Complete Guide of Water Atomization for 3D Printing Metal Powders
Table of Contents
Imagine sculpting intricate metal objects layer by layer, building them from the ground up with the precision of a digital artist. This is the magic of 3D Printing Metal Powders, and at the heart of this revolutionary technology lies a crucial ingredient: metal powder. But how do we transform solid metal into the fine, flowable powder needed for 3D printing? Enter water atomization, a powerful and versatile technique that takes center stage in this guide.
Unveiling the Magic: What is Water Atomization?
Think of water atomization as the art of transforming molten metal into a fine mist of tiny droplets. This seemingly simple process, however, holds immense power. Here’s how it works:
- Melting the Metal: The journey begins with the chosen metal, heated to its molten state in a furnace. Imagine a fiery crucible, glowing with molten metal, ready to be transformed.
- High-Pressure H2O: Next, a high-pressure water jet is unleashed upon the molten metal stream. This powerful jet, akin to a firefighter’s hose on steroids, breaks the liquid metal into a fine spray of tiny droplets.
- Rapid Solidification: As the metal droplets disperse, they rapidly cool and solidify in mid-air, forming individual metal powder particles. Picture tiny metal raindrops, solidifying before they even hit the ground.
- Collection and Processing: The newly formed metal powder is collected, dried, and sieved to achieve the desired particle size and distribution. This ensures consistency and optimal performance for 3D printing applications.
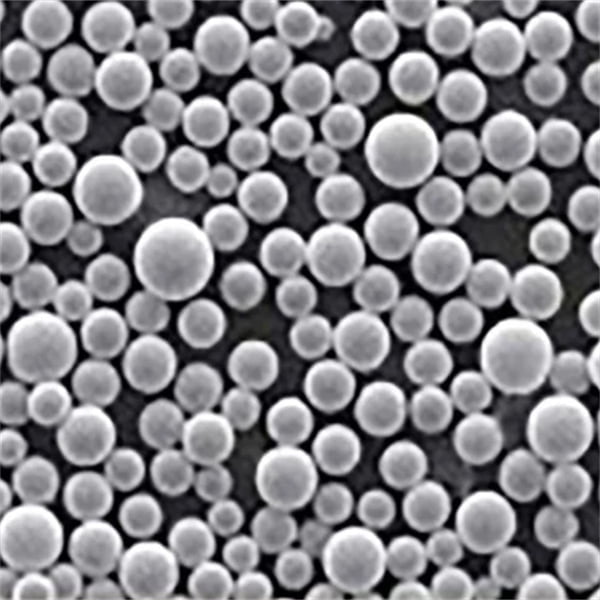
3D Printing Metal Powders: Why Choose This Method?
Feature | Benefit | Explanation |
---|---|---|
Design Freedom | Highly complex geometries | Unlike traditional methods like machining or casting that rely on subtractive or formative techniques, 3D printing with metal powders builds parts layer-by-layer directly from a digital model. This enables the creation of intricate internal features, channels, and lattice structures that would be impossible or highly impractical with other methods. |
Material Versatility | Wide range of metals | Metal powders are available in a vast array of options, from common metals like titanium and aluminum to more exotic materials like Inconel and precious metals like gold. This allows engineers to choose the perfect material for the specific application, considering factors like strength, weight, corrosion resistance, and biocompatibility. |
Rapid Prototyping | Faster design iteration | The digital nature of 3D printing allows for quick and easy design changes. Modifications can be made to the CAD model and a new prototype can be printed within a short timeframe. This significantly reduces development time and cost compared to traditional prototyping methods. |
Lightweighting | Design for efficiency | The ability to create complex internal structures with 3D printing metal powders allows for parts to be lightweight while maintaining their strength. This is crucial in applications like aerospace and automotive where weight reduction translates to improved fuel efficiency and performance. |
On-Demand Manufacturing | Reduced inventory needs | 3D printing with metal powders enables parts to be produced as needed, eliminating the requirement for large production runs and storage of finished goods. This is particularly beneficial for low-volume production or spare parts that may not be readily available through traditional channels. |
Minimal Material Waste | Sustainable production | Metal 3D printing only uses the material required to build the part, unlike traditional methods that generate significant scrap material. This reduces waste and lowers the environmental impact of the manufacturing process. |
Customization | Personalized products | The ability to create complex geometries with 3D printing metal powders allows for the production of highly customized parts. This is beneficial for applications like medical implants, prosthetics, and dental crowns that require a perfect fit for each individual. |
Consolidation of Parts | Reduced assembly complexity | The design freedom offered by 3D printing metal powders allows for the creation of complex parts that integrate the functionality of multiple components. This reduces assembly complexity, lowers production costs, and improves the overall performance of the product. |
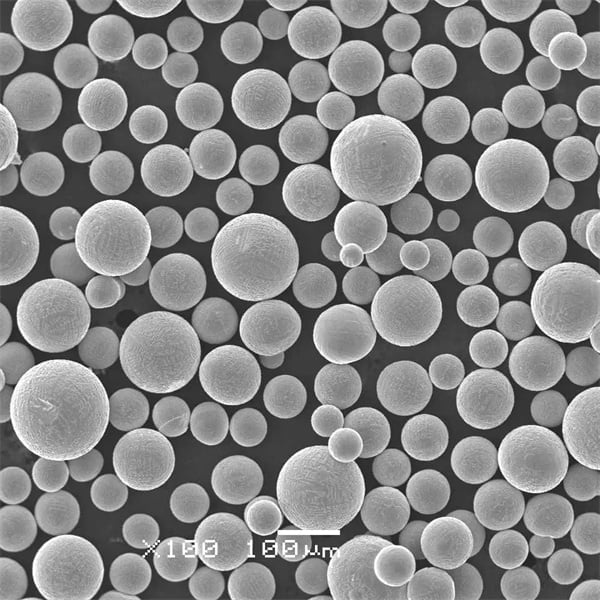
Water Atomization Applications in 3D Printing: Bringing Metal to Life
Process | Description | Advantages | Disadvantages |
---|---|---|---|
Water Atomization | Molten metal is transformed into a fine powder through a multi-step process. First, the metal is melted in a furnace. Then, a high-pressure nozzle forces the liquid metal into a thin stream. This stream is broken into tiny droplets by a high-velocity water jet. Finally, the rapidly cooled droplets solidify into individual powder particles, which are collected, dried, and sieved to achieve a specific size and distribution. | – Cost-effective: Water atomization offers a relatively low-cost method for producing large quantities of metal powder compared to other techniques. – Wide material compatibility: This method can handle a broad spectrum of metals, from common varieties like steel and aluminum to more specialized options. | – Particle shape: Water-atomized powders tend to be less spherical than those produced by other methods. This can affect the flowability of the powder and the packing density within the 3D printing bed, potentially impacting the surface quality of the final printed part. |
Selective Laser Melting (SLM) | A 3D printing technique that utilizes a high-powered laser to selectively melt and fuse metal powder particles layer by layer. The laser beam follows a digital design, building up the desired 3D object. | – High precision and accuracy: SLM allows for the creation of complex geometries with tight tolerances, making it ideal for intricate metal parts. – Design freedom: Unlike traditional manufacturing methods, SLM offers significant design freedom, enabling the production of parts with internal channels, lattices, and other unique features. | – Limited build volume: Current SLM machines typically have a restricted build volume, limiting the size of printable objects. – Surface roughness: The layer-by-layer nature of SLM can result in a slightly rough surface finish on the printed parts, which may require additional post-processing. |
Electron Beam Melting (EBM) | Similar to SLM, EBM employs a high-powered beam, but in this case, an electron beam operates in a vacuum environment. The electron beam melts the metal powder particles, fusing them together to form the desired 3D object. | – Superior mechanical properties: EBM produces parts with excellent mechanical properties, including high strength and good fatigue resistance. This is due to the vacuum environment, which minimizes oxidation and enhances material properties. – Broader material compatibility: Compared to SLM, EBM offers compatibility with a wider range of metals, including reactive materials like titanium. | – Higher cost: EBM systems are generally more expensive than SLM machines, impacting the overall cost of production. – Vacuum requirement: The need for a vacuum environment adds complexity to the EBM process and can limit its accessibility in certain settings. |
Binder Jetting (BJ) | A 3D printing method that utilizes a liquid binding agent to selectively inkjet metal powder particles onto a printing platform. The layers are then cured to create a solid structure. | – High build volume: Binder jetting offers a larger build volume compared to SLM and EBM, enabling the production of bigger metal parts. – Potential for full-color printing: In development are binder jetting techniques that incorporate colored binders, opening doors for the creation of functional and visually appealing metal parts. | – Lower part strength: Parts produced through binder jetting typically exhibit lower strength compared to those made with SLM or EBM. This may necessitate additional post-processing steps, such as infiltration, to achieve the desired mechanical properties. – Limited material options: Currently, binder jetting has a more limited range of compatible metal materials compared to other 3D printing methods. |
Choosing the Right Water-Atomized Metal Powder
Factor | Description | Impact on Additive Manufacturing Process & Final Part |
---|---|---|
Material Properties | The specific metal or alloy chosen will dictate the final properties of the 3D printed part. | • Strength & Durability: Consider applications requiring high strength-to-weight ratios like aerospace components. Nickel alloys or titanium powders excel here. • Corrosion Resistance: Parts exposed to harsh environments might benefit from stainless steel or copper alloys. • Thermal Conductivity & Electrical Conductivity: Heat sinks or electrical conductors might utilize aluminum or copper powders for optimal performance. |
Particle Size & Distribution | The size and variation in size of the powder particles significantly affect printability and final part characteristics. | • Flowability: Uniform, spherical particles flow more easily, leading to consistent layer formation during printing. • Packing Density: The ideal powder packing density allows for maximum material utilization while enabling proper fusion between layers. • Surface Finish: Finer powders generally result in smoother surface finishes on the final part. • Mechanical Properties: Particle size and distribution can influence the final part’s strength, porosity, and ductility. |
Particle Morphology | The shape of the powder particles influences their packing behavior and flowability. | • Sphericity: Highly spherical particles offer superior flowability and packing density, leading to improved printability. • Satellites & Satellited Particles: These are smaller particles attached to larger ones. Excessive satellites can hinder flowability and lead to inconsistencies in the printed part. • Hollow Particles: While offering weight reduction benefits, hollow particles can create internal voids in the final part, impacting its mechanical strength. |
Chemical Composition & Powder Purity | The presence of impurities or deviations from the desired chemical makeup can affect the printing process and final part quality. | • Oxygen Content: Excessive oxygen can lead to higher porosity and reduced mechanical properties. • Moisture Content: Moisture can cause spattering during the printing process and lead to surface defects. • Trace Elements: The presence of unintended elements can influence the material’s properties and printability. Reputable suppliers provide detailed chemical analysis reports to ensure adherence to material specifications. |
Powder Flowability | The ease with which the powder flows is crucial for consistent layer formation in additive manufacturing processes. | Poor flowability can lead to: • Inconsistent layer thickness • Segregation of particles within the powder bed • Difficulties with material spreading mechanisms These issues can all negatively impact the quality and dimensional accuracy of the final part. |
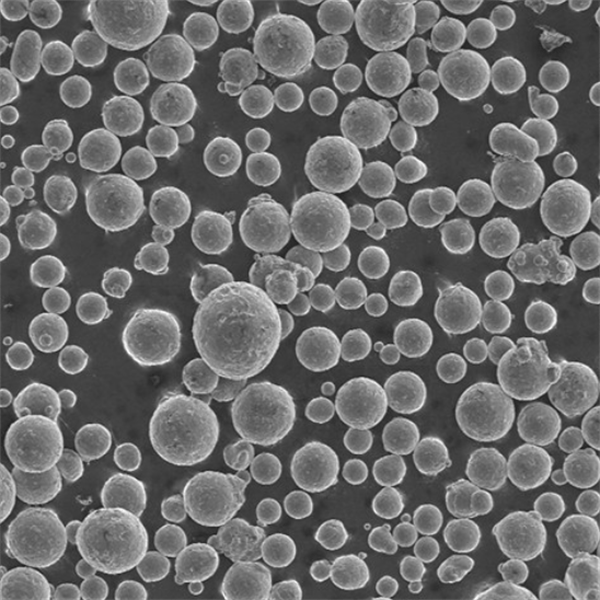
Advanced Considerations for Water Atomization
Factor | Description | Impact on Process | Mitigation Strategies |
---|---|---|---|
Multi-Component Feedstock | When atomizing alloys or slurries containing multiple components, factors like particle size distribution and composition uniformity become critical. | Segregation of components can occur during atomization, leading to variations in final product properties. | – Controlled Mixing: Utilizing high-shear mixers or inline homogenizers can ensure uniform distribution of components within the feedstock. – Co-Atomization: Simultaneous atomization of individual elements can be employed to achieve precise control over final composition. – Monitoring and Feedback Systems: Real-time monitoring of particle size and composition allows for adjustments to atomization parameters for consistent product quality. |
Particle Morphology | The shape and surface characteristics of the atomized particles significantly influence downstream processes like powder handling, sintering, and final product performance. | Irregular particle shapes can lead to challenges in packing density, flowability, and sintering behavior. | – Atomization Pressure and Nozzle Design: Optimizing these parameters can influence the degree of droplet break-up and solidification, leading to more spherical particles. – Surfactant Selection: Specific surfactants can be introduced into the water stream to modify surface tension and promote more uniform particle morphology. – Rapid Solidification: Techniques like high-pressure atomization or rapid quenching can minimize particle growth and promote more spherical shapes. |
Environmental Impact | Water atomization processes can generate wastewater containing metal particles and require significant water consumption. | Untreated wastewater disposal poses environmental hazards. High water usage can strain resources. | – Water Recycling Systems: Closed-loop systems can be implemented to capture and treat the atomization water, minimizing waste and water consumption. – Flocculation and Settling: These techniques can be used to separate metal particles from the wastewater before treatment and disposal. – Advanced Filtration Systems: Membrane filtration or ion exchange processes can be employed for high-efficiency removal of contaminants from wastewater. |
Process Automation and Control | Integration of automation and real-time process control can significantly improve consistency and efficiency. | Manual operation can lead to human error and inconsistencies in product quality. | – Automated Control Systems: Implementing feedback loops and automated adjustments based on sensor data ensures consistent product quality. – Advanced Monitoring Systems: Real-time monitoring of critical parameters like flow rates, pressures, and particle characteristics allows for proactive adjustments and optimization. – Machine Learning Integration: Machine learning algorithms can analyze historical data and sensor readings to predict potential issues and optimize process parameters for improved efficiency and yield. |
Safety Considerations | Water atomization processes involve high pressures, moving parts, and potential exposure to metal particulates. | Improper safety procedures can lead to accidents and injuries. | – Proper Training and Personal Protective Equipment (PPE): Thorough training for operators on safe handling procedures and the use of appropriate PPE is crucial. – Regular Maintenance and Inspection: Implementing preventative maintenance schedules and safety inspections minimizes equipment failure and potential hazards. – Enclosure Design and Ventilation Systems: Enclosing high-pressure areas and utilizing proper ventilation systems mitigate exposure to airborne metal particles. |
FAQ
Question | Answer |
---|---|
What are the typical particle sizes of water-atomized metal powders for 3D printing? | The particle size range typically falls between 10 and 150 micrometers (µm), with the specific range varying depending on the chosen metal and the desired application. |
Can water-atomized metal powders be recycled? | Yes, water-atomized metal powders can be recycled through various techniques, such as re-melting and re-atomization. This promotes sustainability and reduces waste. |
How does water atomization compare to other metal powder production methods? | While water atomization offers advantages in terms of cost-effectiveness and production rate, other methods like gas atomization might yield more spherical particles and are suitable for reactive metals. The choice ultimately depends on the specific application and desired properties. |
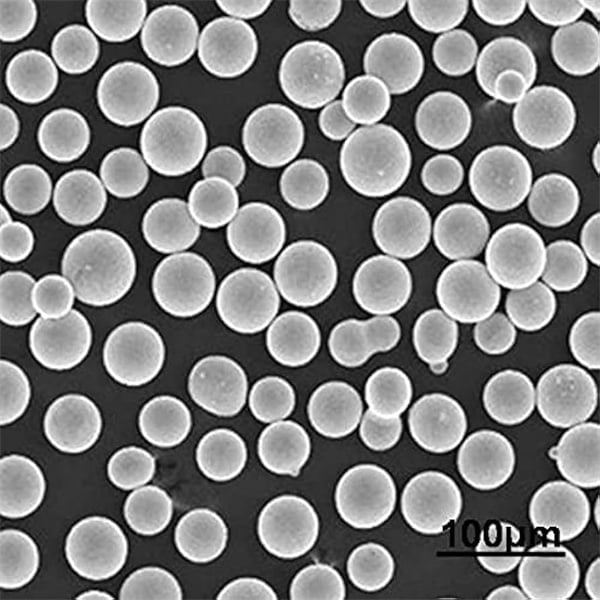
Conclusion: Embracing the Potential of Water Atomization
As the world of 3D printing continues to evolve, water atomization remains a cornerstone technology, offering a reliable and cost-effective means to produce metal powders for various applications. From complex aerospace components to intricate medical implants, water-atomized powders empower the creation of diverse and functional 3D printed parts.
Looking ahead, the future of water atomization is brimming with potential. Continuous advancements in the technology promise:
- Enhanced particle shape: Through refinements in atomization techniques and the exploration of innovative materials, the sphericity of water-atomized powders can be further improved, potentially matching the quality achieved by more expensive methods like gas atomization.
- Expanded material compatibility: Researchers are actively exploring the potential of water atomization for a broader range of metals, including highly reactive materials that pose challenges with conventional methods. This could unlock new avenues for 3D printing applications in demanding industries like aerospace and medicine.
- Sustainable advancements: The focus on environmental responsibility is driving the development of eco-friendly water atomization processes. This might involve closed-loop systems that minimize water usage and waste generation, contributing to a more sustainable future for 3D printing metal powder production.
By embracing the potential of water atomization and continuously pushing its boundaries, we can unlock a future where 3D printing metal becomes an even more powerful and versatile technology, shaping the world around us in innovative and transformative ways.
Share On
MET3DP Technology Co., LTD is a leading provider of additive manufacturing solutions headquartered in Qingdao, China. Our company specializes in 3D printing equipment and high-performance metal powders for industrial applications.
Inquiry to get best price and customized Solution for your business!
Related Articles
About Met3DP
Recent Update
Our Product
CONTACT US
Any questions? Send us message now! We’ll serve your request with a whole team after receiving your message.
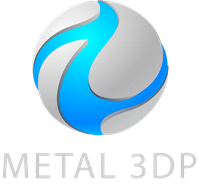
Metal Powders for 3D Printing and Additive Manufacturing