SLM Additive Manufacturing
Table of Contents
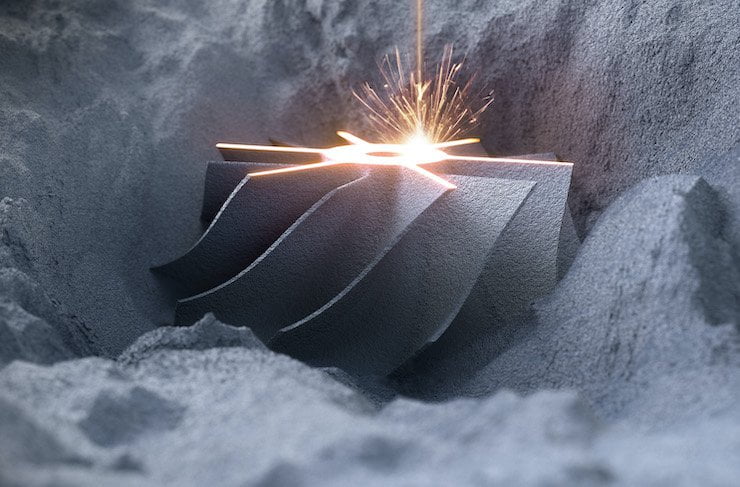
Additive manufacturing, also known as 3D printing, is a transformative way to make parts and products. One of the most widely used additive manufacturing techniques is selective laser melting (SLM). SLM is a powder bed fusion method that uses a high-powered laser to selectively fuse material powder together to build up parts layer-by-layer.
SLM enables complex geometries with intricate internal features to be created directly from 3D CAD data. It also minimizes material waste and offers design flexibility not possible with traditional manufacturing. However, SLM requires specialized equipment, optimized processing parameters, and an understanding of material characteristics.
This comprehensive guide covers everything you need to know about selective laser melting additive manufacturing. It explains the technology, typical materials used, applications, advantages vs limitations, specifications, suppliers, costs, comparisons to other 3D printing methods, and more. Read on to become an SLM expert!
How SLM 3D Printing Works
SLM uses a focused laser beam to melt and fuse metallic powder together. Parts are built up additively layer-by-layer based on slicing 3D CAD model data. Here are the key aspects of the SLM process:
SLM Additive Manufacturing Process Overview
Process Step | Description |
---|---|
3D Model Preparation | The CAD model is converted into thin 2D slices used to direct the laser melting pathway. Support structures may be added for overhangs. |
Powder Spreading | A recoating mechanism spreads a layer of metallic powder evenly across the build platform. |
Laser Melting | A focused high-powered laser selectively melts powder based on each 2D slice, fusing particles together to form a solid. |
Lower Building Platform | After one layer is complete, the build platform lowers, and new powder is spread on top. |
Repeat Steps | The powder spreading, laser melting, and lowering steps repeat until the part is complete. |
Post Processing | The part is cut away from excess powder, then may require supports removal, cleaning, heat treatments, surface finishing, inspection, etc. |
The layered approach allows for the creation of complex, organic shapes with intricate internal cavities and tunnels that could not be made by traditional methods like casting or machining from solid blocks.
SLM is also referred to by similar names including selective laser sintering (SLS), direct metal laser sintering (DMLS), and powder bed fusion (PBF). The core aspects of these powder-based processes are essentially identical with small equipment differences.
SLM Materials
A wide range of metals, alloys, and ceramics can be processed with SLM additive manufacturing technology. The most frequently used include stainless steels, cobalt chrome, titanium, aluminum, and nickel-based superalloys. Material options continue expanding as the technology develops.
Common SLM Materials and Uses
Material | Applications |
---|---|
Stainless Steel (316L, 17-4PH) | Low-cost prototypes, functional metal parts like valves, pumps housings |
Titanium Alloys (Ti-6Al-4V) | Aerospace components, medical implants, automotive parts |
Cobalt Chrome (CoCr) | Dental crowns & bridges, orthopedic knee/hip implants |
Aluminum Alloys (AlSi10Mg) | Lightweight drones, aerospace brackets, automotive prototypes |
Inconel (IN625, IN718) | Turbocharger wheels, combustion chambers, aerospace engines |
Tool Steels (H13, Maraging Steel) | Injection molds, forming dies, tooling fixtures |
The most popular option is 316L stainless steel powder due to its strength, corrosion resistance, high quality finishes, and lower cost compared to exotic alloys.
Materials for SLM go through strict quality control with spherical powder particles sized 15-100 microns in diameter on average. Finer powders improve resolution while coarser ones build faster but with lower accuracy.
SLM Applications
SLM is valued for prototypes, custom tooling, and low-volume production of complex, high-performance metal components with enhanced mechanical properties. Here are some of the leading applications across major industries:
SLM Additive Manufacturing Application Areas
Industry | Common SLM Applications |
---|---|
Aerospace | Turbine blades, fuel injectors, heat exchangers, structural brackets, satellite antennae |
Medical | Personalized implants (hip, knee etc), surgical instruments, orthodontic equipment |
Automotive | Performance car prototypes, customized brackets, lightweight suspension arms |
Industrial | Conformal cooling molds & dies, jigs, fixtures for assembly & inspection |
Oil & Gas | Custom valves, pumps, seals, drill equipment for high pressure needs |
Defense | Drones, small arms customization, vehicular & body armor components |
The ability to consolidate assemblies into single parts, customize designs rapidly, cut lead times from months to days compared to traditional manufacturing methods underpins the growing use of SLM for production applications in these industries.
SLM Printer Manufacturers
Many companies manufacture SLM equipment also referred to as 3D printers. The main players in industrial-grade professional metal 3D printers include:
Leading SLM Machine Providers
Company | Details |
---|---|
EOS | Founded SLM technology, wide material options like EOS Titanium Ti64, extensive aerospace use |
3D Systems | Broad product line from desktop to industrial printers |
GE Additive | Leading US provider, binder jet and laser powder bed options |
Renishaw | High precision optics for micro applications, extensive material testing |
SLM Solutions | Reliable workhorse machines with automated powder handling |
Trumpf | Robust German engineering heritage combined with lasers |
Velo3D | Novel support-free approach enables new geometries |
While initial equipment costs for an industrial SLM machine run from $150,000 to over $1 million, selecting the right system for available space, materials needs, accuracy requirements, and budget considerations is key. Leading manufacturers offer different builds sizes, multi-laser configurations for speed, specialized parameters for quality and repeatability with different alloys, levels of software automation features, and more.
SLM Material Properties
Parts printed on SLM machines exhibit unique properties compared to traditional casting and machining methods due to the layered manufacturing and rapid solidification.
Mechanical Properties Comparison – SLM vs Traditional Manufacturing
Property | SLM Additive Mfg | Traditional Mfg |
---|---|---|
Density | Nearly 100% dense | 99% from cast/wrought |
Surface Finish | Layer lines visible, Ra 6-14 μm | Smoother surface finish |
Tensile Strength | Typically 10-20% higher | Lower strength |
Elongation at Break | Decreased by 5-15% | Higher elongation |
Hardness | Improved up to 2X for some alloys | Lower hardness |
The high cooling rates from the SLM process, exceeding 106 °C/s, create finer microstructures with metastable phases. This accounts for maximum densities from powder consolidation along with excellent mechanical properties like enhanced yield and tensile strength. Elongation is typically lower for SLM parts since high hardness and presence of internal stresses limit ductility.
Proper heat treatments and hot isostatic pressing (HIP) can relieve internal stresses and further optimize physical properties while improving consistency. Overall SLM can achieve over 99.5% density to yield functional metal parts essentially identical to traditional manufacturing.
SLM vs Other 3D Printing
Comparison of SLM to Other Additive Manufacturing Methods
SLM | Binder Jetting | FDM | SLA | |
---|---|---|---|---|
Materials | Metals | Metals, sand molds | Plastics | Resins |
Raw Inputs | Powder bed | Powder bed | Filament on reel | Vat of liquid resin |
Process | Laser fuses powder | Binder glues powder | Filament heated and extruded | Laser cures resin layers |
Key Property | High density | Low cost metal molds | Thermoplastics | Smooth surface finish |
Strengths | Complex metal parts | Rapid sand casting cores/molds | Functional prototypes | Smooth surface finish |
Weaknesses | Lower speed | Brittle low density | Weak mechanics | Limited material options |
SLM differentiates from other powder bed fusion methods like electron beam melting (EBM) in terms of its faster scan speeds to create parts with lower residual stresses and higher resolution. SLM produces fully dense functional metal parts while binder jet 3D printing offers speed but with more post-processing requirements. FDM and SLA systems greatly lag SLM & EBM equipment in available materials strength.
SLM Specifications
3D printers utilizing selective laser melting technology are specified by several key parameters that determine materials, precision, and part sizes that can be produced.
Key SLM Machine Specifications
Parameter | Typical Range | Description |
---|---|---|
Laser Power | 200-500W | Higher power improves build speed but reduces fine feature resolution |
Layer Thickness | 20-100 μm | Thinner layers enhance detail but lengthen build times |
Beam Size | 50-80 μm | Focus spot size affects intricacy of details and melt pool control |
Build Volume | 100-500 mm cubes | Maximum part dimensions the system can produce |
Inert Gas | Nitrogen or Argon | Protects against oxidation; argon enables better material properties |
Scanning Speed | Up to 10 m/s | Faster scanning increases part fabrication times |
These core machine parameters plus factors like incorporated heating for preheating powder and controlling cooling rates enable tuning mechanical characteristics. The inert gas chamber environment also prevents oxidation while lasers raster across the metal powder bed thousands of times per part build.
Accuracy and Surface Finish
dimensional accuracy and surface finish for as-printed SLM parts fall into relatively wide specification ranges depending on selected parameters, geometry complexity, post-processing, and operator technique.
SLM Accuracy and Surface Finish
Metric | Range | Description |
---|---|---|
Dimensional Accuracy | ± 0.1-0.3% with ±50 μm typical | Measure of difference between CAD vs built part |
Minimum Wall Thickness | 0.3-0.5 mm | Thinnest features able to be printed |
Surface Roughness (Ra) | 6-14 μm | Higher roughness than machined parts |
Porosity | <1% density | Nearly fully dense parts under optimum parameters |
Residual Stresses | 50-500 MPa | Must be relieved by heat treatment |
Appropriate orientation, support structures, build plate preheating, optimized scan strategies, and post-processing steps like CNC machining and polishing can improve finish. Dimensional accuracy also depends greatly on properly calibrated equipment.
Post-Processing Requirements
After the SLM system completes fabrication of a component, additional post-processing is typically necessary before putting parts in service. Steps may involve:
- Removing parts from the powder cake
- Eliminating support structures
- Stress relieving heat treatments
- Hot isostatic pressing (HIP)
- Surface grinding, sand blasting, bead blasting, polishing
- Non-destructive inspection
Post-processing aims to reduce surface roughness, relieve residual stresses, close any micro-porosity, and improve dimensional precision and aesthetics.
Specific procedures are determined by material type, production intent (prototype vs. functional part), performance requirements, and critical tolerances needed.
Cost Analysis
Determining return on investment for acquiring and operating in-house SLM additive manufacturing capacity depends on many variables.
SLM Cost Considerations
Cost Factor | Description |
---|---|
Machine Equipment | $150k – $1M+ depending on build volume, multi-laser options, additional capabilities like automated powder handling and recovery |
Facility Requirements | Inert gas handling system, venting filters, explosion proof design, temperature/humidity control |
Installation & Training | 2 weeks typical for machine setup, calibration, software instruction |
Labor | Machine operation less intensive than CNC machining but operators still needed; CAM expert recommended |
Materials | $100-500 per kg powder; recyclability varies; optimized parameters per alloy |
Post-Processing | Labor, tooling, outsourced heat treating, surface finishing |
Software | $10k-$25k range for preprocessing, simulation, remote monitoring apps |
R&D Iterations | Testing parameters for new parts using Agile process vital for qualification |
Order Volume | Low/medium batches ideal vs high volume casting/molding |
Weigh total operating costs against value drivers like:
· Design freedom for weight reduction, customization, part consolidation
· Reduced lead time from months to days/hours
· Supply chain simplification with on-demand manufacturing
· Performance enhancements like increased strength and hardness
· Sustainable production with minimal waste vs subtractive methods
· Increased life span of high value parts like aerospace and medical
Quantifying productivity and innovation gains is crucial. With experience, total cost per part produced via SLM can match CNC machining for lower volume production runs.
Industry Standards
As a relatively new technology, efforts are still underway to implement industry wide specifications, codes, and standards across SLM additive manufacturing.
SLM Standardization Landscape
Standards Body | Scope | Specific Standards |
---|---|---|
ASTM F42 | Additive manufacturing processes | Test methods, terminology, process parameters, environments, materials, health and safety |
America Makes | Additive manufacturing standards | Roadmap for AM standards spanning materials, processes, data formats across defense, aviation, space, maritime |
ISO TC 261 | AM standards | 17 published, 46 in development spanning terminology, processes, workflows, QA, environments, safety |
ASME | Conformity assessment | Program for AM part qualification; certifies AM processes for compliance to codes |
Certification to these standards ensures repeatability and reliability when contracting AM parts across the supply chain. Compliance also unlocks broader adoption in regulated sectors like aerospace and medical devices.
Case Studies
Myriad companies leverage SLM’s design freedom and fast lead times for lighter, stronger components across industries from aerospace rockets to Formula 1 cars.
SLM Additive Manufacturing Application Examples
Industry | Company | Part | Benefits |
---|---|---|---|
Aerospace | SpaceX | SuperDraco Engine Chamber | 75% cost reduction, delivered in days vs months |
Aviation | Boeing | 777X Brackets | Consolidated assemblies, 60% lighter weight |
Automotive | Bugatti | Brake Caliper | Reduced mass by 40%, optimized fluid flow |
Medical | Zimmer Biomet | Spinal Implants | Customized shapes fit anatomy, osteoconductive structures to aid bone ingrowth |
These applications showcase SLM parts outperforming traditional manufacturing constraints. As more companies adopt AM technologies, innovation possibilities keep expanding.
SLM Additive Manufacturing – FAQs
Frequently Asked Questions on SLM
Question | Answer |
---|---|
How does SLM printing work? | SLM builds up parts layer by layer from metallic powder using a laser beam to selectively melt and fuse material based on CAD data |
What materials are available? | Most popular are 316L and 17-4 stainless steel, titanium Ti64 alloy, cobalt chrome, aluminum AlSi10Mg, tool steel, nickel superalloys |
What are some key benefits over machining? | Design freedom for lightweight structures, customization, part consolidation; faster lead times; reduced waste; enhanced mechanical properties |
What determines surface finish? | Layer resolution, build parameters, orientation, post-processing steps like bead blasting |
What accuracy can SLM achieve? | ±0.1-0.3% dimensional accuracy is typical for most applications, with minimum wall thicknesses around 0.3-0.5 mm |
Does the SLM process require supports? | Support structures are required for significant overhangs depending on orientations and geometries |
What post processing is required? | Steps may involve supports removal, stress relieving, hot isostatic pressing, surface finishing like grinding or polishing |
What applications is SLM suitable for? | Rapid prototypes, custom tooling like jigs and fixtures, and direct metal end use parts across aerospace, medical, dental, automotive industries |
How does quality compare to traditional manufacturing? | With optimized parameters, >99% dense SLM parts match or exceed mechanical properties and lifespans |
How should design be adapted for SLM? | Conformal channels, lattices, topology optimization are all uniquely suited to AM. Guidelines help adapt parts. |
This FAQ summarizes answers to top questions about selective laser melting additive manufacturing. SLM unlocks new performance benchmarks thanks to total design freedom.
The Future of SLM
SLM adoption continues accelerating as more industries push the boundaries of additive manufacturing. Advances in equipment, software, materials, and quality processes will drive expanded applications.
Expect wider availability of specialized multi-alloy machines and processing parameters from leading printer manufacturers. Hybrid systems incorporating complementary processes like milling, drilling, inspection are also emerging for integrated manufacturing. Automated powder removal and recovery will reduce costs.
Real-time monitoring will enable even tighter process controls and closed-loop quality assurance. Machine learning algorithms can optimize building performance. As standards solidify around best practices, users will also gain more predictability.
Share On
MET3DP Technology Co., LTD is a leading provider of additive manufacturing solutions headquartered in Qingdao, China. Our company specializes in 3D printing equipment and high-performance metal powders for industrial applications.
Inquiry to get best price and customized Solution for your business!
Related Articles
About Met3DP
Recent Update
Our Product
CONTACT US
Any questions? Send us message now! We’ll serve your request with a whole team after receiving your message.
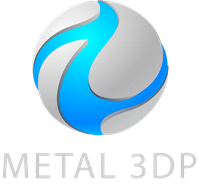
Metal Powders for 3D Printing and Additive Manufacturing