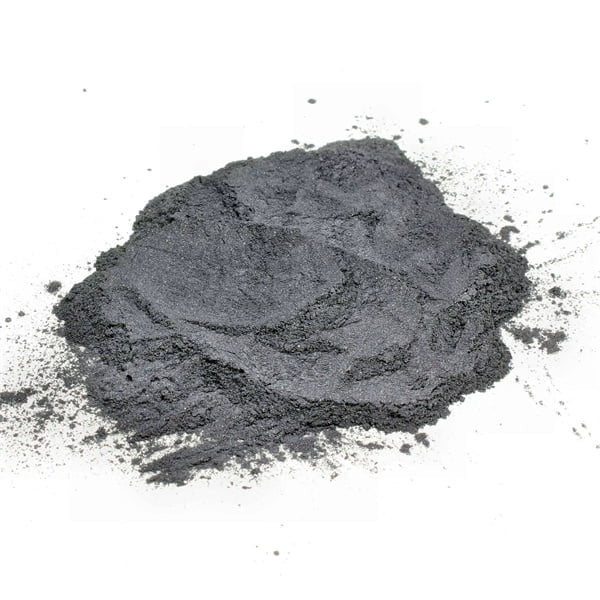
FAQs
Q: What industries use molybdenum powder for manufacturing purposes?
A: Major end-use segments are metallurgy, electronics, catalysts, aerospace, energy, coatings, and chemicals – leveraging properties like high temperature strength, thermal conductivity, electrical resistivity and corrosion resistance.
Q: What typical processes are employed for fabricating parts using molybdenum powder?
A: Main techniques are powder pressing followed by pressureless or pressure-assisted sintering. Powder injection molding and additive manufacturing are also emerging for complex geometries.
Q: What are common contaminants affecting quality of molybdenum powders?
A: Oxygen, carbon, sulfur and chlorine are detrimental impurities impairing utility in applications demanding high chemical purity like electronics. Stringent process controls during manufacturing are critical.
Q: Does molybdenum powder require special handling precautions?
A: Inert gas blanketing, vacuum packing and low humidity storage is necessary for high purity fine powders prone to oxidation at elevated temperatures reached during processing.
Q: What coatings can be sprayed using molybdenum powders?
A: Besides pure molybdenum, composite variations like Mo-Cu, Mo-NiCrBSi, Mo-NiCrFeSiB and carbide coatings blended with nickel or cobalt chrome matrices containing molybdenum provide enhanced functional characteristics.
Q: What testing methods help characterize molybdenum powders?
A: Chemical analysis verifies composition purity levels through techniques like ICP-MS, XRF or LECO analysis. Physical attributes like particle size distribution, shape factors, apparent density and tap density help optimize powder morphology.
Conclusion
Molybdenum metal powder, with its unique electrical, thermal, and mechanical properties, provides differentiated performance making it indispensable for critical applications like aerospace engines, electronics, furnace components and metal alloys where reliability under extreme conditions is vital.
Continual development of purer compositions with precisely engineered particle dimensions, size distribution fractions, shapes, density parameters and microstructures tailored to specific end-uses expands utility across more sectors and technologies.
Enhanced manufacturing methods combined with strong industry demand strongly position fine molybdenum powders to see robust long term growth owing to the material’s distinctive capabilities.
Share On
MET3DP Technology Co., LTD is a leading provider of additive manufacturing solutions headquartered in Qingdao, China. Our company specializes in 3D printing equipment and high-performance metal powders for industrial applications.
Inquiry to get best price and customized Solution for your business!
Related Articles
About Met3DP
Recent Update
Our Product
CONTACT US
Any questions? Send us message now! We’ll serve your request with a whole team after receiving your message.
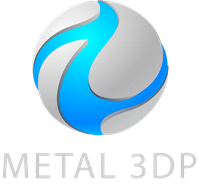
Metal Powders for 3D Printing and Additive Manufacturing