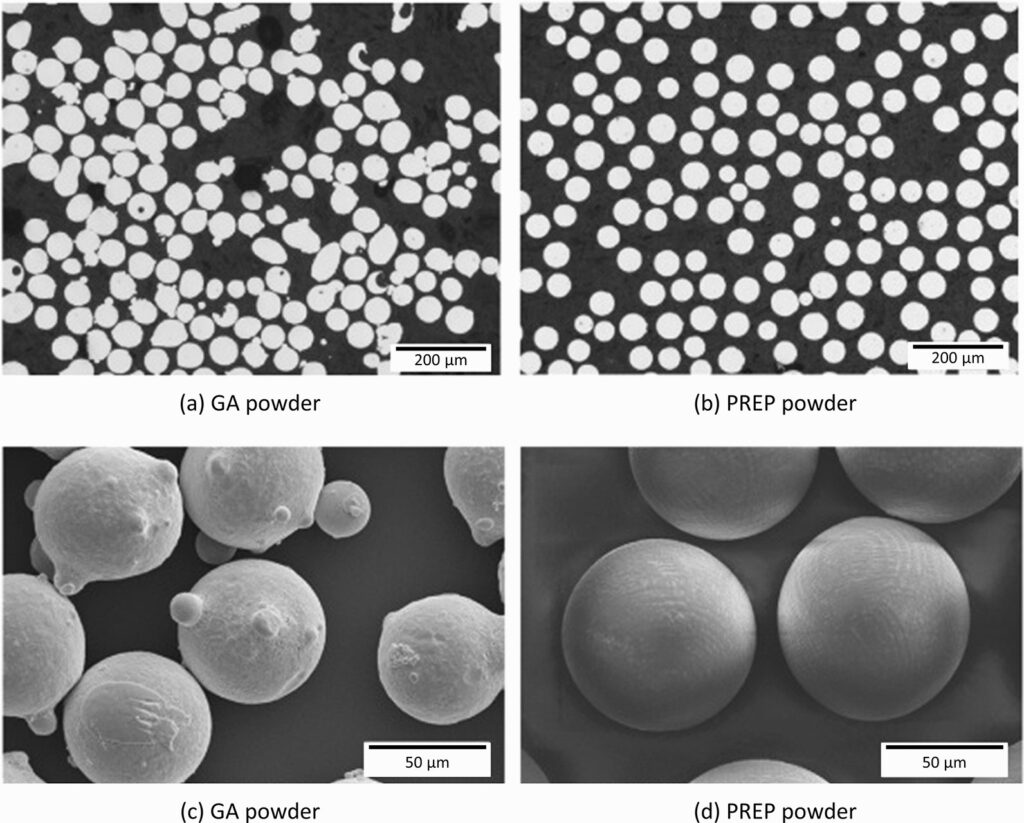
AlSi10 Spherical Aluminum Alloy Powder: Comprehensive Guide
Low MOQ
Provide low minimum order quantity to meet different needs.
OEM & ODM
Provide customized products and design services to meet unique customer needs.
Adequate Stock
Ensure fast order processing and provide reliable and efficient service.
Customer Satisfaction
Provide high quality products with customer satisfaction at the core.
share this article
Table of Contents
Overview of AlSi10 Spherical Aluminum Alloy Powder
When it comes to advanced manufacturing and materials engineering, few materials are as versatile and widely used as AlSi10 Spherical Aluminum Alloy Powder. Its unique combination of lightweight properties, high strength-to-weight ratio, and thermal conductivity makes it an essential material in industries like aerospace, automotive, and 3D printing. But what exactly is AlSi10, and why is it gaining so much traction? Let’s dive into the details.
AlSi10 is a spherical aluminum-silicon alloy powder that consists primarily of aluminum (Al) and silicon (Si), with approximately 10% silicon content. The spherical shape of the powder is achieved through specialized manufacturing processes like gas atomization, which enhances its flowability, packing density, and consistency—key attributes for modern manufacturing techniques like additive manufacturing (AM).
In this guide, we’ll break down the composition, properties, applications, and specifications of AlSi10 Spherical Aluminum Alloy Powder. We’ll also explore its pros and cons, pricing, and suppliers, all while keeping the tone approachable and conversational.
Composition and Characteristics of AlSi10 Spherical Aluminum Alloy Powder
To understand what makes AlSi10 stand out, let’s start with its composition and essential characteristics.
Key Chemical Composition of AlSi10
The table below outlines the typical chemical makeup of AlSi10 Spherical Aluminum Alloy Powder.
Element | Typical Composition (%) |
---|---|
Aluminum (Al) | ~90 |
Silicon (Si) | ~10 |
Iron (Fe) | ≤ 0.5 |
Copper (Cu) | ≤ 0.1 |
Magnesium (Mg) | ≤ 0.1 |
Zinc (Zn) | ≤ 0.05 |
Others | ≤ 0.15 |
Notable Characteristics
The following characteristics make AlSi10 distinct from other alloy powders:
- Spherical Shape: The spherical morphology, achieved through gas atomization, ensures excellent flowability for powder-bed fusion processes.
- High Thermal Conductivity: Thanks to its aluminum content, AlSi10 boasts superior heat dissipation, making it ideal for thermal management applications.
- Lightweight: Aluminum’s low density ensures that even complex designs remain lightweight, which is particularly beneficial in aerospace and automotive applications.
- Oxidation Resistance: The silicon addition enhances resistance to oxidation, improving performance in high-temperature environments.
- Ductility: Despite its strength, AlSi10 retains sufficient ductility for post-processing techniques like machining or cold working.
Properties of AlSi10 Spherical Aluminum Alloy Powder
Understanding the performance of AlSi10 starts with knowing its physical, mechanical, and thermal properties. Below is a detailed overview:
Property | Value/Range | Significance |
---|---|---|
Density | ~2.7 g/cm³ | Lightweight material, ideal for weight-sensitive applications. |
Melting Point | 577–615°C | Suitable for high-temperature manufacturing processes like laser sintering. |
Thermal Conductivity | 150–200 W/m·K | Excellent heat dissipation for thermal management systems. |
Tensile Strength | ~250–300 MPa | Provides structural stability in load-bearing designs. |
Yield Strength | ~170–200 MPa | Good for applications requiring moderate strength without excessive brittleness. |
Hardness (HV) | ~90–120 HV | Sufficient hardness for wear-resistant components. |
Flow Rate | 15–25 s/50g (Hall Flow) | Ensures smooth powder flow for consistent additive manufacturing. |
Particle Size | 10–45 µm (typical) | Optimized for selective laser melting (SLM) and other AM techniques. |
Applications of AlSi10 Spherical Aluminum Alloy Powder
AlSi10 is a highly adaptable material with a wide range of applications across various industries. Below are some of the most common uses:
Application | Industry | Details |
---|---|---|
Additive Manufacturing (3D Printing) | Aerospace, Automotive | Used in SLM and DMLS for lightweight, complex parts. |
Thermal Management Components | Electronics | Heat sinks and housings for efficient heat dissipation. |
Aerospace Components | Aerospace | Lightweight structural parts like brackets and panels. |
Automotive Parts | Automotive | Engine components, wheels, and other high-performance parts. |
Prototyping | Engineering | Quick prototyping of intricate designs with high precision. |
Tooling and Molds | Manufacturing | Durable, lightweight molds for injection molding and casting. |
Medical Devices | Healthcare | Biocompatible parts for surgical instruments and orthopedic implants. |
Specifications, Sizes, and Standards
Manufacturers and suppliers typically provide AlSi10 powder in different grades, particle sizes, and standards. Let’s explore these in more detail:
Specification | Details |
---|---|
Particle Size Distribution | 10–45 µm, 15–53 µm (optimized for AM processes). |
Standards Compliance | ISO 9001, ASTM F3318 (for additive manufacturing powders). |
Packaging | 1 kg, 5 kg, 20 kg containers, vacuum-sealed to prevent oxidation. |
Purity | ≥ 99.95% (high-quality powders). |
Available Grades | Gas-atomized, plasma-atomized for uniformity. |
Suppliers and Pricing Details
Looking to source AlSi10 powder? Here are some common suppliers and their pricing details (approximate as of 2024):
Supplier | Grade Offered | Price (USD/kg) | Location | Contact |
---|---|---|---|---|
Höganäs AB | Gas-Atomized | $80–$120 | Sweden | www.hoganas.com |
EOS GmbH | AM-Optimized Powder | $100–$150 | Germany | www.eos.info |
Carpenter Additive | High-Purity Powder | $90–$130 | USA | www.carpenteradditive.com |
LPW Technology | Plasma-Atomized | $120–$180 | UK | www.lpwtechnology.com |
TLS Technik GmbH | Gas-Atomized | $85–$110 | Germany | www.tls-technik.com |
Advantages and Limitations of AlSi10 Spherical Aluminum Alloy Powder
Like any material, AlSi10 has its strengths and weaknesses. Here’s a detailed comparison:
Advantages | Limitations |
---|---|
Lightweight with high strength-to-weight ratio. | Higher cost compared to conventional aluminum alloys. |
Excellent thermal conductivity. | Limited to specific AM processes (e.g., SLM, DMLS). |
High oxidation resistance due to silicon content. | Requires specialized equipment for processing. |
Uniform particle size ensures consistent results. | May require post-processing to achieve final properties. |
Versatile across industries. | Not ideal for applications needing ultra-high strength. |
FAQs About AlSi10 Spherical Aluminum Alloy Powder
Question | Answer |
---|---|
What is AlSi10 powder used for? | Commonly used in 3D printing, aerospace, automotive, and thermal management systems. |
What are the advantages of spherical powder? | Spherical powders flow better, pack more densely, and produce consistent results. |
How is AlSi10 manufactured? | Typically through gas atomization or plasma atomization for uniformity. |
What particle size is best for 3D printing? | Sizes between 15–45 µm are ideal for SLM and DMLS processes. |
Is AlSi10 biocompatible? | Yes, it is often used in medical applications like surgical instruments. |
Conclusion
AlSi10 Spherical Aluminum Alloy Powder is a game-changer in modern manufacturing. With its lightweight properties, high thermal conductivity, and excellent machinability, it has become a cornerstone material for industries ranging from aerospace to healthcare. Whether you’re looking to create high-performance automotive parts or efficient heat sinks, AlSi10 offers the perfect balance of strength, versatility, and precision.
So, what’s the next step? If you’re in the market for high-quality AlSi10 powder, explore reputable suppliers, evaluate your application requirements, and embrace this cutting-edge material to push the boundaries of innovation in your projects!
Get Latest Price
About Met3DP
Product Category
HOT SALE
CONTACT US
Any questions? Send us message now! We’ll serve your request with a whole team after receiving your message.
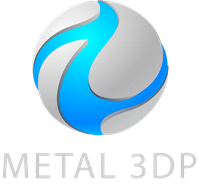
Metal Powders for 3D Printing and Additive Manufacturing