Specialty Metal Powders
Table of Contents
Specialty metal powders refer to metals that have been processed into fine particulate form for use in advanced manufacturing techniques. They exhibit unique properties that make them suitable for specialized applications across industries like aerospace, medical, electronics, and more.
This article will provide a comprehensive overview of various types of specialty metal powders, their composition and characteristics, applications, specifications and grades, suppliers, pricing, and advantages vs limitations.
Types of Specialty Metal Powders
There are many categories and varieties of specialty metal powders used in different technologies. Some major types include:
Type | Description |
---|---|
Nickel Alloys | Inconel, Monel, Hastelloy, Nilo alloys with nickel plus chromium, iron, molybdenum etc. High strength and corrosion resistance at high temperatures |
Cobalt Alloys | Haynes alloys with cobalt and chromium/tungsten/molybdenum. Biocompatibility for implants |
Titanium Alloys | Ti-6Al-4V, Ti-6Al-7Nb etc. Lightweight, strength, biocompatibility |
Refractory Metals | Tungsten, molybdenum, tantalum. Extremely high melting points |
Magnetic Alloys | Iron, nickel or cobalt alloys with high permeability and low coercivity |
Thermal Spray Powders | Spheroidal powders for coatings to resist wear, corrosion etc. |
Advantages of Powder Metallurgy
Advantage | Description | Benefit | Example |
---|---|---|---|
Minimal Waste | Powder metallurgy boasts an exceptionally high material utilization rate, often exceeding 97%. This is because parts are formed from precisely measured quantities of metal powder, minimizing scrap compared to traditional subtractive processes like machining. | Reduced production costs, environment-friendly manufacturing, and minimal post-production cleanup. | Gears, bearings, and other intricate components can be formed with near-net shapes, requiring minimal machining and generating very little scrap. |
Design Flexibility | Unlike traditional techniques limited by the formability of bulk materials, powder metallurgy thrives on intricate shapes. Complex geometries, undercuts, and even internal channels can be incorporated into the design thanks to the freedom of mold pressing. | Parts with intricate features or challenging geometries can be produced efficiently, eliminating the need for assembly of multiple components. | Electrical contacts with intricate details and heat sinks with internal channels for improved heat dissipation can be manufactured using powder metallurgy. |
Material Versatility | The world of metal alloys is at your fingertips with powder metallurgy. By blending different metal powders or incorporating additional elements, a vast array of material properties can be achieved. This includes control over factors like porosity, strength, and conductivity. | Components requiring a specific combination of properties, such as high wear resistance and electrical conductivity, can be tailored through material selection in the powder stage. | Self-lubricating bearings can be produced by incorporating lubricant particles into the metal powder mix. Additionally, components requiring high strength-to-weight ratios can be achieved through the use of lightweight metal alloys. |
Dimensional Accuracy & Repeatability | Powder metallurgy excels in producing parts with tight tolerances. The precise control over powder characteristics and pressing forces translates to consistent part dimensions across high-volume production runs. | Reduced post-machining requirements, improved product quality, and interchangeable parts. | Gears, pistons, and other mechanical components can be manufactured with high dimensional accuracy, ensuring smooth operation and proper assembly. |
Near-Net Shapes & Reduced Machining | The ability to form complex shapes with high precision minimizes the need for extensive post-production machining. This translates to significant cost and time savings. | Faster production times, lower manufacturing costs, and improved surface finishes. | Complex components like cams and sprockets can be near-net shaped, requiring minimal machining to achieve final dimensions. |
Controlled Porosity | Powder metallurgy offers a unique advantage: the ability to tailor the porosity of a part. This controlled pore volume can be beneficial for applications requiring lubrication reservoirs, filtration elements, or even bone implants that promote tissue ingrowth. | Improved functionality, filtration capabilities, or enhanced biocompatibility. | Oil filters and self-lubricating bearings can leverage controlled porosity within the material for improved performance. |
Heat Treatment Capabilities | Similar to wrought metals, powder metallurgy parts can undergo heat treatment processes to enhance their mechanical properties such as strength, hardness, and wear resistance. | Improved performance and broader application suitability. | Gears and sprockets can be heat treated to achieve superior wear resistance and fatigue strength. |
Automation & High-Volume Production | Powder metallurgy is well-suited for automation, enabling high-volume production with consistent quality. The entire process, from powder filling to compaction and sintering, can be automated for efficient manufacturing. | Cost-effective mass production, reduced labor costs, and consistent product quality. | Small, intricate components like fasteners and electronic connectors can be efficiently produced in high volumes using automated powder metallurgy processes. |
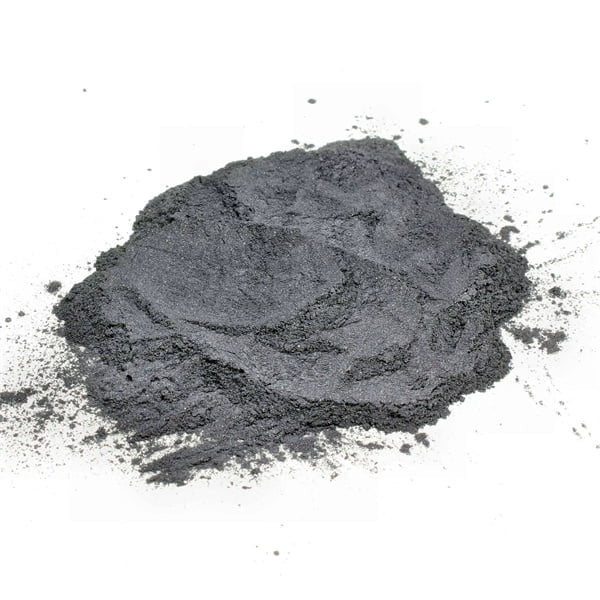
Composition and Characteristics
Specialty metal powders can contain a variety of alloying elements to achieve desired properties. Some typical compositions and characteristics are outlined below:
Material | Typical Composition | Characteristics |
---|---|---|
Nickel Alloys | Ni, Cr, Fe, Nb, Mo | Resistant to heat, corrosion. Good strength and toughness |
Cobalt Alloys | Co, Cr, W, Ni, Mo | Biocompatible, high hardness and wear resistance |
Titanium Alloys | Ti, Al, V, Nb, Ta | Extremely strong yet lightweight. Bio-inertness |
Refractory Metals | W, Mo, Ta | Outstanding high temperature properties, thermal/electrical conductivity |
Magnetic Alloys | Fe, Ni, Co, Nd, Sm | High saturation magnetization and magnetic permeability |
The specific percentages of each element can be varied to produce powders with slightly different properties for intended applications. More exotic specialty alloys are also possible through blending multiple metals.
Particle Characteristics
In addition to composition, powder characteristics like particle shape, size distribution, flowability, and purity also impact performance.
- Particle shape – Spherical, irregular, mixed. Determines packing density and sintering behavior.
- Size distribution – Range and distribution of sizes. Affects densification and properties.
- Flowability – Crucial for dispensing precision in AM. Improved by sphericity and size uniformity.
- Purity – Oxygen/nitrogen content affects quality. Higher is better.
Manufacturers closely control these powder attributes to guarantee consistency between batches.
Applications of Specialty Metal Powders
The unique benefits of specialty metal powders make them suitable for niche applications where traditional metal products fall short. Some examples include:
Industry | Applications |
---|---|
Aerospace | Turbine blades, aircraft fittings, rocket nozzles |
Medical | Orthopedic/dental implants, surgical instruments |
Automotive | Lightweight chassis parts, high performance components |
Electronics | Shielding, contacts, leadframes, connectors |
Industrial | Tooling, heat treatment fixtures, wear/corrosion resistant coatings |
Other common applications are chemical processing equipment, sporting goods, watchmaking components etc. Usage continues to grow with wider adoption of additive manufacturing.
Grades and Specifications
Like conventional metals, powder metallurgy grades are standardized by professional organizations to enable consistent quality and performance. Some key standards include:
Standard | Organization | Materials |
---|---|---|
ASTM | ASTM International | Nickel, cobalt, titanium alloys |
UNS | SAE International | Specialty metal alloys |
ISO | International Organization for Standardization | Wide range metals and ceramics |
Within each standard, materials are designated unique codes for identification. Additionally, specifications related to composition limits, powder characteristics, sampling, testing etc. are provided to regulate quality.
Chemistry conformation certificates and test reports are supplied by reputable manufacturers to validate compliance with the purchased specification. Custom grades outside standards are also possible for proprietary applications.
Suppliers and Pricing
There are a number of leading global suppliers providing specialty metal powders for commercial use:
Supplier | Typical Materials | Average Pricing |
---|---|---|
Sandvik | Nickel, cobalt, titanium alloys | $50 – $100 per kg |
Praxair | Nickel, iron, tungsten alloys | $75 – $250 per kg |
Hoganas | Tool steels, stainless steels | $30 – $150 per kg |
GKN | Titanium, aluminum alloys | $100 – $300 per kg |
Carpenter Tech | Extensive specialty alloys | $250 – $500 per kg |
Pricing ranges significantly depending on alloy complexity, order volume, powder characteristics and quality standards. Generally spherical powders with controlled size distribution command premium pricing.
Comparison Between Materials
There is no universally best specialty alloy – specific tradeoffs exist between various powder metal options:
Parameter | Nickel Alloys | Titanium Alloys | Refractory Metals |
---|---|---|---|
Strength | Very good | Excellent | Good |
Hardness | Good | Very Good | Excellent |
Toughness | Excellent | Good | Average |
Corrosion Resistance | Excellent | Very Good | Average |
High Temperature Resistance | Excellent | Average | Excellent |
Biocompatibility | Average | Excellent | Average |
Cost | High | Very High | Average |
Key Takeaways:
- Nickel alloys offer best all-round properties but are expensive
- Titanium alloys have outstanding strength-to-weight ratio but can lack ductility
- Refractory metals withstand extreme temperatures but are less corrosion resistant
- Correct selection depends on critical performance needs for the application
Advantages of Powder Metallurgy
Some notable benefits of specialty metal powders:
Higher purity – Rapid solidification in atomization allows higher achievable purity over conventional cast/wrought metals. This expands viable applications and operating envelopes.
Precision attributes – Consistent powder characteristics enable repeatable output, tighter tolerances and quality control for critical components like aerospace turbines and medical implants.
Complex geometries – Specialty powders empower production of topologically optimized, lightweight or porous components impossible through subtractive techniques.
Customizability – Alloy chemistry and powder attributes can be tailored to meet specific mechanical, physical or biological property needs.
Sustainability – Additive techniques have lower buy-to-fly ratio and use less material over machining from bulk stock. This supports greener manufacturing.
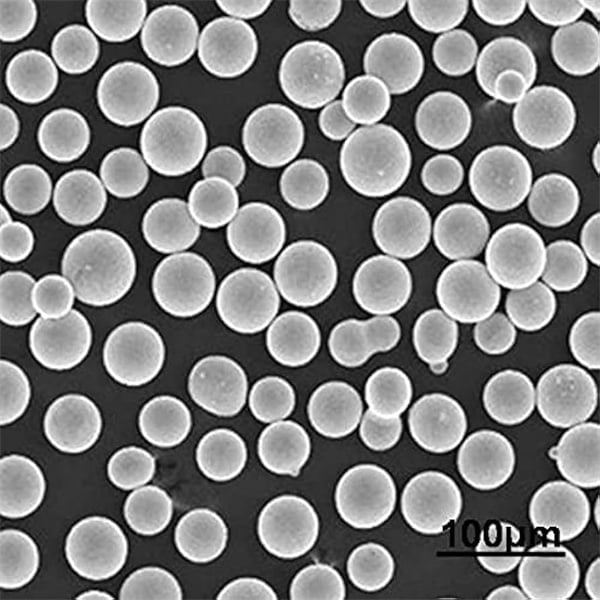
Challenges With Powder Metallurgy
Challenge | Description | Impact | Potential Solutions |
---|---|---|---|
Powder Characteristics and Flowability | Inconsistent particle size, shape, and distribution within the powder can lead to uneven density, porosity, and surface roughness in the final product. Poor flowability of the powder can hinder efficient filling of molds, causing defects and production delays. | Reduced mechanical properties, compromised part integrity, and potential for component failure. Production inefficiencies and increased scrap rates. | Rigorous powder characterization and control of particle size distribution. Utilizing spherical or angular powders depending on the desired density and properties. Employing lubricants or flowability additives to enhance powder flow. |
Density Variations and Porosity | Achieving uniform density throughout complex geometries can be difficult. Internal voids or porosity can weaken the part and impact its functionality. | Reduced strength, ductility, and fatigue resistance. Potential for leaks in pressurized applications. | Utilizing compaction techniques like pressing or isostatic pressing to achieve optimal density. Implementing computer-aided simulations to predict and mitigate density variations. Optimizing part design to minimize complex features and promote even powder flow. |
Delamination and Cracking | Weak inter-particle bonding during compaction can lead to delamination (internal separation) or cracking within the part. | Compromised mechanical properties and potential for catastrophic failure under stress. | Optimizing powder properties like surface morphology and chemical composition to enhance bonding. Utilizing higher compaction pressures or sintering temperatures. Implementing secondary operations like hot isostatic pressing to eliminate internal defects. |
Cost Considerations | High-purity powders, complex near-net-shape manufacturing techniques, and post-processing treatments can significantly increase production costs. | Limited cost-effectiveness compared to traditional metalworking methods for certain applications. | Utilizing cost-effective powder materials and optimizing part design for efficient powder usage. Exploring alternative compaction technologies with lower energy requirements. Implementing powder recycling strategies to minimize material waste. |
Environmental Impact | Powder handling and processing can generate airborne dust and potentially hazardous fumes, posing health risks and environmental concerns. | Detrimental effects on worker health and potential environmental pollution. | Implementing robust dust collection and ventilation systems to maintain a safe working environment. Utilizing eco-friendly lubricants and binders in the powder mix. Following strict environmental regulations for waste disposal. |
Limitations in Material Selection | Not all metals and alloys are readily available in powder form, and some materials may experience degradation during the powder production process. | Restricted design freedom for applications requiring specific material properties. | Ongoing research and development in powder production technologies to expand the material selection for PM. Utilizing composite powder blends or metal injection molding (MIM) for advanced material combinations. |
FAQ
This FAQ section provides answers to common inquiries on powder metallurgy for reference:
What are the most widely used specialty metal powders today?
Titanium alloys, nickel-based superalloys, cobalt-chrome alloys and tool steels comprise majority of demand. Main applications are in aerospace engines, joint replacement implants, automotive/industrial tooling and tool steels for molds and dies.
What methods can be used to produce specialty metal powder?
Common commercial production techniques include gas atomization, plasma atomization, electrolysis and carbonyl decomposition. Each have relative advantages – gas atomization offers the best combination of cost and consistent powder size/shape.
How are metal powders characterized?
Typical characteristics examined are particle size distribution, morphology, flow rate, tap density, chemical composition, microstructure and contamination levels. These influence suitability for AM processes and final part properties.
What size range do specialty powders for AM fall under?
Vast majority of powders fall between 10 microns to 100 microns. Finer particles can combust or be hazardous to handle while larger particles negatively affect resolution, density and surface finish.
What is an inert gas atomized specialty alloy?
It refers to a high performance powder produced by atomizing the molten metal stream using an inert gas like argon or nitrogen to avoid contamination. This is the preferred production method for reactive alloys.
How are parts post-processed after AM?
Common post-processing includes HIP (hot isostatic pressing), heat treatment, Hot Isostatic Pressing (HIP), surface finishing, coating, and final inspection/testing to meet application requirements.
Share On
MET3DP Technology Co., LTD is a leading provider of additive manufacturing solutions headquartered in Qingdao, China. Our company specializes in 3D printing equipment and high-performance metal powders for industrial applications.
Inquiry to get best price and customized Solution for your business!
Related Articles
About Met3DP
Recent Update
Our Product
CONTACT US
Any questions? Send us message now! We’ll serve your request with a whole team after receiving your message.
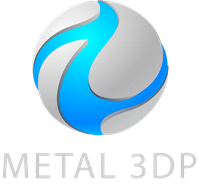
Metal Powders for 3D Printing and Additive Manufacturing