What Precision Parts Can SLM Produce with Metal Powder?
Table of Contents
Imagine crafting intricate, high-performance parts with the precision of a jeweler, but using the strength and versatility of metal. That’s the magic of Selective Laser Melting (SLM), an additive manufacturing technology that transforms metal powder into complex, functional components. But what exactly can SLM create? Let’s delve into the fascinating world of SLM-produced precision parts, exploring the specific metal powders used and the vast applications they unlock.
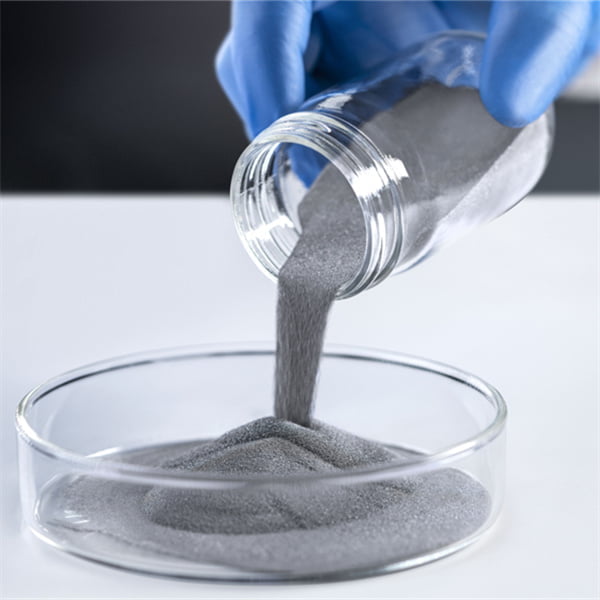
Metal Powders: The Building Blocks of SLM Precision
SLM works by meticulously fusing layers of metal powder using a high-powered laser beam. The choice of metal powder significantly impacts the final part’s properties and performance. Here are ten commonly used metal powders in SLM, each offering unique advantages:
Common Metal Powders for SLM
Metal Powder | Description | Properties | Applications |
---|---|---|---|
316L Stainless Steel | The most widely used SLM powder, offering excellent corrosion resistance, high strength, and biocompatibility. | Versatile, durable, and well-suited for medical implants, aerospace components, and food processing equipment. | |
Titanium-6Al-4V (Ti-6Al-4V) | A workhorse in the aerospace industry, boasting high strength-to-weight ratio, excellent biocompatibility, and good corrosion resistance. | Lightweight, strong, and biocompatible, making it ideal for aerospace parts, medical implants, and prosthetics. | |
Aluminum-Si10Mg (AlSi10Mg) | A popular choice for lightweight components due to its low density and good castability. | Lightweight, good castability, and cost-effective, making it suitable for automotive parts, consumer electronics, and prototyping. | |
Inconel 625 (IN625) | A high-performance nickel-chromium alloy known for its exceptional resistance to high temperatures, corrosion, and oxidation. | High-temperature resistance, corrosion and oxidation resistance, making it ideal for jet engine components, chemical processing equipment, and power generation applications. | |
CoCrMo (Cobalt-Chromium-Molybdenum) | A biocompatible alloy favored for its wear resistance and resistance to body fluids. | Biocompatible, wear-resistant, and corrosion-resistant, making it perfect for medical implants, joint replacements, and dental prosthetics. | |
Stainless Steel 17-4 PH (17-4 PH) | A precipitation-hardening stainless steel with high strength and good corrosion resistance. | High strength, good corrosion resistance, and excellent fatigue strength, making it suitable for aerospace components, automotive parts, and demanding engineering applications. | |
Copper (Cu) | Offers excellent thermal and electrical conductivity, making it valuable for heat exchangers and electrical components. | High thermal and electrical conductivity, but susceptible to oxidation, limiting its applications. | |
Tool Steel (H13) | A high-alloy steel known for its excellent wear resistance and hot work tool properties. | High wear resistance, hot work tool properties, and good dimensional stability, ideal for molds, dies, and cutting tools. | |
Inconel 718 (IN718) | A high-strength nickel-chromium alloy offering superior mechanical properties at elevated temperatures. | High strength, excellent creep resistance, and good oxidation resistance, making it ideal for aerospace components, gas turbine parts, and demanding engineering applications. | |
Titanium Grade 2 (CP Ti) | Commercially pure titanium, offering good ductility, formability, and biocompatibility. | Ductile, formable, and biocompatible, making it suitable for medical implants, chemical processing equipment, and sporting goods. |
Applications of SLM Precision Parts
The ability to create complex geometries with high accuracy and near-net shapes makes SLM a game-changer across various industries:
Fields of Application for SLM Precision Parts
Field | Examples | Benefits |
---|---|---|
Aerospace | Turbine blades, rocket engine components, lightweight airframe structures | Lightweight, high strength-to-weight ratio, and design freedom for complex geometries. |
Medical | Implants, prosthetics, dental crowns and bridges | Biocompatible materials, customized designs for individual patients, and improved functionality. |
Automotive | Engine components, lightweight structural parts, prototypes for rapid development | Lightweighting, design freedom for performance optimization, and faster time-to-market. |
Consumer Electronics | Housings, heat sinks, complex internal components | Lightweight, intricate designs for improved functionality and aesthetics, and freedom for miniaturization. |
Energy | Heat exchangers, turbine blades, components for nuclear reactors | High-performance materials for demanding environments, design freedom for optimized efficiency, and potential for weight reduction. |
The Main Advantages of SLM
SLM offers several compelling advantages over traditional manufacturing methods like machining, casting, and forging:
- Design Freedom: Unlike subtractive methods that remove material from a solid block, SLM builds parts layer-by-layer, enabling the creation of intricate geometries with internal channels, lattice structures, and other complex features impossible with traditional techniques. This opens doors for designing lightweight yet strong components and optimizing parts for specific functions.
- Customization: SLM excels at producing unique and customized parts. Each component is built directly from a digital 3D model, allowing for easy customization and personalization, making it ideal for applications like medical implants, prosthetics, and personalized consumer goods.
- Lightweighting: The ability to create complex internal structures and hollow features allows for significant weight reduction, a critical factor in industries like aerospace and automotive, where every gram saved translates to improved fuel efficiency and performance.
- Reduced Waste: Compared to traditional methods that generate significant material waste, SLM utilizes nearly all the metal powder used in the printing process. This minimizes waste and contributes to a more sustainable manufacturing approach.
- Rapid Prototyping: SLM enables rapid prototyping, allowing designers and engineers to quickly iterate on designs and create functional prototypes for testing and validation. This significantly reduces development times and costs compared to traditional prototyping methods.
- Near-Net Shapes: SLM produces parts with minimal material excess, reducing the need for extensive post-processing steps like machining or finishing. This translates to faster production times and lower overall costs.
Limitations and Considerations
While SLM offers immense potential, it’s crucial to acknowledge its limitations and considerations:
- Cost: Currently, SLM machines and metal powders are relatively expensive, making this technology less suitable for mass production compared to traditional methods. However, as the technology matures and production volumes increase, costs are expected to decrease.
- Surface Finish: SLM parts may require additional post-processing steps to achieve specific surface finishes, which can add to the overall production cost and time.
- Material Availability: While the range of available metal powders for SLM is expanding, the selection is still limited compared to traditional manufacturing materials.
- Process Complexity: Operating and maintaining SLM machines requires expertise in handling metal powders, laser technology, and process parameters, which can be a learning curve for manufacturers accustomed to traditional methods.
Choosing the Right Tool: Comparing SLM to Other Methods
Selecting the most suitable manufacturing method depends on various factors, including part complexity, desired properties, production volume, and budget. Here’s a simplified comparison of SLM with other common techniques:
Comparison of SLM with Other Manufacturing Methods
Feature | SLM | Machining | Casting | Forging |
---|---|---|---|---|
Complexity | High | Moderate | Low | Moderate |
Material Options | Limited | Wide | Wide | Limited |
Strength-to-Weight Ratio | High | Moderate | Varies | High |
Customization | High | Low | Low | Low |
Production Volume | Low-Medium | High | High | Medium |
Cost per Part | High | Low-Medium | Medium | Low |
The Future of SLM: A World of Possibilities
The future of SLM is brimming with exciting possibilities. As research and development continue, we can expect:
- Advancements in material science: New metal powders with enhanced properties, including improved strength, ductility, and high-temperature performance, are under development, expanding the applications of SLM.
- Increased affordability: As the technology matures and production volumes rise, the cost of SLM machines and metal powders is expected to decrease, making it more accessible to a wider range of manufacturers.
- Integration with other technologies: Combining SLM with other additive manufacturing techniques, like 3D printing with multiple materials, opens doors for creating even more complex and functional parts.
- Sustainable manufacturing: SLM’s ability to minimize waste and utilize recycled metal powders positions it as a more sustainable manufacturing option compared to traditional methods.
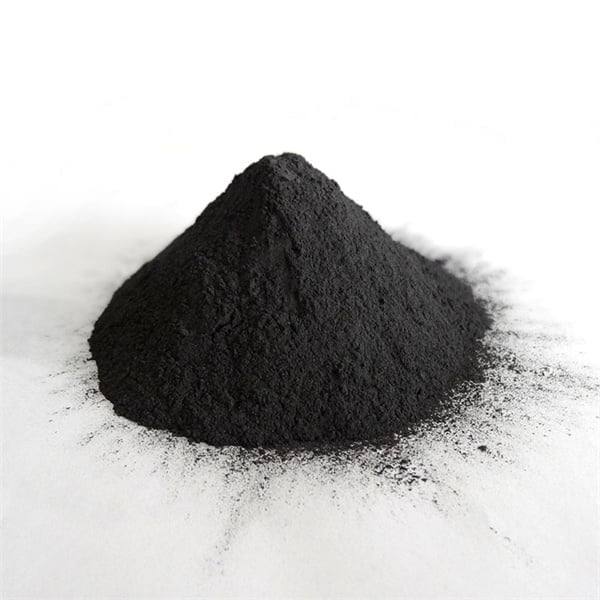
FAQs
Q: What are the size limitations of SLM parts?
A: The size of SLM parts is limited by the build volume of the specific machine. Typically, build volumes range from a few centimeters to several meters, depending on the machine’s size and capabilities.
Q: Can I use SLM to print parts in color?
A: While current SLM technology primarily focuses on single-material printing, research is ongoing in multi-material SLM, which could enable printing parts with different colors or properties within the same build.
Q: What are the environmental benefits of using SLM?
A: Compared to traditional manufacturing methods that generate significant material waste and require extensive machining processes, SLM offers several environmental advantages:
- Reduced waste: SLM utilizes nearly all the metal powder in the printing process, minimizing waste compared to subtractive techniques like machining.
- Energy efficiency: SLM requires less energy consumption compared to traditional methods like casting and forging, which often involve high-temperature processes.
- Recycled materials: SLM is compatible with recycled metal powders, further reducing its environmental footprint and contributing to a more sustainable manufacturing approach.
Q: What are some of the safety considerations when working with SLM?
A: As with any industrial process, working with SLM requires adhering to safety protocols. Here are some key considerations:
- Laser safety: The high-powered lasers used in SLM can pose a risk to eyesight. Proper personal protective equipment (PPE) like laser safety glasses must be worn while operating the machine.
- Metal powder handling: Metal powders can be flammable and pose inhalation risks. Proper ventilation and dust collection systems are crucial to ensure a safe working environment.
- Fire safety: Implementing proper fire safety protocols is essential due to the potential flammability of metal powders and the high temperatures involved in the SLM process.
Q: How does the cost of SLM compare to other manufacturing methods?
A: Currently, SLM is considered a relatively expensive manufacturing method compared to traditional techniques like machining and casting. This is primarily due to the high cost of SLM machines and metal powders. However, as the technology matures and production volumes increase, the cost of SLM is expected to decrease, making it more accessible to a wider range of manufacturers. Additionally, the potential benefits of SLM, such as design freedom, reduced waste, and faster lead times, can contribute to overall cost savings in specific applications.
Share On
MET3DP Technology Co., LTD is a leading provider of additive manufacturing solutions headquartered in Qingdao, China. Our company specializes in 3D printing equipment and high-performance metal powders for industrial applications.
Inquiry to get best price and customized Solution for your business!
Related Articles
About Met3DP
Recent Update
Our Product
CONTACT US
Any questions? Send us message now! We’ll serve your request with a whole team after receiving your message.
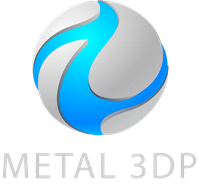
Metal Powders for 3D Printing and Additive Manufacturing
COMPANY
PRODUCT
cONTACT INFO
- Qingdao City, Shandong, China
- [email protected]
- [email protected]
- +86 19116340731