Atomized Metal Powder
Table of Contents
Atomized metal powders refer to metallic materials like aluminum, titanium, nickel, iron or alloys that have been reduced to fine spherical powder form through an atomization process. They exhibit high purity, consistent particle sizes, and powder morphology ideal for industrial applications like metal injection molding (MIM) and additive manufacturing.
This guide covers different types of atomized metal powders, production methods, key properties and characteristics, technical specifications, pricing estimates, supplier details as well as pros, cons and common FAQs when working with precisely engineered, atomized metallic powders across 3D printing, injection molding and other fabrication processes.
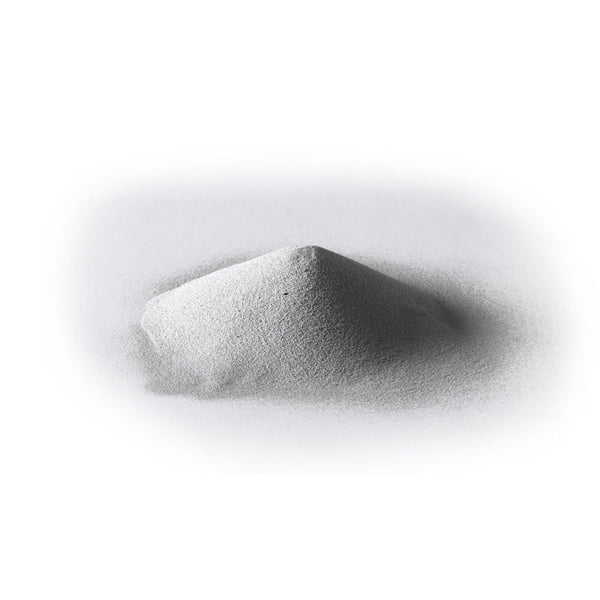
Types of Atomized Metal Powder
Common base metals and alloys available as atomized spherical powders include:
Material | Alloys | Characteristics |
---|---|---|
Aluminum | 6061, 7075, 2024, 7050, | Lightweight, moderate strength |
Titanium | Ti-6Al-4V, Ti 6Al-7Nb | Optimized strength-to-weight ratio |
Nickel | Inconel 718, Invar 36, Kovar | Heat/corrosion resistant options |
Stainless steel | 316L, 430F, 17-4PH | Rust resistant, high hardness variants |
Copper | C11000, Brass, Bronze | High thermal and electrical conductivity |
Properties can be tailored across corrosion resistance, hardness, strength, ductility, operating temperatures and other attributes by alloying mixtures.
Production Methods
Method | Process Description | Particle Size & Morphology | Advantages | Disadvantages | Applications |
---|---|---|---|---|---|
Water Atomization | Molten metal is forced through a nozzle at high pressure and broken up into fine droplets by a high-velocity water jet. The droplets rapidly solidify in contact with the cooling water to form a powder. | 5 μm – 2 mm; Irregular, often with dendritic structures | – Lowest cost among atomization methods – High production rate – Suitable for a wide range of metals | – Powder characteristics can be less uniform – Rougher surface finish on particles – Potential for oxidation due to water exposure | – Low-cost components – Bearings – Gears – Filters |
Gas Atomization | Molten metal is forced through a nozzle at high pressure into an inert gas environment (usually argon or nitrogen). The high-velocity gas stream breaks the metal stream into fine droplets that solidify rapidly due to the rapid cooling. | 10 μm – 1 mm; Smooth, spherical shapes | – Produces high-quality, spherical powders – Consistent particle size distribution – Minimal oxidation | – Higher cost compared to water atomization – Limited range of metals suitable for the process | – Additive manufacturing (3D printing) – High-performance components – Aerospace parts – Medical implants |
Centrifugal Atomization | Molten metal is contained in a rapidly rotating mold. The centrifugal force throws the molten metal outward towards the periphery of the mold, where it breaks up into droplets due to the high shear forces. The droplets then solidify in a controlled atmosphere. | 10 μm – 150 μm; Generally spherical, but can have some irregular shapes | – Produces fine powders – Suitable for reactive metals – Minimal contamination | – Lower production rate compared to other methods – Can be a complex process to control | – Powders for metal injection molding (MIM) – Electronic components – Hardfacing materials |
Plasma Rotating Electrode Process (PREP) | A consumable electrode (usually a rod or disk) is rotated at high speed and melted by a plasma torch. The centrifugal force throws the molten metal droplets outward, which rapidly solidify in an inert gas environment to form a powder. | 10 μm – 100 μm; Highly spherical and clean | – Produces high-purity, spherical powders – Excellent for reactive metals – Tight control over particle size distribution | – Very high cost – Limited production capacity | – High-performance aerospace components – Turbine blades – Medical implants |
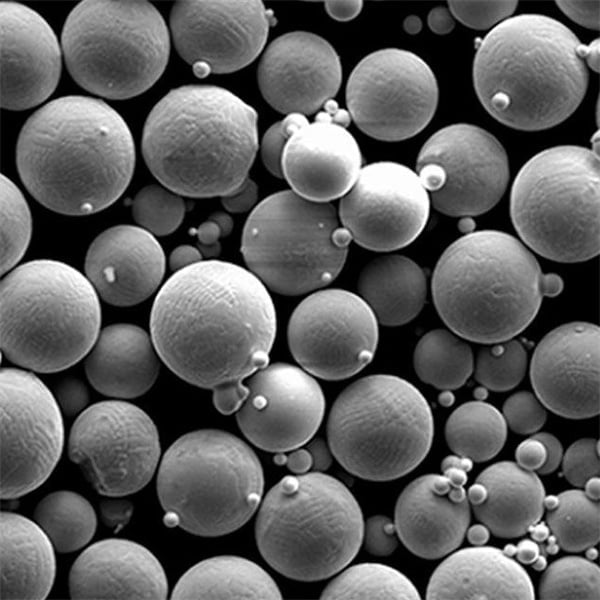
Properties of Atomized Metal Powders
Benefits of these precisely shaped and sized metallic microspheres:
Property | Characteristics | Advantages |
---|---|---|
Controlled particle size | Majority of powder in narrow 5-45 micron range | Optimized flow and packing for sintering consistency |
High sphericity | Powder balls exhibit very round shape with smooth surface | Improves final density and surface finish quality |
Consistent chemistry | Precisely formulated alloys during production | Reliable material performance batch to batch |
High purity | Inert processing without contamination | Necessary for biocompatible implants and electronics |
Modified surfaces | Coatings or lubricants can be added | Improves powder flow and reduces caking risks |
These powders represent ideal raw materials shaped by cutting edge manufacturing means to enable emerging fabrication techniques reshaping industrial production across sectors through enhanced precision.
Applications of Atomized Metal Powders
Major uses of precision spherical metallic powders:
Industry | Applications | Benefits |
---|---|---|
Additive manufacturing | 3D printed aerospace, automotive, medical parts | Excellent flowability through fine powder spreading and recoating mechanisms |
Metal injection molding | Small complex part series for drones, robots, turbines | High purity and consistent chemistry yields reliable material performance |
Electronic packaging | Circuits, sensors, connectors | Sintered porous structures aid miniaturization while allowing functional material infiltrations |
Thermal spraying | Protective anti-corrosive coatings for bridges, pipelines | Dense coatings with bonding optimized particle morphology |
Powder metallurgy | Self-lubricating bearings, filters, magnets | Net and near net shape fabrication simplifies manufacturing steps |
The precision particle engineering behind atomized powders combined with specialized process expertise unlocks game changing production innovations across these key sectors.
Specifications
Standard | Definitions | Common Values |
---|---|---|
ASTM B214 | Sieve Analysis for particle upper limit percentages | -325 mesh = less than 45 microns |
ASTM B822 | Apparent density g/cm3 | Around 35-50% as loose powder |
ASTM B964 | Flow rate second/50g | 15 – 25 seconds range |
ASTM F3049 | Chemistry inclusions content max ppm limits | Fe 300 ppm, O 1500 ppm, N 100 ppm |
International specifications help set consistent baselines defining acceptable material quality and purity thresholds for proper powder performance during loading and sintering stages across various fabrication techniques.
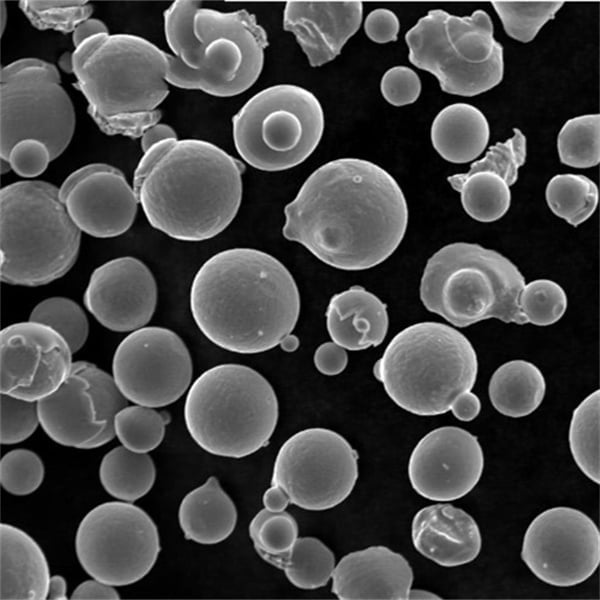
Suppliers and Pricing
Metal | Typical Applications | Reputable Suppliers (Global) | Price Range (USD per Kilogram) | Key Considerations |
---|---|---|---|---|
Aluminum (Al) | – Additive manufacturing – Thermal spraying – Metal injection molding (MIM) | – Höganäs AB (Sweden) – AP Powder Company (US) – AMETEK Inc. (US) | $1 – $10 | – Purity (affects conductivity and reactivity) – Particle size and distribution ( влияет (vliyaniyet) on flowability and packing density) – Surface morphology (affects performance in AM) |
Titanium (Ti) | – Aerospace parts (e.g., turbine blades) – Biomedical implants – High-performance sporting goods | – ATI (Allegheny Technologies Incorporated) (US) – BHP (Broken Hill Proprietory) (Australia) – POLEMA (Germany) | $50 – $300 | – Grade (commercially pure, alloyed) – Oxygen content (critical for some applications) – Minimum order quantity (MOQ) can be high |
Nickel (Ni) | – Electronic components (e.g., capacitors) – Catalysts – Battery electrodes | – AMI Metals (UK) – Sumitomo Metal Industries (Japan) – China Nonferrous Metal Mining Group (China) | $10 – $200 | – Chemical composition (presence of impurities) – Flowability (important for processing) – Country of origin (may impact lead times and regulations) |
Iron (Fe) | – Powder metallurgy components (e.g., gears) – Welding consumables – Friction materials (e.g., brake pads) | – Hoeganaes AB (Sweden) – Höganäs Belgium NV (Belgium) – GKN Powder Metallurgy (Germany) | $1 – $5 | – Apparent density – Compressibility (affects final part properties) – Reduction of oxides (improves performance) |
Cobalt (Co) | – Hardfacing alloys – Cutting tools – Magnetic components | – Höganäs AB (Sweden) – Hunan Shunkang Technology Co., Ltd. (China – Sandvik AB (Sweden) | $150 – $300 | – Particle size distribution ( влияет (vliyaniyet) on packing and sintering) – Sphericity ( влияет (vliyaniyet) on flowability) – Moisture content (can affect processing) |
Copper (Cu) | – Electrical conductors – Heat sinks – Brazing alloys | – AMETEK Inc. (US) – Carpenter Technology Corporation (US) – JX Nippon Mining & Metals Corporation (Japan) | $5 – $20 | – Oxygen content (can affect conductivity) – Surface area ( влияет (vliyaniyet) on reactivity) – Morphology ( влияет (vliyaniyet) on packing density) |
Pros and Cons
Pros | Cons |
---|---|
Excellent morphological control through cutting edge manufacturing methods | Potentially high material price points, especially for highly customized alloys |
Unlocks disruptive part fabrication techniques like binder jetting and DED additive printing | Limited large volume capacity compared to conventional metal production like casting and forging |
Simplifies downstream operations through high purity and flowability | Requires handling expertise and precautions to prevent oxidation risks |
Expands range of alloys tailored to demanding applications | Supply chain volatility as niche producers balance small batches |
Enables complex geometries impossible through subtractive techniques | Post processing often needed to achieve final material properties |
The precise control over powder shape, size, distribution and chemistry conveys tremendous advantages but specialized handling and processing considerations must be addressed.
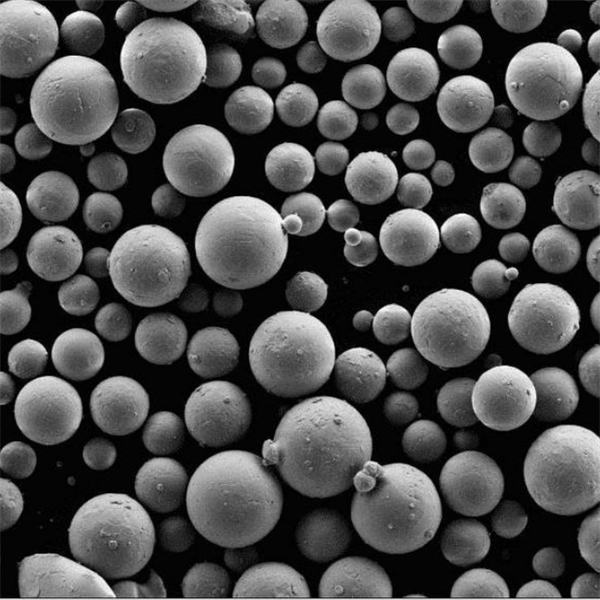
Limitations and Considerations
Aspect | Limitation/Consideration | Impact | Mitigation Strategies |
---|---|---|---|
Particle Characteristics | Particle size distribution: Wide size distribution can lead to uneven packing density and affect final product properties. | Inconsistent material performance, potential for defects. | Utilize classification techniques to achieve a narrower size range. Optimize atomization parameters for better control. |
Particle morphology: Irregular or non-spherical particles can hinder flowability and packing efficiency. | Reduced powder flowability, difficulties in achieving high packing density. | Implement shaping processes like gas atomization for more spherical shapes. Optimize atomization parameters to minimize particle fragmentation. | |
Surface area: High surface area due to fine particles can increase reactivity and oxidation susceptibility. | Moisture absorption, reduced powder shelf life, potential for material degradation. | Maintain a dry, inert storage environment. Implement moisture control measures during handling. Consider using oxygen-getters in storage containers. | |
Material Properties | Oxidation: Rapid cooling during atomization can trap oxides within the particles or form an oxide layer on the surface. | Reduced ductility, altered mechanical properties, potential for internal defects. | Utilize inert gas atomization to minimize oxygen exposure. Implement post-processing techniques like deoxidation to remove oxides. |
Residual porosity: Internal voids within particles can impact strength and fatigue resistance. | Reduced mechanical performance, potential for crack initiation. | Optimize atomization parameters to minimize trapped gas. Utilize consolidation techniques like hot isostatic pressing (HIP) to close porosity. | |
Microstructure: Rapid solidification can result in non-equilibrium microstructures with potentially detrimental effects. | Reduced strength, toughness, and corrosion resistance. | Control cooling rates during atomization to promote desired microstructural features. Implement post-processing techniques like annealing to refine the microstructure. | |
Handling and Processing | Flowability: Poor flowability can hinder effective powder feeding in additive manufacturing processes. | Inconsistent powder deposition, potential for process disruptions. | Utilize flowability enhancers or lubricants. Optimize particle size and shape for better flow characteristics. |
Safety: Fine metal powders can be flammable or explosive under certain conditions. | Risk of fire or explosion during handling and storage. | Implement proper handling procedures, including proper grounding and ventilation. Store powders in a safe location away from heat sources and ignition sources. | |
Environmental impact: Production and handling of metal powders can generate dust and potential environmental contaminants. | Air and water pollution concerns. | Implement dust collection systems during atomization. Utilize closed-loop powder handling systems to minimize environmental impact. |
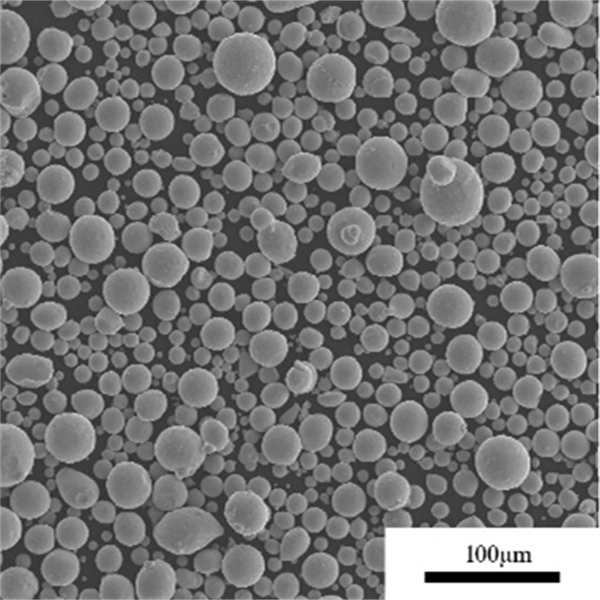
FAQ
Question | Answer |
---|---|
What is the main advantage over water atomized metal powder? | More precise control over particle shape and size distribution consistency |
What is the typical bulk density? | Around 2-4 g/cc is common depending on alloy and particle sizes |
What is flow rate measured in? | Sec/50g gives indication of powder morphological flow through equipment |
What particle size testing is used? | Laser diffraction particle size analyzers in liquid suspensions |
How is chemistry tested? | ICP-OES or GDMS methods used to validate elemental compositions |
Does the powder have unlimited shelf life? | Generally over 5 years if kept sealed from oxygen/moisture, retest after 2-3 years |
What care is needed when handling? | Inert environment glove boxes for Titanium, appropriate PPE for other reactive metals |
What are common applications? | MIM, Binder jetting and DED AM are leading uses currently |
Proper handling and testing processes combined with matched customer application requirements will drive continuing adoption of atomization technology across fabricated metal parts production.
Conclusion
The advanced manufacturing prowess required to mass produce precisely engineered metallic microspheres unlocks tremendous fabrication possibilities across industrial sectors. By leveraging processes like gas atomization to control critical powder characteristics like particle size distribution, shape, purity and chemistry, engineers can take full advantage of emerging techniques like additive manufacturing to simplify production flows. And specialized alloy variants expand the design envelope across challenging temperature, pressure and caustic operating environments. Combine that with lower waste compared to machining processes and simplified logistics through enhanced metal powders shelf life, and innovative businesses are just starting to tap the potential through increased R&D investments tailored to application needs. But proper handling and safety considerations around reactive elemental powders remains mandatory. As additive manufacturing continues its growth trajectory into full scale certified production across aerospace, medical implantation and automotive innovators, expect precise atomization technology to play a crucial role supplying raw materials differentiating leading manufacturers through access to customized, qualified alloys.
Share On
MET3DP Technology Co., LTD is a leading provider of additive manufacturing solutions headquartered in Qingdao, China. Our company specializes in 3D printing equipment and high-performance metal powders for industrial applications.
Inquiry to get best price and customized Solution for your business!
Related Articles
About Met3DP
Recent Update
Our Product
CONTACT US
Any questions? Send us message now! We’ll serve your request with a whole team after receiving your message.
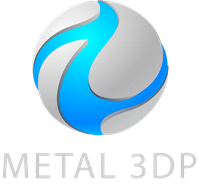
Metal Powders for 3D Printing and Additive Manufacturing
COMPANY
PRODUCT
cONTACT INFO
- Qingdao City, Shandong, China
- [email protected]
- [email protected]
- +86 19116340731