Titanium Powder Suppliers
Table of Contents
titanium powder is a versatile metal powder with unique properties that make it ideal for a wide range of applications across industries like aerospace, medical, automotive, and more. This article provides a comprehensive overview of titanium powder along with details on types, composition, properties, applications, specifications, pricing, pros and cons, and leading global suppliers.
Overview of titanium powder suppliers
Titanium powder is composed of titanium metal particles in powder form produced by various methods like gas atomization, plasma atomization, and hydride-dehydride process. The particles vary in size and shape based on production technique but generally range from 10 microns to 250 microns.
Titanium powder offers excellent strength-to-weight ratio, fatigue and corrosion resistance, biocompatibility, high melting point, and ability to withstand extreme temperatures. Key properties that make titanium powder suitable for high performance applications are summarized below:
Property | Description |
---|---|
High strength | Offers very good tensile and compressive strength for its weight. Stronger than aluminum. |
Lightweight | Almost half the density of steel and superalloys. Reduces component weight. |
Corrosion resistance | Forms protective oxide layer in air. Resists corrosion in harsh environments. |
Biocompatibility | Non-toxic and compatible with human body tissues and bones. |
High temperature | Melting point of 1668°C. Retains properties at high operating temps. |
Thermal properties | Low thermal conductivity. Good heat and thermal shock resistance. |
Non-magnetic | Useful where magnetic materials cause interference. |
The combination of these properties allow titanium powder to outperform competing materials like aluminum, magnesium, or steel alloys in the most demanding applications while still remaining cost-effective.
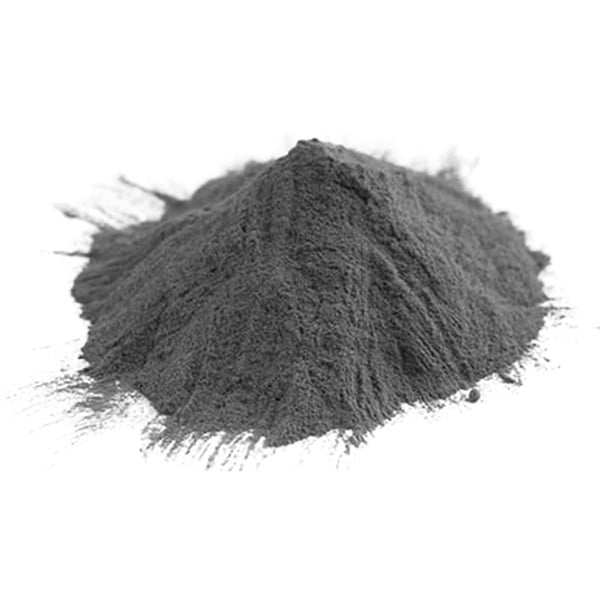
Types of Titanium Powder
Property | Description | Applications |
---|---|---|
Purity | Unalloyed Titanium (CP Ti): This type of titanium powder boasts a minimum titanium content of 99.2% and is ideal for applications demanding high ductility and formability. Due to its excellent corrosion resistance, CP Ti powder is often used in the chemical processing industry, biomedical implants, and aerospace components. Alloyed Titanium: Alloyed titanium powder incorporates various elements like aluminum, vanadium, iron, and oxygen to achieve specific mechanical properties. Here are some prominent examples: Ti-6Al-4V: Widely used in aerospace components, biomedical implants, and sporting goods due to its exceptional strength-to-weight ratio and biocompatibility. Ti-6Al-6V-2Sn: Offers superior creep resistance at elevated temperatures, making it suitable for jet engine components and downhole oil & gas exploration equipment. Ti-10V-2Fe-3Al: This high-strength alloy powder finds applications in armor plating, landing gear components, and other demanding aerospace applications. | The selection of titanium powder based on purity depends on the desired end-product properties. Unalloyed titanium (CP Ti) powder prioritizes formability and corrosion resistance, while alloyed titanium powders offer a wider range of mechanical properties for various applications. |
Particle Size & Distribution | The particle size and distribution of titanium powder significantly influence the final product’s characteristics. Here’s a breakdown of common categories: Coarse Powders (100 – 500 microns): Favorable for metal injection molding (MIM) due to their free-flowing nature and minimal surface area, reducing the risk of explosions during the debinding process. Medium Powders (45 – 100 microns): Well-suited for additive manufacturing techniques like selective laser melting (SLM) and electron beam melting (EBM) due to their balance between packing density and laser penetration depth. Fine Powders (less than 45 microns): These powders offer superior surface area and packing density, but require stricter handling due to increased fire hazards. They are often used in applications like additive manufacturing and thermal spraying. | Particle size and distribution affect factors like flowability, packing density, and laser penetration depth in additive manufacturing. Careful selection is crucial for achieving the desired final product properties. |
Manufacturing Process | The two primary methods for producing titanium powder are: Hydride-Dehydride (HDH) Process: This technique involves reacting titanium sponge with hydrogen to form titanium hydride powder. Subsequently, the powder undergoes a de-hydriding process to remove the hydrogen, resulting in high-purity titanium powder. Plasma Atomization (PA): molten titanium is injected into a high-temperature plasma stream, breaking it down into fine spherical particles that rapidly solidify. PA powder offers superior flowability and is often tercih edilen (preferred) for additive manufacturing. | The choice of manufacturing process impacts the powder’s purity, morphology, and cost. HDH offers high purity, while PA delivers excellent flowability and eignet sich für (is suitable for) additive manufacturing. |
Surface Morphology | The surface morphology of titanium powder refers to the shape and texture of the particles. Here are common variations: Spherical: This ideal morphology offers excellent packing density and flowability, making it advantageous for additive manufacturing processes. Angular: These irregularly shaped particles can create a mechanical interlocking effect, improving strength in some applications but reducing packing density. Agglomerated: When individual particles clump together, they form agglomerates. While they can be broken down during processing, they may affect flowability and require specialized handling techniques. | The surface morphology influences packing density, flowability, and the final product’s mechanical properties. Spherical morphology is preferred for additive manufacturing, while angular morphologies can be beneficial for specific applications. |
Composition and Properties
Titanium powder can be pure titanium or titanium alloys with other elements like aluminum, vanadium, iron, and molybdenum added. This affects the material properties and performance.
Titanium Powder Composition
Element | Composition Range |
---|---|
Titanium (Ti) | Balance |
Aluminum (Al) | 2% – 7% |
Vanadium (V) | 2% – 20% |
Iron (Fe) | 0.3% – 0.8% |
Oxygen (O) | 0.08% – 0.5% |
Carbon (C) | 0% – 0.15% |
Nitrogen (N) | 0% – 0.05% |
- Pure titanium offers the highest tensile strength and low weight.
- Aluminum stabilizes the alpha phase in titanium leading to increased strength.
- Vanadium strengthens titanium and reduces weight loss at high operating temps.
- Small amounts of iron impart ductility during metal working.
- Trace oxygen improves powder flow characteristics.
Effect of Composition on Properties
Property | Pure Titanium | Titanium Alloys |
---|---|---|
Density | Low | Higher than pure titanium |
Tensile strength | High | Very high |
Stiffness | Medium | High |
Ductility | High | Medium to high |
Operating temp | Up to 600°C | Up to 800°C |
Corrosion resistance | Excellent | Good |
Cost | Higher | Lower |
The right composition tailors the titanium powder properties like strength, temperature resistance, weight, ductility, and cost. Titanium alloys offer the best balance across critical performance parameters.
Applications of titanium powder
Industry | Application | Properties Leveraged | Benefits |
---|---|---|---|
Aerospace & Defense | – Aircraft landing gear components – Missile casings – Engine blades – Airframe structures | High strength-to-weight ratio, excellent fatigue resistance, superior corrosion resistance | – Lighter aircraft for increased fuel efficiency and range – Enhanced durability in harsh environments – Improved performance and maneuverability |
Automotive | – High-performance connecting rods – Lightweight suspension components – Exhaust system components | High strength, good ductility at elevated temperatures, good heat transfer properties | – Reduced weight for better fuel economy and handling – Increased power output – Improved resistance to high temperatures and corrosion |
Biomedical & Dental | – Hip and knee replacements – Dental implants – Cranioplasty plates – Maxillofacial prosthetics | Biocompatible, excellent osseointegration (ability to bond with bone), good corrosion resistance in the body | – Improved long-term functionality and biocompatibility of implants – Reduced risk of infection and rejection – Enhanced patient comfort and quality of life |
Consumer Goods | – High-end bicycles – Sporting goods (golf clubs, baseball bats) – Jewelry and watches | High strength-to-weight ratio, good aesthetics, corrosion resistance | – Lighter, stiffer equipment for improved performance – Durable and stylish products with a luxurious feel – Corrosion-resistant jewelry for everyday wear |
Additive Manufacturing | – Complex aerospace components – Medical implants with customized designs – Lightweight and porous structures for heat exchangers | Design flexibility, near-net shape capabilities, excellent mechanical properties | – Production of intricate parts with minimal material waste – Creation of personalized implants for optimal fit and function – Manufacturing of lightweight and efficient heat exchange components |
Emerging Applications | – Filtration media for chemical processes – Bioprinting of human tissues – Hydrogen storage | High corrosion resistance, biocompatibility, good hydrogen absorption properties | – Development of more efficient and sustainable chemical processes – Potential for creating functional human tissues for medical applications – Lightweight and safe storage of hydrogen fuel |
Specifications of Titanium Powder
Feature | Description | Units |
---|---|---|
Particle Size | The diameter of individual titanium powder particles. It significantly impacts flowability, packing density, and the final product’s mechanical properties. | Microns (µm) or mesh (a measure of particle size based on sieve openings) |
Particle Shape | The morphology of the powder particles. It can be spherical, irregular, angular, or dendritic. Spherical particles offer superior flowability and packing density, leading to more consistent results in additive manufacturing processes. | Visual Description (e.g., spherical, angular) |
Purity | The percentage of titanium metal present in the powder by weight. Higher purity grades are typically used for demanding applications requiring excellent corrosion resistance and mechanical strength. | Percentage (%) |
Apparent Density | The weight of titanium powder per unit volume when loosely poured into a container. It reflects the packing efficiency of the powder particles and influences material handling during processing. | Grams per cubic centimeter (g/cm³) |
Tap Density | The density of titanium powder achieved by mechanically tapping the container to minimize voids between particles. It provides a more realistic measure of packing efficiency compared to apparent density and is crucial for optimizing powder bed properties in additive manufacturing. | Grams per cubic centimeter (g/cm³) |
Flowability | The ease with which titanium powder flows under gravity. Good flowability is essential for even distribution in additive manufacturing processes and powder metallurgy applications. Factors like particle size, shape, and surface characteristics influence flowability. | Qualitative Description (e.g., excellent, poor) or Flow Rate (grams per second) |
Sintering Behavior | The ability of titanium powder particles to bond together during a high-temperature heating process (sintering) to form a solid structure. Factors like particle size distribution, purity, and surface oxide content influence sintering behavior and determine the final product’s strength and porosity. | Qualitative Description (e.g., good sinterability, poor sinterability) |
Surface Area | The total surface area of the powder particles per unit mass. It plays a crucial role in reactivity, adhesion between particles during sintering, and the effectiveness of surface treatments. Finer particles have a higher surface area. | Square meters per gram (m²/g) |
Chemical Composition | The elemental makeup of the titanium powder, including the presence of any alloying elements or impurities. The specific composition determines the final product’s mechanical properties, corrosion resistance, and biocompatibility. | Percentage (%) of each element |
Moisture Content | The amount of water vapor adsorbed on the surface of the powder particles. Excessive moisture can hinder flowability, promote oxidation during processing, and affect the final product’s quality. | Percentage (%) |
Oxygen Content | The amount of oxygen present in the powder, typically as titanium oxide (TiO2) on the particle surface. Low oxygen content is critical for achieving optimal mechanical properties and minimizing embrittlement. | Percentage (%) |
Global titanium powder suppliers
Titanium powder production involves specialized equipment and processes necessitating dedicated metal powder producers across geographies. The complex methods also lead to significant quality variations across manufacturers.
The top global titanium powder suppliers known for capacity, quality, costs, and industry expertise are given below:
Leading Titanium Powder Companies
Company | Country | Production Capacity |
---|---|---|
ATI Powder Metals | USA | 5400 tons per year |
Tekna | Canada | 2000 tons per year |
TLS Technik | Germany | 4800 tons per year |
AP&C | Canada | 7000 tons per year |
CRISTAL | France | 8000 tons per year |
OSAKA Titanium | Japan | 4500 tons per year |
These prominent manufacturers have the latest atomization technologies, stringent quality control infrastructure, and decades of powder metals expertise geared towards high end applications. They can customize titanium powder compositions and properties working closely with clients.
Besides these large producers, many smaller regional titanium powder suppliers also exist catering to local markets across Americas, Asia Pacific, and EMEA regions. However quality, consistency and performance parameters may show more variability.
titanium powder Pricing
- Titanium powder is more expensive than competing metal powders like aluminum, iron, nickel etc. owing to complex manufacturing and raw material costs. Prices depend on:
Determining Cost Factors
Factor | Description |
---|---|
Purity | Increases exponentially above 98% titanium content |
Particle size | Ultrafine below 10 microns is costlier |
Order volume | Large bulk orders get discounted rates |
Alloying elements | Each addition increases pricing |
Region | US and Europe command premium over Asia |
- For example spherical Ti-6Al-4V ELI powder with -45 micron size for medical application can cost $100+ per kg compared to $20 per kg for stainless steel powder.
- However titanium becomes cost competitive when lifecycle costs like fuel savings, reduced maintenance etc. are considered against alternative materials.
Titanium Powder Price Ranges
Application | Price per kg |
---|---|
Aerospace | $70 – $150 |
Medical | $80 – $250 |
Automotive | $50 – $100 |
Additive manufacturing | $100 – $300 |
Other | $40 – $120 |
Pricing also varies across manufacturers based on quality, production technology, testing standards and batch traceability followed. Selecting the right supplier that balances price, performance and consistency is key to maintaining part quality and costs.
How to Select Titanium Powder Suppliers
Choosing titanium powder suppliers entails evaluating several parameters across quality, consistency, pricing and service to find the optimal balance for the application.
Key Selection Criteria
Parameter | Checks |
---|---|
Powder specification | Size distribution, morphology, flow rate etc. as per application standards |
Composition | Alloy grade, % titanium, impurities etc. match component design |
Consistent properties | Multiple batch testing data for particle size, density, morphology etc. |
Quality certifications | ISO 9001, AS 9100, ISO 13485 based on end use |
Testing capabilities | In-house lab for comprehensive physical and chemical testing |
Control standards | Traceability for complete production history and parameters |
Post-sales service | Technical support for powder handling, storage, defects etc. |
Pricing | Quoted rate analysis including surcharges, minimums etc. |
Delivery | Lead time, shipment lots and logistics reliability |
- Samples should be procured to conduct trial runs simulating real component manufacturing.
- Site audits of production facilities is highly recommended for strict aerospace & medical applications.
This comprehensive evaluation helps determine if the titanium powder producer has the experience, expertise and infrastructure to deliver the right powder quality over long production cycles demanded by end applications.
Pros and Cons of Titanium Powder
Pros | Cons |
---|---|
Exceptional Strength-to-Weight Ratio: Titanium powder boasts an unmatched ability to deliver exceptional strength while maintaining a remarkably low weight. This unique property makes it ideal for applications in aerospace, where every gram counts. Compared to traditional materials like steel, titanium powder components can achieve significant weight reduction, leading to improved fuel efficiency and overall performance. | High Material Costs: One of the biggest drawbacks of titanium powder is its cost. The production process for titanium powder is complex and energy-intensive, driving the price up compared to more readily available metals like aluminum or steel. This can be a significant hurdle for projects with tight budgets. |
Superior Corrosion Resistance: Titanium is renowned for its exceptional resistance to corrosion, making it a perfect choice for components exposed to harsh environments. Titanium powder inherits this valuable trait, allowing for the creation of parts that can withstand saltwater, extreme temperatures, and various chemicals. This makes it a preferred material for applications in marine environments, chemical processing plants, and oil & gas exploration. | Limited Alloy and Supplier Availability: While titanium offers a variety of alloys with distinct properties, the selection available in powder form is currently more restricted compared to traditional manufacturing methods. Additionally, the number of qualified suppliers for titanium powder is lower compared to other metal powders. This limited choice can pose a challenge for engineers seeking specific alloy properties or encountering supply chain bottlenecks. |
Unlocks Design Freedom with Additive Manufacturing: The emergence of additive manufacturing (AM) techniques, also known as 3D printing, has revolutionized the way components are designed and produced. Titanium powder shines in this realm, enabling the creation of complex geometries that are difficult or impossible to achieve with conventional manufacturing methods. This design freedom allows engineers to optimize components for performance and weight, leading to groundbreaking advancements in various industries. | Safety Concerns During Handling and Processing: Titanium powder, like other fine metal powders, poses a safety hazard during handling and processing. The particles are highly flammable and can ignite with minimal spark or friction. Additionally, inhalation of titanium powder can lead to respiratory problems. Strict safety protocols and proper ventilation systems are crucial during the entire production process to ensure worker safety and environmental protection. |
Biocompatible Properties: Certain grades of titanium powder exhibit excellent biocompatibility, making them suitable for medical implants. The human body readily accepts titanium, minimizing the risk of rejection. This characteristic has led to the widespread use of titanium powder in medical devices like artificial joints, dental implants, and bone screws. | Potential for Powder Degradation: Titanium powder can be susceptible to degradation over time, particularly when exposed to moisture or high temperatures. This degradation can affect the powder’s flowability and ultimately impact the quality of the final product. Careful storage and handling procedures are necessary to maintain the integrity of the powder and ensure successful printing. |
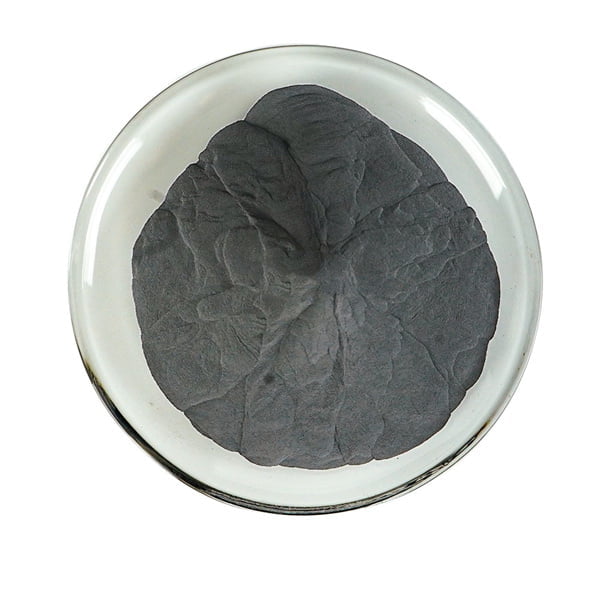
FAQs
Q. What are the different manufacturing methods for titanium powder?
Titanium powder can be produced via gas atomization, plasma atomization, or hydride-dehydride process. Gas atomized powder offers the most spherical morphology preferred for additive manufacturing whereas plasma atomized powder achieves finer sizes.
Q. What particle size is typically used for 3D printing applications?
For most binder-jet and laser powder bed fusion 3D printing, titanium powder between 10 to 45 microns with narrow distribution is recommended by most printer manufacturers to achieve good powder flow and spreadability along with layered fusion.
Q. Which industries use titanium powder for components?
Titanium is used to make high performance components via metal injection molding, hot isostatic pressing, additive manufacturing etc. across aerospace, medical technology, automotive, chemicals, oil and gas, sports equipment, and general engineering.
Q. Does titanium powder require special storage or handling precautions?
Titanium reacts easily with air moisture and oils. So it must be stored in sealed containers under inert argon or nitrogen atmosphere with controlled humidity levels to prevent contamination issues leading to poor material properties.
Q. Where can I find titanium powder suppliers in my country?
The major global titanium powder producers have local sales offices and distributors across most regions in the Americas, Europe and Asia-Pacific. They can guide buyers find the closest supply points for small to large quantities based on application requirements and shipping costs optimization.
Share On
MET3DP Technology Co., LTD is a leading provider of additive manufacturing solutions headquartered in Qingdao, China. Our company specializes in 3D printing equipment and high-performance metal powders for industrial applications.
Inquiry to get best price and customized Solution for your business!
Related Articles
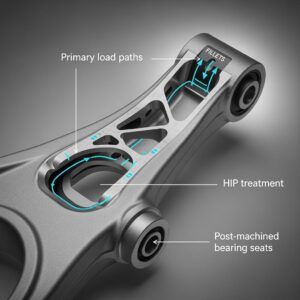
Metal 3D Printing for U.S. Automotive Lightweight Structural Brackets and Suspension Components
Read More »About Met3DP
Recent Update
Our Product
CONTACT US
Any questions? Send us message now! We’ll serve your request with a whole team after receiving your message.