Powder for PBF Technique
Table of Contents
Imagine building intricate metal structures layer by layer, not with rivets and welds, but with lasers and precise manipulation of metal powder. That’s the magic of Powder Bed Fusion (PBF), a revolutionary 3D printing technique that’s transforming the manufacturing landscape. But at the heart of this technology lies a crucial ingredient: the powder itself.
In this comprehensive guide, we’ll delve into the world of Powder for PBF Technique, exploring their types, properties, applications, and the factors that make them tick. We’ll also unveil ten specific metal powder models used in PBF, providing detailed descriptions to empower your understanding. Buckle up and get ready to explore the fascinating world of metal powder for 3D printing!
Advantages of Powder for PBF Technique
PBF technology offers a plethora of advantages over traditional metalworking methods. Here’s how powder plays a starring role in these benefits:
- Design Freedom: Unlike subtractive manufacturing, PBF with powder allows for the creation of complex geometries, including internal channels and lattice structures, previously impossible with conventional techniques. Think of it as building with Lego blocks for adults – the possibilities are virtually endless.
- Lightweighting: Powder particles can be incredibly fine, enabling the creation of lightweight yet robust metal parts. This is a game-changer for industries like aerospace and automotive, where every ounce shaved off translates to significant efficiency gains.
- Material Efficiency: PBF with powder minimizes material waste compared to traditional methods. Think of it like using an ink cartridge for printing – only the necessary material gets used, reducing scrap and associated costs.
- Mass Customization: Since PBF builds parts layer by layer from digital data, it’s perfect for producing customized components. Imagine creating a unique gear or bracket specifically designed for a particular application – powder-based PBF makes it possible.
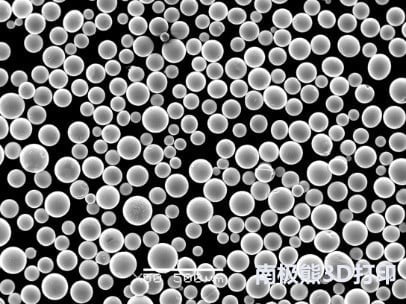
Types of Powder for PBF Technique
PBF powders come in a variety of flavors, each with its unique properties and applications. Here’s a breakdown of the most common types:
Type | Composition | Properties | Characteristics |
---|---|---|---|
Metals | Stainless Steel, Titanium alloys, Inconel, Aluminum alloys, Cobalt Chrome | High strength, heat resistance, corrosion resistance | Vary in particle size, flowability, and surface area |
Polymers | Nylon, Polyamide (PA) | Good mechanical properties, lightweight, biocompatible | Can be blended with metal powders for composite structures |
Within the metal category, different alloys offer distinct advantages:
- Stainless Steel Powders: These versatile powders offer excellent corrosion resistance and are widely used in industries like medical, automotive, and food processing. Imagine creating a lightweight, yet highly durable surgical instrument – stainless steel powder makes it a reality.
- Titanium Alloys: Renowned for their high strength-to-weight ratio and biocompatibility, titanium powders are ideal for aerospace, medical implants, and sporting goods applications. Think of a prosthetic leg that’s not only strong but also lightweight – titanium powder is a key ingredient.
- Inconel Powders: These nickel-chromium-based alloy powders boast exceptional heat and corrosion resistance, making them perfect for high-temperature environments like jet engines and chemical processing equipment. Imagine a turbine blade that can withstand extreme temperatures – Inconel powder makes it possible.
- Aluminum Alloy Powders: Offering a good balance of strength, weight, and affordability, aluminum alloy powders are used in various industries, including automotive, aerospace, and consumer electronics. Imagine a lightweight yet sturdy phone case – aluminum alloy powder is a potential solution.
- Cobalt Chrome Powders: These cobalt-chromium-based alloy powders are known for their biocompatibility, wear resistance, and high strength, making them ideal for medical implants like hip replacements and dental crowns. Imagine a long-lasting, biocompatible hip replacement – cobalt chrome powder plays a crucial role.
Beyond Metals: Exploring Polymer Powders
While metals dominate the PBF landscape, polymer powders are also making inroads. These powders offer good mechanical properties, are lightweight, and can even be biocompatible. They’re often used for prototyping and functional parts that don’t require the extreme strength of metals. Imagine creating a quick and accurate prototype of a new product design – polymer powder can help bring your ideas to life.
Applications of Powder for PBF Technique
The applications of PBF powders are as diverse as human ingenuity itself. Here are some key areas where this technology is making waves:
Industry | Applications | Benefits |
---|---|---|
Aerospace | Lightweight aircraft components, engine parts, heat exchangers | Weight reduction for improved fuel efficiency and performance |
Automotive | Custom parts, complex engine components, lightweight brackets | Enhanced performance, design freedom, and |
Specific Metal Powder Models for PBF Technique
Now that we’ve explored the different types of powders used in PBF, let’s delve into ten specific models to understand their unique characteristics and applications:
- EOS StainlessSteel 316L: This workhorse powder from EOS GmbH is a versatile 316L stainless steel option known for its excellent corrosion resistance, good weldability, and biocompatibility. It’s a popular choice for applications in the medical, food processing, and chemical industries.
- AMCP CP Ti Grade 2: This gas-atomized titanium grade 2 powder from Additive Manufacturing Company (AMCP) offers a high strength-to-weight ratio and excellent biocompatibility. It’s a go-to material for aerospace components, medical implants, and sporting goods due to its lightweight and strong nature.
- SLM Solutions Inconel 625: This high-performance Inconel 625 powder from SLM Solutions is ideal for high-temperature applications. Its exceptional heat and corrosion resistance make it perfect for jet engine components, gas turbines, and chemical processing equipment.
- Renishaw Aluminium AlSi10Mg: This aluminum silicon magnesium alloy powder from Renishaw is a cost-effective option for applications requiring a good balance of strength, weight, and machinability. It’s commonly used in the automotive and aerospace industries for components like brackets, housings, and heat sinks.
- Höganäs Cobalt Chrome CoCrMo: This cobalt-chromium-molybdenum alloy powder from Höganäs AB is biocompatible, wear-resistant, and offers high strength. It’s a preferred material for medical implants like hip replacements, knee joints, and dental crowns due to its long-lasting properties.
- Carpenter Additive Wire DED 1: This unique offering from Carpenter Technology Corporation is a metal powder specifically designed for Directed Energy Deposition (DED) – an additive manufacturing technique similar to PBF. DED 1 offers excellent crack resistance and high strength, making it ideal for repairing and building up metal components in various industries.
- LPW Titanium Ti6Al4V: This titanium alloy powder (Ti6Al4V) from LPW Technology Ltd. is another popular choice for aerospace and medical applications. The presence of aluminum and vanadium in the alloy enhances its strength compared to pure titanium, making it suitable for demanding applications.
- ExOne MetalDesign M2 Tool Steel 1.2344: This tool steel powder from ExOne is formulated for applications requiring high wear resistance and dimensional stability. Imagine creating a mold or cutting tool with exceptional durability – this powder can make it a reality.
- Proto Labs LaserForm Ni60: This nickel-chromium alloy powder (Ni60) from Proto Labs Inc. offers a balance of strength, corrosion resistance, and affordability. It’s a versatile option for various industrial applications, particularly those requiring good mechanical properties at moderate temperatures.
- GE Additive Arcam Ti-6Al-4V ELI: This gas-atomized titanium alloy powder (Ti6Al4V) with an extra low interstitial (ELI) designation from GE Additive is specifically formulated for medical implants. The ELI designation ensures minimal impurities, making it ideal for biocompatible applications.
Choosing the Right Powder: A Balancing Act
Selecting the optimal powder for your PBF project requires careful consideration of several factors:
- Material Properties: Match the powder’s properties like strength, heat resistance, and corrosion resistance to your application’s requirements.
- Particle Size and Distribution: The size and distribution of powder particles significantly impact flowability, surface finish, and mechanical properties of the printed part.
- Laser Compatibility: Ensure the powder’s absorption characteristics are compatible with the specific laser type used in your PBF system.
- Cost: Metal powders can vary significantly in price. Consider the cost-performance trade-off when selecting a powder.
Beyond the Basics: Advanced Considerations
For advanced users, additional factors come into play:
- Powder Sphericity: Highly spherical powders generally offer better flowability and packing density, leading to improved print quality.
- Surface Chemistry: The powder’s surface chemistry can influence factors like laser absorption and inter-particle bonding during the PBF process.
- Powder Re-usability: Some powders can be partially re-used, offering cost savings. However, strict quality control is crucial to ensure consistent performance.
By carefully considering these factors and the specific properties of each powder model, you can make informed decisions to optimize your PBF projects.
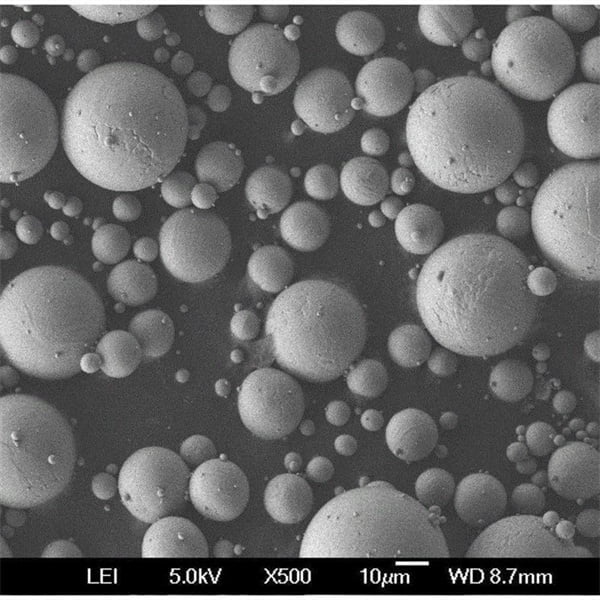
FAQ
Q: What are the safety precautions when handling metal powders?
A: Metal powders can be flammable and pose health risks if inhaled. Here are some safety precautions to follow:
- Always wear appropriate personal protective equipment (PPE) such as gloves, safety glasses, and a respirator when handling metal powders.
- Work in a well-ventilated area to minimize powder dust exposure.
- Store metal powders in sealed containers in a dry and cool location.
- Dispose of metal powders according to local regulations.
Q: Can I use recycled metal powders for PBF?
A: While some metal powders can be partially re-used in PBF, it’s crucial to exercise caution. Recycled powders may have inconsistent properties compared to virgin powders, potentially impacting the quality of printed parts. Here are some things to consider:
- Powder origin and composition: Ensure the recycled powder comes from a reputable source and has a well-defined composition.
- Powder quality control: Implement rigorous quality control procedures to verify the recycled powder’s flowability, particle size distribution, and overall chemical composition before using it in PBF.
- Mixing ratios: Start with a low percentage of recycled powder blended with virgin powder to minimize potential issues. Gradually increase the recycled powder content as you gain confidence in its quality and impact on the printing process.
Q: How do I store metal powders for PBF?
A: Proper storage is essential to maintain the quality and performance of metal powders for PBF. Here are some key storage practices:
- Store powders in sealed containers: This prevents moisture absorption, which can affect flowability and laser interaction during PBF.
- Maintain a cool and dry environment: High temperatures and humidity can degrade the powder’s properties. Consider using desiccants within the storage containers to control moisture levels.
- Protect from contamination: Avoid exposing powders to dust, dirt, or other contaminants that could compromise their printability.
- Label containers clearly: Clearly label containers with the powder type, lot number, and date of purchase to ensure proper identification and traceability.
Q: What are the advantages and disadvantages of different powder particle sizes?
A: The particle size and distribution of metal powders significantly impact PBF printability and the final part’s properties. Here’s a breakdown of the pros and cons:
- Finer Powders:
- Advantages: Finer powders generally offer better surface finish and dimensional accuracy in printed parts.
- Disadvantages: However, finer powders can be more challenging to handle due to poorer flowability and higher risk of caking. They may also require higher laser power densities, which can increase thermal stresses and warping in the printed part.
- Coarser Powders:
- Advantages: Coarser powders typically exhibit better flowability and require lower laser power densities, reducing the risk of warping.
- Disadvantages: The downside is that coarser powders can result in a rougher surface finish and potentially higher porosity in the printed part, impacting its mechanical properties.
The optimal particle size depends on the specific application and desired outcome. A good starting point is to consult the recommendations of the powder manufacturer and your PBF system supplier.
Q: What are the future trends in metal powders for PBF?
A: The future of metal powders for PBF is bright and innovative. Here are some exciting trends to watch:
- Development of new alloys: Material scientists are continuously developing new metal alloys specifically formulated for PBF, offering improved printability, strength, and performance characteristics.
- Nano-powder technology: The use of nano-sized powders holds promise for creating even finer features and achieving superior surface finishes in printed parts.
- Recycled powder advancements: Advancements in powder recycling technologies could lead to more cost-effective and sustainable PBF practices.
- Multi-material printing: The ability to use multiple powder materials within a single PBF build opens doors for creating parts with graded properties or even functional composites.
Share On
MET3DP Technology Co., LTD is a leading provider of additive manufacturing solutions headquartered in Qingdao, China. Our company specializes in 3D printing equipment and high-performance metal powders for industrial applications.
Inquiry to get best price and customized Solution for your business!
Related Articles
About Met3DP
Recent Update
Our Product
CONTACT US
Any questions? Send us message now! We’ll serve your request with a whole team after receiving your message.
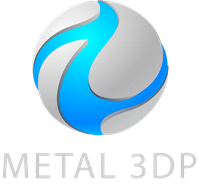
Metal Powders for 3D Printing and Additive Manufacturing
COMPANY
PRODUCT
cONTACT INFO
- Qingdao City, Shandong, China
- [email protected]
- [email protected]
- +86 19116340731