Titanium Alloy Powder: Properties, Production, and Applications
Table of Contents
Titanium alloy powders are advanced engineering materials valued for their high strength-to-weight ratio, corrosion resistance, and biocompatibility. This article provides an overview of titanium alloy powder metallurgy, manufacturing methods, compositions, mechanical properties, uses across industries, and supplier landscape.
Overview of Titanium Alloy Powder
Titanium alloy powder is composed of titanium mixed with other metallic elements like aluminum, vanadium, iron, and molybdenum. The powders are produced through gas atomization and other methods into fine spherical particles.
These advanced powders are used to manufacture high-performance components via powder metallurgy techniques like metal injection molding, additive manufacturing, and hot isostatic pressing. Parts made from titanium alloy powders exhibit superior mechanical properties compared to those made from unalloyed titanium.
The unique qualities of high strength, low density, corrosion resistance, and biocompatibility make titanium alloy powders suitable for aerospace, medical, automotive, chemical, and consumer applications.
Benefits of Titanium Alloy Powder:
- High strength-to-weight ratio
- Excellent corrosion resistance
- Bioinert and biocompatible
- Ability to tailor properties through compositions
- Net-shape manufacturability into components
- Cost savings through powder metallurgy
Challenges with Titanium Alloy Powder:
- High material cost
- Reactivity issues during handling and processing
- Limitations in achievable properties
- Requirement for controlled atmospheres
- Lower ductility than competing alloys
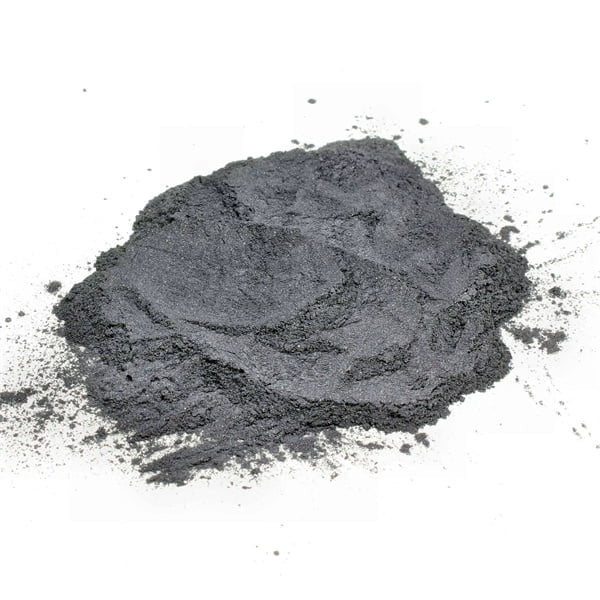
Compositions of Titanium Alloy Powder
Titanium alloys are classified into alpha, alpha-beta, and beta categories according to the microstructure they form after processing. The alloying elements, their concentrations, and thermo-mechanical treatments determine the microstructural phases.
Common alloying elements in titanium alloy powder:
- Aluminum (Al)
- Vanadium (V)
- Iron (Fe)
- Molybdenum (Mo)
- Tin (Sn)
- Zirconium (Zr)
- Niobium (Nb)
Effects of alloying elements:
- Aluminum (Al) – Improves strength and lowers density
- Vanadium (V) – Strengthens alpha and beta phases
- Iron (Fe) – Increases strength and ductility
- Molybdenum (Mo) – Strengthens alloy up to 500°C
- Tin (Sn) – Improves creep resistance
- Zirconium (Zr) – Grains refinement
- Niobium (Nb) – Prevents alpha case formation
Common titanium alloy powder compositions:
Alloy | Key Elements | Phases | Properties |
---|---|---|---|
Ti-6Al-4V (Grade 5) | Al: 6%, V: 4% | Alpha + beta | Excellent strength, moderate ductility, heat treatable, most widely used alloy |
Ti-6Al-7Nb | Al: 6%, Nb: 7% | Near alpha | High tensile strength, bioinert, used in medical implants |
Ti-10V-2Fe-3Al | V: 10%, Fe: 2%, Al: 3% | Beta | Highest strength titanium alloy, low ductility, difficult to machine |
Ti-13V-11Cr-3Al | V: 13%, Cr: 11%, Al: 3% | Alpha + beta | Excellent hot hardness and creep resistance up to 400°C |
Effects of composition on properties:
- Increasing Al content increases tensile strength and decreases density
- Addition of V, Mo, Cr improves high temperature strength
- Fe addition increases room temperature tensile strength
- Sn improves creep resistance of alloy
- Zr and Nb aid in grain structure control
Production Methods for Titanium Alloy Powder
Titanium alloy powder is manufactured through advanced methods that generate fine spherical powders from the molten alloys. The most common production techniques include gas atomization, plasma rotating electrode process (PREP), and plasma atomization.
Gas Atomization
- High-pressure inert gas jets disintegrate molten metal stream into fine droplets
- Generates powders between 10 microns to 250 microns
- Most widely used and economical method
- Powders have irregular shapes and contain satellites
Plasma Rotating Electrode Process (PREP)
- Spinning electrode disintegrates alloy using plasma torches
- Generates very spherical and smooth powders
- Excellent control over powder sizes and distribution
- Used for reactive and high-melting point alloys
Plasma Atomization
- Electric arc or plasma heats and atomizes alloy into droplets
- Produces highly spherical powders with good flowability
- Suitable for small batch production of fine powders below 63 microns
Secondary Processing
The as-atomized powders undergo secondary treatment to improve powder characteristics:
- Sieving into fine particle size distributions
- Conditioning to remove satellites and minimize agglomeration
- Blending elemental or master alloy powders to achieve target compositions
Handling Considerations
- Titanium alloy powders are pyrophoric (flammable) and require controlled environments with oxygen and moisture levels below 50 ppm during storage, processing, and handling. Argon is commonly used as the inert cover gas.
Mechanical Properties of Titanium Alloy Powder
Tensile Properties
Titanium alloys demonstrate higher tensile strength properties compared to unalloyed titanium, depending on their compositions and processing history.
Alloy | Ultimate Tensile Strength (MPa) | Yield Strength (MPa) | Elongation (%) |
---|---|---|---|
CP Titanium Grade 1 | 240-550 | 170-480 | 20-25 |
Ti-6Al-4V ELI Grade 23 | 860-965 | 795-875 | 10-15 |
Ti-6Al-7Nb Grade 26 | 900-1000 | 825-900 | 15-20 |
Ti-15V-3Al-3Cr-3Sn Grade 18 | 900-1000 | 800-900 | 8-14 |
Effects of Alloying Elements:
- Aluminum improves strength through solid solution strengthening
- Additions of V, Mo, Nb, Ta increase high temperature strength
- Iron enhances room temperature tensile strength
Fatigue and Fracture Properties
The fatigue strength and fracture toughness decrease with higher concentrations of beta stabilizers like molybdenum and vanadium. Thermomechanical treatments can be used to optimize combination of strength, ductility, fatigue, and fracture properties.
Industrial Applications of Titanium Alloy Powder
The excellent strength, corrosion resistance, hardness, and biocompatibility of titanium alloys make them suitable for critical applications across industries.
Aerospace Industry
- Aircraft hydraulic systems
- Spacecraft propellant tankage
- Airframe and landing gear components
- Engine parts like compressor blades, disks, and casings
Medical and Dental Industry
- Orthopedic implants like hip joints, bone plates, and screws
- Surgical instruments and bio-implants
- Orthodontic archwires
- Dental implants
Automotive Industry
- Connecting rods, intake valves, valve spring retainers
- Motorcycle and racing components
- Exhaust system parts
Chemical Industry
- Heat exchangers, condensers, and piping
- Process equipment for corrosion resistance
- Desalination and pollution control equipment
Consumer Industry
- Watches and jewelry
- Sports equipment like bicycle frames, golf clubs, lacrosse sticks
- Eyeglass frames, body piercings, and rings
Other Applications
- Marine – Propellers, sonar domes, desalination plants
- Power generation – Steam and gas turbine components
- Architecture – Decorative façade panels, handrails, roofs
The excellent strength-to-weight ratio also makes titanium alloys suitable to replace steel and aluminum components across all industries.
Specifications and Standards
Titanium alloy powders are produced according to ASTM standards that define the acceptable levels of oxygen, nitrogen, carbon, and iron for different grades.
Standard | Scope |
---|---|
ASTM B348 | Specification for titanium and titanium alloy bars and billets |
ASTM B939 | Test methods for titanium alloy powders |
ASTM F67 | Specification for unalloyed titanium bars for surgical implants |
ASTM F1472 | Specification for wrought titanium 6Al-4V ELI for surgical implants |
Suppliers of Titanium Alloy Powder
Titanium alloy powders are supplied by specialty metal powder producers that manufacture different grades tailored to industry applications.
Key titanium alloy powder manufacturers:
Company | Production Capacity | Alloys |
---|---|---|
AMETEK | 5,000 tons annually | Ti-6Al-4V, Ti-6Al-7Nb, Ti-13V-11Cr-3Al |
AP&C | 7,500 tons annually | Ti-6Al-4V, Ti-6Al-7Nb, Ti-555, Ti-1023 |
Tekna | 3,500 tons annually | Ti-6Al-4V ELI, Ti-6Al-7Nb |
Carpenter Technologies | 3,000 tons annually | Ti-6Al-4V, Ti-10V-2Fe-3Al |
Praxair | 4,000 tons annually | CP Ti, Ti-6Al-4V, Ti-6Al-7Nb |
Key titanium alloy powder distributors:
- Atlantic Equipment Engineers
- Micron Metals
- TLS Technik
- Global Titanium
Cost Analysis
Titanium alloy powders range between $$$/kg to $$$$/kg depending on composition, production method, shape, size distribution, quality, order volume, and geographical region.
Generally powders made through vacuum-based methods (plasma atomization, PREP) cost higher than inert gas atomized powders. Fine medical grade powders below 45 microns are more expensive.
Cost Saving Opportunities:
- Use less expensive Ti-6Al-4V instead of premium alloys
- Substitute titanium with stainless steel or aluminum alloys
- Employ additive manufacturing vs CNC machining
- Buy in bulk volumes to avail quantity discounts
Comparison Between Titanium Grades
Ti-6Al-4V vs. Ti-6Al-7Nb Alloys:
Property | Ti-6Al-4V | Ti-6Al-7Nb |
---|---|---|
Tensile strength | 895 MPa | 980 MPa |
Yield strength | 825 MPa | 900 MPa |
Density | 4.43 g/cc | 4.52 g/cc |
Bio-inertness | Moderate | High |
Cost | Lower | Higher |
Ti-6Al-4V vs. CP Titanium Grade 1:
- Ti-6Al-4V has 2X higher tensile and yield strengths
- CP Grade 1 offers better ductility – 25% elongation vs 10-15%
- Ti-6Al-4V is 45% stronger by weight than CP titanium
- CP titanium is more formable and easier to machine than the alloy
Gas vs. Plasma Atomization Methods:
Property | Gas Atomization | Plasma Atomization |
---|---|---|
Particle shape | Irregular with satellites | Highly spherical |
Oxygen pickup | Moderate | Lower oxygen levels |
Cost | Lower | Higher |
Productivity | Higher | Lower |
Processing Methods for Titanium Alloy Powder
The three main powder processing routes for manufacturing titanium components are:
Metal Injection Molding (MIM)
- High volume production of small, complex parts
- Combination of plastic injection molding and metal powder sintering
- Excellent dimensional accuracy and surface finishes
- Aerospace and medical applications
Additive Manufacturing (AM)
- Direct 3D printing of components from CAD data
- Design freedom for complex, lightweight geometries
- Titanium alloys like Ti-6Al-4V widely used
- Used across industries – medical, aerospace, automotive
Hot Isostatic Pressing (HIP)
- Consolidating encapsulated powders using heat and isostatic pressure
- Achieves high densities in complex shapes
- Low cost compared to machining solid metal
- Used for aircraft and medical components
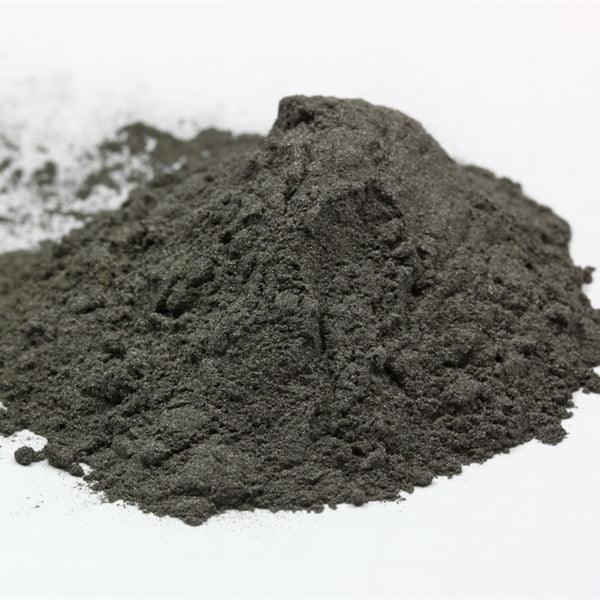
FAQs
What are the different grades of titanium alloy powder?
The most common titanium alloy grades include Ti-6Al-4V, Ti-6Al-7Nb, Ti-10V-2Fe-3Al, and Ti-13V-11Cr-3Al. The grade number indicates composition – for example, Ti-6Al-4V contains 6% aluminum and 4% vanadium.
Why is Ti-6Al-4V the most popular titanium alloy?
Ti-6Al-4V offers the best combination of light weight, corrosion resistance, ease of fabrication, and cost. It has excellent strength in alpha + beta condition and can be further heat treated. It accounts for over 50% of all titanium usage.
What particle sizes are available for titanium alloy powders?
Titanium alloy powders for additive manufacturing range from 15 to 45 microns. Finer powders below 25 microns allow higher resolution but are more expensive. For MIM applications, larger powder sizes between 45 to 250 microns are preferred.
What causes titanium powder to catch fire?
Titanium powders have high affinity for oxygen and can spontaneously ignite if exposed to air. The pyrophoric nature necessitates inert gas environments during handling, storage, and processing. Even moisture and oil residue can initiate fires.
Why is titanium alloy powder expensive?
Titanium alloy powder production involves complex vacuum melting processes under inert atmosphere which makes it costlier than steels and aluminum alloys. Also higher raw material costs, energy consumption, waste generation, and low powder reusability contribute to the high selling price.
What industries use titanium alloy powder?
The main application industries are aerospace, medical and dental, automotive, marine, sports equipment, and chemical processing due to the high strength, low weight, and corrosion resistance. The biocompatibility allows use in surgical implants and orthodontic wires.
Share On
MET3DP Technology Co., LTD is a leading provider of additive manufacturing solutions headquartered in Qingdao, China. Our company specializes in 3D printing equipment and high-performance metal powders for industrial applications.
Inquiry to get best price and customized Solution for your business!
Related Articles
About Met3DP
Recent Update
Our Product
CONTACT US
Any questions? Send us message now! We’ll serve your request with a whole team after receiving your message.
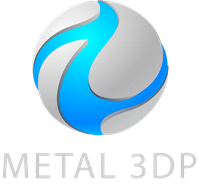
Metal Powders for 3D Printing and Additive Manufacturing