Powder for PBF Technique
Table of Contents
Overview
Powder Bed Fusion (PBF) is a popular additive manufacturing (AM) technique that uses a laser or electron beam to fuse powdered material layer by layer to create complex and high-precision parts. The choice of metal powder is crucial in PBF, as it directly affects the quality, strength, and durability of the final product. This guide delves into the specifics of metal powders suitable for PBF, discussing various models, their properties, applications, and comparative advantages.
Types of Metal Powders for PBF Technique
Metal Powders Overview
Powder Type | Composition | Properties | Characteristics |
---|---|---|---|
Titanium Alloy (Ti6Al4V) | Titanium (90%), Aluminum (6%), Vanadium (4%) | High strength, lightweight, corrosion-resistant | Aerospace, medical implants |
Stainless Steel (316L) | Iron, Chromium, Nickel, Molybdenum | Excellent corrosion resistance, high strength | Food processing, medical devices |
Inconel 718 | Nickel, Chromium, Iron | High temperature resistance, excellent mechanical properties | Aerospace, turbine blades |
Aluminum Alloy (AlSi10Mg) | Aluminum, Silicon, Magnesium | Lightweight, good thermal properties | Automotive, aerospace |
Cobalt Chrome (CoCr) | Cobalt, Chromium | High wear resistance, biocompatibility | Dental, orthopedic implants |
Maraging Steel | Iron, Nickel, Molybdenum, Cobalt | High strength, good toughness | Tooling, aerospace |
Copper Alloy (CuCrZr) | Copper, Chromium, Zirconium | Excellent thermal and electrical conductivity | Electrical components, heat exchangers |
Tungsten Carbide | Tungsten, Carbon | Extreme hardness, wear resistance | Cutting tools, wear parts |
Tool Steel (H13) | Iron, Carbon, Chromium, Molybdenum | High hardness, good thermal fatigue resistance | Injection molding, die casting |
Nickel Alloy (Ni625) | Nickel, Chromium, Molybdenum, Niobium | Corrosion resistance, high strength | Chemical processing, marine |
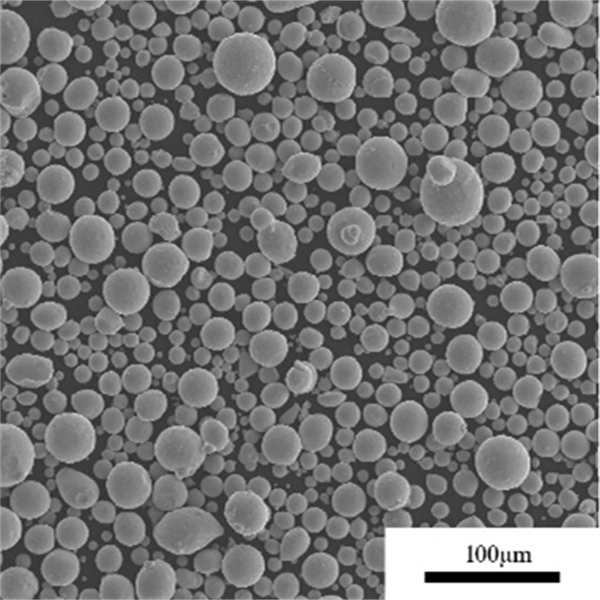
Applications of Metal Powders for PBF Technique
Applications Overview
Powder Type | Applications |
---|---|
Titanium Alloy (Ti6Al4V) | Aircraft components, medical implants |
Stainless Steel (316L) | Food processing equipment, surgical tools |
Inconel 718 | Jet engine parts, gas turbine components |
Aluminum Alloy (AlSi10Mg) | Automotive parts, lightweight structural components |
Cobalt Chrome (CoCr) | Dental prostheses, hip and knee implants |
Maraging Steel | Aerospace structures, high-strength tooling |
Copper Alloy (CuCrZr) | Electrical connectors, heat exchangers |
Tungsten Carbide | Drill bits, cutting tools |
Tool Steel (H13) | Injection molds, die casting dies |
Nickel Alloy (Ni625) | Marine equipment, chemical plant components |
Specifications, Sizes, Grades, and Standards
Specifications and Standards
Powder Type | Specifications | Sizes | Grades | Standards |
---|---|---|---|---|
Titanium Alloy (Ti6Al4V) | ASTM F2924, AMS 4998 | 15-45 microns | Grade 5, Grade 23 | ASTM, AMS |
Stainless Steel (316L) | ASTM A276, F138 | 10-50 microns | 316L | ASTM, ISO |
Inconel 718 | AMS 5662, ASTM B637 | 15-53 microns | AMS 5662 | AMS, ASTM |
Aluminum Alloy (AlSi10Mg) | DIN EN 1706, AMS 4289 | 20-63 microns | AlSi10Mg | DIN, AMS |
Cobalt Chrome (CoCr) | ASTM F75, ISO 5832-4 | 10-45 microns | F75 | ASTM, ISO |
Maraging Steel | AMS 6514, ASTM A538 | 20-50 microns | Grade 250, Grade 300 | AMS, ASTM |
Copper Alloy (CuCrZr) | ASTM B224, DIN 17670 | 15-45 microns | CuCrZr | ASTM, DIN |
Tungsten Carbide | ISO 9001:2008 | 1-15 microns | Various grades | ISO |
Tool Steel (H13) | ASTM A681, DIN 1.2344 | 15-45 microns | H13 | ASTM, DIN |
Nickel Alloy (Ni625) | AMS 5666, ASTM B446 | 15-50 microns | UNS N06625 | AMS, ASTM |
Suppliers and Pricing Details
Supplier and Pricing Overview
Powder Type | Supplier | Price (per kg) | Region |
---|---|---|---|
Titanium Alloy (Ti6Al4V) | Advanced Powders & Coatings | $300 | North America |
Stainless Steel (316L) | Carpenter Technology Corporation | $50 | Global |
Inconel 718 | Praxair Surface Technologies | $200 | Global |
Aluminum Alloy (AlSi10Mg) | ECKART TLS GmbH | $70 | Europe, North America |
Cobalt Chrome (CoCr) | Arcam AB | $350 | Global |
Maraging Steel | Höganäs AB | $100 | Europe, North America |
Copper Alloy (CuCrZr) | Tekna Plasma Systems Inc. | $80 | North America, Europe |
Tungsten Carbide | Global Tungsten & Powders Corp. | $400 | Global |
Tool Steel (H13) | Sandvik AB | $60 | Global |
Nickel Alloy (Ni625) | LPW Technology Ltd | $220 | Europe, North America |
Comparative Advantages and Limitations of Metal Powders for PBF Technique
Comparison Overview
Powder Type | Advantages | Limitations |
---|---|---|
Titanium Alloy (Ti6Al4V) | High strength-to-weight ratio, corrosion-resistant | Expensive, reactive to oxygen and nitrogen |
Stainless Steel (316L) | Excellent corrosion resistance, widely available | Lower strength compared to titanium |
Inconel 718 | High temperature resistance, good mechanical properties | Expensive, difficult to machine |
Aluminum Alloy (AlSi10Mg) | Lightweight, good thermal properties | Lower strength, prone to cracking |
Cobalt Chrome (CoCr) | High wear resistance, biocompatible | Very hard, difficult to machine |
Maraging Steel | High strength, good toughness | Expensive, requires aging heat treatment |
Copper Alloy (CuCrZr) | Excellent thermal and electrical conductivity | Prone to oxidation, challenging to process |
Tungsten Carbide | Extreme hardness, wear resistance | Very brittle, difficult to process |
Tool Steel (H13) | High hardness, good thermal fatigue resistance | Requires post-processing heat treatments |
Nickel Alloy (Ni625) | Corrosion resistance, high strength | Expensive, difficult to machine |
Detailed Descriptions of Specific Metal Powder Models
Titanium Alloy (Ti6Al4V)
One of the most widely used titanium alloys in PBF is Ti6Al4V, also known as Grade 5. It offers an excellent combination of high strength, low weight, and corrosion resistance, making it ideal for aerospace and medical applications. Ti6Al4V is particularly valued for its high fatigue strength and ability to withstand extreme temperatures, making it suitable for critical components in jet engines and spacecraft. However, it is expensive and highly reactive, requiring careful handling during the PBF process to prevent contamination.
Stainless Steel (316L)
316L stainless steel is a popular choice due to its excellent corrosion resistance and good mechanical properties. This alloy is used in a wide range of applications, from food processing equipment to medical instruments, thanks to its biocompatibility and ease of sterilization. 316L can be processed effectively with PBF, resulting in parts with high density and fine detail. The lower cost compared to other high-performance alloys makes it an attractive option for various industries.
Inconel 718
Inconel 718 is a nickel-chromium alloy known for its exceptional high-temperature performance and good mechanical properties. It is widely used in the aerospace industry for turbine blades and other components that must withstand extreme conditions. Inconel 718’s high strength and resistance to oxidation make it suitable for demanding applications, although its processing can be challenging due to its toughness and
tendency to work harden.
Aluminum Alloy (AlSi10Mg)
AlSi10Mg is a lightweight aluminum alloy commonly used in the automotive and aerospace industries for structural components. Its good thermal properties and low density make it ideal for applications where weight savings are crucial. AlSi10Mg can be processed efficiently with PBF, resulting in parts with good surface finish and mechanical properties. However, its lower strength compared to other alloys requires careful consideration in load-bearing applications.
Cobalt Chrome (CoCr)
Cobalt Chrome alloys are renowned for their high wear resistance and biocompatibility, making them ideal for medical implants and dental prostheses. CoCr alloys can withstand the harsh environments of the human body without degrading, and their high hardness ensures long-lasting performance. The primary challenge with CoCr is its difficulty to machine, often requiring specialized equipment and techniques.
Maraging Steel
Maraging steels are known for their high strength and toughness, achieved through a process of martensitic transformation followed by aging. These steels are used in high-stress applications such as aerospace structures and tooling. Maraging steel parts produced via PBF are highly dense and require minimal post-processing, although the material’s cost and the need for heat treatment can be drawbacks.
Copper Alloy (CuCrZr)
CuCrZr is a copper alloy with excellent thermal and electrical conductivity, making it ideal for electrical components and heat exchangers. Its use in PBF is limited by its tendency to oxidize and the difficulty of processing due to its high thermal conductivity. However, advancements in powder production and PBF technology are improving the viability of CuCrZr for complex and high-performance applications.
Tungsten Carbide
Tungsten Carbide is valued for its extreme hardness and wear resistance, making it suitable for cutting tools and wear parts. Its brittleness and difficulty to process are significant challenges, but when successfully printed with PBF, Tungsten Carbide parts exhibit excellent durability and performance in harsh environments.
Tool Steel (H13)
H13 tool steel is widely used for injection molding and die casting due to its high hardness and good thermal fatigue resistance. PBF allows for the production of complex tool steel components with intricate geometries, reducing the need for assembly and improving tool life. Post-processing heat treatments are typically required to achieve optimal mechanical properties.
Nickel Alloy (Ni625)
Ni625 is a versatile nickel alloy with excellent corrosion resistance and high strength, used in marine and chemical processing environments. Its ability to withstand harsh conditions without degrading makes it suitable for critical applications. Processing Ni625 with PBF can be challenging due to its toughness, but the resulting parts offer excellent performance and durability.
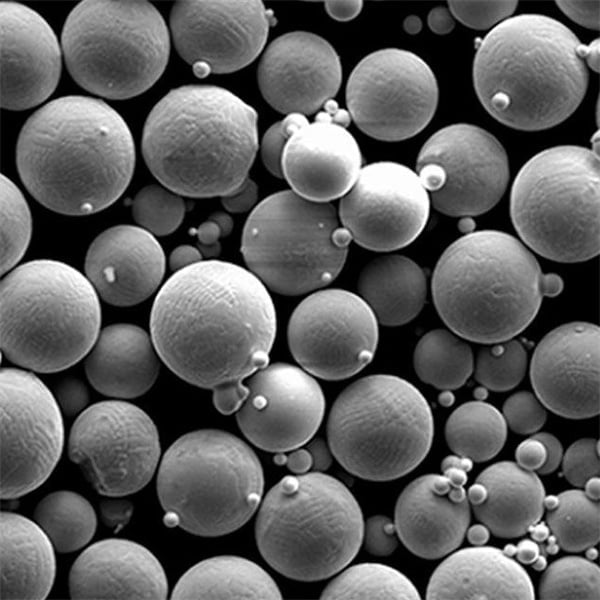
FAQ
Question | Answer |
---|---|
What is Powder Bed Fusion (PBF)? | PBF is an additive manufacturing process that uses a laser or electron beam to fuse powdered material layer by layer to create complex parts. |
What factors should I consider when choosing metal powder for PBF? | Consider the material’s properties, application requirements, cost, and compatibility with PBF technology. |
Why is Ti6Al4V popular in aerospace applications? | Ti6Al4V offers high strength, low weight, and excellent corrosion resistance, making it ideal for aerospace components. |
Can 316L stainless steel be used for medical implants? | Yes, 316L is biocompatible and resistant to corrosion, making it suitable for medical devices and implants. |
What are the advantages of using Inconel 718? | Inconel 718 provides exceptional high-temperature performance and good mechanical properties, ideal for aerospace and turbine applications. |
Why choose AlSi10Mg for automotive parts? | AlSi10Mg is lightweight with good thermal properties, making it ideal for reducing vehicle weight and improving fuel efficiency. |
How does CoCr benefit medical applications? | CoCr alloys are biocompatible and have high wear resistance, making them ideal for long-lasting medical implants. |
What makes maraging steel suitable for tooling? | Maraging steel offers high strength and toughness, essential for high-stress applications like tooling and aerospace structures. |
What are the challenges of using CuCrZr in PBF? | CuCrZr is prone to oxidation and challenging to process due to its high thermal conductivity, but it offers excellent thermal and electrical conductivity. |
Is Tungsten Carbide suitable for wear parts? | Yes, Tungsten Carbide’s extreme hardness and wear resistance make it ideal for cutting tools and wear parts in harsh environments. |
Conclusion
Choosing the right metal powder for PBF is essential for ensuring the quality and performance of the final product. Each type of metal powder offers unique properties and advantages, making it suitable for specific applications. By understanding the characteristics, applications, and limitations of each powder type, manufacturers can make informed decisions to optimize their PBF processes and achieve the best results. Whether you’re working with titanium alloys for aerospace components or stainless steel for medical devices, the right choice of metal powder will significantly impact the success of your additive manufacturing projects.
This guide has provided an in-depth look at various metal powders for PBF, including detailed descriptions, specifications, and comparisons. By leveraging this information, you can select the most appropriate powder for your needs, ensuring high-quality, durable, and efficient production.
Share On
MET3DP Technology Co., LTD is a leading provider of additive manufacturing solutions headquartered in Qingdao, China. Our company specializes in 3D printing equipment and high-performance metal powders for industrial applications.
Inquiry to get best price and customized Solution for your business!
Related Articles
About Met3DP
Recent Update
Our Product
CONTACT US
Any questions? Send us message now! We’ll serve your request with a whole team after receiving your message.
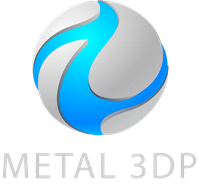
Metal Powders for 3D Printing and Additive Manufacturing