Selective Laser Melting Materials: Unlocking the Potential of 3D Printing Metals
Table of Contents
Imagine building complex, high-performance metal parts layer by layer with a laser beam. This isn’t science fiction; it’s the reality of Selective Laser Melting (SLM), an additive manufacturing (AM) technology revolutionizing the way we create metal components. But just like an artist needs the right paint, SLM thrives on the specific properties of its “paint”: metal powders.
This guide delves into the fascinating world of SLM materials, exploring various powders, their properties, applications, and everything in between. So, grab your metaphorical magnifying glass, and let’s dive in!
Understanding Selective Laser Melting (SLM)
Before we explore the diverse world of SLM materials, let’s revisit the technology itself. SLM uses a high-powered laser beam to selectively melt and fuse metallic powder particles layer by layer, building a 3D object based on a digital design. This process allows for the creation of intricate geometries, lightweight structures, and even components with internal features, all impossible with traditional manufacturing methods.
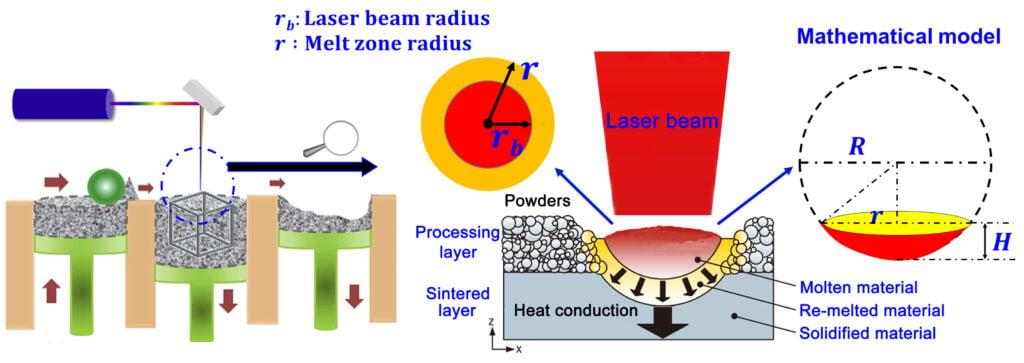
Unveiling the Spectrum of SLM Materials: A Powder Paradise
The success of an SLM project hinges on the carefully chosen metal powder used. Different powders possess unique properties, making them suitable for specific applications. Here are some of the most common and exciting SLM materials:
Metal Powder | Composition | Properties | Applications |
---|---|---|---|
Stainless Steel 316L | Fe (Iron), Cr (Chromium), Ni (Nickel), Mo (Molybdenum) | Excellent corrosion resistance, biocompatible, high strength | Aerospace components, biomedical implants, medical devices |
Titanium Ti6Al4V | Ti (Titanium), Al (Aluminum), V (Vanadium) | High strength-to-weight ratio, good biocompatibility, excellent corrosion resistance | Aerospace components, biomedical implants, sporting goods |
Inconel 625 | Ni (Nickel), Cr (Chromium), Mo (Molybdenum), Fe (Iron) | Exceptional high-temperature resistance, good corrosion resistance, high strength | Gas turbine components, heat exchangers, chemical processing equipment |
Aluminum AlSi10Mg | Al (Aluminum), Si (Silicon), Mg (Magnesium) | High strength-to-weight ratio, good weldability, excellent corrosion resistance | Automotive components, aerospace parts, heat sinks |
Tool Steel H13 | Fe (Iron), Cr (Chromium), Mo (Molybdenum), V (Vanadium) | High wear resistance, good dimensional stability, high strength | Molds, dies, cutting tools |
Copper Cu | Cu (Copper) | High thermal and electrical conductivity, good machinability | Heat exchangers, electrical components, thermal management systems |
Nickel 718 | Ni (Nickel), Cr (Chromium), Fe (Iron), Mo (Molybdenum), Nb (Niobium) | Excellent high-temperature strength, good corrosion resistance | Aerospace components, gas turbine parts, nuclear reactor components |
Cobalt-Chrome CoCrMo | Co (Cobalt), Cr (Chromium), Mo (Molybdenum) | High wear resistance, biocompatible, good corrosion resistance | Biomedical implants, dental prosthetics, wear components |
Tungsten W | W (Tungsten) | Very high melting point, high density, excellent wear resistance | Electrodes, heat shields, armor components |
Maraging Steel 1.2363 | Fe (Iron), Ni (Nickel), Mo (Molybdenum), Ti (Titanium), Al (Aluminum) | Very high strength, good toughness, good corrosion resistance | Aerospace components, weapon systems, high-performance tools |
These are just a few examples, and the list of SLM materials is constantly expanding as research and development efforts continue. Additionally, some manufacturers offer proprietary powder blends with specific properties tailored to individual needs.
Choosing the Right Material for Your SLM Project: A Matchmaker’s Guide
Selecting the optimal SLM material requires careful consideration of several factors:
- Application: The intended use of the final part plays a crucial role. For instance, aerospace components demand high strength-to-weight ratios and excellent corrosion resistance, while biomedical implants require biocompatibility and good wear resistance.
- Properties: Each material boasts a unique set of properties like strength, corrosion resistance, thermal conductivity, and weight. Matching these properties to the application’s demands is essential.
- Processability: Not all powders are created equal. Some powders flow better, leading to smoother layer formation in the SLM process. Conversely, certain powders might be more prone to cracking or warping during printing.
- Cost: Different materials come with varying price tags. Consider the cost of the powder itself, as well as any potential additional processing costs associated with specific materials.
**Remember, choosing the right material is a nuanced process often involving consultations with experienced SLM material suppliers.
Unveiling the Nuances of SLM Materials: A Deeper Dive
While the previous section provided a snapshot of popular SLM materials, let’s delve deeper into some specific aspects to gain a more comprehensive understanding:
1. Grain Size and its Impact:
The size and distribution of individual particles within the powder, known as grain size, significantly influence the final properties of the SLM-printed part. Smaller grain sizes generally lead to:
- Improved mechanical properties: Smaller grains create a more refined microstructure, enhancing the part’s strength, ductility, and fatigue resistance. This is particularly crucial for components experiencing significant stress in operation.
- Enhanced surface finish: Finer grain size translates to smoother surfaces on the printed part, reducing the need for extensive post-processing steps like polishing.
However, finer powders can also pose challenges:
- Increased flowability issues: As particles become smaller, they tend to exhibit poorer flowability, potentially hindering the smooth layering process in SLM. This can lead to printing defects and inconsistencies.
- Higher cost: Producing and handling finer powders can be more expensive compared to their coarser counterparts.
2. The Power of Preheating:
Preheating the powder bed before and during the SLM process offers several benefits:
- Improved laser absorption: Preheating elevates the temperature of the powder bed, allowing the laser beam to be absorbed more efficiently. This translates to better melting and fusion of the powder particles, leading to a denser and stronger final part.
- Reduced residual stress: Preheating helps to mitigate the development of residual stresses within the printed part. These stresses can arise due to the rapid heating and cooling cycles inherent in the SLM process, potentially leading to cracking or warping.
However, preheating also comes with considerations:
- Increased energy consumption: Preheating requires additional energy input, contributing to higher overall operating costs.
- Material compatibility: Not all materials respond favorably to preheating. Certain materials might experience undesirable reactions or property changes at elevated temperatures.
3. The Allure of Alloys:
While pure metals offer specific advantages, the realm of SLM extends to alloys – combinations of two or more elements. Alloys often exhibit superior properties compared to their individual components, making them highly sought-after for diverse applications. For example, the addition of chromium to iron significantly enhances the corrosion resistance of stainless steel, making it ideal for medical implants.
Here are some key considerations when working with SLM alloys:
- Compatibility: Ensuring compatibility between different elements within the alloy is crucial to avoid undesirable reactions during the SLM process.
- Homogeneity: Maintaining homogeneity, or uniform distribution of elements throughout the alloy, is essential for consistent material properties in the final part.
4. The Future of SLM Materials:
The future of SLM materials is brimming with exciting possibilities. Researchers are actively exploring:
- Development of novel alloys: Pushing the boundaries of material science by creating new alloys with tailored properties specifically optimized for SLM.
- Nanoparticle-based powders: Utilizing nanoparticles, particles with dimensions in the nanometer range, to create powders with unique properties, potentially leading to lighter and stronger components.
- Multi-material printing: Combining different materials within a single print to create parts with graded properties or even integrated functionalities, opening doors to revolutionary applications.
Unveiling the Practicalities: Cost, Suppliers, and Specifications
Now that we’ve explored the technical aspects, let’s address some practical considerations:
1. Selective Laser Melting Materials Price Range:
The cost of SLM materials varies significantly depending on several factors:
- Material type: Certain materials, like precious metals or rare earth elements, naturally carry a higher price tag compared to common metals like steel.
- Powder characteristics: Finer powders, with their improved properties, often come at a premium cost compared to coarser ones.
- Supplier and market demand: Different suppliers might offer varying prices for the same material, and market fluctuations can also impact overall cost.
It’s important to consult with potential suppliers and obtain quotes based on your specific material needs and project requirements.
Frequently Asked Questions (FAQ) about Selective Laser Melting Materials
Here are some of the most commonly asked questions regarding Selective Laser Melting (SLM) materials:
Q: What are the advantages of using SLM materials?
A: SLM materials offer several advantages over traditional manufacturing methods, including:
- Design freedom: SLM enables the creation of complex geometries and internal features impossible with conventional techniques.
- Lightweighting: SLM allows for the creation of parts with high strength-to-weight ratios, making them ideal for applications demanding weight optimization, like aerospace and automotive components.
- Mass customization: SLM facilitates the production of customized parts in small batches, catering to niche applications or personalized products.
- Reduced waste: Compared to subtractive manufacturing methods that generate significant material waste, SLM utilizes a near-net-shape approach, minimizing material waste.
Q: What are the limitations of using SLM materials?
A: While offering exciting possibilities, SLM also has limitations to consider:
- Cost: The technology and materials can be expensive compared to traditional methods, limiting its widespread adoption for certain applications.
- Surface finish: SLM-printed parts might require post-processing steps to achieve desired surface finishes.
- Limited material selection: While the range of materials available for SLM is expanding, it’s still not as extensive as those readily available for conventional manufacturing.
Q: How do I choose the right SLM material for my project?
A: Selecting the optimal SLM material requires careful consideration of several factors:
- Application: The intended use of the final part plays a crucial role. Match the material properties to the application’s specific demands.
- Properties: Consider essential properties like strength, corrosion resistance, thermal conductivity, and weight, ensuring they align with your project’s requirements.
- Processability: Choose a material that flows well and exhibits good printability to ensure smooth layer formation during the SLM process.
- Cost: Evaluate the cost of the material itself, along with any potential additional processing costs associated with specific materials.
It’s recommended to consult with experienced SLM professionals or material suppliers to receive personalized guidance based on your specific project needs.
Q: Where can I find more information about SLM materials?
A: Several resources offer valuable information about SLM materials:
- AM Material Guide: https://www.amug.com/
- Metal Additive Manufacturing Magazine: https://www.metal-am.com/
- EOS GmbH: https://www.eos.info/ (SLM machine manufacturer with material information)
- LPW Technology: https://www.carpenteradditive.com/news-events/lpw-launches-new-product-line-powderflow (SLM material supplier)
These resources provide in-depth information, case studies, and industry insights, further enriching your understanding of SLM materials.
By understanding the diverse world of SLM materials, their properties, applications, and limitations, you can make informed decisions for your next SLM project, unlocking the full potential of this transformative technology.
Share On
MET3DP Technology Co., LTD is a leading provider of additive manufacturing solutions headquartered in Qingdao, China. Our company specializes in 3D printing equipment and high-performance metal powders for industrial applications.
Inquiry to get best price and customized Solution for your business!
Related Articles
About Met3DP
Recent Update
Our Product
CONTACT US
Any questions? Send us message now! We’ll serve your request with a whole team after receiving your message.
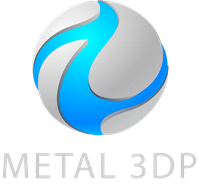
Metal Powders for 3D Printing and Additive Manufacturing