understanding SLM Manufacturing
Table of Contents
slm manufacturing is a powder bed fusion additive manufacturing process used across industries. This guide provides a comprehensive look at SLM – how it works, materials, applications, advantages/disadvantages, system suppliers, and more.
Overview of Selective Laser Melting (SLM)
slm manufacturing is an additive manufacturing process that uses a laser to selectively melt metal powder layer-by-layer to build up fully dense parts. Key attributes:
- Uses 3D CAD data to direct laser melting of powder layers
- Achieves near full density in most alloys (>99%)
- Allows complex geometries not possible with casting/machining
- Common materials include stainless steel, titanium, aluminum, nickel alloys
- Typical layer thickness 20-100 microns
slm manufacturing provides design freedom and mechanical properties approaching traditional manufacturing.
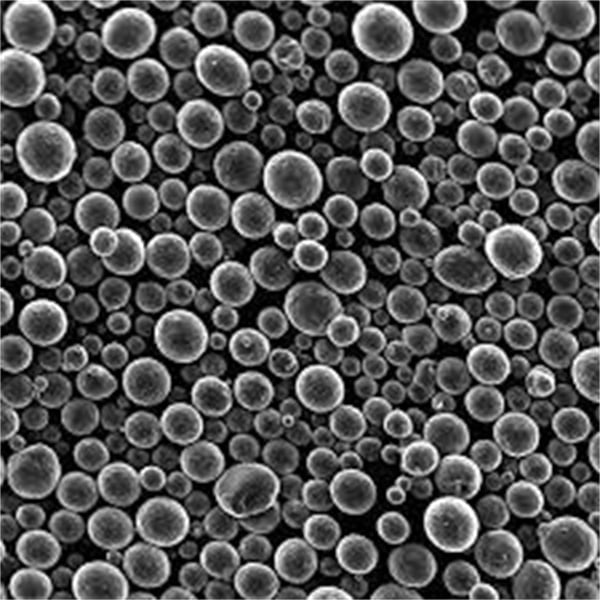
How the slm manufacturing Works
SLM uses a high power laser to melt fine metallic powder in precise patterns:
- CAD model is digitally sliced into thin cross-sectional layers
- Powder layer is spread evenly across the build platform
- Laser melts powder based on each slice, fusing particles together
- Platform lowers, new layer applied, and process repeats
- Fully dense parts are built up additively layer-by-layer
A protective inert gas atmosphere prevents oxidation during builds.
Materials for SLM
Many metal powders can be used for SLM, including:
SLM Metallic Materials
- Stainless steel (316L, 17-4PH, 15-5PH)
- Tool steel (H13, M2)
- Titanium (Ti-6Al-4V)
- Aluminum (AlSi10Mg)
- Cobalt-Chrome (CoCr)
- Nickel alloys (Inconel 625, 718)
- Copper alloys
- Precious metals
Powders range from 15-45 microns typically. Some alloys require specialized parameters to print successfully.
Applications of SLM Parts
slm manufacturing allows consolidating assemblies into one-piece components with no assembly. Common uses include:
SLM Part Applications
- Aerospace – lightweight structures, turbines, brackets
- Medical – implants, prosthetics, surgical instruments
- Automotive – lightweighted components, custom designs
- Tooling – injection molds with conformal cooling
- Energy – complex oil/gas valves, heat exchangers
- Defense – custom drone/robotics parts needing strength
SLM enables optimized designs with reduced weight and lead times versus traditional manufacturing.
Advantages of SLM Additive Manufacturing
Key benefits that make SLM attractive:
- Complex geometries and microstructures possible
- Fully dense and isotropic material properties
- Less waste – only use material required
- Weight reduction by consolidating assemblies
- Fast turnaround for design iterations
- No need for special tooling like cast/forge dies
- Custom alloys and graded materials achievable
slm manufacturing provides nearly unlimited freedom to produce enhanced components otherwise infeasible.
Limitations of slm manufacturing
SLM does have some disadvantages compared to conventional manufacturing:
- Higher part cost for small production volumes
- Limited size based on build chamber dimensions (improving over time)
- Restricted material selection compared to cast or wrought alloys
- Post-processing like surface finishing often required
- Special handling of reactive powders like titanium and aluminum
- Defects possible requiring inspection methods to identify
- anisotropic properties in some materials and builds
Challenges are mitigated through ongoing technology advancements.
SLM System Suppliers
Major SLM equipment manufacturers include:
Notable SLM System Providers
- EOS
- 3D Systems
- GE Additive
- Trumpf
- Renishaw
- DMG Mori
- Sisma
- Mazak
- AMCM
Many provide turnkey systems plus powder handling and post-processing equipment.
Cost Analysis of slm manufacturing Production
Like most AM processes, SLM has high upfront costs but low per-part costs at volume:
- SLM system cost ~$500,000 to $1M+
- Build rate ~5-20 cm3/hour (~10-50g/hour)
- Labor time ~5-10 hrs including post-processing
- Material cost ~$50-200/kg
- Total part cost can be $500 to $5000+
Highest costs are labor, system investment, and materials. Competitive for small/medium volumes.
SLM vs. Metal Casting and Machining
Process | Pros | Cons | Best Applications |
---|---|---|---|
SLM | Design freedom, lightweight, fast turnaround, minimal waste | Limited size, higher cost at low volumes, post-processing | Low and medium volume complex parts |
Metal casting | Near net shape, good for simple to complex parts, lower costs at volume | Extra steps to finish parts, design restrictions, tooling costs | Medium to high production volumes |
CNC machining | Wide material choices, high accuracy, good surface finish | Waste from subtractive process, higher costs at lower quantities, design limitations from tool access | Low to medium volumes where design changes frequently |
Each process has advantages suited to specific applications, production volumes and goals.
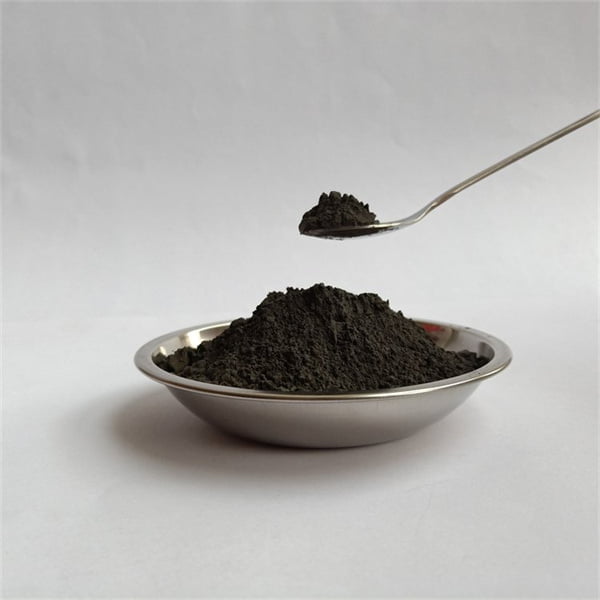
FAQ
What materials can be 3D printed with SLM?
The most common SLM materials are alloys of stainless steel, titanium, aluminum, cobalt-chrome, nickel, copper, and precious metals. Various tool steels and superalloys are also possible.
What is the typical accuracy of SLM parts?
SLM can produce parts with accuracy around +/- 0.005 in/in depending on factors like layer thickness, scan strategy, geometry and post-processing. Critical surfaces may need machining.
What kinds of post-processing are required for SLM parts?
Typical SLM post-processing includes supports removal, stress relieving, surface polishing/linishing, Hot Isostatic Pressing to eliminate internal voids, and heat treatments if needed.
Can SLM make functionally graded materials?
Yes, SLM can fabricate complex graded structures by intelligently varying the feedstock composition and microstructure at various locations in a build.
Is SLM suitable for mass manufacturing?
Currently SLM is most applicable for small to medium production volumes up to thousands of parts where the benefits of design flexibility and customized properties justify costs.
SLM enables breakthrough performance gains using additive techniques. As the technology matures, costs will become more competitive.
Conclusion
Selective laser melting has revolutionized manufacturing across industries by enabling complex optimized geometries once impossible. It builds dense functional metal components from 3D model data by fusing powder layers with a focused laser. While costs are still higher for lower volumes, SLM provides unprecedented freedom to reimagine component designs for performance gains. Materials continuously expand from metals like titanium, aluminum, steel, nickel, and cobalt alloys. As the technology progresses, SLM will become viable for higher volume production, complementing conventional manufacturing where it provides advantages. SLM continues opening new possibilities for designers and engineers.
Share On
MET3DP Technology Co., LTD is a leading provider of additive manufacturing solutions headquartered in Qingdao, China. Our company specializes in 3D printing equipment and high-performance metal powders for industrial applications.
Inquiry to get best price and customized Solution for your business!
Related Articles
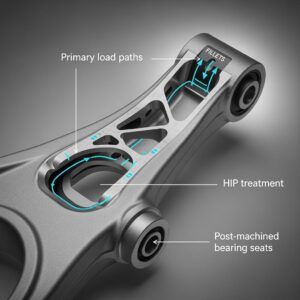
Metal 3D Printing for U.S. Automotive Lightweight Structural Brackets and Suspension Components
Read More »About Met3DP
Recent Update
Our Product
CONTACT US
Any questions? Send us message now! We’ll serve your request with a whole team after receiving your message.