3D Printing Metal Powder:The Economy of Plasma Atomization
Table of Contents
Imagine holding the future in your hands. Not a crystal ball, but something far more tangible – a handful of 3D Printing Metal Powder. These tiny, high-tech particles are the building blocks of a revolution in manufacturing, driven by the power of plasma atomization technology. But this transformative process doesn’t just create innovative materials; it also shapes a complex and fascinating economy. Let’s delve into the world of plasma atomization, exploring its impact on the production, applications, and economic landscape of metal powders.
From Molten Metal to Microscopic Marvels
Plasma atomization is a captivating dance of heat and pressure. Imagine a high-temperature plasma torch, fueled by ionized gas, melting a stream of metal feedstock. This molten metal is then rapidly atomized, breaking down into a fine mist of spherical droplets that solidify into metal powder.
Here’s a table summarizing the key aspects of plasma atomization:
Aspect | Description |
---|---|
Process | High-temperature plasma torch melts and atomizes metal feedstock |
Output | Spherical metal powder particles |
Advantages | High purity, control over particle size and morphology, suitable for reactive and high-melting-point metals |
Limitations | High energy consumption, relatively complex and expensive setup |
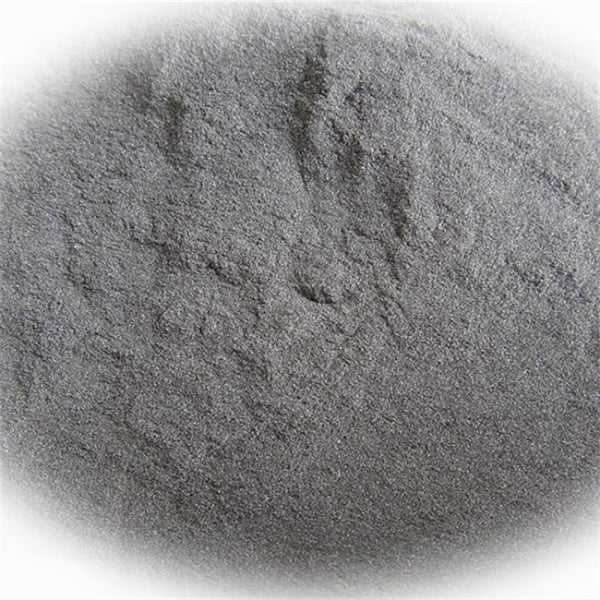
Exploring 3D Printing Metal Powder and their Applications
The beauty of plasma atomization lies in its versatility. It can create a wide range of metal powders, each with unique properties and applications. Here are some examples:
Metal Powder Models:
- Titanium Powder: Renowned for its exceptional strength-to-weight ratio and corrosion resistance, titanium powder is used in aerospace components, medical implants, and high-performance sporting goods.
- Nickel Powder: Offering excellent high-temperature properties and magnetic permeability, nickel powder finds applications in electronics, batteries, and chemical processing equipment.
- Zirconium Powder: This highly corrosion-resistant material is used in nuclear reactors, fuel cells, and chemical processing equipment due to its ability to withstand harsh environments.
- Molybdenum Powder: Known for its high melting point and thermal stability, molybdenum powder is used in high-temperature furnaces, lighting filaments, and rocket engine components.
- Niobium Powder: This superconducting metal finds applications in MRI machines, particle accelerators, and superconducting magnets due to its ability to conduct electricity with zero resistance at very low temperatures.
- Tantalum Powder: Sharing many properties with niobium, tantalum powder is used in capacitors, surgical implants, and chemical processing equipment due to its excellent corrosion resistance and biocompatibility.
- Tungsten Powder: This hardest metal readily available finds applications in cutting tools, welding electrodes, and heat shields due to its exceptional wear resistance and high melting point.
- Cobalt-Chromium Powder: This biocompatible alloy is widely used in medical implants, such as hip and knee replacements, due to its strength, corrosion resistance, and ability to bond with bone.
- Aluminum Alloy Powder: Offering a lightweight and strong alternative to pure aluminum, aluminum alloy powder is used in aerospace components, automotive parts, and consumer electronics.
- Stainless Steel Powder: This versatile material with excellent corrosion resistance is used in a wide range of applications, including medical devices, food processing equipment, and architectural components.
A table showcasing the applications of various metal powders:
Metal Powder | Applications |
---|---|
Titanium | Aerospace components, medical implants, sporting goods |
Nickel | Electronics, batteries, chemical processing equipment |
Zirconium | Nuclear reactors, fuel cells, chemical processing equipment |
Molybdenum | High-temperature furnaces, lighting filaments, rocket engine components |
Niobium | MRI machines, particle accelerators, superconducting magnets |
Tantalum | Capacitors, surgical implants, chemical processing equipment |
Tungsten | Cutting tools, welding electrodes, heat shields |
Cobalt-Chromium | Medical implants |
Aluminum Alloy | Aerospace components, automotive parts, consumer electronics |
Stainless Steel | Medical devices, food processing equipment, architectural components |
-
Ti45Nb Powder for Additive Manufacturing
-
TiNb Alloy Powder
-
TiNbZrSn Alloy Powder
-
Ti6Al4V Powder Titanium Based Metal Powder for Additive Manufacturing
-
CPTi Powder
-
TC18 Powder : Unlocking the Power of Titanium Carbide
-
TC11 Powder : A Comprehensive Guide
-
TC4 ELI Powder
-
Best Ti-6Al-4V powder (TC4 Powder)for additive manufacturing
Cost, Competition, and Future Trends
The economy of plasma atomization is a complex system influenced by various factors.
Cost:
- Production costs: Setting up and operating plasma atomization equipment is capital-intensive, requiring significant upfront investments. Additionally, the high energy consumption adds to the production cost.
- Feedstock costs: The cost of the raw metal feedstock significantly impacts the final price of the metal powder.
Competition:
- Market players: The plasma atomization market is witnessing growing competition from established players and new entrants, especially in Asia. This competition drives innovation and cost reduction, ultimately benefiting consumers.
- Alternative technologies: While plasma atomization is a dominant player, other technologies like water atomization and gas atomization compete in specific market segments. The choice of technology depends on factors like the desired powder characteristics, cost, and material compatibility.
Future trends:
- Growing demand: The demand for metal powders is expected to grow steadily in the coming years, driven by the increasing adoption of additive manufacturing (3D printing) and other advanced manufacturing techniques.
- Technological advancements: Continuous advancements in plasma torch design, process control, and automation are expected to improve efficiency, reduce costs, and expand the range of materials that can be atomized.
- Sustainability: Sustainability concerns are driving the development of environmentally friendly plasma atomization processes, such as those using renewable energy sources and recycling waste materials.
A table comparing the pros and cons of plasma atomization:
Pros | Cons |
---|---|
High purity of metal powders | High energy consumption |
Precise control over particle size and morphology | Relatively complex and expensive setup |
Suitable for reactive and high-melting-point metals | Limited production capacity compared to some alternative technologies |
Additional factors influencing the economy of plasma atomization:
While the cost of equipment and raw materials are commonly cited as crucial factors influencing the economy of plasma atomization, there are several other, often overlooked, aspects that play a significant role:
Regulatory Rollercoaster:
- Environmental Hurdles: Stringent regulations governing air and water emissions can significantly impact the cost of setting up and operating plasma atomization facilities. Implementing pollution control measures adds a layer of complexity and expense to the process.
- Safety First: Stringent safety regulations governing the handling and storage of hazardous materials associated with plasma atomization can also contribute to increased costs. Investing in safety equipment and protocols adds to the overall operational expenditure.
Geography’s Uneven Playing Field:
- Energy Tango: The cost of energy, a critical input for plasma atomization, varies significantly across different geographical regions. Regions with access to cheaper and reliable energy sources will have a clear economic advantage in this industry.
- Labor Labyrinth: Labor costs can also differ substantially depending on the location. Regions with a readily available and skilled workforce specializing in plasma atomization will enjoy a cost advantage compared to those lacking such resources.
Understanding these additional factors is crucial for:
- Businesses: Making informed decisions about where to set up and operate plasma atomization facilities.
- Investors: Assessing the economic viability of plasma atomization ventures in different geographical regions.
- Policymakers: Crafting regulations that balance environmental protection, safety concerns, and the economic viability of the plasma atomization industry.
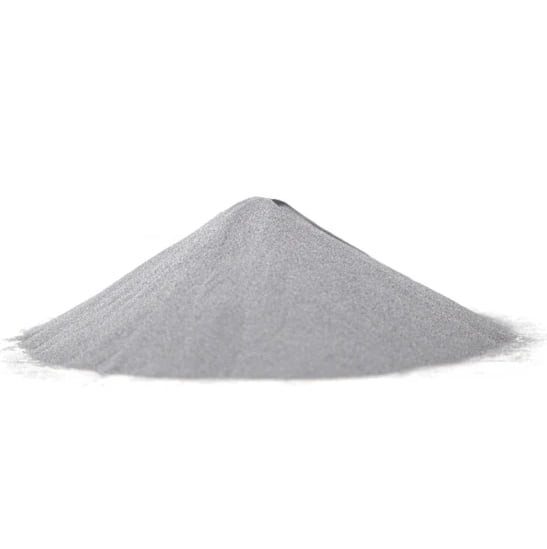
FAQ
Q: What are the advantages of using plasma atomized metal powders compared to other types of metal powders?
A: Plasma atomized metal powders offer several advantages, including:
- High purity: The high-temperature plasma environment removes impurities from the molten metal, resulting in cleaner and more consistent powder particles.
- Precise control over particle size and morphology: The plasma atomization process allows for precise control over the size, shape, and distribution of the powder particles, which is crucial for many applications.
- Suitability for reactive and high-melting-point metals: Plasma atomization can handle reactive metals (such as titanium) and high-melting-point metals (such as tungsten) that are difficult to process using other methods.
Q: What are the limitations of plasma atomization?
A: The main limitations of plasma atomization include:
- High energy consumption: The process requires a significant amount of energy to generate and maintain the high-temperature plasma, which can increase production costs and environmental impact.
- Relatively complex and expensive setup: Setting up and operating a plasma atomization facility requires specialized equipment and expertise, making it a capital-intensive process.
- Limited production capacity: Compared to some other metal powder production methods, plasma atomization typically has a lower production capacity, which can limit its suitability for high-volume applications.
Q: What are the future trends in the plasma atomization market?
A: The future of the plasma atomization market is expected to be shaped by several key trends, including:
- Growing demand for metal powders: Driven by the increasing adoption of additive manufacturing and other advanced manufacturing techniques, the demand for metal powders is expected to continue to grow in the coming years.
- Technological advancements: Continuous advancements in plasma torch design, process control, and automation are expected to improve efficiency, reduce costs, and expand the range of materials that can be atomized.
- Sustainability: Sustainability concerns are driving the development of environmentally friendly plasma atomization processes, such as those using renewable energy sources and recycling waste materials.
In conclusion, the economy of plasma atomization technology is a dynamic and complex landscape shaped by various factors. While the high cost of production and competition from alternative technologies pose challenges, the growing demand for metal powders, ongoing technological advancements, and increasing focus on sustainability offer promising opportunities for the future. As the technology continues to evolve, plasma atomization is poised to play a crucial role in revolutionizing the way we manufacture and interact with metals.
Share On
MET3DP Technology Co., LTD is a leading provider of additive manufacturing solutions headquartered in Qingdao, China. Our company specializes in 3D printing equipment and high-performance metal powders for industrial applications.
Inquiry to get best price and customized Solution for your business!
Related Articles
About Met3DP
Recent Update
Our Product
CONTACT US
Any questions? Send us message now! We’ll serve your request with a whole team after receiving your message.
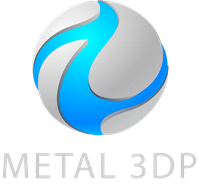
Metal Powders for 3D Printing and Additive Manufacturing