Spherical Tungsten Powder
Table of Contents
Spherical tungsten powder refers to fine granular particles consisting of pure tungsten metal shaped into highly round, smooth microspheres. Precision engineered spherical morphology allows these powders to deliver enhanced flowability, packing density, and sintered part quality compared to irregular crushed tungsten variants across manufacturing techniques leveraging tungsten’s unique density, strength, and thermal properties.
This guide covers different grades of spherical tungsten powders, production methods, key characteristics, specifications, pricing details from suppliers, pros and cons, and answers common questions on integrating spherical tungsten powder into components via advanced fabrication processes.
Types of spherical tungsten powder
Property | Description | Importance in Applications |
---|---|---|
Purity | Measured as a percentage of tungsten (W) by weight, with minimal presence of other elements like oxygen, carbon, or impurities. Common grades range from 99.5% to 梛99.95% (NATO standard for at least 99.95% purity). | High purity ensures the final product’s strength, density, and conductivity. Applications demanding exceptional performance, like armor plating or heat sinks, require higher purity (>99.9%). |
Sphericity | Represents how closely a particle resembles a perfect sphere. Measured as a percentage, with values exceeding 90% considered highly spherical. Techniques like morphological analysis (image analysis) quantify sphericity. | Sphericity influences powder flowability, packing density, and printability in 3D printing. Spherical particles flow freely, enabling consistent material deposition during additive manufacturing. |
Particle Size Distribution (PSD) | Refers to the variation in particle diameters within a powder batch. Typically characterized by a statistical distribution curve, with common methods employing laser diffraction or sieving. | A narrow PSD with minimal outliers (large or small particles) is crucial for uniform packing and minimizing voids in the final product. Tight control over PSD is essential in applications like thermal spraying, where consistent coating properties rely on uniform particle size. |
Apparent Density | Represents the mass of powder per unit volume when loosely packed, expressed in g/cm³. Measured using standardized techniques like the tap density test. | Apparent density influences powder handling, storage requirements, and material usage efficiency. Higher apparent density powders require less storage space and potentially lower overall material usage. |
Flowability | Indicates how easily powder flows under gravity. Measured by the time it takes for a specific amount of powder to flow through a standardized funnel. Units are typically seconds per gram (s/g). | Good flowability is essential for efficient powder handling in various applications. It ensures consistent material feed during additive manufacturing processes and minimizes segregation (uneven distribution) during storage or transportation. |
Surface Morphology | Describes the surface texture and features of the powder particles. Techniques like scanning electron microscopy (SEM) visualize surface morphology. | Surface characteristics can influence factors like sintering behavior (bonding during heat treatment) and interaction with other materials. A smooth surface promotes better packing and sintering, while a rougher surface might enhance adhesion to other materials. |
Oxygen Content | Measured in parts per million (ppm) and represents the amount of oxygen present in the tungsten powder. Low oxygen content is generally desirable. | Excessive oxygen can lead to embrittlement (loss of ductility) and hinder the performance of the final product. Tungsten applications in high-temperature environments often necessitate very low oxygen levels (less than 100 ppm). |
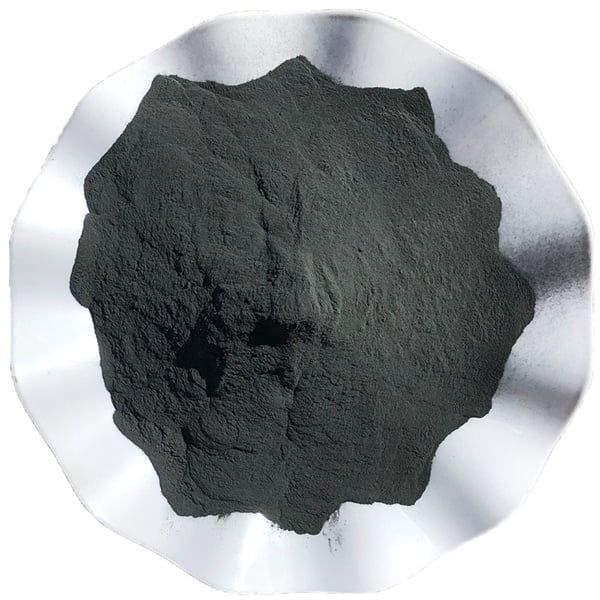
Production Methods
Method | Description | Typical Outputs |
---|---|---|
Plasma Spheroidization | Tungsten ingots atomized into droplets in a plasma torch then rapidly quenched | High purity, spherical morphology, moderate throughput |
RF Plasma Sputtering | Tungsten vapor collects on substrates in a spherical morphology | Ultrafine nano-powders down to 20 nm sizes but low productivity |
Thermal Plasma | Very high temp plasma jet melts tungsten rods into smooth molten droplets | Medium batch sizes with high density |
Rotating Electrode | Centrifugal atomization forces shape droplets detached from spinning tungsten melt stream | Lower cost process but less control over size distribution |
Plasma methods allow precise tuning of particle formation leading powders with smoother, rounder profiles preferred for higher packing densities in sintering processes or binder flow dynamics across metal injection molding techniques.
Properties of Spherical Tungsten Powder
Benefits stemming from the spherical morphology and purity include:
Property | Characteristics | Advantages |
---|---|---|
Improved flowability | Powder feeds smoothly without clogging valves and pipes | Prevents jams during dispensing for printing processes |
Enhanced packing density | Microspheres stack tightly with optimized space filling | Increases green compact density before sintering to near theoretical levels |
Higher sintered density | Roundness aids internal pores and voids elimination | Maximizes mechanical performance – hardness, strength, thermal/electric conductivity |
Consistent shrinkage | Low variation across precise batches | Tighter process controls and product performance standards |
Increased surface area | Smoother micro-ball structure across larger collective area | Improves powders reactivity across chemical, electrical and thermal interfaces |
The premium qualities imparted by spherical morphology promote downstream fabrication innovations and tighter tolerances.
Applications of Spherical Tungsten Powder
Primary uses include:
Industry | Common Applications | Benefits |
---|---|---|
Additive Manufacturing | Printed dense tungsten weights, shielding | High density without voids in printed geometry |
Injection Molding | Radiation shielding, balancing components | Improved binder flow allows complex molds |
Electronics | Heat sinks, electrodes, contacts | Enhanced thermal dissipation across larger surface area |
Radiology Equipment | Collimator components, beam blocking shields | Dense high Z-number element blocks X-Rays |
Vibration Dampening | Gyroscope weights, audio speaker mass balances | Density combined with ductility reduces resonance |
Fishing Lure Weights | Eco-friendly non-toxic alternative to lead weights | Heavy weights for sinkers, jigs, or ballast |
Leveraging spherical morphology to fully harness tungsten’s intrinsically high density and temperature resistance supports innovative fabricated solutions across this wide range of industries.
Specifications of Spherical Tungsten Powder
Property | Description | Importance for Applications |
---|---|---|
Purity | ≥99.9% Tungsten (W) | High purity minimizes impurities that can weaken the final product and hinder its performance. Electrical and thermal conductivity rely heavily on minimal impurities for optimal function. |
Oxygen Content | ≤100ppm (parts per million) | Low oxygen content prevents the formation of tungsten oxides which can lead to brittleness and hinder sintering (bonding) during processing. |
Sphericity | ≥98% | A highly spherical shape offers several advantages: * Improved Flowability: Spherical particles flow freely, enabling consistent packing and density in applications like 3D printing. * Packing Efficiency: Spherical particles pack more densely, leading to higher achievable densities in the final product. * Reduced Surface Area: Lower surface area minimizes interaction with surrounding materials and reduces oxidation during processing. |
Surface Morphology | Smooth surface, free from satellite particles | A smooth surface minimizes defects and promotes good inter-particle bonding during sintering. Satellite particles (small particles attached to larger ones) can act as stress concentrators and weaken the final product. |
Particle Size Distribution | Typically offered in a range of sizes (e.g., 5-25μm, 15-45μm) | Controlled particle size distribution is crucial for several reasons: * Packing Density: A narrow size distribution allows for denser packing and minimizes voids in the final product. * 3D Printing: Particle size needs to be compatible with the specific 3D printing technology being used. * Sintering Behavior: Particle size can influence the sintering process, with smaller particles typically sintering faster than larger ones. |
Flowability | ≤6.0 seconds for 50g of powder | Excellent flowability ensures smooth and consistent powder movement during processing. This is critical in applications like 3D printing where consistent powder flow is essential for building precise features. |
Density | High loose density (≥9.5 g/cm³) and high vibration density (≥11.5 g/cm³) | High density is a key characteristic of tungsten, contributing to its strength, weight, and superior performance in applications like radiation shielding and armor. * Loose density refers to the density of unpacked powder. * Vibration density is the density achieved after the powder is vibrated to achieve a closer packing. |
Melting Point | 3422°C (6192°F) | The extremely high melting point of tungsten makes it suitable for high-temperature applications like heating elements, rocket nozzles, and furnace linings. |
Electrical Conductivity | High (similar to copper) | Excellent electrical conductivity allows tungsten to be used in electrical contacts, electrodes, and filaments in incandescent lamps. |
Thermal Conductivity | High (amongst the highest of metals) | Superior thermal conductivity makes tungsten ideal for heat sinks, heat pipes, and applications requiring efficient heat dissipation. |
Suppliers and Pricing
Supplier | Grades | Pricing Estimate |
---|---|---|
Midwest Tungsten | 99.9% – 99.995% Purity<br>1-10 micron sizes | $50 – $150 per kg |
Buffalo Tungsten | 99-99.9% grades<br>Fine to coarse sizes | $45 – $280 per kg |
Global Tungsten | 99.9%, 99.95%, 99.99%<br>Custom alloys | $55 – $250 per kg |
Nano Research Labs | 99.9% pure under 1 micron | $150+ per kg |
Pricing ranges widely from $50/kg for common purity and size variants suitable for fishing lure weights and kinetics experiments requiring only basic density up to over $250/kg for high purity submicron nano powders used in specialized additive manufacturing or electronics applications where consistent chemistry and sizes are paramount.
Pros and Cons
Pros | Cons |
---|---|
Enhanced flowability through binders and spraying mechanisms | Requires inert atmosphere handling given risks of hydrogen embrittlement from moisture |
Higher green part density before sintering | Brittle after densification – requires ductile metal infiltrations |
Improves surface finish of finished components | Handling as carcinogenic dust challenges at industrial levels |
Environmentally friendlier than lead for heavy weights | Conflict sourcing concerns for raw tungsten supply chains |
Allows ultrafine detail resolution with nano grade particles | Higher costs than crushing irregular powder from scrap |
Spherical shaping coupled with advanced manufacturing techniques expands applications for tungsten while mandatory handling precautions must be codified.
Limitations and Considerations
Limitation/Consideration | Description | Impact | Mitigation Strategies |
---|---|---|---|
Cost | Spherical tungsten powder is generally more expensive than irregularly shaped tungsten powder due to the complex manufacturing processes involved. | The higher cost can be a significant factor for some applications, especially those requiring large quantities of powder. | * Evaluate the cost-benefit trade-off. Spherical tungsten powder’s superior performance may justify the cost in some applications. * Explore alternative manufacturing methods that may offer a balance between cost and desired properties. |
Handling Precautions | Tungsten powder is a fine dust and can be a respiratory hazard if inhaled. Additionally, tungsten can be pyrophoric (ignite spontaneously) in finely divided forms. | Improper handling can pose safety and health risks. | * Implement strict safety protocols for handling tungsten powder, including proper ventilation, personal protective equipment (PPE) like respirators, and careful handling techniques to minimize dust generation. * Follow safe storage practices to prevent fires and explosions. Grounding and inert atmosphere storage may be necessary for very fine powders. |
Moisture Sensitivity | Spherical tungsten powder is susceptible to oxidation when exposed to moisture. Oxidation can lead to the formation of tungsten oxides which can negatively impact processing and final product properties. | Maintaining a dry environment is crucial for storage and handling. | * Store spherical tungsten powder in sealed containers with desiccant packs to control moisture. * Utilize moisture meters to monitor moisture content during processing. |
Brittleness of Densified Parts | While spherical tungsten powder offers good packing density, the final sintered product can be brittle, especially without further processing. | Brittleness limits the applications of pure tungsten parts. | * Utilize post-sintering infiltration with ductile metals like copper or nickel to enhance toughness and ductility. * Explore alternative materials or composites that may offer a better balance of strength and ductility for specific applications. |
Limited Availability of Ultra-Fine Powders | Spherical tungsten powder below 1 micron in size can be challenging and expensive to produce. | Limited availability can restrict applications requiring extremely fine features or high packing densities. | * Source from specialized manufacturers who can produce ultra-fine spherical tungsten powder. * Explore alternative materials or powder manufacturing techniques that may offer suitable alternatives for ultra-fine applications. |
Environmental and Ethical Considerations | Tungsten mining can have negative environmental impacts, and conflict minerals may be a concern in the supply chain. | Responsible sourcing practices are essential. | * Source tungsten powder from reputable suppliers who prioritize sustainable mining practices and ethical sourcing. * Look for certifications that ensure responsible tungsten sourcing, such as the Conflict-Free Smelter Initiative (CFSI). |
FAQ
Question | Answer |
---|---|
What particle size is typically used? | 1-20 microns common, with nano grades below 1 micron gaining traction |
What is the melting point of tungsten? | 3422 °C, one of the highest melting point metal elements |
Is spherical powder safer than crushed variants? | Reduced dust is safer but still requires careful handling precautions |
What is spherical tungsten mainly used for today? | Around 65% consumed for tungsten carbide production as precursor |
How heavy is tungsten compared to steel? | Nearly 2X as dense. Steel ~8 g/cc, tungsten 19 g/cc |
Where is natural tungsten ore mined? | China provides over 80% of current global supply |
Does it carry conflict mineral risks like cobalt? | Less severe than cobalt but responsible sourcing still essential |
Is the powder flammable or explosive? | No flammability but fine dust burn/detonation risks requiring precautions |
Broadening applications take advantage of premium qualities while securing supply chains against disruptions proves pivotal.
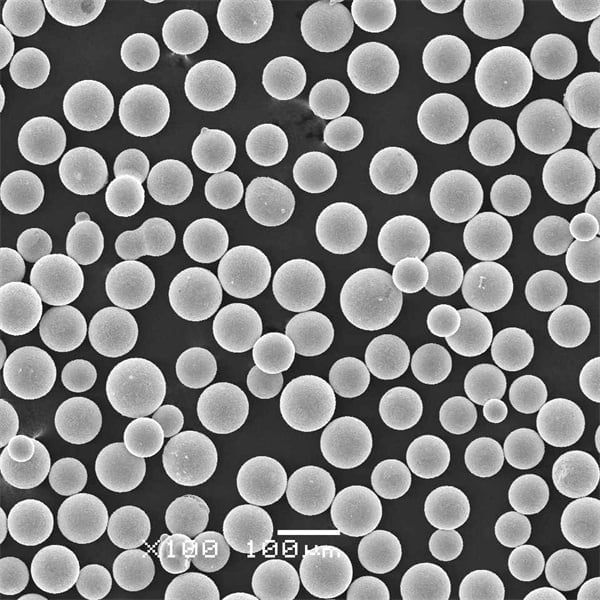
Conclusion
Precision spherical shaping unlocks improved fabrication results across metal additive manufacturing and injection molding processes ready to displace waste-heavy traditional machining techniques across growing application segments as diverse as radiation shielding and audiophile speakers. But capturing these opportunities sustainably while navigating raw materials shortages layered atop geopolitical conflict concerns presses manufacturers toward responsible, localized supply chains increasingly prioritizing recycling. Simultaneously, innovations from augmented reality-guided handling procedures to reactive atmosphere glove boxes must permeate downstream to research and development labs as universities and startups expandaccess to capital equipment democratizing nanoscale explorations with high purity submicron spherical tungsten. By proactively developing staff expertise and codifying best practices embracing powder production hazards, manufacturers can responsibly develop this unique material’s potential.
Share On
MET3DP Technology Co., LTD is a leading provider of additive manufacturing solutions headquartered in Qingdao, China. Our company specializes in 3D printing equipment and high-performance metal powders for industrial applications.
Inquiry to get best price and customized Solution for your business!
Related Articles
About Met3DP
Recent Update
Our Product
CONTACT US
Any questions? Send us message now! We’ll serve your request with a whole team after receiving your message.
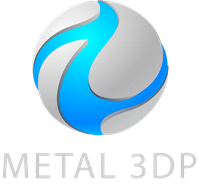
Metal Powders for 3D Printing and Additive Manufacturing