Powder for Weld
Table of Contents
When it comes to welding, the choice of materials can make all the difference between a solid, durable weld and a weak, flawed joint. One critical component in certain types of welding is the metal powder used. But what exactly is powder for weld, and why is it so important? This guide will dive deep into the world of welding powders, exploring everything from specific metal powder models to their applications, advantages, disadvantages, and more.
Overview of Welding Powders
Welding powders are finely ground metal particles used in various welding processes, including powder welding and laser cladding. These powders enhance weld quality by providing a controlled, homogeneous material that can be evenly distributed during the welding process. They are critical in industries requiring high precision and performance, such as aerospace, automotive, and heavy machinery.
Key Details of Welding Powders
Feature | Description |
---|---|
Composition | Pure metals, alloys, composite materials |
Properties | High melting point, excellent flowability, uniform particle size |
Applications | Repair and maintenance, surface coating, additive manufacturing |
Advantages | Consistent quality, enhanced weld strength, precision |
Disadvantages | Cost, need for specialized equipment |
Standards | ASTM, ISO, DIN standards for quality and performance |
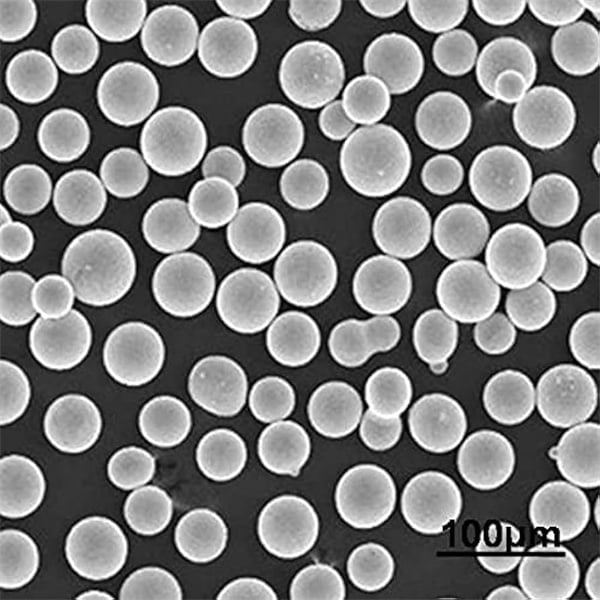
Specific Metal Powder Models for Welding
To help you navigate the market, here are ten specific metal powder models commonly used in welding, each with its unique properties and applications:
- Metco 42C
- Composition: Nickel-chromium-boron-silicon alloy
- Properties: Excellent corrosion resistance, high hardness
- Applications: Surface coating, wear resistance applications
- Höganäs AM 50
- Composition: Iron-based alloy with carbon and chromium
- Properties: High strength, good ductility
- Applications: Additive manufacturing, repair welding
- AMETEK Grade 316L
- Composition: Stainless steel (316L)
- Properties: Corrosion resistance, high toughness
- Applications: Medical devices, food processing equipment
- Carpenter 20
- Composition: Nickel-iron-chromium alloy
- Properties: Excellent resistance to acid and alkali corrosion
- Applications: Chemical processing, marine environments
- Oerlikon Metco 53NS
- Composition: Nickel-chromium alloy
- Properties: Oxidation resistance, thermal stability
- Applications: High-temperature environments, gas turbines
- Sandvik Osprey 25
- Composition: Cobalt-chromium alloy
- Properties: High wear resistance, good toughness
- Applications: Aerospace components, dental implants
- Kennametal Stellite 6
- Composition: Cobalt-based alloy with chromium and tungsten
- Properties: Extreme wear and corrosion resistance
- Applications: Valve seats, bearings, cutting tools
- H.C. Starck Refractory Metals TZM
- Composition: Titanium-zirconium-molybdenum alloy
- Properties: High temperature resistance, excellent strength
- Applications: Aerospace, nuclear reactors
- Eutectic Castolin 11718
- Composition: Nickel-based alloy
- Properties: High hardness, good wear resistance
- Applications: Mining equipment, industrial machinery
- Praxair NiCrAlY
- Composition: Nickel-chromium-aluminum-yttrium alloy
- Properties: Oxidation and corrosion resistance
- Applications: Thermal barrier coatings, turbine blades
Properties and Characteristics of Welding Powders
Understanding the properties and characteristics of welding powders is essential to selecting the right material for your specific application. Here’s a closer look at what makes these powders unique:
Properties of Welding Powders
Property | Description |
---|---|
Melting Point | Typically high, varies with composition |
Flowability | Important for even distribution |
Particle Size | Uniform size ensures consistent quality |
Purity | High purity reduces contamination risk |
Hardness | Varies depending on alloy composition |
Corrosion Resistance | Essential for harsh environments |
Characteristics of Popular Welding Powders
Powder Model | Melting Point (°C) | Hardness (HV) | Corrosion Resistance | Flowability |
---|---|---|---|---|
Metco 42C | 1050 | 600 | Excellent | Good |
Höganäs AM 50 | 1450 | 250 | Moderate | Excellent |
AMETEK Grade 316L | 1400 | 220 | High | Good |
Carpenter 20 | 1370 | 200 | Very High | Moderate |
Oerlikon Metco 53NS | 1400 | 500 | High | Excellent |
Sandvik Osprey 25 | 1330 | 400 | Good | Good |
Kennametal Stellite 6 | 1380 | 600 | Very High | Moderate |
H.C. Starck TZM | 2600 | 350 | Good | Poor |
Eutectic Castolin 11718 | 1350 | 450 | Moderate | Good |
Praxair NiCrAlY | 1370 | 350 | High | Excellent |
Applications of Welding Powders
Welding powders are used in various applications across multiple industries. Here’s a breakdown of where these powders are typically employed:
Common Applications
Application | Description |
---|---|
Repair and Maintenance | Used for rebuilding worn-out parts, enhancing their lifespan |
Surface Coating | Provides protective coatings to resist wear and corrosion |
Additive Manufacturing | Used in 3D printing for creating complex metal parts |
Thermal Spraying | Creates thermal barriers in high-temperature environments |
Hardfacing | Applies hard, wear-resistant surfaces on tools and machinery |
Industry-Specific Uses
Industry | Applications |
---|---|
Aerospace | Coating turbine blades, repairing airframe components |
Automotive | Repairing engine parts, enhancing surface durability |
Medical | Manufacturing surgical tools, prosthetic implants |
Oil and Gas | Coating pipelines, repairing drilling equipment |
Heavy Machinery | Rebuilding heavy-duty equipment, enhancing wear resistance |
Specifications, Sizes, Grades, and Standards
Choosing the right welding powder requires understanding its specifications, available sizes, grades, and adherence to industry standards. Here’s a detailed look:
Specifications and Sizes
Powder Model | Particle Size Range (µm) | Available Grades |
---|---|---|
Metco 42C | 45-125 | Standard, Fine |
Höganäs AM 50 | 20-63 | Standard, Extra Fine |
AMETEK Grade 316L | 15-45 | Medical, Industrial |
Carpenter 20 | 50-150 | Industrial |
Oerlikon Metco 53NS | 15-53 | High Performance |
Sandvik Osprey 25 | 10-45 | Biomedical |
Kennametal Stellite 6 | 44-105 | Wear Resistant |
H.C. Starck TZM | 50-150 | Aerospace, Nuclear |
Eutectic Castolin 11718 | 53-180 | Heavy Duty |
Praxair NiCrAlY | 10-63 | Thermal Spray |
Industry Standards
Standard | Description |
---|---|
ASTM | Ensures material properties and quality |
ISO | International standards for consistency |
DIN | German standards for precision and quality |
AMS | Aerospace material standards |
NACE | Corrosion resistance standards |
Suppliers and Pricing Details
Finding the right supplier for welding powders can be challenging. Here’s a list of some prominent suppliers and an idea of the pricing:
Major Suppliers
Supplier | Powder Models Offered | Pricing (per kg) |
---|---|---|
Oerlikon Metco | Metco 42C, Metco 53NS | $100 – $150 |
Höganäs AB | AM 50 | $80 – $120 |
AMETEK | Grade 316L | $90 – $140 |
Carpenter Technology | Carpenter 20 | $110 – $160 |
Sandvik | Osprey 25 | $130 – $180 |
Kennametal | Stellite 6 | $150 – $200 |
H.C. Starck | TZM | $200 – $250 |
Castolin Eutectic | 11718 | $100 – $150 |
Praxair | NiCrAlY | $120 – $170 |
Price Comparison
Powder Model | Low-End Price ($) | High-End Price ($) |
---|---|---|
Metco 42C | 100 | 150 |
Höganäs AM 50 | 80 | 120 |
AMETEK Grade 316L | 90 | 140 |
Carpenter 20 | 110 | 160 |
Oerlikon Metco 53NS | 130 | 180 |
Sandvik Osprey 25 | 130 | 180 |
Kennametal Stellite 6 | 150 | 200 |
H.C. Starck TZM | 200 | 250 |
Eutectic Castolin 11718 | 100 | 150 |
Praxair NiCrAlY | 120 | 170 |
Comparing Pros and Cons of Welding Powders
Each welding powder has its unique advantages and disadvantages. Here’s a comparison to help you decide which is best for your needs:
Advantages and Limitations
Powder Model | Advantages | Limitations |
---|---|---|
Metco 42C | High corrosion resistance, hard | Expensive, requires expertise |
Höganäs AM 50 | Good ductility, cost-effective | Moderate corrosion resistance |
AMETEK Grade 316L | Excellent toughness, corrosion-resistant | Higher cost |
Carpenter 20 | Superior acid resistance | High price |
Oerlikon Metco 53NS | Thermal stability, high performance | Complex application methods |
Sandvik Osprey 25 | High wear resistance | Moderate corrosion resistance |
Kennametal Stellite 6 | Extreme wear resistance | Expensive, limited ductility |
H.C. Starck TZM | High temperature capability | Poor flowability |
Eutectic Castolin 11718 | Good wear resistance | Moderate corrosion resistance |
Praxair NiCrAlY | High oxidation resistance | Requires specific equipment |
Detailed Comparison of Welding Powders
Performance Comparison
Powder Model | Wear Resistance | Thermal Stability | Corrosion Resistance |
---|---|---|---|
Metco 42C | High | Moderate | Excellent |
Höganäs AM 50 | Moderate | Moderate | Moderate |
AMETEK Grade 316L | Low | Moderate | High |
Carpenter 20 | Low | Moderate | Very High |
Oerlikon Metco 53NS | High | High | High |
Sandvik Osprey 25 | High | Moderate | Good |
Kennametal Stellite 6 | Very High | Moderate | Very High |
H.C. Starck TZM | Moderate | Very High | Good |
Eutectic Castolin 11718 | High | Moderate | Moderate |
Praxair NiCrAlY | Moderate | High | High |
Cost-Efficiency Comparison
Powder Model | Initial Cost | Long-Term Savings | Overall Value |
---|---|---|---|
Metco 42C | High | High | Excellent |
Höganäs AM 50 | Low | Moderate | Good |
AMETEK Grade 316L | High | High | Very Good |
Carpenter 20 | High | Very High | Excellent |
Oerlikon Metco 53NS | Moderate | High | Very Good |
Sandvik Osprey 25 | High | Moderate | Good |
Kennametal Stellite 6 | Very High | High | Very Good |
H.C. Starck TZM | Very High | High | Good |
Eutectic Castolin 11718 | Low | Moderate | Good |
Praxair NiCrAlY | Moderate | High | Very Good |
Advantages of Powder for Weld
1. Consistent Quality
Welding powders provide a consistent quality that is hard to achieve with other forms of welding materials. Their uniform particle size and composition ensure that every weld is strong and reliable.
2. Enhanced Weld Strength
By using welding powders, you can significantly enhance the strength of your welds. These powders fill in gaps and create a more uniform, solid joint compared to traditional welding methods.
3. Precision and Control
With welding powders, you have greater control over the welding process. The powders can be precisely applied, allowing for intricate and detailed welding that would be difficult with other materials.
4. Versatility
Welding powders are incredibly versatile and can be used in a variety of applications, from repairing worn-out parts to creating new components through additive manufacturing.
Disadvantages of Powder for Weld
1. Cost
One of the main disadvantages of using welding powders is the cost. These materials can be expensive, especially high-performance alloys, which might not be feasible for all budgets.
2. Specialized Equipment Needed
Using welding powders often requires specialized equipment and expertise. This can be a barrier for smaller operations or those without access to the necessary technology.
3. Handling and Storage
Welding powders need to be handled and stored carefully to maintain their quality. They are sensitive to moisture and contamination, which can affect their performance.
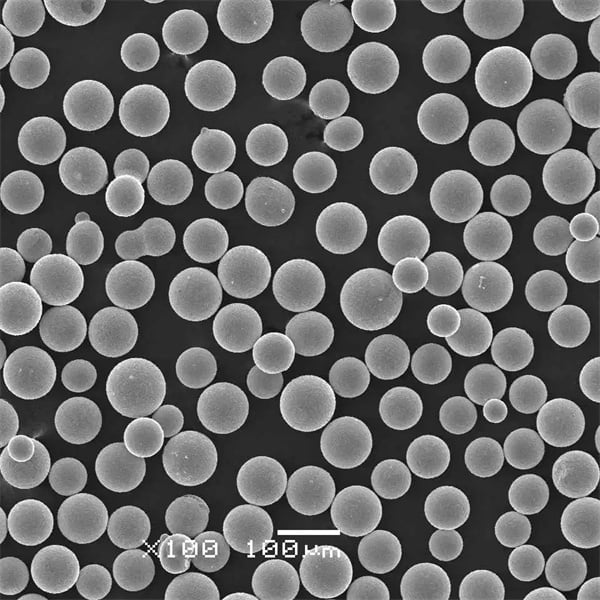
FAQs
Question | Answer |
---|---|
What are welding powders used for? | Welding powders are used for enhancing weld strength, surface coating, repair and maintenance, and additive manufacturing. |
How are welding powders applied? | They can be applied through various techniques such as powder welding, laser cladding, and thermal spraying. |
What is the advantage of using welding powders over traditional welding rods? | Welding powders offer greater control, consistent quality, and the ability to create more precise and durable welds. |
Are welding powders expensive? | Yes, they can be more expensive than traditional welding materials, but they offer enhanced performance and durability. |
Can welding powders be used in any welding process? | Not all welding processes can use powders; they are typically used in specialized techniques like powder welding and laser cladding. |
How do I store welding powders? | They should be stored in a dry, clean environment to prevent contamination and moisture absorption. |
Is special training required to use welding powders? | Yes, using welding powders often requires specialized training and equipment. |
What industries use welding powders the most? | Industries like aerospace, automotive, medical, and heavy machinery heavily rely on welding powders. |
Conclusion
Welding powders are a game-changer in the world of welding, offering unmatched precision, strength, and versatility. Whether you’re repairing a worn-out part or creating a high-performance component, choosing the right welding powder can make all the difference. While they come with their set of challenges, such as cost and the need for specialized equipment, the benefits they offer make them a valuable addition to any welding operation.
By understanding the specific properties and applications of various welding powders, you can make informed decisions that will enhance the quality and durability of your welds. So, the next time you’re faced with a welding project, consider the power of powder for weld and how it can take your work to the next level.
Share On
MET3DP Technology Co., LTD is a leading provider of additive manufacturing solutions headquartered in Qingdao, China. Our company specializes in 3D printing equipment and high-performance metal powders for industrial applications.
Inquiry to get best price and customized Solution for your business!
Related Articles
About Met3DP
Recent Update
Our Product
CONTACT US
Any questions? Send us message now! We’ll serve your request with a whole team after receiving your message.
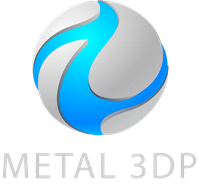
Metal Powders for 3D Printing and Additive Manufacturing