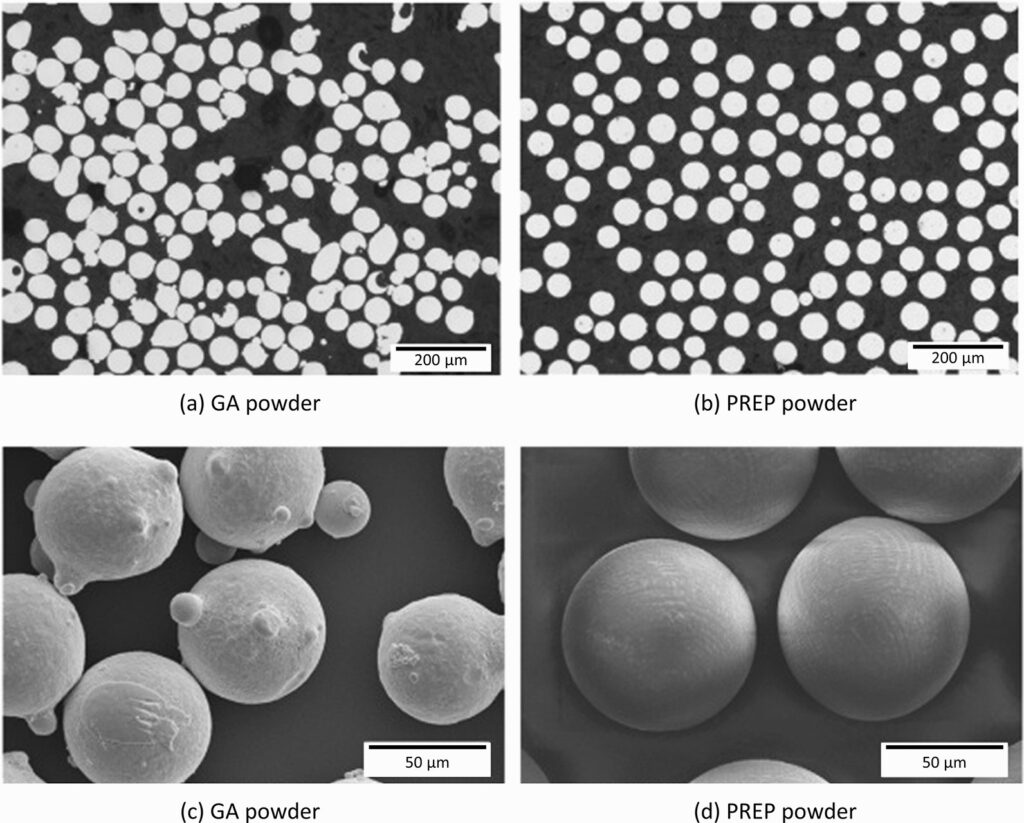
Atomized Spherical Mg-Gd-Zr Alloy Powder: Perfect Balance of Strength and Weight
Low MOQ
Provide low minimum order quantity to meet different needs.
OEM & ODM
Provide customized products and design services to meet unique customer needs.
Adequate Stock
Ensure fast order processing and provide reliable and efficient service.
Customer Satisfaction
Provide high quality products with customer satisfaction at the core.
share this article
Table of Contents
Overview of Atomized Spherical Mg-Gd-Zr Alloy Powder
If you’re on the lookout for a material that’s lightweight yet strong, corrosion-resistant, and capable of withstanding high temperatures, look no further than Atomized Spherical Mg-Gd-Zr Alloy Powder. This innovative alloy combines the best properties of magnesium (Mg), gadolinium (Gd), and zirconium (Zr) to deliver outstanding performance for modern engineering applications.
What makes this material stand out? Its atomized spherical powder form. Unlike irregularly shaped powders, the spherical particles ensure better flowability, packing density, and uniformity, making it ideal for additive manufacturing, thermal spraying, and powder metallurgy. With its high strength-to-weight ratio and excellent thermal stability, it’s no wonder that industries like aerospace, automotive, and medical technology are turning to this alloy for their most demanding projects.
In this article, we’ll dive deep into the world of atomized spherical Mg-Gd-Zr alloy powder. From its types and composition to its applications, advantages, and pricing, this comprehensive guide will give you everything you need to know. Whether you’re an engineer, manufacturer, or researcher, understanding this material could be the key to unlocking new possibilities in your field.
Types, Composition, and Properties of Atomized Spherical Mg-Gd-Zr Alloy Powder
Let’s start by breaking down the essential details about Mg-Gd-Zr alloy powder: its types, chemical composition, and the properties that make it such a sought-after material.
Types of Atomized Spherical Mg-Gd-Zr Alloy Powder
Type | Description |
---|---|
High-Purity Mg-Gd-Zr Powder | Premium-grade powder with minimal impurities for consistent performance in critical applications. |
Fine-Particle Mg-Gd-Zr Powder | Ultra-fine particles (<50 µm) for high-precision applications, such as medical implants and electronics. |
Coated Mg-Gd-Zr Powder | Features oxidation-resistant coatings to enhance storage and processing stability. |
Custom Mg-Gd-Zr Powder | Tailored compositions and particle sizes to meet specific industry requirements, such as aerospace components. |
Composition of Atomized Spherical Mg-Gd-Zr Alloy Powder
The unique properties of this alloy come from its carefully balanced composition. Here’s a breakdown of the key elements:
Element | Typical Proportion (%) | Function in the Alloy |
---|---|---|
Magnesium (Mg) | ~90-94% | Provides lightweight properties and good machinability. |
Gadolinium (Gd) | 4-8% | Improves high-temperature strength, creep resistance, and corrosion resistance. |
Zirconium (Zr) | 0.5-1% | Enhances grain refinement and overall mechanical properties. |
Key Properties of Atomized Spherical Mg-Gd-Zr Alloy Powder
Property | Details |
---|---|
Density | ~1.8-1.9 g/cm³, making it significantly lighter than traditional metals like aluminum or steel. |
Melting Point | ~540–640°C, suitable for medium- to high-temperature applications. |
Thermal Conductivity | High, ensuring effective heat dissipation in thermal management applications. |
Corrosion Resistance | Excellent, especially in marine or humid environments. |
Strength-to-Weight Ratio | Exceptional, ideal for aerospace and automotive applications requiring weight reduction. |
Flowability | Outstanding, thanks to its spherical shape, which ensures smooth processing in manufacturing. |
Oxidation Resistance | Moderate; protective coatings or inert storage are recommended to prevent degradation. |
Applications of Atomized Spherical Mg-Gd-Zr Alloy Powder
The versatility of Mg-Gd-Zr alloy powder makes it a vital material across multiple industries. Here’s how it’s being used to revolutionize manufacturing and engineering.
Common Applications of Atomized Spherical Mg-Gd-Zr Alloy Powder
Industry | Application |
---|---|
Aerospace | Lightweight structural components, aircraft interiors, engine parts, and satellite systems. |
Automotive | High-performance engine components, lightweight chassis, and heat-resistant brake systems. |
Additive Manufacturing | 3D-printed parts for complex geometries in aerospace, medical, and automotive applications. |
Biomedical | Biocompatible implants, such as bone screws and plates, and lightweight prosthetic devices. |
Defense | Lightweight armor and structural components for military vehicles and equipment. |
Electronics | Heat sinks, casings, and other components requiring effective thermal management. |
Example: Mg-Gd-Zr Alloy in Aerospace Applications
In aerospace engineering, weight is a critical factor. By using Mg-Gd-Zr alloy powder, manufacturers can produce lightweight yet durable components for aircraft and spacecraft. For instance, this material is frequently used in engine casings, where its ability to withstand high temperatures and extreme mechanical stress ensures safety and reliability during flight.
Specifications, Sizes, and Standards for Atomized Spherical Mg-Gd-Zr Alloy Powder
When selecting the right material for your project, understanding the available specifications and standards is key.
Specifications and Sizes of Atomized Spherical Mg-Gd-Zr Alloy Powder
Specification | Details |
---|---|
Particle Size Range | Available in various ranges, such as 10-45 µm (fine) and 50-150 µm (coarse). |
Purity | ≥99.5%, ensuring minimal impurities for consistent performance. |
Shape | Perfectly spherical, enhancing flowability and packing density. |
Density | ~1.8-1.9 g/cm³, making it one of the lightest structural materials available. |
Compliance Standards | Meets international standards like ASTM E505 for aerospace and ISO 13485 for medical devices. |
Suppliers and Pricing for Atomized Spherical Mg-Gd-Zr Alloy Powder
Finding a reliable supplier can make all the difference when sourcing Mg-Gd-Zr alloy powder. Pricing varies depending on factors such as particle size, purity, and order volume.
Leading Suppliers and Pricing Information
Supplier | Region | Price Range (per kg) | Specialization |
---|---|---|---|
Advanced Alloy Solutions | USA | $200 – $400 | High-purity powders for aerospace and defense applications. |
Rare Earth Powders Ltd. | Europe | $220 – $450 | Customizable powders for additive manufacturing and biomedical uses. |
Magnesium Alloys Asia | Asia | $180 – $350 | Bulk orders for industrial-scale applications. |
Global Powder Tech | Global | $250 – $500 | Supplies nano-sized powders for high-precision manufacturing. |
Advantages and Limitations of Atomized Spherical Mg-Gd-Zr Alloy Powder
While Mg-Gd-Zr alloy powder has many strengths, it’s important to consider its challenges as well.
Advantages of Atomized Spherical Mg-Gd-Zr Alloy Powder
Advantage | Description |
---|---|
Lightweight | Reduces overall weight in aerospace and automotive applications. |
High-Temperature Resistance | Maintains strength and stability at elevated temperatures. |
Corrosion Resistance | Performs well in harsh environments, such as marine or humid conditions. |
Flowability | Excellent flow properties enable efficient use in additive manufacturing and powder metallurgy. |
Limitations of Atomized Spherical Mg-Gd-Zr Alloy Powder
Limitation | Description |
---|---|
Cost | Higher production costs due to advanced atomization techniques. |
Oxidation Sensitivity | Requires careful storage to prevent degradation over time. |
Limited General Use | Primarily suited for high-performance industries, limiting accessibility for low-cost applications. |
Frequently Asked Questions (FAQ) About Atomized Spherical Mg-Gd-Zr Alloy Powder
Question | Answer |
---|---|
What is Mg-Gd-Zr alloy powder used for? | It’s widely used in aerospace, automotive, and biomedical applications for its lightweight strength. |
How is it stored safely? | Store in airtight containers, away from moisture and oxygen, to prevent oxidation. |
Is it suitable for 3D printing? | Yes, its spherical shape and flowability make it ideal for additive manufacturing. |
What industries benefit most from it? | Aerospace, automotive, defense, and medical industries benefit significantly. |
How much does it cost? | Prices range from $200 to $500 per kilogram, depending on specifications and supplier. |
Conclusion
Atomized Spherical Mg-Gd-Zr Alloy Powder is redefining the possibilities of lightweight materials. With its exceptional strength-to-weight ratio, thermal stability, and corrosion resistance, it’s no surprise that industries like aerospace, automotive, and biomedical are turning to this material for their most demanding projects. While it may come with challenges such as higher costs and oxidation sensitivity, its advantages far outweigh these limitations for applications requiring cutting-edge performance.
Whether you’re designing the next-generation aircraft, developing advanced medical implants, or creating high-precision 3D-printed parts, Mg-Gd-Zr alloy powder is a material worth considering. It’s not just a powder—it’s a solution for the future.
Get Latest Price
About Met3DP
Product Category
HOT SALE
CONTACT US
Any questions? Send us message now! We’ll serve your request with a whole team after receiving your message.
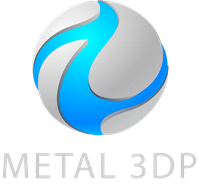
Metal Powders for 3D Printing and Additive Manufacturing