S136 steel powder
Table of Contents
Powder metallurgy (PM) is a manufacturing technique that utilizes metal powders to create complex and near-net-shape components. It offers several advantages over traditional casting and machining, including design flexibility, material efficiency, and the ability to produce parts with unique properties. But the magic of PM lies in the metal powders themselves, and S136 steel powder stands out as a champion in this realm.
Unveiling the Power of S136
S136 is a martensitic stainless steel specifically designed for powder metallurgy applications. It boasts a unique chemical composition that grants it a winning combination of strength, corrosion resistance, and excellent formability – all crucial attributes for high-performance PM parts.
Here’s a breakdown of S136’s key characteristics:
Property | Description |
---|---|
Chemical Composition (wt%) | C: 0.40%, Si: 1.00%, Mn: 1.00%, Cr: 12.00%, Mo: 0.30%, Ni: 0.50% |
Hardness | Up to 58 HRC (Rockwell Hardness) |
Corrosion Resistance | Excellent resistance to wear, abrasion, and mild corrosion |
Formability | Good formability for complex shapes |
Sinterability | Achieves high density during sintering process |
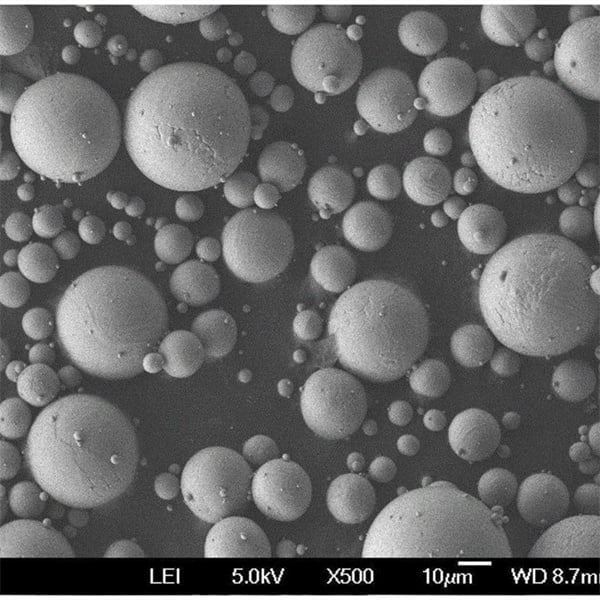
Exploring S136 steel powder for PM
S136 isn’t the only player in the PM powder game. Here’s a glimpse into some other widely used metal powders and their strengths:
- 316L Stainless Steel Powder: The king of corrosion resistance, 316L powder excels in applications demanding resistance to harsh chemicals and environments.
- 17-4 PH Stainless Steel Powder: High strength and good toughness make 17-4 PH a preferred choice for aerospace and medical components.
- Nickel Alloy Powders (IN625, Inconel 625): Offering exceptional high-temperature strength and oxidation resistance, nickel alloy powders find use in jet engine components and heat exchangers.
- Tool Steel Powders (H13, AISI H13): Known for their exceptional wear resistance and hot work capabilities, tool steel powders are ideal for molds and dies.
- Copper Powders: Offering high thermal and electrical conductivity, copper powders are utilized in heat sinks, electrical connectors, and electromagnetic components.
- Titanium Powders: Lightweight and boasting excellent strength-to-weight ratio, titanium powders are employed in aerospace and biomedical applications.
- Aluminum Powders: Highly cost-effective and lightweight, aluminum powders find use in heat sinks, electronic housings, and automotive components.
- MIM (Metal Injection Molding) Powders: These pre-alloyed powders combine metal powder with a binder for intricate and near-net-shape parts.
Applications of S136 steel powder
S136’s unique blend of properties unlocks its potential in a variety of applications. Let’s delve into some key areas where S136 shines:
Application | Advantages |
---|---|
Gears and Sprockets | High strength and wear resistance make S136 ideal for gears and sprockets found in power transmission systems. |
Cutting and Shearing Tools | S136’s excellent wear resistance translates to sharp and durable cutting and shearing tools. |
Bearings and Bushings | S136 offers a winning combination of strength, wear resistance, and corrosion resistance for bearings and bushings. |
Molding and Forming Tools | S136’s good formability allows for complex tool shapes while maintaining high strength and wear resistance. |
Aerospace and Defense Components | S136’s strength-to-weight ratio and corrosion resistance make it suitable for certain aerospace and defense applications. |
Specifications of S136 steel powder
When selecting S136 powder for your PM project, understanding its specifications is crucial. Here’s a breakdown of key parameters:
Parameter | Description |
---|---|
Particle Size | Typically ranges from 10 to 50 microns (μm). |
Apparent Density | Around 4.5 g/cm³ (grams per cubic centimeter). |
Flowability | Good flowability for efficient powder handling and compaction. |
Sintering Temperature | Typically ranges from 1120°C to 1150°C (Celsius). |
Sourcing S136: A Guide for Your PM Journey
Finding reliable suppliers for your S136 powder needs is vital for a successful PM project. Here are some key considerations:
- Reputation and Experience: Look for established suppliers with a proven track record in supplying high-quality S136 powder for PM applications.
- Powder Quality and Certification: Ensure the supplier provides S136 powder that meets industry standards and adheres to relevant certifications like ASTM International (ASTM) or European Committee for Standardization (CEN).
- Technical Support: Choose a supplier that offers technical support to assist you with selecting the right S136 powder grade and particle size for your specific application.
- Pricing and Availability: Compare pricing from different suppliers while considering factors like order quantity, delivery lead times, and any minimum order requirements.
Pros and Cons of S136 steel powder
Every material has its own strengths and weaknesses. Let’s weigh the pros and cons of S136 for PM applications:
Pros
- Excellent Strength and Wear Resistance: S136 excels in applications requiring high strength and resistance to wear and tear.
- Good Corrosion Resistance: S136 offers good resistance to mild corrosion, making it suitable for various environments.
- Formability: Compared to some other high-strength PM steels, S136 exhibits good formability, allowing for more intricate shapes.
- Sinterability: S136 readily achieves high density during the sintering process, leading to strong and reliable PM parts.
Cons
- Cost: Compared to some more common PM steels, S136 can be slightly more expensive due to its specific alloying elements.
- Machinability: S136 can be somewhat challenging to machine due to its high hardness. Post-processing techniques like grinding or polishing may be necessary.
- Limited High-Temperature Performance: While offering good overall properties, S136 might not be the best choice for applications requiring extreme high-temperature performance.
Making the Choice: When to Consider S136
S136 is an excellent choice for PM applications where the following factors are crucial:
- High Strength and Wear Resistance: If your application demands components that can withstand significant wear and tear, S136 is a strong contender.
- Moderate Corrosion Resistance: For environments with mild corrosive elements, S136 provides adequate protection.
- Formability: If your PM parts require complex shapes, S136’s good formability offers design flexibility.
- Sinterability: When achieving high density in the final PM part is a priority, S136’s sinterability is a significant advantage.
Remember, the ideal PM material selection depends on the specific needs of your project. Consider factors like required mechanical properties, environmental exposure, cost constraints, and desired part complexity before making a decision.
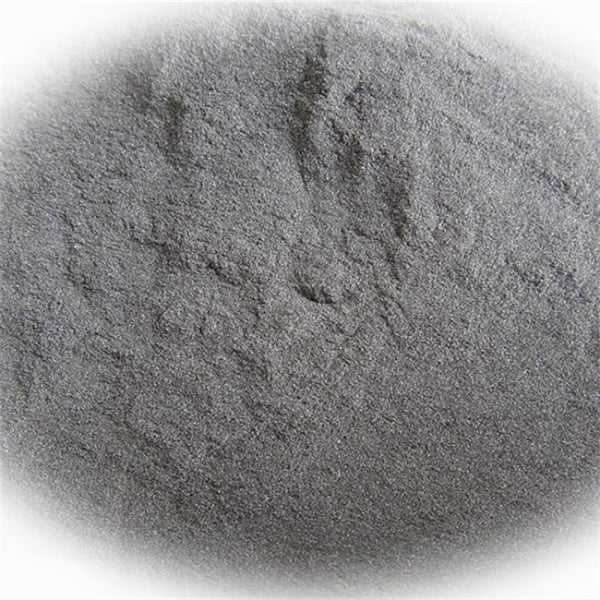
FAQ
Q: How does S136 compare to other stainless steel powders for PM?
A: Compared to standard 300 series stainless steel powders, S136 offers superior strength and wear resistance. However, 316L stainless steel powder boasts better overall corrosion resistance. When both strength and corrosion resistance are crucial, some manufacturers offer high-nitrogen versions of 316L that offer a balance of these properties.
Q: Can S136 be heat treated for further improvement in properties?
A: Yes, S136 can be heat treated to achieve even higher hardness and wear resistance. However, this can come at the expense of some ductility and toughness.
Q: Are there any safety considerations when handling S136 powder?
A: S136 powder, like most metal powders, can be a respiratory irritant. Proper personal protective equipment (PPE) like dust masks and gloves are recommended when handling S136 powder. Additionally, proper ventilation and housekeeping practices are essential to minimize dust exposure.
Conclusion
S136 steel powder stands as a valuable asset within the PM toolbox. Its combination of strength, wear resistance, formability, and good corrosion resistance makes it suitable for a wide range of applications. By understanding its properties, limitations, and comparing it to other PM materials, you can make an informed decision on whether S136 is the right choice for your next PM project.
Share On
MET3DP Technology Co., LTD is a leading provider of additive manufacturing solutions headquartered in Qingdao, China. Our company specializes in 3D printing equipment and high-performance metal powders for industrial applications.
Inquiry to get best price and customized Solution for your business!
Related Articles
About Met3DP
Recent Update
Our Product
CONTACT US
Any questions? Send us message now! We’ll serve your request with a whole team after receiving your message.
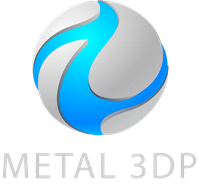
Metal Powders for 3D Printing and Additive Manufacturing