3D Printing Metal powers: Water atomization’s Limitations and Solutions
Table of Contents
The world of 3D Printing Metal powers is constantly evolving, pushing the boundaries of what’s possible in manufacturing. One exciting technology making waves is water misting atomization, a method for producing 3D Printing Metal Powders with unique properties and potential applications. But, like any innovation, water misting comes with its own set of limitations. Let’s delve into the fascinating world of metallic mist, exploring both its strengths and weaknesses, and uncovering potential solutions that could pave the way for a more robust and efficient future.
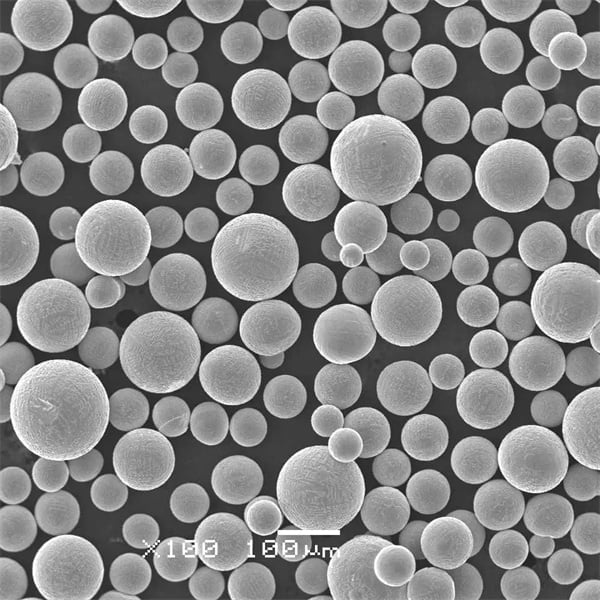
Limitations of Water atomization for 3D Printing Metal powers
Imagine creating metal powder as fine as mist, swirling and condensing into tiny, perfectly formed particles. That’s the essence of water misting atomization. However, this seemingly magical process faces some limitations:
- Particle size control: Achieving consistent and precise particle size distribution can be challenging. Factors like water flow rate, pressure, and nozzle design can significantly impact particle size, potentially leading to inconsistencies in the final printed product.
- Powder morphology: The shape and surface characteristics of the powder particles can be irregular, which can affect their flowability, packing density, and ultimately, the printability of the metal powder. Irregularly shaped particles can be difficult to spread evenly in the printing bed, impacting the quality and consistency of the printed object.
- Oxidation: The exposure of metal particles to water and air during the atomization process can lead to oxidation, which can affect the final properties of the printed metal. The presence of oxides can hinder the bonding between metal particles, impacting the mechanical strength and overall quality of the printed object.
- Safety concerns: Working with water and high-pressure systems necessitates strict safety protocols to be in place. Additionally, the fine metallic mist can pose health risks if inhaled, requiring proper ventilation and personal protective equipment for operators.
These limitations highlight the need for continuous research and development to refine the water misting process and overcome these challenges.
Solutions of these Limitations
While the limitations of water misting are real, innovative solutions are emerging to address them:
- Advanced process control: Implementing sophisticated control systems can help maintain consistent water flow rates, pressure, and other crucial parameters during atomization. This precise control can lead to more consistent and predictable particle size distribution.
- Nozzle design optimization: Developing specialized nozzles with specific geometries and materials can optimize the atomization process, promoting the formation of spherical particles with smooth surfaces. This can improve powder flowability, packing density, and ultimately, the printability of the metal powder.
- Inert gas atomization: Utilizing inert gases like argon or nitrogen during the atomization process can significantly reduce the risk of oxidation. These gases create an oxygen-free environment, minimizing the interaction between the metal particles and air, leading to less oxidation and improved final product quality.
- Enhanced safety measures: Implementing robust ventilation systems and ensuring operators wear appropriate personal protective equipment (PPE) can significantly mitigate the safety risks associated with water misting atomization. Additionally, regular equipment maintenance and safety training are crucial for safe operation.
By implementing these solutions, the limitations of water misting can be gradually overcome, paving the way for a more reliable and efficient production of high-quality 3D metal powders.
Benefits and Applications: Why Embrace the Metallic Mist?
Despite the limitations, water misting offers several advantages that make it an attractive option for 3D Printing Metal Powders production:
- High cooling efficiency: The water misting process effectively cools the molten metal during atomization, leading to the formation of finer and more spherical particles compared to traditional methods like gas atomization. This can be beneficial for applications requiring high-precision metal components.
- Cost-effectiveness: Compared to other atomization methods, water misting can be a more cost-effective solution, especially for large-scale production. This advantage can pave the way for more affordable 3D metal printing.
- Environmentally friendly: Water misting utilizes water instead of harmful gases like nitrogen, reducing the environmental impact of the atomization process. This aligns with the growing focus on sustainable manufacturing practices.
These benefits, coupled with the ongoing efforts to address the limitations, make water misting a promising technology with diverse potential applications:
- Aerospace and defense: The production of lightweight and high-strength components for aircraft and spacecraft.
- Medical implants: The creation of biocompatible metal powders for personalized implants with improved functionality and osseointegration (bone bonding).
- Automotive: The development of customized and lightweight parts for vehicles.
- Electronics: The fabrication of intricate and high-performance electronic components.
As research and development continue, the potential applications of water misting in 3D metal printing are likely to expand even further, shaping the future of this transformative technology.
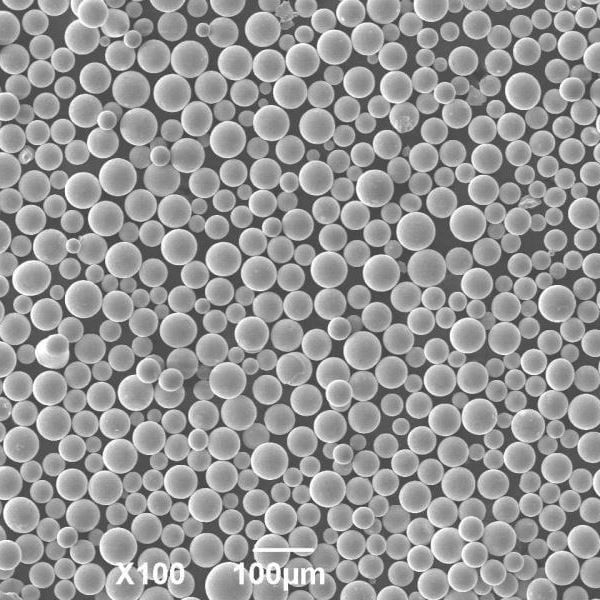
FAQ
Q: What are the typical particle sizes achievable with water misting atomization?
A: The achievable particle size range for water misting atomization typically falls between 10 and 3D Printing Metal Powders100 micrometers. However, achieving consistent and precise control within this range can be challenging, as discussed in the limitations section.
Q: How does water misting compare to other atomization methods like gas atomization?
A: While both methods involve breaking down molten metal into fine particles, there are key differences:
- Cooling mechanism: Water misting uses water for rapid cooling, while gas atomization relies on inert gases like argon or nitrogen.
- Particle size and morphology: Water misting can often produce finer and more spherical particles compared to gas atomization.
- Cost: Water misting can be a more cost-effective option, especially for large-scale production.
- Environmental impact: Water misting is generally considered more environmentally friendly due to the use of water instead of gases.
It’s important to note that the choice between water misting and gas atomization depends on various factors, including the desired particle size, material properties, and cost considerations.
Q: What safety precautions are necessary when working with water misting atomization?
A: Due to the presence of water and high-pressure systems, several safety measures are crucial:
- Proper ventilation: Efficient ventilation systems are essential to remove the metallic mist and prevent inhalation risks.
- Personal protective equipment (PPE): Operators should wear appropriate PPE, including respirators, gloves, and eye protection, to minimize exposure to the metallic mist.
- Regular maintenance: Regular equipment maintenance is vital to ensure safe operation and prevent potential hazards.
- Safety training: Providing operators with comprehensive safety training on the proper handling of equipment and procedures is crucial.
By adhering to these precautions, the safety risks associated with water misting atomization can be effectively mitigated.
Q: What is the future outlook for water misting atomization in 3D metal printing?
A: The future of water misting atomization appears promising. With ongoing research and development efforts focused on overcoming limitations and improving process control, this technology has the potential to become a more reliable, cost-effective, and environmentally friendly solution for producing high-quality 3D metal powders. This, in turn, can lead to wider adoption of 3D metal printing across various industries, revolutionizing the manufacturing landscape.
Share On
MET3DP Technology Co., LTD is a leading provider of additive manufacturing solutions headquartered in Qingdao, China. Our company specializes in 3D printing equipment and high-performance metal powders for industrial applications.
Inquiry to get best price and customized Solution for your business!
Related Articles
About Met3DP
Recent Update
Our Product
CONTACT US
Any questions? Send us message now! We’ll serve your request with a whole team after receiving your message.
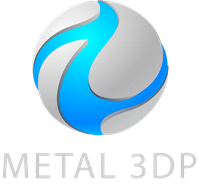
Metal Powders for 3D Printing and Additive Manufacturing
COMPANY
PRODUCT
cONTACT INFO
- Qingdao City, Shandong, China
- [email protected]
- [email protected]
- +86 19116340731