The Advantages of Water Atomization for 3D Printing Metal Powder
Table of Contents
Unleashing the Potential of 3D Printing Metal Powder
Imagine crafting intricate objects not from clay or wood, but from the very essence of strength and durability – metal. This futuristic vision is becoming a reality thanks to 3D Printing Metal Powder technology. However, creating the fine, flowable powder needed for this transformative process requires a specific technique: water atomization.
This article delves into the world of water atomization, exploring its advantages and unique capabilities in crafting the building blocks of 3D printed metal marvels.
Cost-effectiveness of Water Atomization: A Winning Formula
3D Printing Metal Powder is known for its precision and versatility, but concerns surrounding cost often arise. Thankfully, water atomization enters the scene as a cost-effective solution.
Here’s why:
- Readily available resources: Water, the primary element in this process, is readily available and significantly less expensive compared to the inert gases used in alternative atomization methods like gas atomization.
- Simplified process: Water atomization relies on a streamlined setup, requiring less complex equipment and energy consumption compared to other methods.
- High production rates: This technique boasts impressive production efficiency, translating to a higher output of metal powder per unit cost.
This cost advantage plays a crucial role in making 3D Printing Metal Powder technology more accessible and scalable, paving the way for wider adoption across various industries.
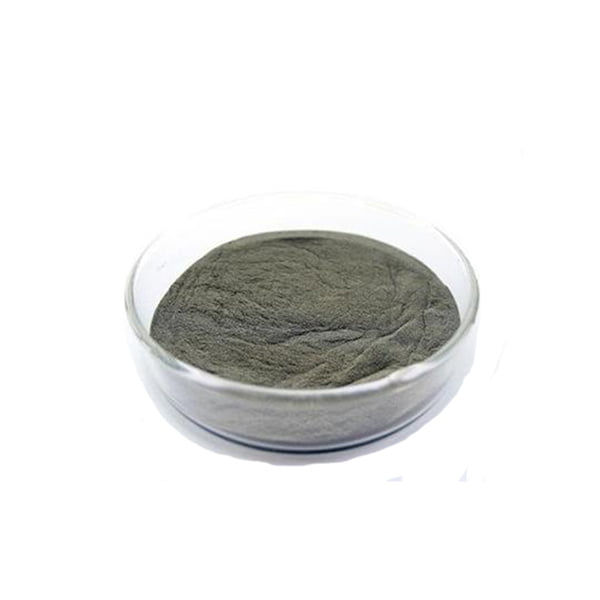
Suitable for a Variety of Metals: Unlocking Diverse Applications
The beauty of water atomization lies in its versatility. Unlike some techniques limited to specific metals, water atomization caters to a diverse range of metal types, including:
Metal Type | Description |
---|---|
Low-alloy steel | The workhorse of the metal world, known for its affordability and strength. |
Stainless steel | Renowned for its corrosion resistance, making it ideal for applications demanding hygiene and durability. |
Nickel-based superalloys | Exhibit exceptional high-temperature strength, perfect for aerospace and energy sectors. |
Titanium alloys | Boast a phenomenal strength-to-weight ratio, making them ideal for applications demanding lightweight yet robust structures. |
Copper and copper alloys | Offer excellent electrical conductivity, finding use in electronics and heat exchange applications. |
Aluminum and aluminum alloys | Lightweight and corrosion-resistant, making them suitable for aerospace and automotive industries. |
Cobalt-chromium alloys | Biocompatible and wear-resistant, ideal for medical implants and prosthetics. |
Tool steels | Possess exceptional hardness and wear resistance, perfect for cutting tools and dies. |
Tungsten and tungsten alloys | Extremely dense and have high melting points, used in applications requiring high-temperature resistance and radiation shielding. |
Precious metals (gold, silver, etc.) | Can be atomized for specialized applications like jewelry and electronics. |
This diverse compatibility opens doors to a widening range of applications in industries like:
- Aerospace: From lightweight aircraft components to high-temperature engine parts.
- Automotive: Creating lightweight and fuel-efficient car parts.
- Medical: Crafting customized implants and prosthetics.
- Consumer goods: Producing personalized jewelry and high-performance sporting equipment.
The ability to utilize a variety of metals through water atomization empowers innovation and unlocks new possibilities in diverse fields.
Tailored to Perfection: Achieving Desired Powder Properties
Not all metal powders are created equal. Water atomization offers the ability to fine-tune the properties of the powder to suit specific needs.
Factors influencing powder properties:
- Water pressure: Higher pressure leads to finer and more spherical powder particles.
- Metal composition: Different metals possess varying melting points and flow characteristics, impacting the atomization process.
- Cooling rate: Rapid cooling results in finer and more spherical particles, affecting the powder’s flowability and packing density.
By optimizing these parameters, manufacturers can achieve desired powder characteristics, such as:
- Particle size and distribution: Crucial for ensuring smooth and consistent 3D printing processes.
- Sphericity: Spherical particles offer better flowability and packing density, leading to improved printing quality.
- Porosity: The presence of pores can influence the final properties of the printed metal object.
This level of control and tailoring allows for the creation of high-quality metal powders, leading to superior results in the 3D Printing Metal Powder process.
Beyond Cost and Versatility: Unveiling Additional Advantages
While cost-effectiveness and broad metal compatibility are key strengths, water atomization offers additional benefits:
- Environmentally friendly: Compared to gas atomization, which utilizes inert gases that can contribute to greenhouse gas emissions, water atomization uses readily available and eco-friendly water as the atomization medium. Additionally, advancements in water recycling systems minimize water waste, further reducing environmental impact.
- Scalability: The simplicity and efficiency of the water atomization process make it scalable. This allows for the production of large quantities of metal powder to meet the growing demand for 3D printed metal components.
- Safety: While safety precautions are crucial in any industrial process, water atomization generally presents fewer safety concerns compared to techniques involving flammable or explosive materials.
These additional advantages solidify water atomization as a reliable and sustainable solution for 3D printing metal powder production.
Specifications, Sizes, Grades, and Standards
Understanding the specific specifications, sizes, grades, and standards of water-atomized metal powders is essential for selecting the most suitable material for a particular 3D printing application.
Key specifications typically considered:
- Chemical composition: The specific elements and their weight percentages present in the powder.
- Particle size and distribution: Measured in micrometers (μm), it affects flowability and packing density.
- Sphericity: The degree to which particles resemble perfect spheres, impacting flowability and printability.
- Flowability: The ease with which powder flows, crucial for consistent and efficient printing.
- Apparent density: The bulk density of the powder, influencing the final product’s density.
Commonly available sizes and grades:
- Particle size: Ranges from 10 to 150 μm, with specific size ranges chosen based on the desired printed features and 3D printing technology.
- Grades: Varying grades are offered based on chemical composition and purity, catering to diverse application requirements.
Standards:
Several international standards govern the production and properties of water-atomized metal powders, including:
- ASTM International (ASTM): Sets standards for various materials, including metal powders.
- International Organization for Standardization (ISO): Develops and publishes international standards for a wide range of products and services, including metal powders.
- Additive Manufacturing Standards Organization (AMSO): Focuses on developing standards specifically for additive manufacturing, including metal powder specifications.
By consulting these specifications, sizes, grades, and standards, users can ensure they select the optimal water-atomized metal powder for their specific 3D printing needs.
Suppliers and Pricing
The availability and pricing of water-atomized metal powders vary depending on the specific metal type, desired specifications, and market dynamics. Here’s a general overview:
Metal Type | Typical Price Range (USD/kg) |
---|---|
Low-alloy steel | $2 – $5 |
Stainless steel | $5 – $10 |
Nickel-based superalloys | $20 – $50 |
Titanium alloys | $10 – $20 |
Copper and copper alloys | $5 – $8 |
Aluminum and aluminum alloys | $3 – $5 |
Cobalt-chromium alloys | $15 – $25 |
Tool steels | $5 – $8 |
Tungsten and tungsten alloys | $20 – $30 |
Precious metals (gold, silver, etc.) | Market dependent, significantly higher than other metals |
Suppliers:
Numerous companies worldwide specialize in the production and supply of water-atomized metal powders. Some prominent names include:
- Höganäs AB (Sweden)
- AP Powder Company (USA)
- AMETEK (USA)
- Carpenter Additive (USA)
- SLM Solutions (Germany)
It’s crucial to research and compare different suppliers to find the most suitable option considering factors like pricing, product quality, availability, and customer service.
A Balanced Perspective: Weighing the Pros and Cons
While water atomization offers numerous advantages, it’s essential to acknowledge its limitations for a balanced perspective:
Pros:
- Cost-effective
- Suitable for a wide variety of metals
- Allows tailoring of powder properties
- Environmentally friendly
- Scalable
- Generally safe
Cons:
- May not be suitable for all metals, particularly reactive ones
- Particle size and morphology might not be as precise as some other atomization methods
- Requires careful process control to maintain consistent quality
When making a decision, carefully weigh the pros and cons against your specific needs and application requirements.
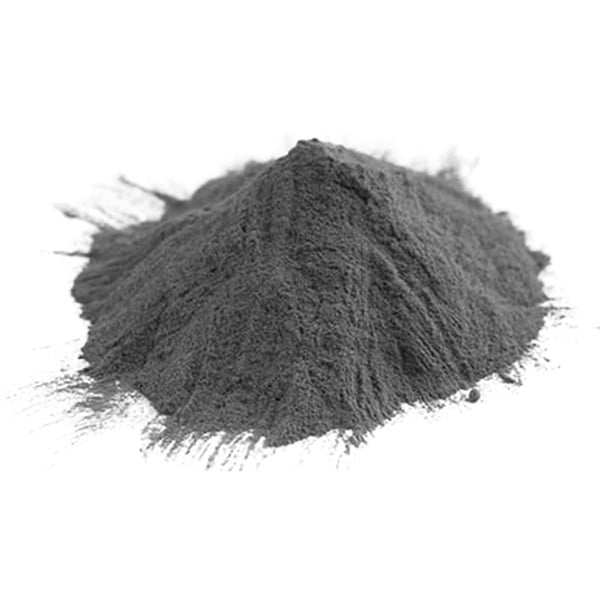
FAQs
Q: Is water atomization the only method for producing metal powder for 3D printing?
Water atomization offers several advantages compared to other methods like gas atomization or atomized shot:
- Cost-effective: Water is readily available and significantly less expensive than the inert gases used in gas atomization.
- Environmentally Friendly: Water atomization generally has a lower environmental footprint compared to gas atomization, which can generate greenhouse gas emissions.
- Broader range of materials: Water atomization can effectively process a wider range of metal types and alloys compared to some other methods.
2. How are metal powders used in 3D printing?
Metal powders are the primary building material for metal additive manufacturing (AM) techniques like Selective Laser Melting (SLM) and Electron Beam Melting (EBM). The powder is fed into the 3D printer layer by layer, where a laser or electron beam melts the powder, fusing it to create the desired 3D object.
3. What are some safety precautions to take when handling metal powders?
Metal powders can pose various safety risks, including:
- Inhalation: Fine metal particles can be inhaled and cause respiratory irritation or even lung damage.
- Fire and explosion: Some metal powders, particularly those with high surface area like magnesium powders, can be flammable and pose a fire or explosion risk.
- Skin and eye irritation: Direct contact with metal powders can irritate the skin and eyes.
To mitigate these risks, it’s crucial to:
- Wear appropriate personal protective equipment (PPE) like respirators, gloves, and safety glasses when handling metal powders.
- Work in well-ventilated areas to prevent inhalation risks.
- Implement proper storage and handling procedures to minimize fire and explosion risks.
- Follow safety data sheets (SDS) for specific metal powders to understand their unique risks and handling guidelines.
4. What are some future trends in the metal powder industry?
The metal powder industry is expected to witness significant growth in the coming years, driven by several factors:
- Advancements in additive manufacturing: As metal AM technologies continue to evolve, the demand for high-quality metal powders for 3D printing is expected to rise significantly.
- Development of novel materials: Research focusing on creating metal powders with unique properties, such as nanopowders or functionally graded materials, is expected to unlock new applications and possibilities.
- Focus on sustainability: Advancements in water atomization technology are likely to focus on reducing energy consumption, minimizing waste generation, and utilizing recycled materials, contributing to a more sustainable future for metal powder production.
5. Where can I find more information about specific metal powders and their suppliers?
Several resources can help you learn more about specific metal powders and their suppliers:
- Metal powder supplier websites: Most reputable suppliers have detailed information about their product offerings, specifications, and technical data on their websites.
- Industry publications and trade shows: Industry publications and trade shows related to metal powders, additive manufacturing, or specific application areas can provide valuable insights and connect you with potential suppliers.
- Scientific research papers and online databases: Research papers and online databases focused on material science and engineering can offer in-depth information about the properties and applications of various metal powders.
Share On
MET3DP Technology Co., LTD is a leading provider of additive manufacturing solutions headquartered in Qingdao, China. Our company specializes in 3D printing equipment and high-performance metal powders for industrial applications.
Inquiry to get best price and customized Solution for your business!
Related Articles
About Met3DP
Recent Update
Our Product
CONTACT US
Any questions? Send us message now! We’ll serve your request with a whole team after receiving your message.
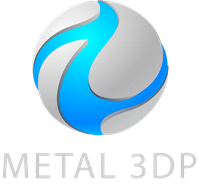
Metal Powders for 3D Printing and Additive Manufacturing
COMPANY
PRODUCT
cONTACT INFO
- Qingdao City, Shandong, China
- [email protected]
- [email protected]
- +86 19116340731