SLS Metal Powder: Properties,Applications,and Suppliers
Table of Contents
Selective laser sintering (SLS) is an additive manufacturing technique that uses a laser to fuse small particles of plastic, metal, ceramic or glass powders into a 3D object. SLS metal powders with the right characteristics are critical to fabricating high-quality metal parts with complex geometries via this process.
Overview of SLS Metal Powders
SLS metal powders refer to metallic powders that are optimized for use in selective laser sintering 3D printers to produce metal parts and prototypes. The most commonly used SLS metal powders include:
SLS Metal Powder Types
Type | Composition | Key Characteristics |
---|---|---|
Stainless steel | Fe, Cr, Ni alloys | Corrosion resistance, high strength |
Tool steel | Fe, Cr, Mo alloys | High hardness, heat treatable |
Alloy steel | Fe, Cr, Ni alloys | Heat treatable, machinable |
Cobalt-chrome | Co, Cr alloys | Biocompatible, wear/corrosion resistant |
Titanium & alloys | Ti, Al, V alloys | Lightweight, biocompatible, strong |
Inconel | Ni, Cr alloys | Heat/corrosion resistant |
Aluminum alloys | Al, Cu, Mg alloys | Lightweight, strong |
These metal powders must have properties like flowability, particle shape and size distribution tailored to produce high density SLS parts with accuracy, precision and desired mechanical properties.
Key Properties of SLS Metal Powders
Parameter | Description | Requirements |
---|---|---|
Size range | Powder particle dimensions | 10-45 microns common |
Size distribution | Range of powder sizes | Mostly spherical with some satellites allowed |
Morphology | Powder particle shape | Spherical is optimal, satellites can cause defects |
Flow rate | Powder flowability | 35-40 s/50g from Hall flowmeter |
Apparent density | Powder packing density | Around 60% of true density |
True density | Material density | Varies by composition |
Surface area | Particle surface area per unit mass | Lower is better to reduce oxidation |
Residual gases & moisture | Impurities present with powder | Minimized for high quality parts |
SLS Metal Powder Characteristics
Characteristic | Role in SLS Process |
---|---|
Particle shape and surface texture | Affect powder flow into each new layer, laser absorption, reflectivity |
Particle size distribution | Impacts packing density, melt pool dynamics, spreadability |
Flow characteristics | Allows uniform spreadability, layer consistency |
Apparent density | Controls spacing between particles, energy input needed |
True density | Determines final maximum attainable part density |
Alloying additions | Enables specific material properties like strength, hardness etc. |
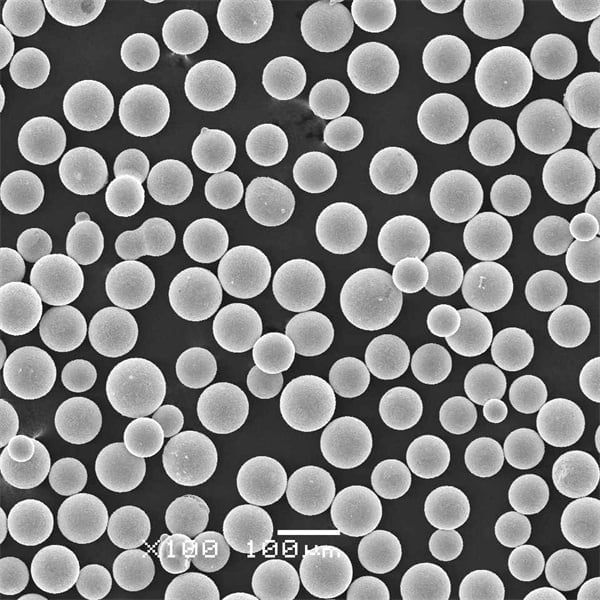
Applications of SLS Metal Powders
SLS metal powder enables printing of full density functional metal parts serving prototyping, tooling and short run production needs across industries like:
Industry Applications of SLS Printed Metal Parts
Industry | Applications | Common Materials Used |
---|---|---|
Aerospace | Turbine blades, engine/structural components | Stainless steels, superalloys, titanium alloys |
Automotive | Prototype parts, custom tooling | Stainless steels, tool steels, aluminum alloys |
Medical implants | Patient-specific implants, guides | Cobalt chrome, titanium alloys, stainless steel |
Industrial | Precision tooling, robot grippers | Stainless steels, tool steels |
Jewelry | Rings, chains, custom pieces | Precious metals like gold alloys, silver |
Some unique benefits versus traditional manufacturing routes:
Advantages of SLS for Metal Part Production
Benefit | Description |
---|---|
Geometry freedom | No part geometry restrictions unlike subtractive/casting methods |
Quick turnaround | Rapid printing from CAD data |
Light weighting | Lattice structures reduce weight by >30% |
Part consolidation | Integrally printed assemblies replace joints |
Mass customization | Patient-specific medical devices |
Hybrid structures | Metal & polymer multi-material parts possible |
Common SLS printed metal part applications across industries:
Typical Applications of SLS Printed Metal Parts
Application | Examples | Materials Used |
---|---|---|
Functional prototypes | Engine components, implants | Alloy steels, Ti alloys |
Tools | Drill guides, fixtures, jigs | Stainless steels |
Mold tooling | Injection molding tooling | Tool steels like H13 |
Series production | Aerospace/medical components | Ti & Ni alloys, CoCr |
Lightweight structures | Lattice panels, braces | Al alloys, Ti alloys |
SLS Metal Powder Specifications
SLS system manufacturers like EOS, 3D Systems, and Renishaw provide qualified SLS metal powder specifications tailored for their printer models. Some common metal powders and sizes include:
SLS Metal Powder Types and Size Ranges
Material | Powder Types Available | Particle Size Range |
---|---|---|
Stainless steel | 316L, 17-4PH, 303, 410 | 15-45 microns |
Maraging steel | MS1, 18Ni300, 18Ni350 | 15-45 microns |
Cobalt chrome | CoCr, CoCrMo | 15-45 microns |
Aluminum alloy | AlSi10Mg, AlSi12 | 15-45 microns |
Titanium alloy | Ti6Al4V Grade 5 | 15-45 microns |
Nickel alloy | Inconel 718, Inconel 625 | 15-45 microns |
Standards organizations have defined classifications for different metal powder grades used in AM processes:
Metal Powder Grades per ISO/ASTM Standards
Standard | Grades | Description |
---|---|---|
ISO 17296-2 | PA1 to PA6 | Defines increasingly stricter requirements on impurities from P1 to P6 |
ISO 17296-3 | PM1 to PM4 | Defines particle shape, size parameters from PM1 to PM4 |
ASTM F3049 | Class 1 to Class 4 | Defines allowable limits on composition ranges from 1 to 4 |
ASTM F3056 | Type 1 to Type 3 | Defines statistical size distribution parameters from 1 to 3 |
These grading schemes help set benchmark quality levels and aid buyers in procurement. High purity PA5 grade powder would ensure minimal contamination. Similarly Class 4 tighter chemistry control reduces variability.
SLS Metal Powder Suppliers
A variety of vendors supply ready-to-use SLS powders worldwide. Some leading global suppliers are:
Key SLS Metal Powder Suppliers
Supplier | Materials Offered | Geographies Served |
---|---|---|
Sandvik | Stainless steel, Ni alloys, CoCr, tool steel, aluminum alloys | Europe, Asia |
Praxair | Ti alloys, Ni alloys, stainless, tool steels | North America |
LPW Technology | Stainless steel, aluminum alloys, CoCr | UK, Europe |
Carpenter Additive | Stainless steels, CoCr, Cu, aluminum alloys | Global |
Hoganas | Stainless steels, tool steels | Europe, Asia |
Usual supply minimums are around 10 kg per material grade, though large volume contracts also exist for OEM buyers. Packaging options range from vacuum sealed cans to specialized SLS machine cartridges holding 700 g to 1 kg powder each.
SLS Metal Powder Packaging Types
Type | Volume Ranges | Characteristics |
---|---|---|
Vacuum cans | 500g to 20kg batches | Shelf life up to 1 year |
Printer cartridges | 700 to 1000g batches | Minimized handling exposure |
Material towers | 700 to 1200g cartridges | Automated feed into printer |
Price ranges for common materials in small quantities are:
Metal Powder Cost Ranges for SLS Printing
Material | Small Quantity Price Range* |
---|---|
Stainless steel 316L | $60-$100 per kg |
Aluminum AlSi10Mg | $80-$130 per kg |
Maraging steel | $90-$140 per kg |
Titanium Ti6Al4V | $200-$350 per kg |
Cobalt chrome | $300-$500 per kg |
Precious metals | $3000+ per kg |
Comparing SLS Metal Powder Materials
Various metal alloys are used for SLS printing, each with their own properties and tradeoffs:
SLS Metal Powder Materials Comparison
Parameter | Stainless Steels | Tool Steels | Titanium Alloys | Nickel Alloys | Cobalt Chrome | Aluminum Alloys |
---|---|---|---|---|---|---|
Density | Medium | Higher | Lower | High | High | Lowest |
Strength | Medium | Highest | Medium-High | Medium-High | Medium | Medium |
Hardness | Lower | Very high | Medium | Medium | Higher | Low-Medium |
Corrosion Resistance | Excellent | Medium | Excellent | Excellent | Excellent | Medium-Good |
Bio-compatibility | Good | Limited | Excellent | Limited | Excellent | Good |
Heat Resistance | Medium | Medium-High | Medium | Very High | Very High | Lower |
Cost | Lowest | Medium | High | Very High | High | Low |
We can see stainless steels offer the best combinational properties when cost is a consideration, while tool steels provide extreme hardness. Titanium brings biocompatibility and strength with low density. Superalloys like Inconel and CoCr offer thermal stability and biocompatibility. Aluminum alloys are the most cost-effective lightweight option.
Pros and Cons of Common SLS Metal Powders
Material | Advantages | Disadvantages |
---|---|---|
Stainless steels | Cost-effective, readily machinable | Lower hardness and strength |
Tool steels | Extremely hard and heat treatable | Less corrosion resistance, biocompatibility |
Titanium alloys | Strong, lightweight, bio-friendly | Expensive, can burn in oxygen atmosphere |
Nickel alloys | Excellent heat/corrosion resistance | Heavy, toxic, very expensive |
Cobalt chrome | Biocompatible, corrosion resistant | Heavy, medium cost |
Aluminum alloys | Lightweight, good strength | Lower melting point, hardness |
Customer Criteria for Selecting SLS Metal Powder
Selection Criteria | Key Questions |
---|---|
Mechanical properties | Does it meet target application strength, wear resistance and other mechanical specifications? |
Material cost | Does desired metal powder type fit application budgets? |
Post-processing | Are secondary operations like Hot Isostatic Pressing or heat treatment needed? |
Production run size | Is target volume too high for production SLS printing? |
Part size dimensions | Is maximum printer build volume sufficient for largest part geometries? |
Resolution, surface finish | Can SLS process achieve fine-feature-detail and surface quality requirements? |
Delivery lead time | Is supplier lead time acceptable considering production timeline? |
The end part application guides optimal material selection balancing performance needs and economics.
SLS Metal Printing Process Overview
Understanding SLS 3D printing helps appreciate how powder properties affect part quality:
SLS 3D Printing Process Stages
Stage | Description |
---|---|
3D Modeling | CAD software creates solid/mesh model of part to print |
Slicing | Model is digitally sliced into layers to generate printer file |
Powder spreading | Roller or blade spreads thin layer of powder on build platform |
Laser scanning | CO2 laser scans over powder bed to melt particles together |
Lowering platform | Build platform lowers by 1 layer thickness (~50 microns) |
Repeat spreading/melting | Steps repeat until full object is built up layer-by-layer |
Post-processing | Excess powder removed, final treatments done to finish part |
How Powder Characteristics Impact Print Results
Powder Property | Influence on Print Quality |
---|---|
Powder geometry | Spherical particles with good flow enable uniform layers without defects |
Particle size range | Too fine powders have poor flow, too large creates poor resolution |
Size distribution | Too wide a distribution can segregate or create variable melting |
Apparent density | Higher density yields greater final part density after sintering |
True density | Places upper limit on achievable part density |
Surface texture | Rougher particles can trap gases or hamper powder flow |
We can see several powder physical properties directly impact print results, so tight control by suppliers is crucial.
Post-Processing of SLS Printed Metal Parts
After the SLS printing process, additional finishing steps help improve final part properties:
Common SLS Part Post-Processing Steps
Process | Description | Benefits |
---|---|---|
Powder removal | Excess powder brushed/blasted off | Reveals printed object |
Stress relieving | Heating to remove residual stresses | Improves dimensional accuracy |
Surface finishing | Sanding, polishing, bead blasting | Smoothens surface, aids coating adhesion |
Infiltration | Liquid fills residual porosity | Further increases density, improves strength |
Heat treatment | Hardening and tempering thermal cycles | Enhances hardness in steels |
Post-Processing Effects on Part Properties
Property | Post-Processing Influence |
---|---|
Density | Infiltration with epoxy or bronze fills pores increasing density 5-15% |
Surface roughness | Manual/automated polishing can achieve under 2 micron roughness |
Dimensional accuracy | Stress relieving heat cycle reduces warpage improving precision |
Tensile strength | Infiltration improves UTS while heat treatment can double yields strength |
Ductility | Tradeoff with strength improvement from post-treatments |
Hardness | Precipitation hardenable alloys like 17-4PH respond well to aging treatments |
Thus post-processing allows tailoring metal properties further based on application needs.
SLS Metal Printing Quality Control
Consistent high quality powder feedstock coupled with SLS process monitoring ensures reliable parts:
Quality Control for SLS Metal Powder
Parameter | Typical Specification | Test Methods |
---|---|---|
Particle size distribution | Hall flow rate > 35s/50g | Sieving, laser diffraction |
Apparent density | 65-80% of true density | Gravimetric measurement |
Powder composition | Alloying ranges per ISO 27296 | X-Ray fluorescence |
Surface morphology | Median circularity > 0.75 | Micrographs, image analysis |
Contamination | < 50 ppm oxygen, < 150 ppm nitrogen | Inert gas fusion analysis |
In-Process Monitoring for SLS Printing
Metric | Sensor Used | Purpose |
---|---|---|
Laser power | Built-in photodiode | Maintains fusion consistency |
Powder bed temp | IR sensor | Ensures part integrity, no warping |
Atmosphere | Oxygen analyzer | Avoids powder ignition in build chamber |
Layer thickness | Z-axis encoder | Precise reproducible layers |
Such stringent control over input powder and process settings results in high quality metal parts from each production run.
SLS Metal Printing Compared to Alternatives
Other metal 3D printing alternatives to SLS include:
Comparison of Metal 3D Printing Methods
Metric | Binder Jetting | DMLS | SLM | EBM |
---|---|---|---|---|
Raw material | Metal/polymer mix powder | Metal powder | Metal powder | Metal wire/powder |
Energy source | Liquid binder | Fiber laser | Powerful Yb fiber laser | Electron beam |
Build speed | Moderate, faster than laser methods | Slow due to point-by-point scanning | Very fast, full melting occurs | Fastest method |
Resolution, surface finish | Poorer due to binder, post-processing helps | Very good due to fine laser spot | Excellent due to full melting | Moderate due to partial melting |
Dimensional accuracy | +/- 0.3% with CTQ process | +/- 0.1-0.2% | +/- 0.1-0.2% | +/- 0.2-0.3% |
Post-processing | Curing, sintering both needed | Only support removal | Some machining may be needed | Most secondary work needed |
Cost per part | Lower material cost helps reduce price | Much higher operating cost | High equipment, material cost | High equipment cost |
Among all methods, binder jetting has emerged as most cost-effective for metal part production at lower volumes up to 10,000 units. SLS provides the easiest post-processing combined with good accuracy and surface finish.
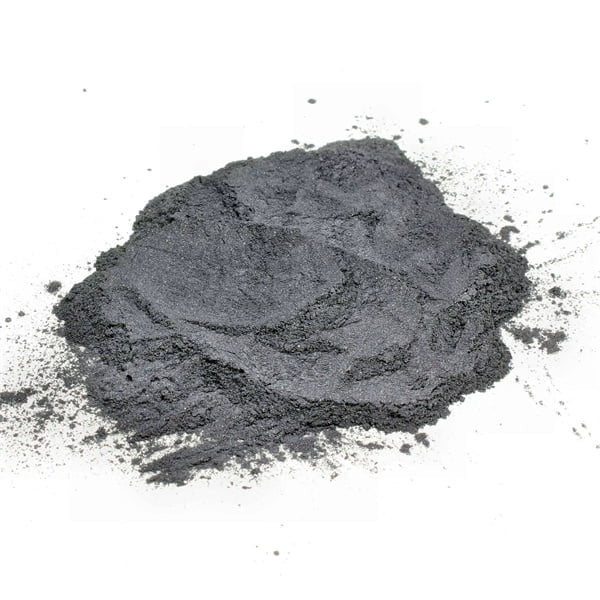
FAQs
What industries use SLS metal printing?
SLS metal printing is used in aerospace, automotive, medical, and many other industries where precision metal parts are required.
What is the accuracy and resolution of SLS metal printing?
The accuracy and resolution depend on several factors, including the machine, material, and process parameters, but SLS metal printing can achieve high levels of precision.
Is post-processing required for SLS metal-printed parts?
Yes, post-processing may be required to remove support structures, improve surface finish, and meet specific requirements for the application.
What are the limitations of SLS metal printing?
Some limitations include the cost of equipment, limited size of build chambers, and the need for proper safety measures due to the use of lasers and metal powders.
Can SLS metal printing be used for mass production?
Yes, SLS metal printing can be used for both prototyping and low to medium-volume production of metal parts.
Is SLS metal printing environmentally friendly?
While it can reduce material waste compared to traditional manufacturing methods, the disposal of metal powders and energy consumption are factors to consider regarding its environmental impact.
Are there any safety precautions when working with SLS metal printing?
Yes, safety measures should be taken when handling metal powders, and operators should be trained to work with laser-based systems safely.
What is the cost of SLS metal printing services?
The cost varies depending on factors such as material choice, part complexity, and quantity. It’s best to request quotes from service providers for specific projects.
Share On
MET3DP Technology Co., LTD is a leading provider of additive manufacturing solutions headquartered in Qingdao, China. Our company specializes in 3D printing equipment and high-performance metal powders for industrial applications.
Inquiry to get best price and customized Solution for your business!
Related Articles
About Met3DP
Recent Update
Our Product
CONTACT US
Any questions? Send us message now! We’ll serve your request with a whole team after receiving your message.
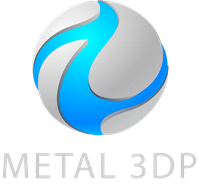
Metal Powders for 3D Printing and Additive Manufacturing