Titanium 3D Printing Powder
Table of Contents
titanium 3d printing powder is a strong, lightweight, and corrosion-resistant metal that is ideal for 3D printing complex and durable parts across aerospace, medical, automotive, and other industrial applications. This article provides a comprehensive overview of titanium powder metallurgy for additive manufacturing.
Overview of titanium 3d printing powder
Titanium is one of the most popular metals used in powder bed fusion and directed energy deposition 3D printing technologies. Some key advantages of 3D printed titanium parts include:
- High strength-to-weight ratio
- Withstands extreme temperatures and corrosion
- Biocompatible for medical implants
- Complex geometries not possible with casting or machining
- Reduced waste compared to subtractive methods
- Shorter lead times and costs compared to traditional titanium fabrication
However, titanium is reactive at high temperatures and requires inert chamber environments during printing using argon or nitrogen gases. The properties of 3D printed titanium depend on various factors:
Key Factors Influencing Titanium 3D Print Properties
Parameter | Description | Effect on Properties |
---|---|---|
Titanium alloy grade | Purity levels of titanium, aluminum, vanadium, etc. | Strength, hardness, ductility, corrosion resistance |
Powder size distribution | Range of fine to coarse powder particles | Density, surface finish, precision |
Layer thickness | Thinner layers improve resolution but increase print times | Accuracy, tolerances, surface roughness |
Energy source | Laser, electron beam, plasma arc | Localized melting, heating, cooling rates affect microstructure |
Print orientation | Vertical vs. horizontal structures | Anisotropic strength, may require supports |
Hot isostatic pressing | Post-process to eliminate pores | Significantly improves density, fatigue life |
With optimal parameters, 3D printed titanium parts meet or exceed wrought mill-product properties while enabling innovative designs not possible with subtractive methods.
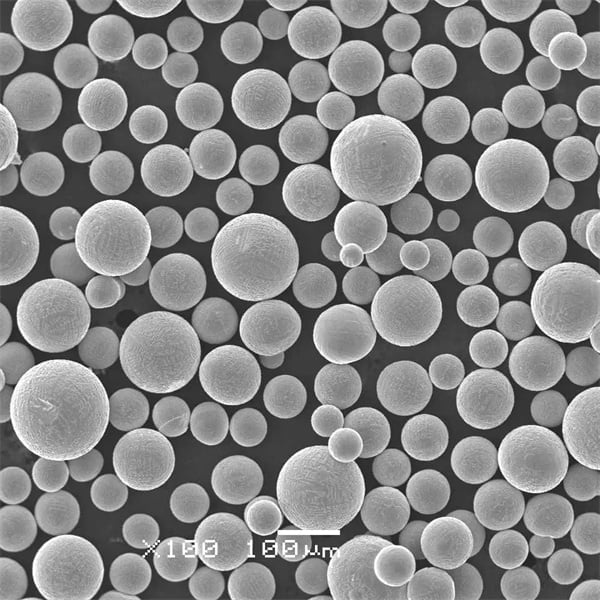
Types of titanium 3d printing powder for AM
Titanium alloys are available in various grades formulated for different additive manufacturing processes. The most common titanium powders are:
Common Titanium Powder Grades for 3D Printing
Alloy | Description | Applications |
---|---|---|
Ti-6Al-4V ELI | Extra-low interstitial version of workhorse Ti64 alloy | Aerospace components, biomechanical implants |
Ti 6Al-4V | Most popular grade, good strength and corrosion resistance | Automotive, marine hardware, sporting goods |
Ti-6Al-7Nb | Higher biocompatibility than Ti64 | Orthopedic and dental implants, surgical instruments |
CP-Ti Grade 2 | Commercially pure titanium, softer than alloys | Food/chemical process equipment |
Ti-555 | Aerospace grade with high strength | Aircraft structural components, rocket engines |
Ti-1023 | Exceptional fatigue and creep resistance | Turbine blades, landing gear, fasteners |
The particle size distribution is a key characteristic determining final density and surface finish. Finer powders around 10-45 microns flow and compact better, while coarser powders above 100 microns facilitate easier powder removal and reduce material costs.
Titanium Powder Specifications
Parameter | Typical Range |
---|---|
Particle size | 15-45 microns, up to 150 μm |
Flow rate | <15 s/50 g |
Apparent density | 2.1-3.0 g/cm3 |
Tap density | 3.2-4.1 g/cm3 |
Purity | >99.5% titanium |
Oxygen content | <0.20% |
Nitrogen content | <0.03% |
Hydrogen content | <0.015% |
Manufacturers continuously refine titanium powder production methods and alloy compositions to meet the growing demand for high-performance additively manufactured titanium components across industries.
How Titanium Powder is Made
Titanium metal powder has a higher surface area to volume ratio compared to solid forms like ingots or feedstock wire. There are several modern powder manufacturing techniques:
- Plasma Atomization – High velocity inert gas jets break up molten titanium streams into fine droplets that rapidly solidify into spherical powders with smooth surface morphology. This produces consistent particle sizes with few satellites.
- Gas Atomization – Similar to plasma atomization, lower gas pressures generate less fine powders suitable for EBM printing. Powders show some spatter with irregular shapes and satellites.
- Rotating Electrode Process – Bars or wires of titanium alloy are melted by arcs under inert atmosphere and centrifugal forces eject the metal which then solidifies into flattened spherical particles. Economical production of sponge-like powders.
- Hydride-Dehydride Process – Finely divided titanium hydride powder is decomposed in a vacuum, causing it to disintegrate into fine metallic titanium powder with higher oxygen impurity around 0.35-0.5%.
All methods require extensive powder sieving and separation to obtain specific size fractions appropriate for 3D printing technique, typically around 10-150 microns. Smooth spherical particles yield better packing density and flowability. Appropriate powder reconditioning, blending, and storage under inert atmosphere is critical before use.
Titanium Powder Manufacturers
Some of the major global suppliers of titanium printing powders include:
Company | Location | Products |
---|---|---|
AP&C | Canada | Ti-6Al-4V, Ti-6Al-4V ELI, Ti-6Al-7Nb, Custom alloys |
Carpenter Additive | USA | Ti-6Al-4V, Ti 6-4 ELI, Custom grades |
GKN Additive | Sweden | Ti-6Al-4V ELI, Ti-6Al-4V, Ti-64 grades |
LPW Technology | UK | Ti-6Al-4V, Ti-6Al-4V ELI, Blended alloys |
Praxair | USA | CP Ti grade 2, Ti-6Al-4V, Ti-6Al-4V ELI |
TLS Technik | Germany | Ti-6Al-4V, Ti-Al-Fe alloys |
These companies continuously improve production processes and quality standards to supply defect-free titanium powders customized for all major metal 3D printing machines.
Titanium Powder Costs
As a lightweight structural material, titanium metal powders are around 4-5 times more expensive than aluminum and 2-3 times costlier than common steels by weight. Prices vary by alloy grade, quality, lot size from a few kgs to a ton.
Alloy | Price Range per Kg |
---|---|
CP Ti Gr 2 | $50 – $150 |
Ti-6Al-4V | $80 – $450 |
Ti-6Al-4V ELI | $100 – $650 |
Ti 6Al-7Nb | $250 – $1000 |
Ti-555 | $150 – $850 |
Ti-1023 | $500 – $2000 |
Scrap titanium powder from 3D printing can be reused to offset material costs after testing for contamination and verifying properties. Overall part costs depend on build rates, labor, design complexity, and post-processing besides raw material expenses.
Applications of 3D Printed Titanium Parts
Thanks to its durability, biocompatibility and design freedom, metal 3D printing expands titanium use across diverse industries:
Aerospace – Aircraft and rocket engine components, airframes, helicopters, drones. Reduces part counts up to 90% vs assembled structures.
Medical and Dental – Orthopedic implants, prosthetics, fixations and instruments where high strength and bio-compatibility is vital. Enables customized designs matched to patient anatomy.
Automotive and Motorsports – Lightweighting parts like connecting rods, gear shifters, propeller shafts while exceeding safety requirements. Allows performance gains by topology optimization.
Industrial Equipment – Solid titanium impellers, valves, pipes, heat exchangers resistant to corrosion/erosion. Conformal cooling channels minimize tool wear during injection molding.
Consumer Goods – Customized sporting gear like bicycle frames, golf club heads, kayak paddles featuring integrated ergonomic titanium lattice structures.
3D printing unlocks new geometries in titanium not feasible with casting while supporting low volume production typical for specialized applications with accelerated lead times and life-cycle cost savings.
Metal 3D Printing Processes for Titanium
There are several additive manufacturing techniques suitable for titanium powder bed fusion:
Powder Bed Fusion Processes
Process | Description | Hardware Examples |
---|---|---|
DMLS | Direct metal laser sintering fuses powder using fiber laser | EOS M series |
SLM | Selective laser melting fully melts powder into dense parts | SLM Solutions |
EBM | Electron beam selectively melts powder in vacuum | Arcam A2X |
These powder bed processes involve spreading a thin layer of titanium powder, selectively melting it using a focused heat source, lowering the build plate, and repeating the process to build parts from bottom up. The inert gas chamber prevents oxidation at high temperatures. The melt pools rapidly solidify resulting in fine equiaxed titanium grains leading to isotopic properties similar to wrought products.
SLM and DMLS offer higher resolution and surface finishes while EBM features faster build rates for cheaper low-density prototypes. Hybrid multi-laser systems are lowering part costs and build times.
Directed Energy Deposition
DED processes like laser engineered net shaping (LENS) blow metal powder into a molten pool created by a focused laser or arc onto a substrate plate to deposit beads side by side. DED is ideal for large near-net shape parts which undergo final machining. Titanium alloys with higher strength, ductility, fracture toughness, and creep resistance can be fabricated by optimized LENS parameters.
Binder Jetting
Using inkjet print head technology, binder jetting selectively deposits a liquid binding agent onto a bed of titanium powder to form green compact parts layer-by-layer. Sintering at high temperatures achieves ~95% density while avoiding residual stresses during printing. Binder jetting is more suitable for smaller titanium components with moderate structural loads and properties below wrought materials.
Post-Processing of titanium 3d printing powder Parts
After the build process, titanium components may undergo several post-processing steps:
- Support structure removal via EDM wire cutting
- Stress-relieving heat treatment
- Hot Isostatic Pressing (HIP)
- Solution treating & aging
- Shot peening to induce compressive stresses
- Machining – turning, drilling, milling to meet tolerance requirements on critical mating surfaces
- Surface finishing – grinding, sand blasting, polishing, etching to smooth surfaces
- Cleaning and sterilization for medical parts
HIP treatment applies high pressure argon gas under vacuum using elevated temperature. This helps eliminate internal voids and microporosity thereby improving fatigue life by 5-10X for mission-critical aerospace components. However, HIP changes the as-printed microstructure.
Overall part costs increase due to extensive manual post-processing steps for quality-critical applications. Integrated, automated post-processing stations are emerging adjacent to metal printers along with quality standardization efforts across the AM value chain promising higher consistency and repeatability for end-use titanium components.
Properties of 3D Printed Titanium Alloys
Mechanical properties of commonly used titanium alloys depend on various factors like powder quality, layer thickness, laser parameters, build orientation, heat treatments, and HIP.
Ti-6Al-4V ELI Properties
Parameter | As printed | After HIP | Wrought Ti-6Al-4V ELI |
---|---|---|---|
Tensile strength | 1050 – 1250 MPa | ~980 MPa | 860 – 965 MPa |
Yield strength (0.2% offset) | 1000 – 1150 MPa | ~930 MPa | 795 – 880 MPa |
Elongation at break | 8 – 15% | 10 – 18% | 10 – 16% |
Modulus of elasticity | 100 – 114 GPa | 110 – 115 GPa | 110 – 114 GPa |
Fatigue strength (10^7 cycles) | 400 – 600 MPa | 500 – 800 MPa | 550 – 750 MPa |
Hardness | 34 – 44 HRC | 32 – 40 HRC | 33 – 37 HRC |
Ti-6Al-4V ELI shows comparable or better tensile strength and hardness than traditional wrought products while ductility and high-cycle fatigue approaches forged material properties after HIP.
Ti-6Al-7Nb Properties
Parameter | Typical As-Printed Values | Wrought |
---|---|---|
Tensile strength | 900 – 1300 MPa | 860 – 1100 MPa |
Yield strength (0.2% offset) | 800 – 1250 MPa | 795 – 965 MPa |
Elongation at break | 5 – 15 % | 8 – 20% |
Modulus of elasticity | 95 – 115 GPa | 100 – 115 GPa |
Hardness | ~334 HV | ~302 HV |
The niobium addition increases biocompatibility compared to vanadium while providing strength exceeding traditional Ti-6Al-4V implants. Optimized SLM parameters produce dense medical-grade Ti-6Al-7Nb structures rivaling wrought properties.
Design Guidelines and Limitations
To fully utilize the benefits of powder bed fusion, engineers should design parts specifically for additive manufacturing:
Optimal Design Practices
- Minimize unnecessary mass for weight savings using lattice structures
- Consolidate sub-assemblies into single components
- Incorporate organic shapes, contours unavailable in machining
- Embed convergent cooling channels not possible with castings
- Reinforce high stress regions with gyroid infill or texture
- Standardize interfaces, fittings, fixtures for modular assemblies
- Parameterize families of parts keeping critical features common
Design Limits
- Overhang angles above 60 degrees require supports
- Extreme aspect ratios over 5:1 risk collapse or deformation
- Minimum wall thickness ~0.8 mm, fine features > 0.4 mm
- Tight pockets may trap unsintered powder needing evacuation holes
- Avoid hollow cavities isolated from powder removal access
- Generous fillets needed to relieve residual stresses
- Post-machining essential for mating fits, seals, bearings
Upfront DfAM training for engineers combined with AM-experienced designers can prevent reworks due to lack of production-ready designs required for end-use metal printed parts.
Comparative Analysis
3D Printing vs Cast or Machined Titanium
Additive Manufacturing Pros
- Design freedom for lightweight structures
- Part count reduction via consolidation
- Customizedshapes matching field requirements
- Eliminate tools needed for casting dies or CNC
- Safer, sustainable process with less waste
- Shorter lead time for low volume batches
Cons
- Slower build rates than mass production
- Size limits imposed by smaller build chambers
- Higher cost per part in medium quantities
- Extensive support cleanup causing surface defects
- Post-processing lowers as-printed material properties
- Anisotropy leads to directional weaknesses
- Standards and qualifications still maturing
3D Printed Titanium vs Other Metals
Parameter | Titanium | Aluminum | Stainless Steel | Nickel Alloys |
---|---|---|---|---|
Strength | High | Medium | Medium | Very high |
Stiffness | Medium | Medium | High | High |
Density | Lightweight | Very light | Heavier | Heavier |
Cost | High | Low | Medium | High |
Life at temperature | Excellent | Fair | Better | Best |
Corrosion resistance | Excellent | Fair/Coatings | Best | Better |
Bio-compatibility | Excellent | Good | Fair | Poor |
Magnetic properties | No | No | Slightly magnetic | Magnetic |
Titanium stands out where high-temperature mechanical performance combines with design flexibility, low mass, and resilience to extremes. The expanded capabilities of AM helps overcome its traditional fabrication challenges of high buy-to-fly ratios and long lead times that limited applications earlier despite outstanding properties.
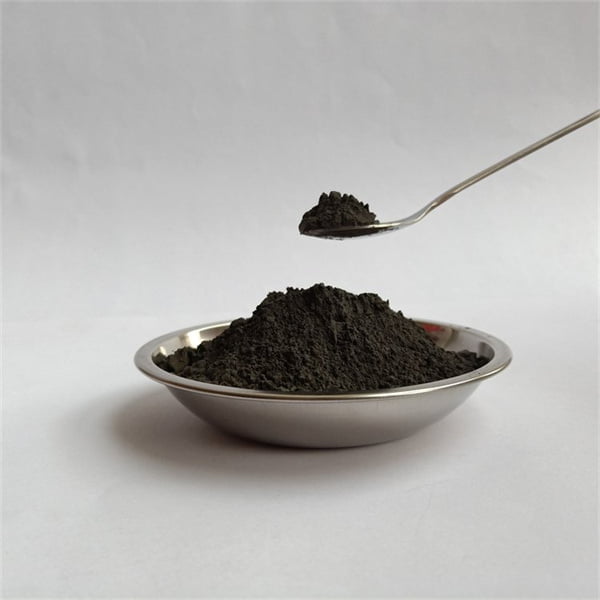
Industry Outlook and Future of Titanium AM
Additive is one of the fastest growing manufacturing segments withprinters getting bigger and faster using multiple lasers and robotic arms. Titanium parts are being qualified for series production across aviation, space, energy, motorsports, and medical sectors.
Some trends influencing titanium powder bed fusion adoption:
- Declining system costs improving affordability
- Automated post-processing driving repeatability
- Big area additive manufacturing (BAAM) techniques for large titanium structures
- New specialized alloys with superior creep and fatigue strength
- Simulation and AI for defect prediction, process optimization, quality assurance
- Hybrid printing combining additive, subtractive, inspection, automation
- Supply chain maturity ensuring material traceability and process standards
As titanium AM parts gain flight safety and medical certifications, 3D printing is poised to transform inventory-heavy industries like aerospace via distributed manufacturing models. Companies are collaborating across the value chain bringing innovative designs into mission-critical applications faster and at lower costs than ever feasible before.
Share On
MET3DP Technology Co., LTD is a leading provider of additive manufacturing solutions headquartered in Qingdao, China. Our company specializes in 3D printing equipment and high-performance metal powders for industrial applications.
Inquiry to get best price and customized Solution for your business!
Related Articles
About Met3DP
Recent Update
Our Product
CONTACT US
Any questions? Send us message now! We’ll serve your request with a whole team after receiving your message.