The Rotating Electrode Process
Table of Contents
Imagine a process that transforms a solid metal rod into a swarm of tiny, near-perfect spheres – the building blocks for cutting-edge 3D printing and other advanced applications. This is the magic of the Rotating Electrode Process (REP), a marvel of physics and material science that we’re about to delve into.
Process Principle of the Rotating Electrode Process
The REP, sometimes called the Plasma Rotating Electrode Process (PREP), operates like a high-tech ballet within a sealed chamber. Here’s a breakdown of the key steps:
Stage | Description | Function |
---|---|---|
Plasma Generation | Inert gas (typically argon or nitrogen) is introduced into a chamber and subjected to high temperatures or electromagnetic fields. This process strips electrons from the gas atoms, creating a hot, ionized gas called plasma. | The plasma serves two crucial functions. First, it acts as a highly concentrated heat source to melt the feedstock material (the electrode). Second, the inert nature of the plasma minimizes contamination of the molten metal. |
Feedstock Electrode Rotation | A rod of the target metal (the feedstock) is secured within the chamber and spun at high speeds (several thousand RPMs). | The rapid rotation of the electrode creates a strong centrifugal force. This force plays a vital role in the atomization process later. |
Plasma Melting | The high-temperature plasma torch is directed towards the tip of the rotating electrode. The intense heat from the plasma rapidly melts the metal at the point of contact. | Molten metal forms a small pool at the tip of the rotating electrode. The properties of the plasma (temperature and gas composition) can be adjusted to achieve precise control over the melting rate and minimize overheating. |
Metal Atomization | The interplay between the molten metal pool and the centrifugal force becomes crucial at this stage. As the molten metal accumulates at the tip of the rapidly spinning electrode, the centrifugal force overcomes the surface tension of the liquid metal. | The molten metal gets flung outwards from the tip of the electrode due to the centrifugal force. This action breaks the molten metal into tiny droplets. The size and distribution of these droplets are primarily influenced by the rotation speed and the properties of the molten metal. |
Solidification | The ejected metal droplets rapidly cool and solidify as they travel through the chamber’s inert gas environment. The rapid cooling promotes the formation of a fine-grained microstructure within the solidified particles. | Solidification typically occurs within milliseconds due to the small size of the droplets and the cool surrounding gas. This rapid solidification process can lead to the formation of unique metastable phases or extended solid solutions that wouldn’t be achievable with slower cooling rates. |
Powder Collection | The chamber is equipped with a collection system designed to capture the solidified metal particles. The specific design of the collection system can vary depending on the desired characteristics of the final powder. | Inert gas flow patterns within the chamber and strategically placed baffles or filters can be used to achieve the desired particle size distribution and morphology. |
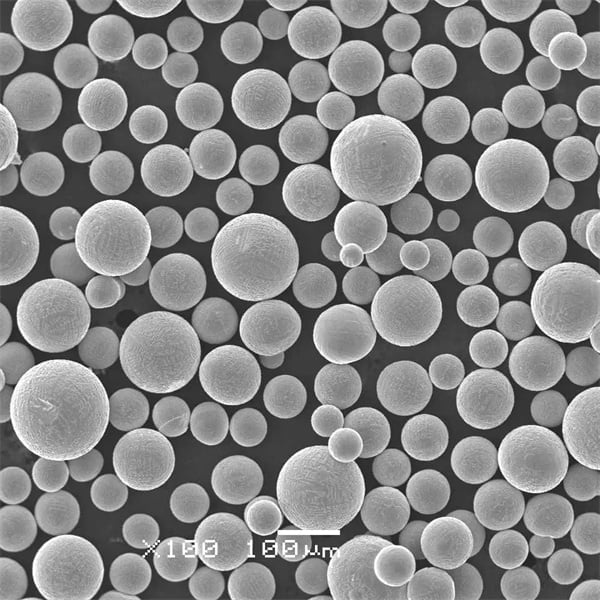
Process Characteristics of the Rotating Electrode Process
Feature | Description | Advantage |
---|---|---|
Feedstock Material | The REP process can handle a wide variety of feedstock materials, including metals, alloys, ceramics, and even some polymers. | This versatility allows for the production of powders and coatings with a wide range of properties. |
Melting Mechanism | In REP, a high-intensity heat source, typically a plasma torch or induction coil, melts the feedstock material. | This rapid and localized melting minimizes contamination and allows for precise control over the process temperature. |
Electrode Rotation | A key feature of REP is the rotation of the electrode. This rotation serves several purposes: | * Centrifugal Force: The rotation creates a centrifugal force that throws molten droplets off the tip of the electrode. This force helps to create uniformly sized particles and reduces the formation of satellites (smaller particles attached to larger ones). * Fresh Surface Exposure: As the electrode rotates, a fresh surface is constantly exposed to the molten material, promoting efficient melting and preventing overheating. * Enhanced Mixing: The rotation also helps to promote mixing within the molten pool, leading to a more homogeneous material. |
Particle Formation | The molten droplets ejected from the electrode solidify rapidly due to the small size and exposure to a cooler environment. | This rapid solidification results in powders with a fine grain structure and minimal internal defects. |
Particle Morphology | One of the most significant advantages of REP is the ability to produce spherical particles. | Spherical particles offer several advantages in additive manufacturing and other applications, including: * Improved Flowability: Spherical particles flow more easily, leading to better packing density in powders used for 3D printing and other powder-bed processes. * Reduced Segregation: Spherical particles are less prone to segregation, which can occur during handling and storage of non-spherical powders. * Enhanced Packing Density: The close packing of spherical particles allows for higher packing densities, which can be beneficial in applications such as electrodes for batteries. |
Particle Size Distribution | The REP process allows for good control over the particle size distribution of the produced powder. | This control is achieved by adjusting various process parameters such as rotation speed, feedstock feed rate, and plasma power. A narrow particle size distribution is desirable for many applications, as it ensures consistent material properties. |
Surface Area | Due to the formation of spherical particles, the REP process produces powders with a lower specific surface area compared to irregularly shaped particles. | This lower surface area can be advantageous in applications where high surface area is not required, such as in some coatings or thermal spray applications. However, for applications where a high surface area is desired, such as in some catalysts or electrodes, alternative powder production methods may be more suitable. |
Purity | The REP process can produce powders with a high degree of purity. | This is due to the minimal interaction between the molten material and the surrounding environment. The use of an inert atmosphere further minimizes contamination. High purity powders are essential for many high-performance applications. |
Metal Powder Applications of the Rotating Electrode Process
The REP-produced metal powders find application in a wide range of industries:
Application | Desired Powder Properties | Advantages of REP Powders |
---|---|---|
Additive Manufacturing (AM) Techniques: | * Fine particle size for high resolution printing * Spherical morphology for good flowability and packing density * Narrow particle size distribution for consistent material properties * High purity for high-quality final parts | * REP powders are well-suited for various AM techniques such as Selective Laser Melting (SLM) and Electron Beam Melting (EBM) due to their fine size, spherical shape, and narrow size distribution. These characteristics enable precise control over the printing process and lead to high-density, high-strength final parts. * The high purity of REP powders minimizes the risk of defects and impurities in the finished product. |
Metal Injection Molding (MIM): | * Fine and spherical particles for good packing density and mold filling * Narrow size distribution for dimensional accuracy * Controlled surface area for proper sintering behavior | * The spherical morphology and good flowability of REP powders allow for efficient mold filling during MIM, leading to improved dimensional accuracy and surface finish of the final parts. * The narrow particle size distribution ensures consistent material properties throughout the molded part. * The ability to control the surface area of REP powders can be beneficial for tailoring the sintering behavior and achieving the desired mechanical properties in the final product. |
Thermal Spray Coatings: | * Spherical particles for good deposition efficiency and splat bonding * Powders with good flowability for smooth and uniform coatings * Powders with appropriate size for the desired coating thickness | * The spherical shape of REP powders allows for efficient deposition during thermal spraying processes like plasma spraying and high-velocity oxy-fuel (HVOF) spraying. Spherical particles have good splat bonding characteristics, leading to strong adhesion between the deposited layers and the substrate. * The good flowability of REP powders enables the formation of smooth and uniform coatings with minimal surface defects. * By controlling the particle size of REP powders, the thickness of the thermal spray coating can be precisely tailored for the specific application. |
Friction Welding: | * Clean and spherical particles for good flow and material consolidation * Powders with controlled size and melting point for optimized welding process | * REP powders are suitable for friction welding applications due to their spherical shape and clean surfaces. These characteristics ensure good flowability during the welding process and promote strong material consolidation at the weld interface. * The ability to control the size and melting point of REP powders allows for optimization of the welding process parameters for different materials and joint configurations. |
Electrical and Electronic Applications: | * High purity powders for minimal electrical resistivity * Powders with controlled morphology for tailored electrical properties * Spherical powders for improved packing density in electrodes | * The high purity of REP powders minimizes electrical resistivity, making them suitable for applications such as battery electrodes and electrical conductors. * The ability to control the morphology and surface area of REP powders allows for tailoring their electrical properties for specific applications. For example, spherical powders can be beneficial for achieving high packing density in battery electrodes, which improves the energy density of the battery. |
Metal Powders Produced by the Rotating Electrode Process
The REP can handle a wide variety of metals, but here are 10 specific metal powder models with their unique characteristics:
Metal Powder Model | Description |
---|---|
Gas-Atomized Titanium Powder (Ti-6Al-4V) | This workhorse alloy is widely used in AM for aerospace components due to its high strength-to-weight ratio and excellent corrosion resistance. REP-produced Ti-6Al-4V powder offers superior flowability and low oxygen content for reliable printing. |
Gas-Atomized Nickel Superalloy Powder (Inconel 718) | Inconel 718 is a high-performance nickel-chromium superalloy known for its exceptional strength at high temperatures. REP-produced Inconel 718 powder enables the creation of complex, high-temperature components for jet engines, gas turbines, and other demanding applications. |
Gas-Atomized Aluminum Powder (AA2024) | AA2024 is a high-strength aluminum alloy commonly used in the aerospace industry. REP-produced AA2024 powder offers excellent strength-to-weight ratio and good machinability, making it ideal for lightweight aircraft components. |
Gas-Atomized Copper Powder (Cu) | Copper is a vital material for electrical applications due to its excellent conductivity. REP-produced copper powder offers high purity, tight particle size distribution, and good flowability for applications in thermal spraying, brazing, and conductive inks. |
Metal Powder Model | Description |
---|---|
Gas-Atomized Stainless Steel Powder (316L) | This versatile stainless steel grade offers excellent corrosion resistance and good formability. REP-produced 316L powder finds applications in medical implants, chemical processing equipment, and other applications requiring high corrosion resistance. |
Gas-Atomized Cobalt Chrome Powder (CoCr) | A biocompatible alloy commonly used for medical implants like hip and knee replacements. REP-produced CoCr powder offers high strength, wear resistance, and biocompatibility, making it ideal for long-lasting implants. |
Gas-Atomized Tungsten Powder (W) | Tungsten is a high-density metal known for its exceptional heat resistance. REP-produced tungsten powder is used in applications like welding electrodes, heat sinks, and armor due to its high melting point and mechanical strength. |
Gas-Atomized Molybdenum Powder (Mo) | Molybdenum is another high-temperature metal with good strength and corrosion resistance. REP-produced molybdenum powder finds applications in heating elements, electrodes, and rocket engine components. |
Gas-Atomized Niobium Powder (Nb) | Niobium is a superconductor at low temperatures and finds application in MRI machines and other scientific equipment. REP-produced niobium powder offers high purity and controlled particle size for reliable superconductor performance. |
Gas-Atomized Tantalum Powder (Ta) | Tantalum is a corrosion-resistant metal with a high melting point. REP-produced tantalum powder is used in capacitors, surgical implants, and other applications requiring high corrosion resistance and biocompatibility. |
Selection Considerations for Metal Powders from the Rotating Electrode Process
Choosing the right REP metal powder depends on the intended application. Here are some key factors to consider:
- Material Properties: Match the powder’s properties (strength, corrosion resistance, etc.) to the application’s requirements.
- Particle Size: The desired final product may dictate a specific particle size range for optimal processing.
- Flowability: Powders with good flowability ensure efficient handling and minimize processing issues.
- Oxygen Content: For certain metals like titanium and tantalum, low oxygen content is crucial for optimal performance.
- Cost: The cost of the powder can vary depending on the metal and its processing requirements.
Typical Specifications, Sizes, and Grades of Metal Powders from REP
Here’s a table outlining typical specifications, sizes, and grades of some commonly used REP metal powders:
Metal Powder | Particle Size (µm) | Grades | Typical Applications |
---|---|---|---|
Ti-6Al-4V | 25-100 | CP (commercially pure), ASTM F3056 | Aerospace components, medical implants |
Inconel 718 | 15-100 | AMS 5662 | Jet engine components, gas turbines |
AA2024 | 15-75 | AA2024 | Aircraft components, heat exchangers |
Cu | 10-100 | C1010, C1100 | Thermal spraying, brazing, conductive inks |
316L | 15-100 | 316L | Medical implants, chemical processing equipment |
CoCr | 10-50 | ASTM F75 | Medical implants, hip and knee replacements |
W | 2-50 | Pure Tungsten | Welding electrodes, heat sinks, armor |
Mo | 3-75 | High purity (99.9%) | Heating elements, electrodes, rocket engine components |
Nb | 10-50 | RRR grade (high purity) | MRI machines, superconductors |
Ta | 10-45 | ASTM F752 | Capacitors, surgical implants |
Suppliers and Pricing of Metal Powders from REP
Several reputable suppliers offer REP metal powders. Pricing can vary depending on the specific metal, particle size, quantity, and market fluctuations. Here’s a table with a general overview (note: specific pricing may require contacting suppliers):
Metal Powder | Typical Suppliers | Price Range (USD/kg) |
---|---|---|
Ti-6Al-4V | AP Powder, Höganäs, AMETEK SMP | $50-150 |
Inconel 718 | Special Metals Corporation, Carpenter Additive, Aubert & Duval | $100-200 |
AA2024 | AMETEK SMP, Höganäs, Sandvik Hyperion | $20- |
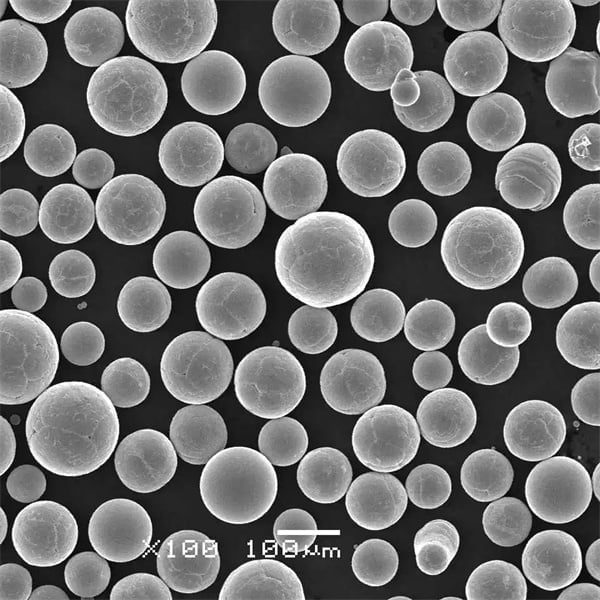
Advantages and Disadvantages of Metal Powders from REP
Advantages:
- High Sphericity: REP powders boast near-perfect spherical shapes, ideal for smooth powder flow in AM and other processes.
- Tight Particle Size Distribution: The narrow range of particle sizes ensures consistent melting behavior and minimizes inconsistencies in the final product.
- Low Oxygen Content: The inert gas environment minimizes oxidation during processing, leading to powders with low oxygen content, crucial for some metals.
- High Purity: The REP process generally yields high-purity powders, essential for applications demanding optimal material properties.
- Wide Variety of Materials: The REP process can handle a vast array of metals, offering flexibility for diverse applications.
Disadvantages:
- Higher Cost: Compared to some other powder production methods, REP can be a costlier process, impacting the final powder price.
- Limited Production Rates: The REP process might have slower production rates compared to high-volume techniques, affecting availability for large-scale projects.
- Process Complexity: The REP setup and operation require expertise and specialized equipment, potentially limiting widespread adoption.
Applications – A Deeper Dive
We’ve briefly touched on REP metal powder applications, but let’s delve deeper into some specific examples:
- Aerospace: The high strength-to-weight ratio and excellent mechanical properties of REP-produced titanium and aluminum alloys make them ideal for aircraft components. These powders enable the creation of lightweight, high-performance parts for airframes, engines, and other aerospace applications.
- Medical Implants: The biocompatibility and corrosion resistance of REP-produced stainless steel, cobalt chrome, and tantalum powders make them suitable for medical implants. These powders allow for the creation of long-lasting, biocompatible implants like hip and knee replacements, improving patient outcomes.
- Automotive: The potential for weight reduction and design flexibility with AM is driving the use of REP aluminum and nickel superalloy powders in automotive applications. These powders can be used to create lightweight components for car bodies, wheels, and engine parts, improving fuel efficiency and performance.
- Electronics: The high purity and conductivity of REP copper powders make them valuable for electrical applications. These powders can be used in thermal spraying to create conductive coatings for electrical components or in brazing to join electrical components securely.
FAQ
Q: What are the benefits of using REP metal powders compared to other powder production methods?
A: REP powders offer superior sphericity, tight particle size distribution, low oxygen content, and high purity, leading to improved performance in AM and other applications.
Q: Are REP metal powders always the most cost-effective option?
A: No, REP powders can be more expensive than some other methods. Consider the application’s requirements and weigh the cost against the benefits of using REP powders.
Q: What are some limitations of the REP process?
A: The REP process can have slower production rates and higher costs compared to high-volume techniques. Additionally, it requires specialized equipment and expertise.
Q: How can I choose the right REP metal powder for my application?
A: Consider factors like the desired material properties, required particle size, flowability needs, oxygen content limitations, and overall cost. Consulting with a reputable REP metal powder supplier is recommended.
Share On
MET3DP Technology Co., LTD is a leading provider of additive manufacturing solutions headquartered in Qingdao, China. Our company specializes in 3D printing equipment and high-performance metal powders for industrial applications.
Inquiry to get best price and customized Solution for your business!
Related Articles
About Met3DP
Recent Update
Our Product
CONTACT US
Any questions? Send us message now! We’ll serve your request with a whole team after receiving your message.
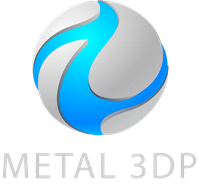
Metal Powders for 3D Printing and Additive Manufacturing
COMPANY
PRODUCT
cONTACT INFO
- Qingdao City, Shandong, China
- [email protected]
- [email protected]
- +86 19116340731