15n20 Steel Powder: Properties, Production and Applications
Table of Contents
Overview of 15n20 Steel Powder
15n20 steel powder is an iron-based alloy powder containing nickel, chromium, molybdenum, and carbon. It features high strength, hardness, wear resistance, and corrosion resistance along with good dimensional stability during sintering.
Key properties and characteristics of 15n20 steel powder include:
Composition
- Iron (Fe) balance
- Chromium (Cr) 3-5 wt%
- Nickel (Ni) 1%
- Molybdenum (Mo) 0.3-0.6%
- Carbon (C) 0.2% max
Properties
- Density: 7.7-7.9 g/cm3
- Compressibility: Good
- Green strength: High
- Sintered strength: Very high
- Hardness: High
- Wear resistance: Excellent
- Corrosion resistance: Very good
- Maximum service temperature: ~500°C
Characteristics
- Shape: Irregular, angular
- Size range: 10-150 μm
- Flowability: Medium
- Compactability: High
- Sinterability: Good to 1350°C
- Machinability: Moderate
15n20 steel is valued for its ability to attain high strength levels up to and exceeding 1,000 MPa while preserving reasonable ductility after sintering. Parts can be heat treated for enhanced mechanical performance.
The nickel addition boosts hardenability and impact properties while the chromium and molybdenum increase strength through solid solution and precipitation strengthening. The composition is designed specifically for press and sinter powder metallurgy applications requiring a robust material.
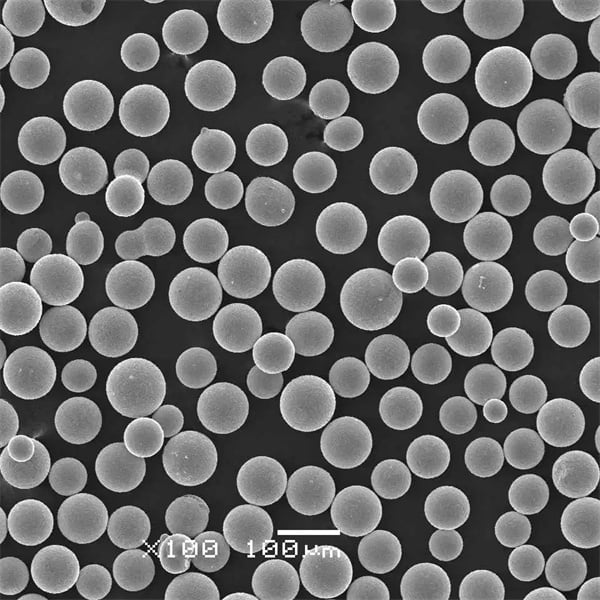
Production Methods for 15n20 Steel Powder
15n20 steel powder can be produced through the following methods:
Water Atomization
Molten steel alloy is disintegrated by high-pressure water jets into fine droplets that solidify into irregular powders with a large surface area ideal for rapid sintering. This is the most common and economic production route. Water atomized powders feature good flow and compaction properties preferred for automatic pressing.
Gas Atomization
Inert gas jets break up the molten stream into small particles with spherical morphology and very high purity. The process is slower and more expensive but necessary for more advanced PM parts. Gas atomized powders have excellent flow and packing characteristics sought for complex component shapes and thin sections.
Electrolysis
The composition is electrodeposited onto a cathode substrate and removed by mechanical methods to yield flaky powders. Though the chemistry is controlled precisely, electrolytic powders can suffer from high oxygen levels requiring annealing treatments prior to pressing. The irregular shape impacts density but allows binderless pressing.
Mechanical Alloying
Elemental metal powders are blended and subjected to intense mechanical working action in a ball mill with process control agent. Mechanical alloying produces homogeneous compositional mixes unavailable by conventional ingot metallurgy. However the composite particles may still require thermal processing before use in PM.
Applications and Uses of 15n20 Steel Powder
15n20 steel powder is specifically designed for powder metallurgy structural parts production via compacting and sintering.
Typical applications for sintered 15n20 steel components include:
- Automotive – Gears, sprockets, connecting rods, wrist pins, rocker arms
- Consumer – Knives, scissors, razor blades, padlocks
- Industrial – Bearings, bushings, seal rings, valve seats, wear strips
- Military – Gun components, missile and ordinance parts
- Oil & Gas – Well completion tools, perforating guns, downhole valves
The material offers an excellent combination of properties – strength, hardness, wear performance, thermal resistance – necessary across this range of critical applications. The chromium, molybdenum, and nickel in 15n20 steel also provide substantial corrosion resistance in different environments.
Many parts are heat treated (carburizing, carbonitriding, induction hardening) after sintering for localized hardness optimization depending on end-use stresses and demands. High production rates at lower costs compared to cast or forged equivalents makes 15n20 a popular powder metallurgy alloy.
Specifications of 15n20 Steel Powder
15n20 steel powder conforms to various classifications and its chemical composition is governed by international specifications:
Classifications
- High speed steel
- P/M structural steel
- Chromium-nickel molybdenum steel
Standards
- ISO 4491 15n20
- JIS SUS 15n20
- ASTM A331 15n20
- DIN 1.2702
Composition Specs
Element | Weight % |
---|---|
Iron (Fe) | Balance |
Chromium (Cr) | 3.00-5.00 |
Nickel (Ni) | 1.00 max |
Molybdenum (Mo) | 0.30-0.60 |
Carbon (C) | 0.20 max |
Manganese (Mn) | 0.10 max |
Silicon (Si) | 0.10 max |
Sulfur (S) | 0.10 max |
Phosphorus (P) | 0.10 max |
Size Range
Mesh | Microns |
---|---|
140 – 325 | 45 – 105 |
Powders for pressing are normally finer than 45 microns. Coarser particles 125+ microns can be used for metal injection molding of sintered components. Tighter size distributions result in better compaction density.
Suppliers of 15n20 Steel Powder
Many of the world’s top powder manufacturers and metal powder suppliers produce 15n20 steel powder including:
- Höganäs (Sweden)
- Rio Tinto Metal Powders (USA)
- JFE Steel (Japan)
- CNPC Powder (China)
- Sandvik Osprey (UK)
- AMETEK (USA)
- Carpenter Powder Products (USA)
Pricing
15n20 steel powder is sold by unit weight, typically in 25-500 kg bags or drums. Pricing varies by:
- Purity level
- Production method
- Size range and distribution
- Purchase quantity and bulk order discounts
Quantity | Price Range |
---|---|
1-10 kg | $15-25 per kg |
10-100 kg | $12-18 per kg |
>100 kg | $8-15 per kg |
Prices depend strongly on market dynamics between supply-demand and raw material input costs. Contact vendors directly for latest quote based on your annual volume and purity requirements.
Comparison Between 15n20 Steel Powder Products
Key variables when selecting 15n20 powder suppliers:
Production Method
- Water atomization provides the best balance of cost and properties
- Gas atomized and electrolytic powders used where purity is critical
- Mechanical alloyed powders offer customized compositions
Powder Morphology
- Irregular, angular powders improve green strength
- Rounded, spherical powders enhance flow and packing
Powder Size Range
- Ultrafine <20 microns for micro-components
- Sub 45 microns standard for pressing
- Larger particles >100 microns suitable for metal injection molding
Purity Standards
- Less oxygen preferred
- Lower N and S for high performance
- Strict control of light elements
Always evaluate composition certification, manufacturing control standards, testing protocols, and quality procedures before purchasing.
Advantages and Limitations of 15n20 Steel Powder
Advantages
- High strength after sintering – up to 1200 MPa
- Excellent wear properties and wear resistance
- Very good toughness
- Corrosion resistant especially in hot work environments
- Stable dimensions during liquid phase sintering
- Lower cost than many tool steels and stainless grades
- Sinter at lower temperatures to retain fine carbides
Limitations
- Lower strength after full dense heat treatment compared to forged equivalents
- Not recommended for low stress applications – shallow hardenability
- Susceptible to grain coarsening above 1250°C
- Difficult to machine intricate features due to hardness
- Large parts slower to densify – shrinkage variation
- Expensive gas atomized and electrolytic powders
For maximum benefits, engineers must design parts factoring in performance parameters of P/M 15n20 steel considering both capabilities and constraints.
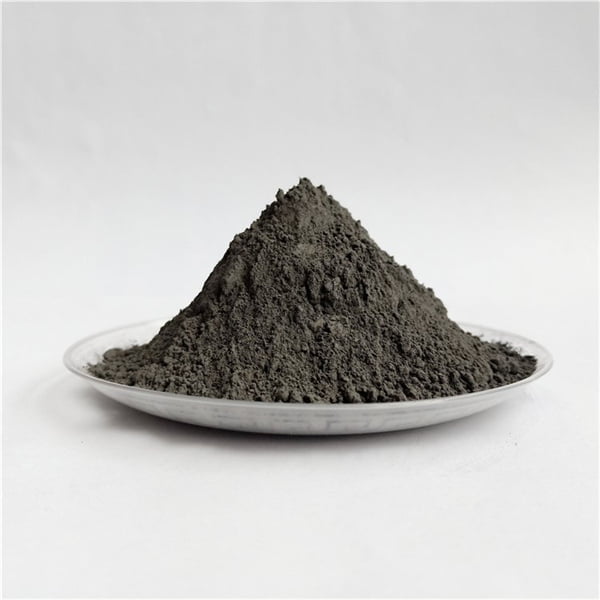
FAQs
What is 15n20 steel?
15n20 steel is a chromium-nickel-molybdenum low alloy powder metallurgy steel exhibiting high strength, hardness, wear properties, and moderate corrosion resistance after sintering and/or secondary heat treatment.
What is 15N20 steel powder?
15N20 is a high-carbon, nickel-bearing steel often used in the production of Damascus and pattern-welded blades. 15N20 steel powder is a finely ground form of this steel that is commonly used in powder metallurgy processes for manufacturing blades and other metal products.
What are the main properties of 15N20 steel?
15N20 steel is known for its high carbon content (approximately 0.75-0.85%), nickel alloying, and good edge retention. It is also known for its ability to create intricate patterns when forged in combination with other steels.
How is 15N20 steel powder produced?
15N20 steel powder is typically produced using a process called atomization or gas atomization. In this process, molten 15N20 steel is sprayed through a nozzle and rapidly cooled with a high-pressure gas, resulting in fine powder particles.
What are the applications of 15N20 steel powder?
15N20 steel powder is primarily used in the production of Damascus and pattern-welded blades. It can also be used in other applications where high carbon content and good edge retention are desired, such as knife making, swordsmithing, and blacksmithing.
Share On
MET3DP Technology Co., LTD is a leading provider of additive manufacturing solutions headquartered in Qingdao, China. Our company specializes in 3D printing equipment and high-performance metal powders for industrial applications.
Inquiry to get best price and customized Solution for your business!
Related Articles
About Met3DP
Recent Update
Our Product
CONTACT US
Any questions? Send us message now! We’ll serve your request with a whole team after receiving your message.