rotary atomization
Table of Contents
Rotary atomization, a technological marvel lurking beneath the seemingly mundane act of spraying, is a cornerstone of various industries. Imagine transforming a stream of liquid into a fine mist of tiny droplets – that’s the magic of rotary atomization. But this technology goes beyond mere aesthetics; it unlocks a world of possibilities, from creating high-performance metal powders for 3D printing to ensuring flawless paint jobs on your car.
This comprehensive guide delves into the intricate world of rotary atomization, unraveling its secrets and exploring its diverse applications. We’ll equip you with the knowledge to navigate this fascinating technology, from the fundamental principles to the nitty-gritty details. So, buckle up and prepare to be amazed by the power of a spinning disk!
How Rotary Atomization Works
At the heart of rotary atomization lies a deceptively simple concept – centrifugal force. Picture a high-speed spinning disc, cup, or wheel. Now, imagine feeding a liquid into this rapidly rotating contraption. As the liquid journeys through the spinning device, centrifugal forces take hold, flinging the liquid outwards with tremendous energy. Upon reaching the rim, the liquid is sheared into a fine mist of droplets, their size dictated by the rotation speed.
Think of it like a kid whirling a bucket of water around their head. The faster they spin, the more forcefully the water gets ejected, creating a spectacular (and potentially messy!) spray. Rotary atomization operates on the same principle, but with a touch more control and a whole lot less potential for soaking bystanders.
A Showcase of Powders Made with Rotary Atomization
Rotary atomization plays a starring role in the production of metal powders for 3D printing. These powders, the building blocks of incredible creations, wouldn’t exist without this ingenious technology. Here’s a glimpse into some of the most popular metal powders crafted using rotary atomization:
Metal Powder | Description | Applications |
---|---|---|
Stainless Steel 316L | An austenitic stainless steel known for its excellent corrosion resistance. | Aerospace components, medical implants, chemical processing equipment |
Titanium (Ti-6Al-4V) | A high-strength, low-weight titanium alloy commonly used in aerospace and biomedical applications. | Aircraft parts, prosthetic limbs, dental implants |
Inconel 625 | A superalloy renowned for its exceptional high-temperature strength and resistance to harsh environments. | Turbine blades, rocket engine components, heat exchangers |
Aluminum (AlSi10Mg) | A versatile aluminum alloy offering a good balance of strength, ductility, and castability. | Automotive components, electronic enclosures, architectural elements |
Copper | A highly conductive metal valued for its electrical and thermal properties. | Heat sinks, electrical conductors, electrodes |
Nickel | A versatile metal often used in combination with other metals to create alloys. | Catalysts, batteries, electroplating applications |
Cobalt-Chrome (CoCr) | A biocompatible alloy with excellent wear resistance, ideal for medical implants. | Hip and knee replacements, dental implants, surgical instruments |
Tool Steel | A group of steels formulated for exceptional hardness and wear resistance. | Cutting tools, dies, molds |
Tungsten | A very dense and high-melting point metal often used in combination with other metals. | Tungsten carbide cutting tools, filaments for incandescent lamps, ballistic armor |
Molybdenum | A refractory metal known for its high-temperature strength. | Missile components, heat shields, furnace parts |
This is just a sampling of the vast array of metal powders that rotary atomization helps bring to life. Each powder boasts unique properties that cater to specific applications. For instance, stainless steel 316L is a champion of corrosion resistance, making it perfect for medical implants that need to withstand the body’s harsh internal environment. On the other hand, titanium alloys like Ti-6Al-4V offer an unbeatable combination of lightness and strength, ideal for soaring through the skies in aircraft parts.
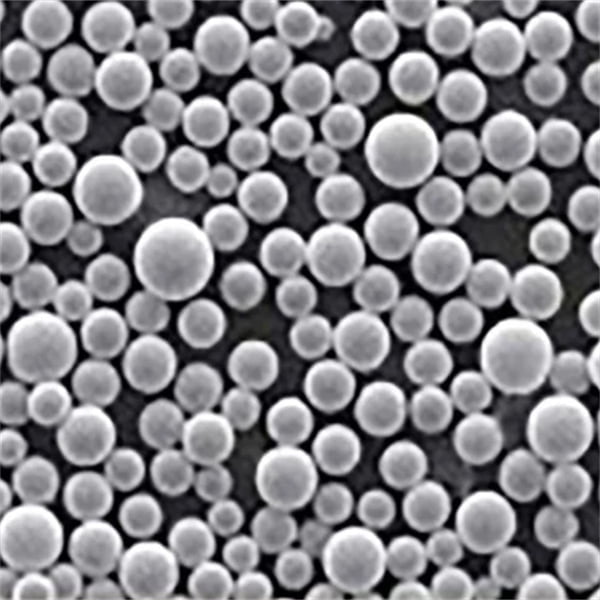
Applications of Rotary Atomization
Rotary atomization’s reach extends far beyond the realm of metal powders. This technology finds applications in a diverse range of industries, each leveraging its unique ability to create a fine mist of liquid droplets. Here are some of the most common applications:
- Spray Painting: Rotary atomizers ensure a smooth, even coat of paint on automobiles, furniture, and countless other objects. The precise control over droplet size allows painters to achieve a flawless finish, minimizing drips and splatters.
- Spray Drying: In the food industry, for example, rotary atomization helps create instant coffee, powdered milk, and baby formula. The rapid drying process facilitated by the fine droplets preserves the product’s qualities and extends its shelf life.
- Fuel Injection: Modern gasoline and diesel engines rely on rotary atomization to deliver a precisely metered spray of fuel into the combustion chamber. This ensures efficient combustion, maximizing engine performance and minimizing fuel consumption.
- Coating Applications: Rotary atomization plays a crucial role in applying thin and uniform coatings on various materials. These coatings can be functional, like corrosion-resistant layers on metals, or aesthetic, like the metallic sheen on car parts.
- Biomedical Applications: Beyond creating metal powders for 3D-printed implants, rotary atomization is used in processes like drug delivery and tissue engineering. The fine droplets offer a controlled and targeted way to deliver medications or create biocompatible scaffolds for cell growth.
- Agricultural Applications: Rotary atomizers help farmers apply pesticides, herbicides, and fertilizers more effectively. The fine mist ensures even coverage on crops, minimizing waste and maximizing the impact of these agricultural chemicals.
- Electronics Manufacturing: Rotary atomization is employed in the production of printed circuit boards (PCBs) by precisely depositing thin layers of conductive materials. This intricate process contributes to the miniaturization and functionality of modern electronics.
These are just a few examples of how rotary atomization weaves its magic across various industries. Its ability to create a controllable and uniform mist of droplets makes it an indispensable tool for diverse applications.
Advantages and Limitations of Rotary Atomization
No technology is perfect, and rotary atomization is no exception. While it offers numerous advantages, it also comes with limitations that need to be considered.
Advantages of Rotary Atomization:
- High Efficiency: Rotary atomizers achieve excellent atomization with minimal energy consumption compared to other methods like pressure nozzles.
- Uniform Droplet Size: The precise control over rotation speed allows for consistent droplet size distribution, crucial for achieving desired results in various applications.
- Wide Range of Applications: The versatility of rotary atomization makes it suitable for a vast array of processes, from spray painting to creating metal powders for 3D printing.
- Scalability: Rotary atomizers can be designed for various production capacities, catering to both small-scale and large-scale industrial applications.
- Relatively Simple Design: Compared to some atomization methods, rotary atomizers possess a simpler design, potentially reducing maintenance costs and complexity.
Disadvantages of Rotary Atomization:
- Shear Sensitivity: Some materials, particularly those with a high viscosity or containing large particles, can be sensitive to the shearing forces within the atomizer, potentially affecting product quality.
- Limited Droplet Size Range: While offering good control, rotary atomization may not be ideal for creating extremely fine droplets compared to some alternative methods.
- Potential for Clogging: Depending on the material being atomized, there’s a risk of clogging within the atomizer, requiring regular cleaning and maintenance.
- Noise Generation: The high-speed rotation of the atomizer disc can generate significant noise, which may necessitate additional noise control measures.
Understanding these advantages and limitations allows users to determine if rotary atomization is the best fit for their specific application.
Making the Choice: Rotary Atomization vs. Other Methods
When it comes to atomization, rotary atomization isn’t the only player in the game. Here’s a quick comparison of rotary atomization with two other common methods:
- Pressure Nozzles: These nozzles rely on pressurized gas or liquid to break up the liquid into droplets. While offering a wider range of droplet sizes, pressure nozzles can be less efficient and require higher energy consumption compared to rotary atomizers.
- Ultrasonic Atomization: This method uses high-frequency sound waves to create atomization. It excels at generating very fine droplets but can be more complex and expensive to implement compared to rotary atomization.
The choice between rotary atomization and other methods depends on several factors, including:
- Desired droplet size: For applications requiring extremely fine droplets, ultrasonic atomization might be a better choice.
- Material properties: Shear-sensitive materials may benefit from pressure nozzles or other methods that minimize shearing forces.
- Production volume: For high-volume applications, the efficiency and scalability of rotary atomization become significant advantages.
- Cost considerations: The initial investment and ongoing maintenance costs of each method should be factored into the decision.
Consulting with an expert in atomization technology can help you determine the most suitable method for your specific needs.
Specifications and Considerations
Selecting the right rotary atomizer requires careful consideration of several factors. Here’s a breakdown of some key specifications and aspects to ponder:
Types of Rotary Atomizers:
- Disc Atomizers: These feature a high-speed rotating disc that generates a hollow cone spray pattern. They are widely used for various applications due to their simplicity and efficiency.
- Cup Atomizers: Employing a rapidly spinning cup, these atomizers deliver a narrow, focused spray pattern. They are ideal for applications requiring precise control over droplet placement.
- Wheel Atomizers: These utilize a slotted wheel to create a sheet of liquid that breaks up into droplets due to centrifugal forces and air shearing. They offer a high capacity for atomization and are often used in large-scale industrial processes.
Factors to Consider When Choosing a Rotary Atomizer:
- Liquid Properties: The viscosity, density, and presence of solids in the liquid being atomized can influence the choice of atomizer type and disc design.
- Desired Droplet Size: Different atomizer designs and operating speeds can achieve varying droplet size ranges. Selecting the right combination is crucial for the application.
- Material Compatibility: The atomizer’s material construction needs to be compatible with the liquid being processed to avoid corrosion or contamination.
- Production Capacity: The atomizer’s capacity to handle the desired flow rate of the liquid is essential for efficient production.
- Maintenance Considerations: Ease of cleaning and maintenance should be factored in, especially for processes involving materials prone to clogging.
Additional Considerations:
- Automation Compatibility: For integration into automated production lines, selecting an atomizer compatible with automated control systems is crucial.
- Safety Features: Depending on the application, safety features like explosion-proof designs might be necessary.
- Environmental Regulations: Compliance with relevant environmental regulations regarding emissions or noise levels might influence the choice of atomizer.
Understanding the Costs
The cost of implementing rotary atomization goes beyond just the initial purchase price of the atomizer itself. Here’s a breakdown of some additional cost factors to consider:
- Installation: The cost of installing and integrating the atomizer into your production line.
- Maintenance: Regular cleaning and upkeep of the atomizer are essential for optimal performance.
- Energy Consumption: The energy required to operate the atomizer should be factored into the overall cost equation.
- Waste Disposal: Depending on the liquid being atomized, there might be costs associated with proper disposal of any waste generated during the process.
By carefully considering these specifications, factors, and costs, you can make an informed decision when selecting the most suitable rotary atomizer for your specific application.
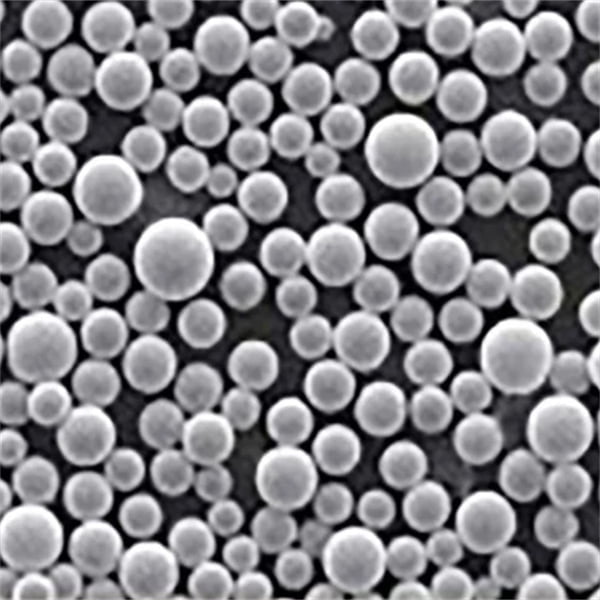
FAQ
Q: What are the advantages of rotary atomization over other atomization methods?
A: Rotary atomization offers several advantages, including high efficiency, consistent droplet size distribution, versatility across applications, scalability for various production volumes, and a relatively simple design for potentially lower maintenance costs.
Q: What are the limitations of rotary atomization?
A: Some limitations include challenges with shear-sensitive materials, a limited range of achievable droplet sizes compared to some methods, potential for clogging, and noise generation requiring control measures.
Q: What are some common applications of rotary atomization?
A: Rotary atomization finds applications in spray painting, spray drying, fuel injection, coating applications, biomedical processes, agricultural applications, and electronics manufacturing.
Q: How do I choose the right rotary atomizer for my needs?
A: Consider factors like the liquid properties, desired droplet size, material compatibility, production capacity, maintenance needs, automation compatibility, and safety features. Consulting with an expert in atomization technology is recommended for tailored advice.
Q: Where can I buy a rotary atomizer?
A: Several manufacturers offer rotary atomizers. Researching reputable suppliers and requesting quotes specific to your needs is essential.
Share On
MET3DP Technology Co., LTD is a leading provider of additive manufacturing solutions headquartered in Qingdao, China. Our company specializes in 3D printing equipment and high-performance metal powders for industrial applications.
Inquiry to get best price and customized Solution for your business!
Related Articles
About Met3DP
Recent Update
Our Product
CONTACT US
Any questions? Send us message now! We’ll serve your request with a whole team after receiving your message.
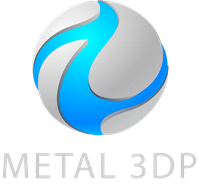
Metal Powders for 3D Printing and Additive Manufacturing
COMPANY
PRODUCT
cONTACT INFO
- Qingdao City, Shandong, China
- [email protected]
- [email protected]
- +86 19116340731