Aluminium Alloy 7050 Powder
Table of Contents
aluminium alloy 7050 powder is a high-strength aerospace alloy also available in powder form for additive manufacturing and other powder metallurgy applications. With zinc and magnesium as primary alloyants, this 7xxx series alloy demonstrates superior mechanical properties ideal for critical structural components.
Overview of aluminium alloy 7050 powder
Property | Description |
---|---|
Alloy | AA7050 |
UNS Number | A97050 |
EN Designation | EN AW-7050 |
Primary Alloying Elements | Zinc (Zn), Magnesium (Mg), Copper (Cu) |
Strength | High strength-to-weight ratio |
Tensile Strength | Up to 570 MPa (T651 temper) |
Yield Strength | Up to 500 MPa (T651 temper) |
Fracture Toughness | Around 33 MPa√m (T7351 temper) |
Fatigue Strength | About 310 MPa at 107 cycles (T7351 temper) |
Corrosion Resistance | Good |
Thermal Conductivity | High |
Machinability | Good |
Applications | |
Aerospace | Structural airframe components, landing gear, rockets |
Automotive | Wheels, control arms, drivetrain parts |
Industrial | Robotics, tooling jigs and fixtures, instrumentation |
Marine | Propellers, drive shafts, pumps, valves |
Powder Production Methods | Gas atomization, plasma atomization, cryomilling |
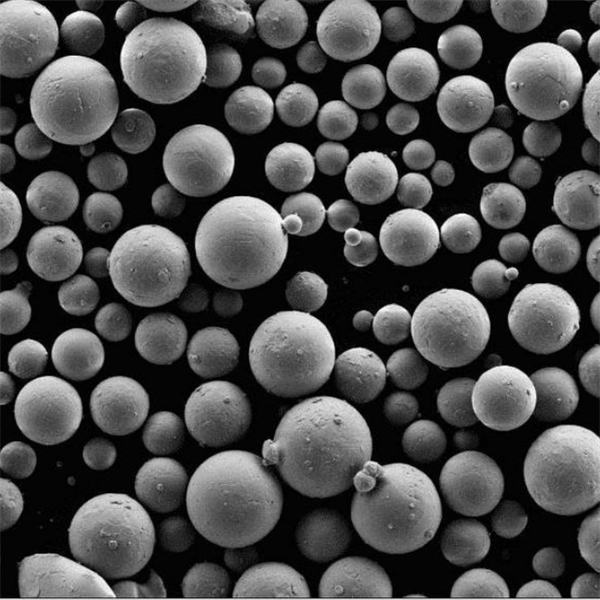
Types of Aluminium 7050 Powder
Based on production method and characteristics, common Al7050 powder varieties include:
Type | Description | Particle Size | Morphology | Apparent Density |
---|---|---|---|---|
Gas atomized | Inert gas atomization provides spherical powder | 15-45 μm | Rounded | ∼1.6 g/cc |
Water atomized | Water breaking up of melt forms irregular particles | 15-100 μm | Jagged, porous | ∼1.2 g/cc |
Plasma atomized | Smooth, spherical nano-to-micron powder from plasma | 5-45 μm | Very spherical | ∼2 g/cc |
Mechanical alloyed | High-energy ball milling blendes and refines powder | 15-100 μm | Jagged, composite particles | ∼1.8 g/cc |
Based on final application method, suitable grade is chosen. Smaller sizes below 100 microns allow better powder bed densities and printing resolution.
Composition of aluminium alloy 7050 powder
As an aerospace structural alloy, 7050 composition is:
Element | Weight % | Role |
---|---|---|
Zinc | 5.7 – 6.7% | Major alloying element, improves strength through precipitation |
Magnesium | 1.9 – 2.6% | Strengthening element, forms MgZn2 precipitates |
Copper | 2.0 – 2.6% | Helps fine-tune mechanical properties |
Iron | ≤0.15% | Impurity level, kept low |
Silicon | ≤0.12% | Impurity element |
Chromium | ≤0.04% | Present only as trace impurity |
Manganese | ≤0.05% | Kept low as impurity |
Aluminum | Balance | Base element |
intentional additions of silver, lithium or other elements are sometimes used to modify powder characteristics.
aluminium alloy 7050 powder Properties
Key properties of Al7050 alloy powder suitable for additive manufacturing:
Physical Properties
Property | Value |
---|---|
Density | 2.83 g/cm<sup>3</sup> |
Melting Point | ∼635°C |
Thermal Conductivity | 130 W/m-K |
Specific Heat Capacity | 0.88 J/g-K |
Electrical Resistivity | ∼4.5 μΩ-cm |
CTE | 23 μm/m-K |
Color | Dark gray to black |
Low density coupled with strength makes Al7050 suited for aerospace and aviation sectors enabling weight savings.
Mechanical Properties
Property | As-printed | Heat-treated |
---|---|---|
Tensile Strength | ≥450 MPa | ≥570 MPa |
Yield Strength | ≥400 MPa | ≥500 MPa |
Elongation | ∼8% | ∼10% |
Hardness | ∼150 VPN | ∼195 VPN |
Fatigue Strength | 100 MPa | 230 MPa |
Controlled low-stress heat treatment develops optimal precipitation microstructure enhancing mechanical performance.
Performance Attributes
Parameter | Value | Unit |
---|---|---|
Strength-to-weight ratio | High | MPa/(g/cm<sup>3</sup>) |
Stiffness-to-weight ratio | High | GPa/(g/cm<sup>3</sup>) |
Corrosion Resistance | Good | – |
Weldability | Fair | – |
Conductivity | Excellent | %IACS |
High temperature performance | Good | – |
These characteristics make Al7050 suitable for commercial and defense aerospace applications.
Production of aluminium alloy 7050 powder
Process | Description |
---|---|
Atomization | Molten 7050 alloy is fed into the atomizer. Inert gas (typically nitrogen) or plasma jet is used to break up the liquid metal into fine droplets. Droplets rapidly solidify into spherical powder particles due to the high surface area to volume ratio. Various techniques exist, including: Gas Atomization (GA) – Most common method for 7050 powder production. Plasma Atomization (PA) – Offers finer particle size control. |
Milling | Optional step to further refine particle size and morphology, typically used for powders produced by GA. Mechanical milling uses grinding media to achieve the desired particle characteristics. Cryomilling – A specialized milling process conducted at low temperatures to minimize oxidation and improve powder flow. |
Sieving/Classification | Powder is separated into specific size fractions using sieves or classifiers. Ensures consistent particle size distribution for optimal flow and packing in Additive Manufacturing (AM) processes. |
Mixing (Optional) | Blending powders from different batches to achieve uniform chemistry and properties. |
Quality Control | Powder is rigorously tested to ensure it meets strict specifications for: Chemical composition Particle size distribution Morphology (shape) Flowability Moisture content Oxygen content |
Key Powder Characteristics | Description | Importance for AM |
---|---|---|
Particle Size Distribution | Distribution of powder particle sizes. | Affects packing density, flowability, and final part properties. Typically desired range for 7050 AM is 15-63 microns. |
Morphology | Shape of the powder particles. | Spherical particles offer better flowability and packing compared to irregular shapes. |
Alloy Composition | Specific percentages of elements in the powder. | Determines the mechanical properties, corrosion resistance, and other characteristics of the final part. 7050 powder typically contains Zinc (6%), Magnesium (2%), Copper (2.3%) as key alloying elements. |
Apparent Density | Bulk density of the powder. | Impacts the final density of the printed part. |
Flowability | Ease with which powder flows. | Measured by Hall flow rate. Crucial for uniform layer formation in AM processes. |
Moisture Content | Amount of moisture absorbed by the powder. | Minimizes powder oxidation during storage and AM processing. Typically below 0.1% for 7050 powder. |
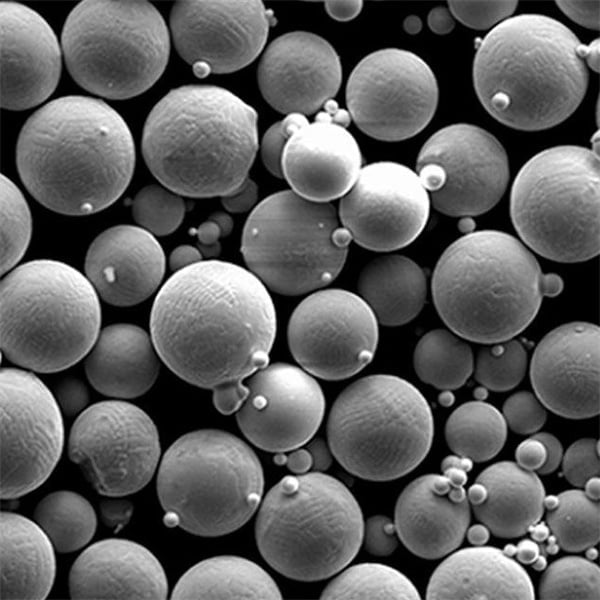
Applications of aluminium alloy 7050 powder
Applications | Properties desired |
---|---|
Aerospace (including aircraft structures, landing gear, and spacecraft components) | High strength, fracture toughness, fatigue strength |
Automotive (including wheels, engine components, and body panels) | High strength, light weight |
Sporting goods (including baseball bats, bicycle frames, and golf clubs) | High strength, good fatigue resistance |
Military applications (including armor, weapons, and vehicles) | High strength, weldability |
Molding and tooling (due to its good dimensional stability and wear resistance) | Dimensional stability, wear resistance |
Electronics (due to its good electrical conductivity) | Electrical conductivity |
Cryogenic applications (due to its good low-temperature strength) | Low-temperature strength |
Marine applications (due to its good corrosion resistance) | Corrosion resistance |
Medical applications (due to its biocompatibility) | Biocompatibility |
Construction (due to its high strength-to-weight ratio) | High strength-to-weight ratio |
aluminium alloy 7050 powder Specifications
Aluminum Alloy 7050 Powder Specifications
Property | Description | Typical Value | Units |
---|---|---|---|
Chemical Composition | Aluminum alloy 7050 powder is a high-strength aluminum alloy containing several key elements in specific proportions. | Aluminum (Al): Balance Zinc (Zn): 5.7 – 6.7% Magnesium (Mg): 2.0 – 2.6% Copper (Cu): 2.0 – 2.5% Other elements (Si, Fe, Mn, Cr, Ti, Zr): ≤ 0.15% total | wt% |
Particle Morphology | The shape and surface characteristics of the powder particles influence their flowability, packing density, and printability. | Spherical or near-spherical | |
Particle Size Distribution | The size of the powder particles plays a crucial role in determining the surface finish, mechanical properties, and overall quality of the final printed part. | Typically offered in a range of sizes, such as 15-45 μm, 45-100 μm, or 100-150 μm. Narrower size distributions may be desired for specific applications. | μm |
Apparent Density | This refers to the bulk density of the powder, considering the spaces between particles. | Approximately 2.6 – 2.8 g/cm³ | g/cm³ |
Tap Density | Tap density represents the density of the powder after a standardized tapping process to minimize voids. | Slightly higher than apparent density, typically around 3.0 – 3.2 g/cm³ | g/cm³ |
Flowability | Good flowability is essential for even powder deposition in additive manufacturing processes. | Spherical morphology and appropriate particle size distribution contribute to good flowability. | |
Mechanical Properties (wrought equivalent) | While the exact properties can vary depending on the manufacturing process and post-processing techniques, 7050 aluminum powder generally offers excellent mechanical properties comparable to wrought (bulk) 7050 aluminum. | Yield Strength: 415 – 475 MPa Tensile Strength: 500 – 570 MPa Elongation: 12 – 18% | MPa, % |
Grades
Per MPIF 35 standards based on particle size:
Grade | Particle Size |
---|---|
Ultrafine | 1 – 20 μm |
Very Fine | 15 – 45 μm |
Fine | 25 – 75 μm |
Relatively Coarse | 53 – 105 μm |
Ultrafine and very fine Al7050 suitable for laser-based fusion.
Standards
- ASTM B233 – Standard for Aluminum Powder and Flake for Thermal Spraying
- MPIF 35 – Standard for Aluminum and Aluminum Alloy Powders
- ISO 22053 – Determination of particle size of metal powders used for additive manufacturing
Pricing of aluminium alloy 7050 powder
Representative pricing, 2023:
Grade | Price |
---|---|
Ultrafine | $45 – $55 per kg |
Very Fine | $35 – $50 per kg |
Fine | $18 – $35 per kg |
Coarse | $12 – $25 per kg |
Higher sphericity, smaller and narrow distribution powder sizes command premium pricing.
Pros and Cons of Aluminum Alloy 7050 Powder
Pros | Cons |
---|---|
High Strength: Aluminum alloy 7050 powder boasts excellent strength properties, exceeding those of other commonly used aluminum alloys for additive manufacturing like 6061 or 7075. This makes it suitable for applications requiring high load-bearing capacity, such as aerospace components or structural parts. | Limited Ductility: Compared to some other aluminum alloys, 7050 powder exhibits lower ductility, meaning it has a reduced ability to deform plastically before fracture. This can be a drawback for applications requiring some degree of flexibility or bendability. |
Good Corrosion Resistance: 7050 aluminum powder offers good resistance to corrosion, particularly for applications involving saltwater environments. The presence of zinc and magnesium in the alloy contributes to this enhanced corrosion performance. | Post-Processing Requirements: To achieve the optimal mechanical properties of 7050 aluminum, parts printed with 7050 powder often require post-processing steps like hot isostatic pressing (HIP). This adds complexity and cost to the manufacturing process. |
Lightweight: As with all aluminum alloys, 7050 powder offers a significant weight advantage compared to heavier materials like steel or titanium. This makes it ideal for weight-critical applications in aerospace, automotive, and other industries. | Higher Cost: Aluminum alloy 7050 powder can be more expensive than some other aluminum powders due to the additional elements included in the alloy and the potential need for specialized manufacturing processes. |
Excellent Weldability: 7050 aluminum powder exhibits good weldability, allowing for the joining of 3D printed parts or the creation of hybrid structures combining additively manufactured components with traditionally fabricated elements. | Anisotropy: Similar to other metal alloy powders, parts printed with 7050 powder can exhibit anisotropic properties. This means their mechanical strength can vary depending on the printing direction. Careful design considerations are necessary to mitigate this effect. |
Tailorable Properties: The specific properties of 7050 aluminum powder can be influenced by adjustments in the manufacturing process, such as powder atomization parameters and heat treatment techniques. This allows for some degree of customization to achieve desired characteristics for a particular application. | Safety Precautions: Aluminum alloy 7050 powder, like most metal powders, can pose safety hazards during handling. Proper ventilation, personal protective equipment, and adherence to safety protocols are essential to minimize risks. |
aluminium alloy 7050 powder Suppliers
Prominent Al7050 powder manufacturers include:
Company | Location |
---|---|
Alpoco | UK |
AMC Powders | Germany |
Makin Metal Powders | UK |
Sandvik Osprey | UK |
PyroGenesis | Canada |
TLS Technik | Germany |
These and secondary LPF machine suppliers provide application-specific Al7050 powder lots to industrial buyers.
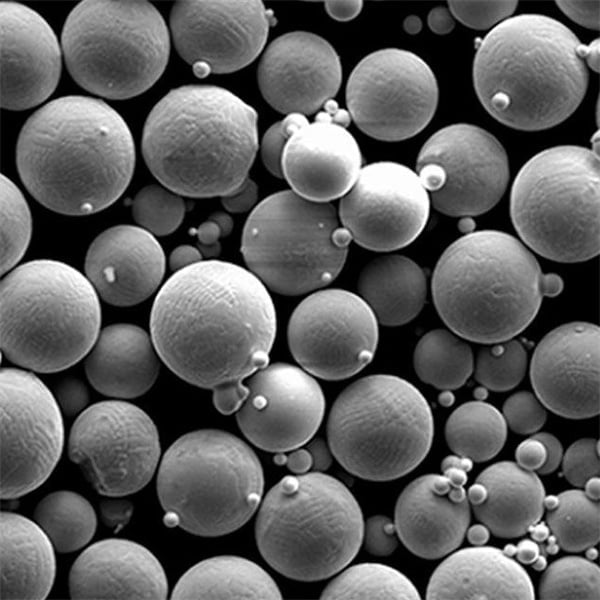
FAQs
Question | Answer |
---|---|
What is aluminium alloy 7050 powder? | Spheroidal gas or water atomized powder of the 7xxx series aerospace alloy with primary alloying additions of zinc and magnesium |
What is 7050 alloy powder used for? | Additive manufacturing of lightweight structural components for aviation, automotive and marine applications |
What is the typical composition of Al7050 powder? | ∼6% zinc, ∼2.5% magnesium, ∼2.4% copper balanced by aluminium plus trace elements like Fe, Si, Mn. |
What are the different varieties of Al7050 powder? | Gas atomized, water atomized, plasma atomized and mechanically alloyed powder |
What are the properties of Al7050 alloy powder? | Density – 2.83 g/cm<sup>3</sup>; tensile strength – over 500 MPa; hardness – 150 to 200 VPN; excellent strength-to-weight ratio; moderate corrosion resistance |
What is the typical particle size of Al7050 powder for additive manufacturing? | 15 to 45 microns classified into Very Fine grade size |
Does Al7050 powder require deoxidation or spheroidization before use? | Desirable to have lower than 50 to 100 ppm oxygen content; sphericity over 0.9 preferred |
Is Al7050 hazardous during handling and storage? | No major hazards, but inhalation of fine powder can cause respiratory irritation |
Summary
With a potent blend of high strength, respectable fracture toughness and moderate corrosion resistance, aluminum 7050 alloy demonstrates attractive properties from among nonferrous powder options for additive manufacturing. Careful attention to powder quality and recyclability promises exceptional in-service structural performance once components are processed via latest generation large powder bed systems.
As aluminum alloys gain wider acceptance across aviation, rocketry and premium automotive sectors, Al7050 powder will spearhead manufacturability of complex lightweight shapes and lattices hitherto unviable, backing new levels of functionality.
Share On
MET3DP Technology Co., LTD is a leading provider of additive manufacturing solutions headquartered in Qingdao, China. Our company specializes in 3D printing equipment and high-performance metal powders for industrial applications.
Inquiry to get best price and customized Solution for your business!
Related Articles
About Met3DP
Recent Update
Our Product
CONTACT US
Any questions? Send us message now! We’ll serve your request with a whole team after receiving your message.
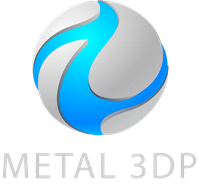
Metal Powders for 3D Printing and Additive Manufacturing