The Application of Binder Jetting in Consumer Electronics
Table of Contents
Imagine a world where your phone case perfectly reflects your unique style, boasting intricate designs and custom engravings. Or picture sleek, lightweight headphone cases that seamlessly integrate with your existing devices. This isn’t science fiction; it’s the exciting reality of binder jetting in consumer electronics.
Binder Jetting: A Manufacturing Revolution
Binder jetting is a 3D printing technique that’s rapidly transforming the manufacturing landscape. Unlike traditional methods that remove material (subtractive), binder jetting builds objects layer-by-layer using a liquid binding agent that glues together powdered materials. This innovative approach offers several advantages for consumer electronics:
- Design Freedom: Binder jetting unlocks unparalleled design flexibility. Complex geometries, intricate details, and even internal channels become easily achievable, pushing the boundaries of what’s possible in consumer electronics.
- Mass Customization: Imagine phone cases with your favorite artist’s signature or earbuds adorned with your initials. Binder jetting empowers manufacturers to produce personalized electronics on a large scale, catering to individual preferences.
- Lightweight Construction: The use of metal powders in binder jetting allows for the creation of incredibly strong yet lightweight components. This translates to sleeker, more portable designs for devices like headphones and wearables.
But what exactly can be created with binder jetting in the realm of consumer electronics? Let’s delve deeper into the exciting possibilities.
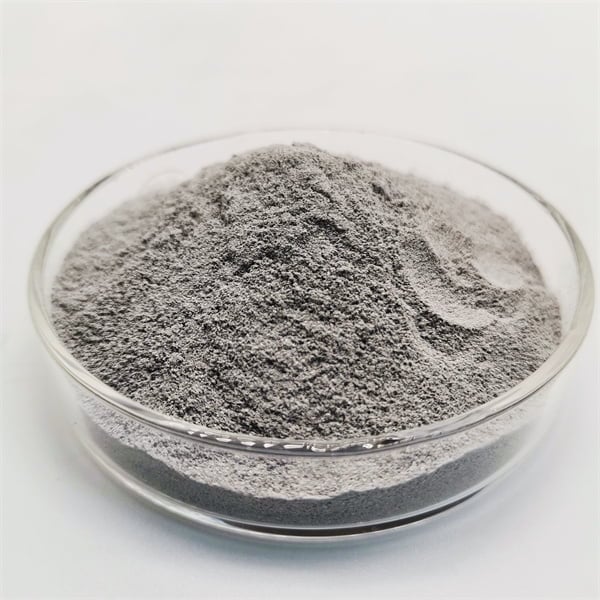
Binder Jetting Applications in Consumer Electronics
Binder Jetting for Personalized Phone Cases: Say goodbye to generic phone covers! Binder jetting can create custom phone cases with intricate designs, logos, or even your favorite characters. Imagine a phone case that reflects your personality and complements your style – the possibilities are endless.
Binder Jetting for Lightweight, Integrated Headphone Cases: Current headphone cases often feel bulky and cumbersome. Binder jetting allows for the creation of lightweight, yet highly durable, headphone cases that seamlessly integrate with the headphones themselves. This not only enhances portability but also creates a sleek, unified aesthetic.
Binder Jetting for Smartwatch Cases with Complex Shapes: Smartwatches are becoming increasingly sophisticated, often boasting curved displays and unique functionalities. Binder jetting’s ability to handle complex geometries perfectly aligns with this trend. Manufacturers can create smartwatch cases with intricate shapes and integrated features, pushing the boundaries of design in this rapidly evolving market.
Binder Jetting for Internal Electronic Components: Beyond the eye-catching exteriors, binder jetting has the potential to revolutionize internal components as well. Imagine intricate heat sinks or customized antenna designs produced using this innovative technique. This could lead to improved device performance and thermal management in a way that traditional manufacturing methods might struggle to achieve.
The Arsenal of Materials: Metal Powders for Binder Jetting
The magic of binder jetting lies not just in the process but also in the materials it utilizes. Here are some of the most promising metal powders being used in consumer electronics applications:
Metal Powder | Description | Properties |
---|---|---|
Stainless Steel 316L | A versatile and widely used austenitic stainless steel known for its excellent corrosion resistance, making it ideal for phone cases and wearable components. | High strength, good ductility, biocompatible. |
Inconel 625 | A high-performance nickel-chromium superalloy known for its exceptional strength and resistance to high temperatures. | Ideal for demanding applications like heat sinks or headphone cases exposed to extreme conditions. |
Titanium (Ti-6Al-4V) | A lightweight and high-strength titanium alloy prized for its excellent biocompatibility and corrosion resistance. | Perfect for creating strong yet lightweight components for wearables like smartwatches. |
Copper | An excellent conductor of electricity and heat, making it a valuable material for internal components. | High thermal and electrical conductivity, readily available. |
Aluminum (AlSi10Mg) | A lightweight and readily available aluminum alloy with good strength and castability. | Commonly used for creating lightweight and affordable components. |
Kovar | A controlled expansion alloy that matches the thermal expansion coefficient of glass, making it ideal for applications involving glass components. | Crucial for components that need to integrate seamlessly with glass displays or other glass elements. |
Tungsten | An incredibly dense and high-melting-point metal known for its exceptional hardness and strength. | Limited use due to high cost but offers unparalleled strength and heat resistance for specialized applications. |
Nickel | A versatile metal with good electrical conductivity and corrosion resistance. | Commonly used for creating electrical components and connectors within consumer electronics. |
Maraging Steel | A high-strength, low-carbon steel known for its excellent toughness and dimensional stability after heat treatment. | Ideal for creating components that require exceptional strength and resistance to deformation. |
Copper-Tin Alloys | These alloys offer a blend of copper’s excellent conductivity with the improved strength and corrosion resistance of tin. | Tailored properties for specific applications like heat sinks or connectors requiring both good electrical performance and durability. |
Choosing the Right Metal Powder
Selecting the ideal metal powder for binder jetting in consumer electronics depends on several factors:
- Desired Properties: Is strength, weight, conductivity, or corrosion resistance the primary concern?
- Application: Are you creating a phone case, a heat sink, or an internal component? Each application has its specific needs.
- Cost Considerations: While some metal powders like stainless steel are readily available and affordable, others like tungsten are considerably more expensive.
The Future of Binder Jetting in Consumer Electronics
Binder jetting is still in its early stages within the consumer electronics industry, but its potential is undeniable. As the technology matures and costs decrease, we can expect to see a wider adoption of this innovative technique. Here are some exciting possibilities for the future:
- Mass Customization on Demand: Imagine walking into a store and having a custom phone case or headphone design printed on the spot using binder jetting. This level of personalization could revolutionize the way we interact with consumer electronics.
- Functional Integration: Binder jetting’s ability to create complex geometries could lead to the integration of multiple functionalities within a single component. Imagine a phone case that doubles as a wireless charger or a smartwatch band that houses additional sensors.
- Sustainable Manufacturing: Binder jetting offers the potential for reduced waste compared to traditional methods. Additionally, the use of metal powders allows for easier recycling of materials, contributing to a more sustainable electronics industry.
Challenges and Considerations
Despite its promise, binder jetting in consumer electronics isn’t without its challenges. Here are some key considerations:
- Post-Processing: Binder jetted parts often require additional post-processing steps like sintering to achieve their final properties. This can add time and cost to the overall manufacturing process.
- Material Limitations: While the range of available metal powders is growing, it’s still not as extensive as with traditional manufacturing methods. This may limit the applications of binder jetting in certain areas.
- Surface Finish: Binder jetted parts may not have the same smooth surface finish as those produced using other techniques. This might necessitate additional finishing steps depending on the desired aesthetics.
Binder Jetting vs. Traditional Manufacturing Techniques
Binder jetting offers several advantages over traditional manufacturing methods like CNC machining or injection molding:
- Design Freedom: Binder jetting excels at creating complex geometries that would be difficult or impossible to achieve with traditional techniques.
- Mass Customization: Binder jetting allows for the production of customized parts without significant cost increases, unlike traditional methods geared towards mass production.
- Reduced Lead Times: Binder jetting can potentially reduce lead times compared to traditional methods, especially for complex designs.
However, traditional methods also have their strengths:
- Surface Finish: Traditional techniques often offer smoother surface finishes compared to binder jetting in its current state.
- Material Availability: A wider range of materials is readily available with traditional methods compared to binder jetting’s current selection of metal powders.
- Established Infrastructure: Traditional manufacturing methods have a well-established infrastructure, making them a more familiar and potentially less risky option for some manufacturers.
The choice between binder jetting and traditional techniques will depend on the specific application and the desired outcome.
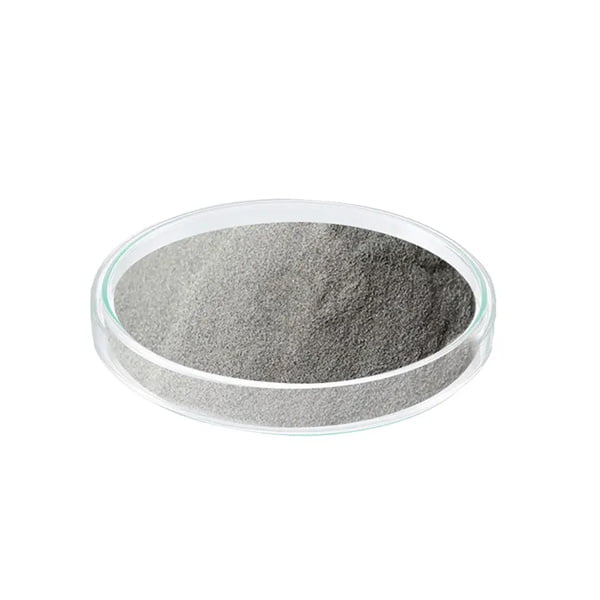
FAQs
What are the benefits of using binder jetting for consumer electronics?
Binder jetting offers several benefits for consumer electronics, including:
- Design freedom for creating complex shapes and intricate details.
- Mass customization for personalized electronics.
- Lightweight construction for sleeker and more portable devices.
- Potential for functional integration of multiple components.
What are the challenges of using binder jetting for consumer electronics?
Some challenges associated with binder jetting in consumer electronics include:
- Post-processing steps that can add time and cost.
- Limited availability of certain metal powders compared to traditional methods.
- Potential for a rougher surface finish compared to some traditional techniques.
Is binder jetting the future of consumer electronics manufacturing?
Binder jetting holds immense potential for the future of consumer electronics manufacturing. As the technology matures and costs decrease, we can expect to see wider adoption and exciting advancements in design, customization, and functionality. However, it will likely co-exist with traditional methods, with the choice depending on the specific application.
Share On
MET3DP Technology Co., LTD is a leading provider of additive manufacturing solutions headquartered in Qingdao, China. Our company specializes in 3D printing equipment and high-performance metal powders for industrial applications.
Inquiry to get best price and customized Solution for your business!
Related Articles
About Met3DP
Recent Update
Our Product
CONTACT US
Any questions? Send us message now! We’ll serve your request with a whole team after receiving your message.
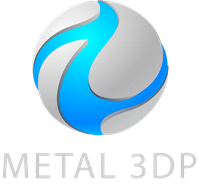
Metal Powders for 3D Printing and Additive Manufacturing