Multi-Material Structures
Table of Contents
Overview
Multi-material structures are revolutionizing industries by combining the best properties of different materials into a single, optimized system. These structures are increasingly prevalent in aerospace, automotive, and consumer electronics, offering enhanced performance, weight reduction, and cost efficiency. This comprehensive guide will delve into the intricacies of multi-material structures, highlighting their types, compositions, properties, characteristics, applications, specifications, suppliers, and pricing details. We’ll also compare the advantages and disadvantages, providing a thorough understanding of this innovative technology.
What are Multi-Material Structures?
Multi-material structures are engineered systems that integrate two or more materials with different properties to create a composite that leverages the strengths of each constituent. Imagine a car’s body that combines lightweight aluminum with high-strength steel – it’s lighter and stronger than if it were made from a single material. This concept isn’t just limited to metals; it spans ceramics, polymers, and more, each selected to optimize performance for specific applications.
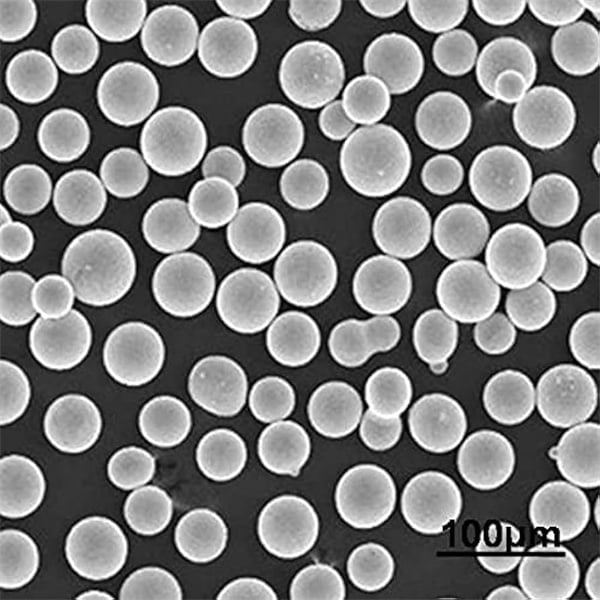
Types of Multi-Material Structures
The world of multi-material structures is vast and varied. Let’s break down some of the common types:
Type | Composition | Properties | Applications |
---|---|---|---|
Bimetallic | Two layers of metals (e.g., steel and aluminum) | Enhanced thermal and electrical properties | Electrical components, heat exchangers |
Metal Matrix Composites (MMCs) | Metal matrix with ceramic or metallic reinforcements | High strength-to-weight ratio, excellent wear resistance | Aerospace, automotive, sports equipment |
Hybrid Polymers | Blends of different polymers or polymers with fillers | Improved mechanical and thermal properties | Packaging, electronics, medical devices |
Ceramic Matrix Composites (CMCs) | Ceramic matrix with ceramic or metallic fibers | High-temperature stability, low density | Turbine blades, aerospace components |
Fiber-Reinforced Polymers (FRPs) | Polymer matrix with fibrous reinforcement (e.g., carbon or glass fibers) | High tensile strength, corrosion resistance | Construction, automotive, sports gear |
Specific Metal Powder Models
In the realm of metal powder models, which are crucial for creating high-performance multi-material structures, here are ten notable examples:
- AlSi10Mg: An aluminum-silicon-magnesium alloy known for its lightweight and high strength, often used in aerospace and automotive applications.
- 316L Stainless Steel: Renowned for its corrosion resistance and mechanical properties, widely used in medical and industrial applications.
- Inconel 718: A nickel-chromium alloy that offers excellent high-temperature strength and oxidation resistance, ideal for aerospace and gas turbines.
- Ti6Al4V (Titanium Grade 5): A titanium alloy prized for its high strength-to-weight ratio and biocompatibility, common in aerospace and biomedical fields.
- CoCrMo (Cobalt-Chromium-Molybdenum): Known for its wear resistance and high strength, used in medical implants and aerospace components.
- Maraging Steel (18Ni300): Offers high strength and toughness after aging, used in tooling and aerospace applications.
- Copper (Cu): Excellent thermal and electrical conductivity, used in electronics and heat exchangers.
- Aluminum (AlSi12): Lightweight with good casting properties, used in automotive and consumer electronics.
- Hastelloy X: A nickel-based alloy known for its oxidation resistance and high-temperature strength, used in chemical processing and aerospace.
- Nickel 625: Offers excellent fatigue and thermal-fatigue strength, oxidation, and corrosion resistance, used in marine and chemical industries.
Properties and Characteristics
Understanding the properties and characteristics of multi-material structures is crucial for selecting the right combination for specific applications.
Material | Density (g/cm³) | Tensile Strength (MPa) | Young’s Modulus (GPa) | Thermal Conductivity (W/mK) | Corrosion Resistance |
---|---|---|---|---|---|
AlSi10Mg | 2.68 | 400 | 70 | 170 | Good |
316L Stainless Steel | 7.99 | 580 | 193 | 16 | Excellent |
Inconel 718 | 8.19 | 1100 | 211 | 11 | Excellent |
Ti6Al4V | 4.43 | 900 | 120 | 7 | Excellent |
CoCrMo | 8.29 | 1000 | 210 | 14 | Excellent |
Maraging Steel | 8.0 | 2000 | 185 | 14 | Good |
Copper | 8.96 | 210 | 130 | 400 | Poor |
AlSi12 | 2.68 | 320 | 70 | 150 | Good |
Hastelloy X | 8.22 | 800 | 205 | 11 | Excellent |
Nickel 625 | 8.44 | 760 | 206 | 10 | Excellent |
Applications of Multi-Material Structures
Multi-material structures find applications across various industries due to their tailored properties. Here’s a closer look at some of the prominent applications:
Industry | Application | Materials Used | Benefits |
---|---|---|---|
Aerospace | Turbine blades, fuselage panels | Titanium alloys, MMCs | High strength-to-weight ratio, thermal stability |
Automotive | Body panels, engine components | Aluminum, high-strength steel | Weight reduction, improved fuel efficiency |
Medical | Implants, surgical tools | CoCrMo, 316L stainless steel | Biocompatibility, corrosion resistance |
Electronics | Heat sinks, circuit boards | Copper, AlSi10Mg | Thermal management, electrical conductivity |
Construction | Structural beams, reinforcements | FRPs, hybrid polymers | High strength, corrosion resistance |
These applications highlight the versatility and advantages of using multi-material structures in various demanding environments.
Specifications and Standards
When dealing with multi-material structures, adhering to specifications and standards is crucial to ensure quality and performance.
Material | Standard | Specifications |
---|---|---|
AlSi10Mg | ASTM F3318 | Chemical composition, mechanical properties |
316L Stainless Steel | ASTM A240 | Chemical composition, mechanical properties, corrosion resistance |
Inconel 718 | ASTM B637 | Mechanical properties, heat treatment conditions |
Ti6Al4V | ASTM F1472 | Chemical composition, mechanical properties, biocompatibility |
CoCrMo | ASTM F1537 | Chemical composition, mechanical properties, wear resistance |
Maraging Steel | AMS 6514 | Mechanical properties, aging process |
Copper | ASTM B152 | Chemical composition, electrical and thermal properties |
AlSi12 | EN AC-43400 | Chemical composition, casting properties |
Hastelloy X | ASTM B572 | Mechanical properties, corrosion resistance |
Nickel 625 | ASTM B443 | Mechanical properties, corrosion resistance |
These standards ensure that materials meet the necessary criteria for performance and safety in their respective applications.
Suppliers and Pricing
Finding the right supplier and understanding the pricing is essential for sourcing materials for multi-material structures.
Material | Supplier | Approximate Price (per kg) |
---|---|---|
AlSi10Mg | EOS GmbH | $50-$70 |
316L Stainless Steel | Sandvik | $30-$50 |
Inconel 718 | Special Metals | $100-$150 |
Ti6Al4V | ATI Metals | $200-$300 |
CoCrMo | Carpenter Technology | $100-$150 |
Maraging Steel | Uddeholm | $70-$90 |
Copper | KME Group | $10-$20 |
AlSi12 | Norsk Hydro | $30-$50 |
Hastelloy X | Haynes International | $80-$120 |
Nickel 625 | VDM Metals | $120-$160 |
These prices can vary based on factors such as quantity, supplier, and market conditions, so it’s always a good idea to get quotes from multiple sources.
Advantages of Multi-Material Structures
Multi-material structures offer a plethora of benefits, driving their adoption across various industries. Let’s dive into some of the key advantages:
Enhanced Performance
One of the primary advantages is the ability to tailor properties to specific applications. By combining materials with different strengths, you can achieve a balance of performance characteristics that would be impossible with a single material. For example, using aluminum for its lightweight properties and steel for its strength can lead to a component that is both light and strong.
Weight Reduction
In industries like aerospace and automotive, reducing weight is crucial for improving fuel efficiency and performance. Multi-material structures allow designers to use lightweight materials in areas where weight savings are critical, while still maintaining structural integrity with stronger materials in high-stress areas.
Cost Efficiency
Although the initial cost of multi-material structures can be higher due to the complexity of manufacturing, the long-term benefits often outweigh these costs. Improved performance and weight reduction can lead to significant savings in fuel costs and increased lifespan of the components, resulting in lower overall costs.
Corrosion Resistance
Combining materials that offer corrosion resistance with those that provide strength can lead to components that are not only durable but also resistant to environmental factors. This is particularly beneficial in industries such as marine and medical, where corrosion resistance is paramount.
Thermal and Electrical Properties
Multi-material structures can be designed to optimize thermal and electrical properties. For instance, combining copper’s excellent thermal conductivity with another material’s strength can result in heat exchangers that are both efficient and durable.
Disadvantages of Multi-Material Structures
Despite their numerous benefits, multi-material structures also come with some challenges and limitations:
Complex Manufacturing
The process of creating multi-material structures is often more complex than working with a single material. This can involve sophisticated joining techniques, such as welding, adhesive bonding, or mechanical fastening, which can increase manufacturing time and cost.
Material Compatibility
Ensuring that different materials are compatible with each other can be challenging. Issues such as galvanic corrosion, differential thermal expansion, and mechanical mismatch need to be addressed to prevent failure.
Higher Initial Costs
While multi-material structures can lead to cost savings in the long run, the initial costs are often higher due to the complexity of design and manufacturing. This can be a barrier for some applications, especially where budget constraints are significant.
Design and Analysis Complexity
The design and analysis of multi-material structures require advanced simulation and modeling techniques. Engineers need to understand how different materials interact under various conditions, which can be more challenging than designing with a single material.
Repair and Maintenance
Repairing multi-material structures can be more difficult compared to single-material components. Specialized techniques and materials may be required to ensure the integrity of the repaired structure, which can increase maintenance costs.
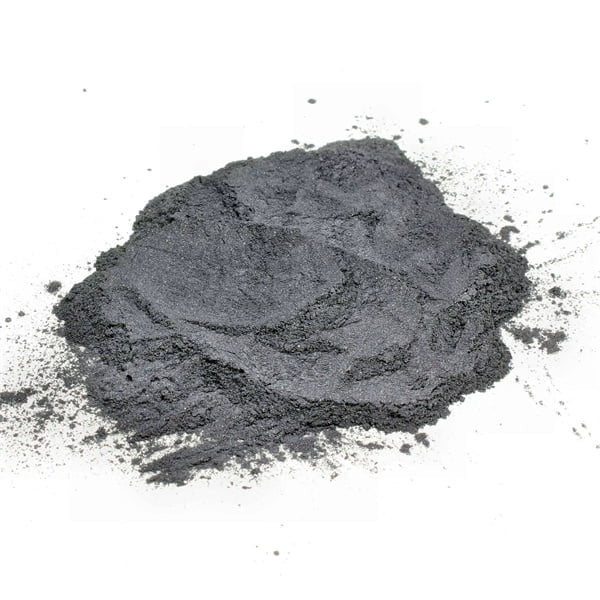
FAQs
What are multi-material structures?
Multi-material structures are engineered systems that integrate two or more materials to create a composite with enhanced properties. They are used in various industries to optimize performance, reduce weight, and improve cost efficiency.
What are the benefits of using multi-material structures?
The primary benefits include enhanced performance, weight reduction, cost efficiency, corrosion resistance, and improved thermal and electrical properties.
What are some common applications of multi-material structures?
Common applications include aerospace components, automotive parts, medical implants, electronics, and construction materials.
What are the challenges associated with multi-material structures?
Challenges include complex manufacturing processes, material compatibility issues, higher initial costs, design and analysis complexity, and difficulties in repair and maintenance.
How do multi-material structures reduce weight?
By using lightweight materials in areas where weight savings are critical and stronger materials in high-stress areas, multi-material structures achieve an optimal balance of strength and weight.
Can multi-material structures be used in medical applications?
Yes, multi-material structures are used in medical applications such as implants and surgical tools due to their biocompatibility and corrosion resistance.
Conclusion
Multi-material structures represent a significant advancement in materials engineering, offering the potential to revolutionize various industries through enhanced performance, weight reduction, and cost efficiency. By combining the best properties of different materials, these structures provide solutions that single-material systems simply cannot achieve. However, they also come with challenges that need to be carefully managed, including complex manufacturing processes and material compatibility issues.
Whether in aerospace, automotive, medical, or electronics, the applications of multi-material structures are vast and varied, showcasing their versatility and importance in modern engineering. As technology continues to advance, the development and implementation of multi-material structures are likely to become even more prominent, driving further innovations and improvements across multiple fields.
Share On
MET3DP Technology Co., LTD is a leading provider of additive manufacturing solutions headquartered in Qingdao, China. Our company specializes in 3D printing equipment and high-performance metal powders for industrial applications.
Inquiry to get best price and customized Solution for your business!
Related Articles
About Met3DP
Recent Update
Our Product
CONTACT US
Any questions? Send us message now! We’ll serve your request with a whole team after receiving your message.
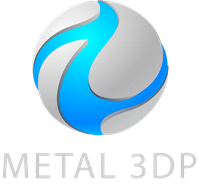
Metal Powders for 3D Printing and Additive Manufacturing