Stainless Steel 3D Printing Metal Powder
Table of Contents
Stainless steel. The name itself evokes images of strength, resilience, and a touch of modern elegance. It’s no surprise then that this wonder material has found its way into the cutting- edge world of 3D printing. But what exactly makes stainless steel 3D printing metal powder tick? Buckle up, because we’re about to embark on a journey into the heart of this transformative technology.
Specific Powders of Stainless Steel 3D Printing Metal Powder
Not all stainless steels are created equal, and the same goes for 3D printing metal powders. Here’s a closer look at some of the most popular players in the game:
Powder Type | Composition | Properties | Applications |
---|---|---|---|
316L | 16-18% Chromium, 10-14% Nickel, 2-3% Molybdenum | Excellent corrosion resistance, good weldability, high strength | Aerospace components, medical implants, chemical processing equipment, jewelry |
17-4PH | 17% Chromium, 4% Copper, < 0.05% Carbon | High strength, good ductility, excellent hardenability | Gears, shafts, clamps, surgical instruments |
304L | 18% Chromium, 8% Nickel | Good corrosion resistance, formability, affordability | Food processing equipment, architectural components, household appliances |
CL63 | 17% Chromium, 4.5% Nickel, 1.5% Copper, 0.25% Niobium | High strength, good ductility, improved corrosion resistance compared to 316L | Marine components, oil & gas equipment, heat exchangers |
254SMO | 19-21% Chromium, 5-7% Molybdenum, 4-6% Nickel | Exceptional resistance to pitting and crevice corrosion | Valves, pumps, pipelines used in harsh environments |
15-5PH | 15% Chromium, 5% Nickel | High strength, good toughness, age-hardenable | Molds, tools, springs, aerospace parts |
Custom Alloys | Tailored compositions | Properties designed for specific applications | High-performance parts requiring unique combinations of strength, corrosion resistance, and other properties |
This is just a taste of the stainless steel 3D printing metal powder buffet. Remember, the “secret sauce” lies in the specific ratios of elements that make up each powder. These ratios dictate the final properties of the printed part, allowing engineers to create components perfectly suited for their intended use.
Here’s a fun analogy to consider: Think of different types of stainless steel 3D printing metal powder like spice blends. Each blend (powder) has a unique combination of ingredients (elements) that create a distinct flavor profile (set of properties) for the final dish (printed part). Just like you wouldn’t use a fiery chili powder blend on your morning pancakes, you wouldn’t choose a low-corrosion resistance powder for a critical marine application.
Applications of Stainless Steel 3D Printing Metal Powder
The possibilities with stainless steel 3D printing metal powder are truly boundless. Here are just a few of the exciting ways it’s being used to revolutionize various industries:
- Aerospace: Lighter, stronger aircraft components with complex geometries are being created, leading to improved fuel efficiency and performance.
- Medical: Custom-designed implants and prosthetics are being printed to perfectly fit individual patients, leading to faster healing and improved quality of life.
- Chemical Processing: Highly resistant equipment is being 3D printed to handle harsh chemicals, ensuring safety and extending equipment lifespan.
- Consumer Goods: From intricate jewelry pieces to customized bicycle frames, stainless steel 3D printing metal powder is bringing innovation and personalization to everyday products.
As 3D printing technology continues to evolve, we can expect even more groundbreaking applications for stainless steel 3D printing metal powder to emerge. Imagine a world where critical automotive parts are printed on-demand, or personalized tools are created for artisans at the push of a button. The future is brimming with possibilities!
Characteristics of Stainless Steel 3D Printing Metal Powder
Stainless steel 3D printing metal powder isn’t your average beach sand. Here are some key characteristics that set it apart:
- Particle size and distribution: The size and distribution of the powder particles play a crucial role in the printing process. Consistent, fine particles ensure smooth operation and high-quality printed parts.
- Sphericity: Ideally, the powder particles should be as close to perfect spheres as possible. This enhances flowability, minimizes friction during printing, and leads to better packing density (how tightly the particles are packed together) in the powder bed. Think of it like trying to stack marbles versus oddly shaped pebbles – spheres simply pack together more efficiently.
- Flowability: Smooth, free-flowing powder is essential for consistent material delivery in the 3D printer. Imagine trying to pour chunky salsa versus a smooth liquid – flowability is all about ease of movement.
- Apparent density: This refers to the bulk density of the powder, considering both the solid particles and the air spaces between them. A high apparent density allows for more material to be packed into the printing bed, resulting in potentially stronger and more precise parts.
- Chemical composition: As mentioned earlier, the specific elements and their ratios in the powder dictate the final properties of the printed part. Tight control over the chemical composition ensures consistent performance and predictable results.
Here’s an interesting fact: The development of stainless steel 3D printing metal powder involved overcoming a significant challenge. Traditional stainless steel powders were often irregular in shape and didn’t flow well, making them unsuitable for 3D printing processes. Through advancements in powder manufacturing techniques like gas atomization, engineers were able to create the spherical and free-flowing powders we use today.
Different Types of Stainless Steel 3D Printed Metal Powder
We’ve already explored some of the most popular stainless steel 3D printing metal powder types, but let’s delve a little deeper. Here’s a breakdown of some key considerations when choosing a powder for your specific application:
- Corrosion resistance: Different stainless steel alloys offer varying degrees of corrosion resistance. If the printed part will be exposed to harsh environments (like saltwater or strong chemicals), a powder with high chromium and molybdenum content (like 316L or 254SMO) would be a wise choice.
- Strength: The need for strength will vary depending on the application. For high-stress components, powders like 17-4PH or custom high-strength alloys might be preferred.
- Ductility: Ductility refers to a material’s ability to deform under stress without breaking. If the printed part needs to be flexible or bendable, a powder with good ductility (like 304L) might be suitable.
- Weldability: If the printed part needs to be joined to other components, weldability becomes a factor. 316L is a popular choice due to its excellent weldability.
- Cost: Not all stainless steel 3D printing metal powders are created equal in terms of price. Factors like the specific alloy composition and powder manufacturing techniques can influence cost.
The key takeaway? Choosing the right stainless steel 3D printing metal powder requires carefully considering the desired properties for the final printed part. There’s no “one size fits all” solution, and understanding the strengths and limitations of each powder type is crucial for success.
Using Various 3D Printing Processes
Stainless steel 3D printing metal powder can be utilized in a variety of 3D printing processes, each with its own advantages and limitations. Here’s a quick overview of some of the most common methods:
- Selective Laser Melting (SLM): A high-powered laser beam selectively melts the powder particles layer by layer, building the 3D object. SLM offers excellent precision and detail but can be a slower and more expensive process.
- Electron Beam Melting (EBM): Similar to SLM, but uses an electron beam instead of a laser for melting. EBM can handle a wider range of materials, including reactive metals like titanium, but requires a vacuum environment, adding complexity.
- Binder Jetting (BJ): A liquid binder is jetted onto the powder bed, selectively gluing the particles together. BJ is a faster and more affordable process compared to SLM and EBM, but the printed parts typically require additional post-processing for full density and strength.
The choice of 3D printing process depends on factors like the desired level of detail, dimensional accuracy, material compatibility, and budget constraints. Evaluating these factors alongside the chosen stainless steel 3D printing metal powder is essential for achieving optimal results.
Let’s revisit our culinary analogy: Think of the 3D printing process as the cooking method. Just like you wouldn’t bake a cake in a deep fryer, the choice of 3D printing process needs to complement the properties of the stainless steel 3D printing metal powder you’ve selected.
Advantages and Limitations of Stainless Steel 3D Printing Metal Powder
Advantages:
- Design freedom: Stainless steel 3D printing metal powder enables the creation of complex geometries that are impossible or highly challenging with traditional manufacturing techniques. This opens doors for innovative designs and improved functionality.
- Lightweighting: 3D printing allows for the creation of intricate lattice structures within the printed part, reducing weight while maintaining strength. This is a game-changer for applications like aerospace and automotive where weight reduction is critical.
- Mass customization: The ability to produce parts on-demand with minimal setup times makes stainless steel 3D printing metal powder ideal for creating customized components or producing low-volume batches.
- Reduced waste: Compared to traditional subtractive manufacturing methods that generate significant scrap material, 3D printing with metal powder minimizes waste, making it a more sustainable option.
Limitations:
- Cost: While costs are steadily decreasing, stainless steel 3D printing metal powder and the 3D printing processes themselves can still be expensive compared to some traditional manufacturing techniques.
- Build size limitations: Current 3D printing technology has limitations on the size of parts that can be produced. However, advancements are being made to address this limitation.
- Surface finish: The surface finish of 3D printed metal parts can be rougher than those produced with traditional methods. Post-processing techniques like machining or polishing might be necessary to achieve a desired surface finish.
- Material limitations: While the range of available stainless steel 3D printing metal powders is expanding, it’s still not as vast as the options available for traditional manufacturing.
Finding the middle ground: Despite these limitations, the advantages of stainless steel 3D printing metal powder are undeniable. As technology continues to develop and costs come down, we can expect this revolutionary technology to become even more widely adopted across various industries.
Specifications, Sizes, Grades, Standards
Let’s delve into the technical specifications of stainless steel 3D printing metal powder. Understanding these details is essential for engineers and designers working with this material.
While there’s no single governing standard for stainless steel 3D printing metal powder, several industry associations and material suppliers have developed their own specifications. These specifications typically cover factors like:
- Powder particle size and distribution: As mentioned earlier, consistent particle size and distribution are crucial for optimal printing performance. Specifications might define acceptable ranges for particle size and the desired distribution profile.
- Chemical composition: The specific elements and their weight percentages are clearly defined to ensure consistent material properties in the printed parts.
- Flowability: Standards might specify minimum flowability values to guarantee smooth powder movement during the printing process.
- Apparent density: This value might be included to ensure sufficient packing density can be achieved in the powder bed.
Here’s a table summarizing some of the key specifications to consider:
Specification | Description |
---|---|
Particle size range | Typically between 15 and 100 microns |
Sphericity | As close to spherical as possible |
Flowability | Minimum flow rate to ensure smooth powder movement |
Apparent density | May vary depending on the specific powder type |
Chemical composition | Defined by weight percentages of elements (e.g., Chromium, Nickel, Molybdenum) |
In addition to specifications, factors like powder size and grade can also play a role.
- Powder size: The choice of powder size depends on the specific 3D printing process being used. For example, SLM typically works best with finer powders compared to Binder Jetting.
- Powder grade: Similar to other materials, stainless steel 3D printing metal powder can come in different grades. The grade might indicate the level of purity or the presence of additional elements for specific properties.
It’s important to consult with the material supplier and the 3D printing machine manufacturer to determine the optimal specifications, size, and grade of stainless steel 3D printing metal powder for your specific application.
Suppliers and Pricing of Stainless Steel 3D Printing Metal Powder
The market for stainless steel 3D printing metal powder is constantly evolving, with new suppliers emerging and established players expanding their offerings. Here’s a brief overview of some key considerations when sourcing stainless steel 3D printing metal powder:
- Reputation and experience: Choose a supplier with a proven track record in providing high-quality stainless steel 3D printing metal powder. Look for companies with experience catering to various industries and applications.
- Material variety: Consider the range of stainless steel powder types offered by the supplier. Having access to a wider selection allows for greater flexibility in choosing the right material for your needs.
- Technical expertise: A reputable supplier should have a team with strong technical expertise in stainless steel 3D printing metal powders. This ensures they can provide valuable advice and support throughout the selection process.
- Pricing and minimum order quantities: Pricing for stainless steel 3D printing metal powder can vary depending on the specific powder type, quantity ordered, and supplier. Be sure to inquire about minimum order quantities (MOQs) to ensure you can purchase the amount you need.
Here’s a table listing some prominent suppliers of stainless steel 3D printing metal powder (please note that this is not an exhaustive list and pricing information may vary):
Supplier | Location | Website |
---|---|---|
Metal3DP | China | https://met3dp.com/ |
Carpenter Additive | United States | https://www.carpentertechnology.com/additive-manufacturing |
APower | China | https://all3dp.com/2/powder-3d-printer-guide/ |
EOS GmbH | Germany | https://www.eos.info/en-us/about-us/locations-worldwide |
AM Powder | United Kingdom | http://ampowder.ch/ |
Pricing for stainless steel 3D printing metal powder can range from several tens of dollars per kilogram to hundreds of dollars per kilogram, depending on the specific powder type and quantity. It’s always best to contact potential suppliers directly for current pricing information and to discuss your specific needs.
FAQ
Q: What are the benefits of using stainless steel 3D printing metal powder over traditional manufacturing methods?
A: Stainless steel 3D printing metal powder offers several advantages, including design freedom, lightweighting, mass customization, and reduced waste.
Q: What are the limitations of using stainless steel 3D printing metal powder?
A: Current limitations include cost, build size limitations, surface finish requirements, and a limited range of materials compared to traditional manufacturing.
Q: What are some of the typical applications for stainless steel 3D printing metal powder?
A: Applications span various industries, including aerospace, medical, chemical processing, and consumer goods.
Q: How do I choose the right type of stainless steel 3D printing metal powder for my application?
A: Consider factors like desired properties (corrosion resistance, strength, ductility), compatibility with your chosen 3D printing process, and budget constraints. Consulting with a material supplier and 3D printing machine manufacturer is recommended.
The Future of Stainless Steel 3D Printing Metal Powder
The future of stainless steel 3D printing metal powder is bright. As technology advances, we can expect to see:
- Reduced costs: Making 3D printing metal powder more affordable will broaden its adoption across various industries.
- Expanded material range: The development of new and improved stainless steel alloys specifically designed for 3D printing will offer even more options for engineers and designers.
- Larger build sizes: Advancements in 3D printing technology will enable the creation of larger and more complex parts.
- Improved surface finishes: Techniques for achieving smoother surface finishes directly from the printing process will continue to evolve.
Stainless steel 3D printing metal powder is a powerful tool with the potential to revolutionize manufacturing. By understanding its properties, limitations, and various applications, you can harness its potential to create innovative and high-performance parts for the future.
Share On
MET3DP Technology Co., LTD is a leading provider of additive manufacturing solutions headquartered in Qingdao, China. Our company specializes in 3D printing equipment and high-performance metal powders for industrial applications.
Inquiry to get best price and customized Solution for your business!
Related Articles
About Met3DP
Recent Update
Our Product
CONTACT US
Any questions? Send us message now! We’ll serve your request with a whole team after receiving your message.
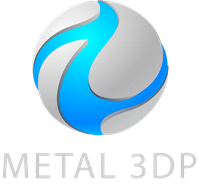
Metal Powders for 3D Printing and Additive Manufacturing