Aluminium Alloy Powder
Table of Contents
Aluminium alloy powder refers to powder metallurgy forms of aluminium alloys. Aluminium powders find use in various applications due to their lightweight, high strength, corrosion resistance, thermal conductivity, and electrical conductivity.
Overview of Aluminium Alloy Powder
Aluminium alloy powder is produced by atomization of molten alloys into fine droplets which solidify into powder particles. The composition and properties of the alloy powder can be tailored based on requirements.
Key details about aluminium alloy powder:
- Produced by atomization of aluminium alloys into fine powder
- Particle size ranges from few microns to millimeters
- Spherical, irregular, or flake particle shapes
- Variety of alloying elements used – Si, Mg, Zn, Cu etc.
- Properties dependent on alloy composition
- Lightweight, high strength, corrosion resistance
- Used for additive manufacturing, thermal spray, MIM etc.
Aluminium Alloy Powder Types
Type | Composition | Characteristics |
---|---|---|
Pure Al | 99%+ Al | Low strength, high electrical conductivity |
1000 series | Al + Mn, Fe, Si | Work-hardenable, higher strength |
2000 series | Al-Cu | Heat treatable, high strength |
5000 series | Al-Mg | Moderate to high strength |
6000 series | Al-Mg-Si | Medium to high strength |
7000 series | Al-Zn | Highest strength |
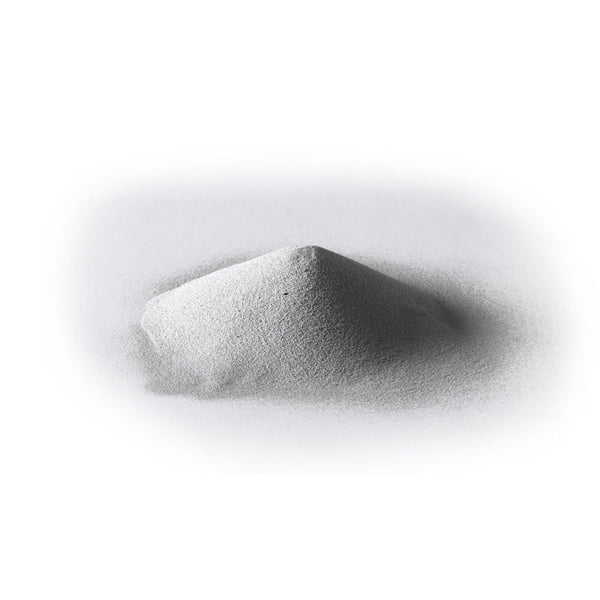
Aluminium Alloy Powder Composition
Aluminium alloy powders contain aluminium as the base metal along with alloying elements. Some common alloy additions include:
Alloy Series | Primary Alloying Elements | Applications | Properties Enhanced by Alloying Elements |
---|---|---|---|
1XXX Series | > 99% Aluminium (Al) | * Electrical conductors * Heat exchangers * Food packaging | * High electrical conductivity * Excellent formability * Superior corrosion resistance |
2XXX Series | Al + Copper (Cu) (Up to 5.5%) | * Aerospace components * Busbars * Automotive parts | * Increased strength * Improved machinability * Good weldability |
3XXX Series | Al + Manganese (Mn) (Up to 1.3%) | * Building and construction materials * Signs and panels * Storage tanks | * Enhanced work hardening * Superior formability * Excellent brazeability |
4XXX Series | Al + Silicon (Si) (Up to 12%) | * Engine blocks * Cylinder heads * Welding wires | * Excellent casting characteristics * Low coefficient of thermal expansion * Wear resistance |
5XXX Series | Al + Magnesium (Mg) (Up to 5.6%) | * Shipbuilding * Pressure vessels * Chemical storage tanks | * High strength-to-weight ratio * Excellent corrosion resistance * Good weldability |
6XXX Series | Al + Magnesium (Mg) + Silicon (Si) (Up to 1 Mg & 0.6 Si) | * Aircraft structures * Bridges * Transportation components | * Excellent machinability * Good strength * Superior formability |
7XXX Series | Al + Zinc (Zn) (Up to 6.5%) | * Aircraft wings * Sporting goods * High-strength fasteners | * High strength * Good fatigue resistance * Wear resistance (with additional alloying elements) |
8XXX Series | Al + Lithium (Li) (Up to 12%) | * Aerospace components requiring very low weight * High-performance vehicles | * Extremely low density * High strength-to-weight ratio * Limited applications due to high cost and processing challenges |
Aluminium Alloy Powder Characteristics
Aluminium Alloy Powder Characteristics
Property | Description | Benefits in Additive Manufacturing |
---|---|---|
Particle Size & Distribution | Aluminium alloy powders are available in a range of particle sizes, typically between 10 and 150 micrometers. The distribution of these particle sizes within the powder bed is also crucial. | Particle size and distribution significantly impact the final properties of the additively manufactured part. <br> – Finer particles generally create smoother surface finishes but can be more challenging to process due to increased flowability issues and higher surface area for oxidation. <br> – Larger particles improve flowability but may result in a rougher surface finish and potential porosity within the finished part. <br> – A tight particle size distribution with minimal variation ensures consistent packing density and minimizes internal stresses within the printed part. |
Particle Shape | The shape of the aluminium alloy powder particles can influence packing density, flowability, and the final microstructure of the additively manufactured component. | – Spherical particles pack more efficiently, leading to higher density and potentially improved mechanical properties. <br> – Irregularly shaped particles can create interlocking features that improve layer adhesion but may also lead to higher internal stresses and potential cracking. |
Powder Flowability | Powder flowability refers to the ease with which the powder particles can move and spread within the machine’s build chamber. | Good flowability is essential for ensuring consistent layer deposition and accurate part geometry. <br> – Powders with poor flowability can lead to uneven deposition, inconsistencies in density, and potential printing defects. |
Apparent Density | The apparent density of an aluminium alloy powder is the mass of powder per unit volume, taking into account the spaces between the particles. | Apparent density is a crucial factor in determining the amount of material required for a specific build volume and can influence the shrinkage of the part during the printing process. |
Packing Density | Packing density refers to the ratio of the solid volume of the powder particles to the total volume occupied by the powder. | Packing density is typically lower than apparent density due to the presence of voids between particles. Higher packing density generally leads to improved mechanical properties in the final part. |
Chemical Composition | The specific alloying elements present in the aluminium powder significantly influence the final properties of the additively manufactured part. Common alloying elements include silicon, copper, magnesium, manganese, and zinc. | The selection of the appropriate aluminium alloy powder depends on the desired properties of the finished part, such as strength, corrosion resistance, and heat resistance. <br> For instance, adding copper can enhance strength but reduce corrosion resistance. |
Surface Chemistry | The surface chemistry of the aluminium alloy powder particles can impact their flowability, reactivity, and bonding during the printing process. | A thin oxide layer naturally forms on the surface of aluminium particles. <br> – Surface modification techniques can be employed to improve flowability and promote inter-particle bonding during the additive manufacturing process. |
Moisture Content | Aluminium alloy powders are hygroscopic, meaning they readily absorb moisture from the surrounding environment. | Excessive moisture content in the powder can lead to hydrogen porosity within the additively manufactured part, negatively impacting mechanical properties. <br> – Proper storage and handling techniques are crucial to maintain low moisture levels in the powder. |
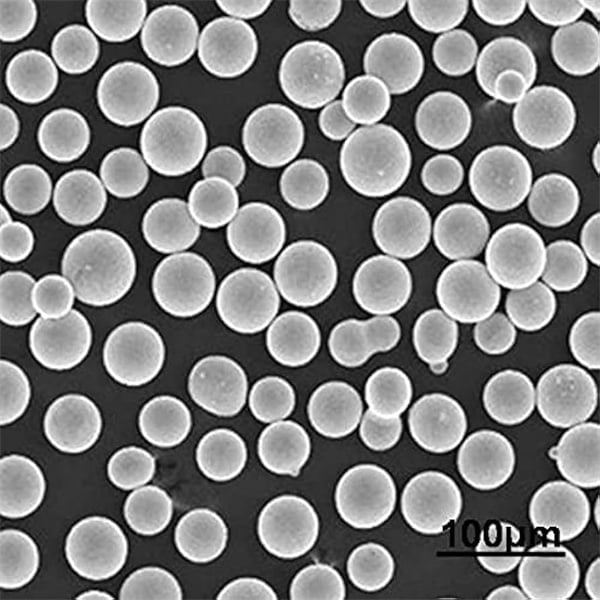
Aluminium Alloy Powder Applications
Application | Description | Advantages of Aluminium Alloy Powders | Limitations |
---|---|---|---|
Aerospace Components | Aluminium alloy powders are widely used for additively manufacturing (AM) of high-performance aerospace components due to their excellent strength-to-weight ratio and favorable mechanical properties. Common applications include: – Aircraft fuselages and wing components – Engine components – Satellite structures | – Lightweight construction: Aluminium alloys offer significant weight reduction compared to traditional materials like steel, enabling improved fuel efficiency and payload capacity in aerospace vehicles. – Design freedom: AM allows for the creation of complex, lightweight structures with internal channels and lattices that are difficult or impossible to achieve with conventional manufacturing methods. – Performance tailoring: Specific aluminium alloys can be chosen to meet the demanding requirements of aerospace applications, such as high strength, good fatigue resistance, and excellent corrosion resistance. | – Powder cost: Aluminium alloy powders can be more expensive than some alternative materials used in aerospace, such as titanium alloys. – Surface roughness: While AM processes are continuously improving, additively manufactured aluminium components may still exhibit a rougher surface finish compared to machined parts. Post-processing techniques like machining or polishing may be required for certain applications. |
Automotive Components | Aluminium alloy powders are finding increasing use in AM for the production of lightweight and complex automotive components. Examples include: – Structural components like brackets and housings – Heat sinks for power electronics – Customised engine components | – Weight reduction: Aluminium AM components contribute to improved fuel efficiency and overall vehicle performance. – Functional integration: AM allows for the design and creation of parts with integrated functionalities, reducing the number of components and simplifying assembly processes. – Performance optimization: Aluminium alloys can be chosen to provide specific properties like high strength for structural components or good thermal conductivity for heat sinks. | – Part qualification: Extensive testing and certification may be required for safety-critical automotive parts produced via AM. – Production volume: While AM is increasingly used for prototyping and short-run production, its scalability for high-volume automotive manufacturing is still under development. |
Medical Implants | Aluminium alloy powders with biocompatible properties are being explored for AM of customized medical implants, such as: – Bone repair plates and screws – Dental implants – Prosthetic components | – Biocompatibility: Certain aluminium alloys exhibit good biocompatibility, minimizing the risk of rejection by the human body. – Customization: AM enables the creation of patient-specific implants that perfectly match individual anatomy, improving implant fit and function. – Porous structures: Porous aluminium structures created via AM can promote bone ingrowth and improve implant osseointegration (bonding with bone). | – Limited range of biocompatible alloys: Currently, only a few aluminium alloys are considered biocompatible for medical applications. – Mechanical properties: Some aluminium alloys may not possess the necessary strength or fatigue resistance for certain high-load bearing implants. – Regulatory requirements: Strict regulatory approval processes must be followed for medical devices produced via AM. |
Consumer Electronics | Aluminium alloy powders are used for AM of various components in consumer electronics due to their good thermal conductivity and lightweight properties. Examples include: – Heat sinks for electronic devices – Lightweight enclosures for laptops and mobile phones | – Thermal management: Aluminium’s good thermal conductivity helps dissipate heat generated by electronic components, improving device performance and reliability. – Lightweight design: Aluminium AM components contribute to the overall weight reduction of electronic devices, enhancing portability and user experience. | – Limited strength: Pure aluminium or some aluminium alloys may not be suitable for structural components requiring high strength. – Surface finish: Similar to other AM applications, surface roughness may require additional post-processing for certain aesthetic requirements. |
Additive Manufacturing Using Aluminium Alloy Powder
Some benefits of AM with Al alloy powder:
Benefit | Description | Impact |
---|---|---|
Design Freedom & Complexity | Additive manufacturing (AM) allows for the creation of intricate and complex geometries that are difficult or impossible to achieve with traditional manufacturing techniques like machining or casting. Aluminium alloy powders further enhance this design freedom due to their flowability and ability to be selectively melted or bound. | – Lightweight structures: AM enables the design of lightweight components with internal lattices and channels, optimizing strength-to-weight ratios for applications like aerospace and automotive. – Functional integration: Parts can be designed with integrated functionalities, reducing the need for multiple components and simplifying assembly processes. – Customization: AM allows for the creation of customized parts tailored to specific needs, such as patient-specific medical implants or bespoke consumer electronics enclosures. |
Material Efficiency & Reduced Waste | Unlike traditional subtractive manufacturing methods that generate significant scrap material, AM with aluminium alloy powder offers a more sustainable approach. Material is only used where needed during the layer-by-layer build process, minimizing waste. | – Reduced environmental impact: Lower material consumption translates to a smaller environmental footprint compared to traditional manufacturing processes. – On-demand manufacturing: AM allows for the production of parts on-demand, eliminating the need for large inventories and potentially reducing transportation requirements. |
Rapid Prototyping & Short-Run Production | AM with aluminium alloy powder excels in rapid prototyping, enabling the swift creation of functional prototypes for design verification and testing. Additionally, AM facilitates short-run production of complex parts without the need for expensive tooling, making it ideal for low-volume applications. | – Faster product development cycles: Rapid prototyping allows for quicker design iterations and feedback loops, accelerating the product development process. – Reduced time-to-market: AM enables the production of parts on-demand, eliminating long lead times associated with traditional manufacturing methods. – Cost-effective for low volumes: For low-volume production runs, the cost of AM with aluminium alloy powder can be competitive compared to traditional methods that require tooling investment. |
Performance Tailoring & Lightweighting | A wide range of aluminium alloys are available in powder form, each offering distinct properties like strength, corrosion resistance, and thermal conductivity. This allows for the selection of the optimal aluminium alloy powder to achieve the desired performance characteristics for a specific application. | – Lightweighting for performance: Aluminium’s inherent lightweight nature, coupled with the design freedom of AM, enables the creation of lighter components that improve fuel efficiency in vehicles or payload capacity in aerospace applications. – Functional optimization: Specific aluminium alloys can be chosen to meet the performance demands of an application. For instance, high-strength alloys can be used for structural components, while alloys with good thermal conductivity are ideal for heat sinks. |
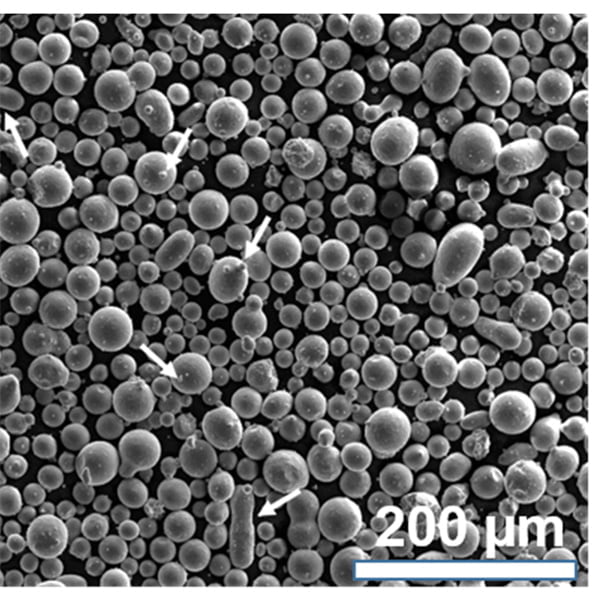
Current Limitations in AM Using Al Powder
Aspect | Limitation | Impact | Potential Solutions |
---|---|---|---|
Powder characteristics | Irregular particle shape and size distribution | Inconsistent laser absorption, poor flowability, increased porosity in final parts | Development of more efficient atomization techniques for spherical powders, tighter control over particle size distribution |
Powder flowability | Poor flow can hinder uniform spreading | Inconsistent layer density, weak inter-layer bonding | Utilizing flowability agents or vibratory systems to improve powder spreading, exploring alternative powder bed fusion techniques like binder jetting |
Powder recyclability | Limited reuse cycles due to oxidation and contamination | Increased material cost, environmental impact | Development of closed-loop powder management systems with integrated cleaning and sieving processes, exploring Al alloys less susceptible to oxidation |
Surface quality | High surface roughness due to unmelted particles | Post-processing steps required, potential for fatigue crack initiation | Laser parameter optimization for improved melting efficiency, exploring alternative finishing techniques like shot peening or electropolishing |
Mechanical properties | Porosity can lead to reduced strength and ductility | Parts may not meet design requirements | Utilizing hot isostatic pressing (HIP) for pore closure, exploring laser post-processing techniques like melt pool refinement |
Residual stress | Rapid solidification can induce high residual stress | Increased risk of warping and cracking | Preheating the powder bed, optimizing laser scan strategies to minimize thermal gradients, utilizing stress relief heat treatments |
Cost | High cost of Al powder production | Limits the economic viability for certain applications | Development of more energy-efficient atomization techniques, exploring alternative manufacturing methods for simpler geometries |
Environmental impact | High energy consumption during powder production | Increased carbon footprint | Research into green AM techniques like cold spray or binder jetting with water-based binders, exploring the use of recycled aluminum sources |
Part size limitations | Build volume restrictions of AM machines | Large-scale aluminum components cannot be readily produced | Development of larger AM machines with higher build volumes, exploring hybrid AM techniques for combining functionalities |
Design considerations | Need for design optimization for AM | Conventional design rules may not translate directly | Development of design guidelines and software tools specific for AM of Al components, promoting knowledge sharing and best practices within the AM community |
Metal Injection Molding with Aluminium Alloy Powder
Metal injection molding (MIM) can produce complex, tight tolerance, net-shape metallic components using aluminium alloy powder feedstock at relatively low costs.
Benefits of MIM with aluminium alloy powder
Feature | Benefit | Example Application |
---|---|---|
Complex Geometries | Aluminum alloy MIM excels at producing intricate shapes with tight tolerances. Unlike traditional casting methods, MIM isn’t limited by mold parting lines, allowing for undercuts, thin walls, and internal channels. | Miniature gears in a medical device with interlocking teeth and internal lubricant channels. |
High Volume Production | MIM offers a cost-effective solution for high volume production of small metal parts. The injection molding process allows for rapid cycle times and minimal post-processing, leading to significant cost savings compared to machining intricate components. | Electrical connectors for consumer electronics with complex pin configurations, produced in large quantities. |
Material Versatility | A wide range of aluminum alloys can be used in MIM, each offering unique properties. This allows for selection based on the specific needs of the application, such as high strength (e.g., Al7075), good corrosion resistance (e.g., Al5052), or excellent thermal conductivity (e.g., Al6061). | Lightweight heat sinks for electronic devices, utilizing Al6061 for efficient heat dissipation. |
Net-Shape Manufacturing | MIM parts require minimal post-processing after sintering. Near-final dimensions are achieved directly from the mold, minimizing the need for additional machining or finishing steps. | Biosensor components with integrated microfluidic channels, requiring high precision and minimal post-processing for biocompatibility. |
Lightweighting | Aluminum alloys are inherently lightweight, making MIM ideal for applications where weight reduction is critical. This is particularly beneficial in aerospace, automotive, and consumer electronics industries. | Structural components in drones, leveraging the high strength-to-weight ratio of Al alloys produced via MIM. |
Design Freedom | MIM allows for the integration of multiple features into a single component. This reduces assembly complexity, improves part functionality, and potentially lowers overall production costs. | Multi-functional valve components for fluidic systems, combining flow control elements, filters, and pressure regulation features. |
Improved Surface Finish | MIM parts typically have a smooth surface finish, reducing the need for additional polishing or finishing steps. This can be crucial for applications requiring a high degree of surface quality, such as medical implants or optical components. | Biocompatible bone screws with a smooth surface finish to promote tissue integration and minimize infection risks. |
Material Efficiency | MIM utilizes a near net-shape manufacturing process, minimizing material waste compared to traditional machining techniques. This benefit aligns with sustainable manufacturing practices. | Production of complex gears and sprockets with minimal scrap material, promoting resource conservation. |
Limitations for MIM using aluminium powders
Factor | Limitation | Impact |
---|---|---|
Sintering Challenges | Aluminum’s high reactivity with oxygen can lead to the formation of surface oxides during the sintering process. These oxides hinder particle bonding, resulting in lower mechanical strength and increased porosity compared to MIM parts made from other materials like steel. | Components requiring high structural integrity or pressure resistance may not be suitable for aluminum MIM due to potential strength limitations. |
Powder Characteristics | Aluminum powders used in MIM are typically finer than those used for other metals. This fine particle size can make it difficult to achieve good flowability in the feedstock, potentially leading to injection molding defects like surface roughness or incomplete part filling. | Strict control over powder characteristics and careful optimization of the feedstock recipe are necessary to ensure successful part production. |
Part Size Restrictions | Due to the high shrinkage that occurs during sintering (up to 20% for aluminum), the size and complexity of parts that can be effectively manufactured using aluminum MIM are limited. Large or intricate components may be prone to cracking or warping. | Aluminum MIM is best suited for small to medium-sized parts with relatively simple geometries. |
Cost Considerations | While MIM offers cost advantages for high-volume production, the upfront costs associated with tooling and powder development can be significant. Additionally, aluminum powders for MIM are typically more expensive than some other metal powders. | For low-volume applications, traditional machining or alternative manufacturing techniques might be more cost-effective. |
Post-Processing Requirements | Although near-net shapes are achievable, aluminum MIM parts may still require some post-processing steps like deburring, heat treatment, or surface finishing depending on the specific application requirements. | These additional steps can add to the overall manufacturing time and cost. |
Material Property Limitations | Compared to some other metals suitable for MIM, aluminum alloys generally have lower strength and wear resistance. This can restrict their use in applications demanding high mechanical performance under harsh operating conditions. | Aluminum MIM parts may not be suitable for applications requiring high loads, extreme temperatures, or abrasive environments. |
Surface Roughness | While MIM aluminum parts can achieve good surface finishes, they might not be as smooth as those achievable with some other metalworking techniques. This can be a limitation for applications requiring exceptional surface quality for aesthetic or functional reasons. | Smoothing or polishing steps might be necessary for certain applications. |
Limited Alloy Selection | The range of aluminum alloys available for MIM is currently smaller compared to other metals commonly used in this process. This restricts the ability to tailor material properties for specific performance needs. | Ongoing research and development are expanding the selection of aluminum alloys suitable for MIM, but options may still be limited compared to other materials. |
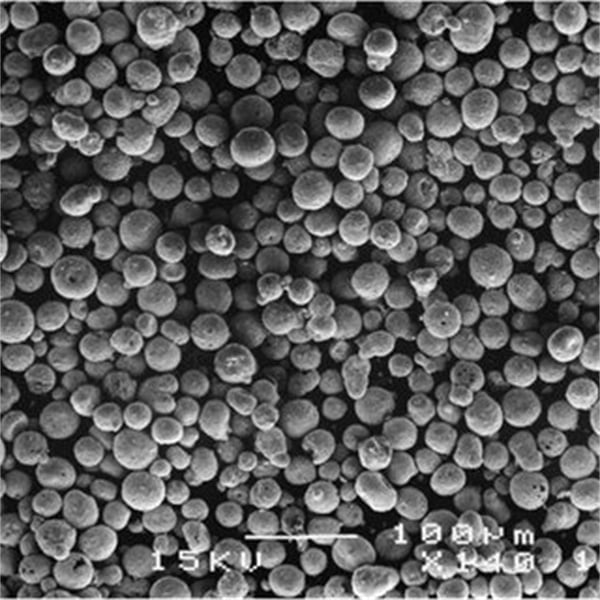
Aluminium Alloy Powder for Thermal Spray
Property | Description | Advantages | Disadvantages |
---|---|---|---|
Alloy Composition | Aluminium alloy powders come in a variety of compositions, each offering distinct properties. Common alloying elements include silicon (Si), magnesium (Mg), copper (Cu), and manganese (Mn). | – Si: Improves wear resistance and castability. – Mg: Reduces weight and enhances corrosion resistance. – Cu: Increases strength and thermal conductivity. – Mn: Improves workability and high-temperature strength. | – Selection depends heavily on the desired end properties of the coating. – Specific alloy knowledge is required for optimal choice. |
Particle Size & Morphology | The size and shape of the powder particles significantly impact the coating characteristics. Powders range from finer than 10 microns to coarses exceeding 100 microns, with spherical or irregular morphologies. | – Fine Powders (< 45 microns): Produce denser coatings with smoother surfaces, ideal for applications requiring wear resistance and corrosion protection. – Coarser Powders (> 45 microns): Offer faster deposition rates and improved bond strength, suitable for rebuilding worn components. – Spherical Powders: Enhance flowability and packing efficiency, leading to more uniform coatings. – Irregular Powders: May create a rougher surface but can improve mechanical interlocking within the coating. | – Finer powders require specialized thermal spray equipment for proper feeding. – Coarser powders might result in higher porosity within the coating. |
Thermal Spray Technique | Different thermal spray processes utilize aluminium alloy powders with varying degrees of effectiveness. Common techniques include: – High-Velocity Oxy-Fuel (HVOF) – Plasma Spray (PS) – Cold Spray (CS) | – HVOF: Delivers high particle velocities, resulting in dense coatings with excellent wear and corrosion resistance. Well-suited for Si- and Cu-alloyed powders. – PS: Offers process versatility for a wider range of aluminium alloy powders. – CS: Utilizes lower particle temperatures, minimizing metallurgical changes in the powder and reducing residual stress in the coating. More suitable for Mg-alloyed powders. | – Selection depends on the powder’s melting point and desired coating properties. – Each technique has its own limitations in terms of deposition rate, coating thickness, and cost. |
Surface Preparation | The substrate’s surface condition significantly influences the adhesion and performance of the thermal spray coating. | – Ensures a clean and roughened surface for optimal mechanical bonding. – Techniques like grit blasting or grit etching are commonly employed. | – Improper surface preparation can lead to weak bonding and premature coating failure. |
Coating Properties | Aluminium alloy thermal spray coatings offer a unique combination of properties: – Electrical Conductivity: Varies depending on the alloy composition. Pure aluminium offers the highest conductivity, while Si and Mg additions can reduce it. – Thermal Conductivity: Generally lower than the bulk aluminium but can be improved with certain alloying elements like Cu. – Corrosion Resistance: Aluminium itself exhibits good corrosion resistance, further enhanced by Mg additions. – Wear Resistance: Improved by Si and Cu additions, making the coating suitable for wear applications. | – Tailored to meet specific application requirements through alloy selection and process optimization. – Trade-offs exist between different properties; for example, maximizing wear resistance might compromise electrical conductivity. | |
Applications | Aluminium alloy thermal spray coatings find use in diverse industries due to their versatility: – Automotive: Pistons, cylinder heads, brake calipers (for wear resistance and heat dissipation). – Aerospace: Landing gear components, airframe components (for corrosion protection and weight reduction). – Electronics: Heat sinks, electrical busbars (depending on the chosen alloy for conductivity). – Chemical Processing: Chemical vessels, pipes (for corrosion resistance). | – Offer a cost-effective solution for component repair, performance enhancement, and service life extension. – Material selection and process control are crucial for achieving desired outcomes in each application. |
Aluminium Alloy Powder Specifications
Aluminium alloy powders are produced according to various standard specifications that define the acceptable composition limits, particle size ranges, shape control etc.
Standard | Description |
---|---|
AMS 4200 | Aerospace material specification for atomized Al alloy powder |
ASTM B602 | Standard specification for Al alloy powders |
EN 1706 | European standard specification for atomized Al powders |
ISO 13318 | International standard for gas and water atomized Al powders |
DIN 50125 | German national standard for atomized Al powders |
Specifications allow customers to procure powder suitable for their specific application and process requirements.
Sizes of Aluminium Alloy Powder
Various size ranges of aluminium alloy powder are produced depending on end use:
- Ultrafine powder < 10 microns for reactive applications
- Fine powder 15 – 45 microns commonly for thermal spray
- Medium powder 45 – 100 microns widely used size
- Coarse powder up to 150 microns for specialty applications
Larger particles over 180 microns mainly used in cold spray processes for thicker coatings. Control of particle size distribution is also important for some applications.
Grades of Aluminium Alloy Powder
Aluminium alloy powder is manufactured into different established grades based on the alloy type:
- 1xxx series powders – AA1100, AA1350
- 2xxx series powders – AA2014, AA2024, AA2219, AA2519
- 5xxx series powders – AA5083, AA5654
- 6xxx series powders – AA6061, AA6082
- 7xxx series powders – AA7050, AA7075
Higher number series indicate higher alloying levels and strength. Custom alloy compositions are also possible for proprietary grades.
Aluminium Alloy Powder Comparison
Parameter | Cold Gas Atomization | Water Atomization |
---|---|---|
Particle shape | Highly spherical | More irregular, satellites |
Particle size range | 15 – 180 microns | 5 – 350 microns |
Size distribution | Tighter control | Wider distribution |
Apparent density | Higher | Lower |
Production rate | Lower | Higher |
Cost | Higher | Lower |
Water atomized powders tend to have a cost advantage but suffer from less sphericity and broader particle distributions compared to gas atomized aluminium alloy powder.
Aluminium Alloy Powder Standards
Key standards for aluminium alloy powder:
Standard | Organization | Description |
---|---|---|
AMS4200 | SAE | Aerospace material specification |
ASTM B602 | ASTM | Chemical compositions and sieve sizes |
EN1706 | CEN | European standard specification |
ISO13318 | ISO | International standard for gas atomized and water atomized forms |
Various national and organizational standards help ensure quality and consistency of aluminium alloy powder supply.
Global Suppliers of Aluminium Alloy Powder
Supplier | Location | Capabilities |
---|---|---|
Valimet Inc. | USA | Wide range of atomization, large capacity |
Sandvik Osprey | UK | Leading supplier of controlled powders |
TLS Technik GmbH | Germany | Specialist in gas and water atomized powders |
Fukuda Metal Foil & Powder Co. | Japan | Broad alloy offerings |
SCM Metal Products | Singapore | Focus on aluminum and copper alloys |
Pricing for Aluminium Alloy Powders
Price for aluminum alloy powder varies based on:
- Alloy grade and characteristics
- Particle shape and size specifications
- Purchase quantity and lot size
- Regional tariffs and transportation
Type | Price Range |
---|---|
1xxx series | $5 – $15 per kg |
2xxx series | $10 – $30 per kg |
5xxx series | $15 – $35 per kg |
6xxx series | $20 – $40 per kg |
7xxx series | $30 – $60 per kg |
Prices above are approximate ranges for reference purpose only. Contact suppliers for exact current pricing based on your specific needs.
Advantages and Limitations of Aluminium Alloy Powder
Advantages | Limitations |
---|---|
High Strength-to-Weight Ratio | Powder Handling |
Aluminium alloy powder offers exceptional strength for its weight. This makes it ideal for applications where weight reduction is critical, such as aerospace components, automotive parts, and prosthetics. Compared to traditional metals like steel, aluminium alloy powder parts can achieve similar strength levels while significantly reducing overall weight. | Aluminium alloy powder, particularly finer grades, can be challenging to handle due to its flowability and potential for dust explosions. Specialized handling equipment and precautions are necessary to ensure safe and efficient powder management during storage, transportation, and additive manufacturing processes. |
Complex Geometries | Surface Roughness |
Aluminium alloy powder thrives in additive manufacturing (AM) techniques like 3D printing. Unlike traditional subtractive manufacturing methods that remove material to create a desired shape, AM builds parts layer-by-layer from the powder. This allows for the creation of intricate, lightweight components with complex geometries that would be difficult or impossible to achieve with conventional methods. | Parts produced using aluminium alloy powder can exhibit a slightly rougher surface finish compared to machined components. While post-processing techniques like polishing or blasting can improve surface texture, these steps add to the overall manufacturing time and cost. |
Material Versatility | Material Cost |
A wide variety of aluminium alloys can be used in powder form, each with its own unique properties. This allows engineers to tailor the material selection to the specific requirements of the application. For instance, some alloys prioritize high strength, while others offer superior corrosion resistance or improved machinability after fabrication. | Aluminium alloy powder can be more expensive than traditional aluminium ingots or wrought products. This is partially due to the additional processing steps involved in powder production and the specialized handling requirements. However, the benefits of AM, such as reduced material waste and near-net-shape manufacturing, can offset the higher material cost in some applications. |
Near-Net-Shape Manufacturing | Isotropic Properties |
Additive manufacturing with aluminium alloy powder enables near-net-shape manufacturing. This means the final component shape is achieved with minimal post-processing waste. This reduces material consumption and streamlines the production process compared to conventional methods that often involve significant material removal. | Parts fabricated from aluminium alloy powder may exhibit slightly anisotropic properties, meaning their mechanical strength can vary depending on the build direction. This is because the powder particles tend to align along the build direction during the AM process. However, advancements in powder technology and AM techniques are continuously improving the isotropy of aluminium alloy components. |
Recyclability | Environmental Impact |
Aluminium alloy powder offers excellent recyclability. Similar to traditional aluminium scrap, used powder can be reprocessed and reused in AM processes, minimizing waste and promoting sustainable manufacturing practices. | The production of aluminium alloy powder can be energy-intensive, and depending on the energy source used, it might have a higher environmental footprint compared to traditional manufacturing methods. However, ongoing research focuses on developing more energy-efficient powder production techniques to reduce the environmental impact. |
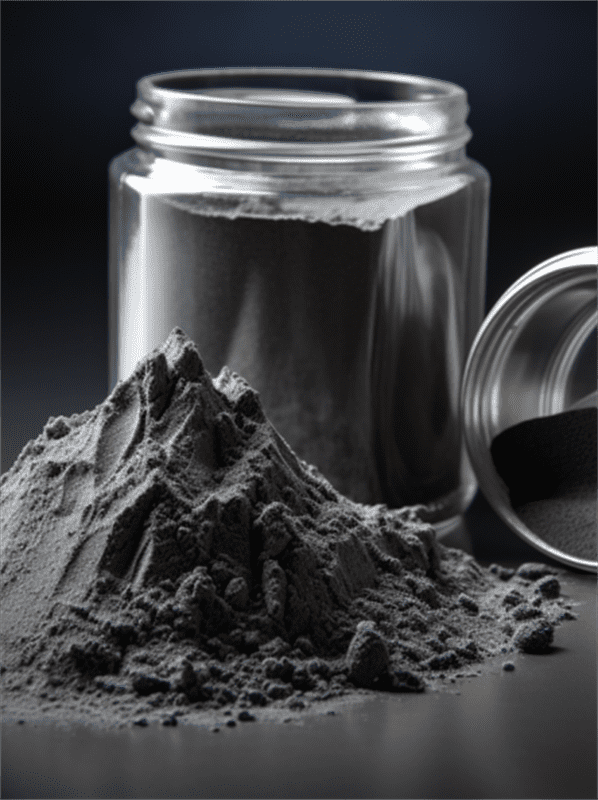
FAQs
What are the most common alloys used as aluminium alloy powder?
The most common alloy powders are: 2xxx series such as 2014 and 2024, 5xxx alloys like 5083, 6xxx alloys including 6061 and 6082, and 7xxx alloys with 7050 and 7075 being popular.
What particle size is best for metal injection molding using aluminium powders?
A particle size range between 15-45 microns is typically recommended for metal injection molding using aluminium alloy powders.
What types of atomization processes can produce aluminium alloy powder?
Gas atomization and water atomization are the two main industrial processes used. Rotating disk atomization method can also produce aluminum powders.
What is the benefit of using 5xxx series aluminum alloys for thermal spraying?
5xxx series Al alloys like 5083 have excellent corrosion resistance while remaining dimensionally stable at elevated temperatures making them suitable for thermal spray coatings for marine and chemical exposures.
What affects the pricing of aluminum alloy powder?
The alloy composition, particle characteristics like size and shape, order volume, regional tariffs and transportation costs determine the final pricing from different aluminum powder suppliers.
What standards apply to aluminum alloy powders for additive manufacturing uses?
Key standards include ASTM B602, AMS4200, EN1706, and ISO 13318. Additional AM-specific standards are under development to address process-related requirements.
Can aluminum alloy powder be reused?
Reusing aluminum powder is generally not recommended for critical applications. Storage conditions can allow moisture pickup and oxidation limiting powder performance. Minor reuse may be possible in non-critical applications with appropriate testing.
Are higher number aluminum alloys always stronger than lower number alloys?
In general, higher number 2xxx, 6xxx, and 7xxx series powders have higher strength than 1xxx or 5xxx alloys, but significant overlap can exist based on exact composition, powder characteristics and processing history. Always check supplier data for guaranteed powder properties.
Why is porosity and anisotropy a concern for AM made aluminum components?
High thermal conductivity and reflectivity of aluminum combined with rapid solidification during laser or e-beam melting hinders optimal fusion and gas bubble escape leading to defects. Different mechanical properties parallel and transverse to build layers also arise.
Can I mix different aluminum alloy powders to create custom grades?
It is generally not advisable to mix powders to create intermediate or custom alloys due to risks of incomplete mixing, alloy reactions, or inadequate particle bonding during part manufacture. Consult closely with your powder supplier when exploration property combinations.
Share On
MET3DP Technology Co., LTD is a leading provider of additive manufacturing solutions headquartered in Qingdao, China. Our company specializes in 3D printing equipment and high-performance metal powders for industrial applications.
Inquiry to get best price and customized Solution for your business!
Related Articles
About Met3DP
Recent Update
Our Product
CONTACT US
Any questions? Send us message now! We’ll serve your request with a whole team after receiving your message.
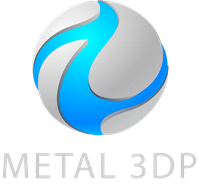
Metal Powders for 3D Printing and Additive Manufacturing