Binder Jetting Additive Manufacturing
Table of Contents
Overview of Binder Jetting Additive Manufacturing
Binder Jetting Additive Manufacturing, often referred to as Binder Jetting, is a groundbreaking technology in the realm of 3D printing. This innovative process involves the use of a binder to selectively join powder particles together to form an object. What makes Binder Jetting unique is its ability to create complex geometries with high precision and speed, making it an attractive option for various industries, including aerospace, automotive, and healthcare. Let’s dive deeper into the specifics of this fascinating technology.
Key Highlights:
- Process: Utilizes a liquid binding agent to adhere layers of powder material.
- Materials: Capable of using a wide range of materials, including metals, ceramics, and polymers.
- Applications: Suitable for producing prototypes, functional parts, and complex structures.
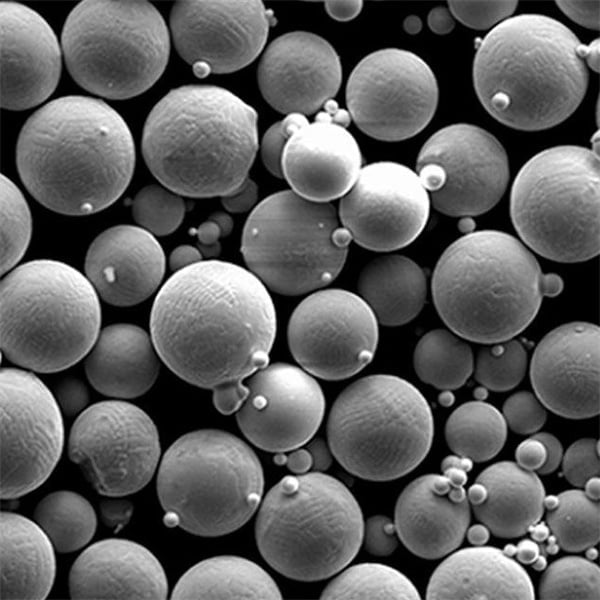
Understanding the Binder Jetting Process
Binder Jetting operates in a layered fashion, where a print head moves across a bed of powder, selectively depositing a binder. Each layer is then cured, and the process repeats until the final object is formed. The unbound powder acts as a support structure, allowing for the creation of intricate designs without the need for additional supports.
Step-by-Step Process:
- Powder Spreading: A thin layer of powder is spread over the build platform.
- Binder Deposition: The print head deposits the binder onto the powder bed according to the design.
- Curing: Each layer is cured to solidify the binder.
- Layering: The process repeats layer by layer until the entire object is built.
- Depowdering: Unbound powder is removed, revealing the finished part.
- Post-Processing: Additional steps such as sintering or infiltration may be required to achieve desired properties.
Types of Metal Powders for Binder Jetting
Common Metal Powders:
Here’s a look at some of the most commonly used metal powders in Binder Jetting, along with their specific characteristics and applications.
Metal Powder | Composition | Properties | Applications |
---|---|---|---|
Stainless Steel 316L | Fe, Cr, Ni, Mo | Corrosion resistance, high ductility | Medical devices, marine components |
Inconel 625 | Ni, Cr, Mo, Nb | High strength, oxidation resistance | Aerospace, chemical processing |
Titanium Ti6Al4V | Ti, Al, V | High strength-to-weight ratio, biocompatibility | Aerospace, biomedical implants |
Aluminum AlSi10Mg | Al, Si, Mg | Lightweight, good thermal properties | Automotive, aerospace |
Cobalt-Chrome (CoCr) | Co, Cr, Mo | Wear resistance, biocompatibility | Dental implants, turbine blades |
Tool Steel H13 | Fe, Cr, Mo, V | Hardness, thermal fatigue resistance | Injection molds, die casting |
Copper (Cu) | Cu | High thermal and electrical conductivity | Heat exchangers, electrical components |
Bronze | Cu, Sn | Good machinability, wear resistance | Art, sculptures, bushings |
Nickel Alloy 718 | Ni, Cr, Fe, Nb | High tensile strength, corrosion resistance | Aerospace, oil and gas |
Tungsten (W) | W | High density, high melting point | Radiation shielding, electrical contacts |
Applications of Binder Jetting Additive Manufacturing
Binder Jetting is versatile and finds applications across various sectors due to its ability to produce complex parts with fine details.
Industries and Uses:
Industry | Applications |
---|---|
Aerospace | Turbine blades, engine components, lightweight structures |
Automotive | Prototypes, functional parts, customized components |
Medical | Surgical instruments, dental implants, orthopedic implants |
Consumer Goods | Jewelry, art, customized items |
Industrial | Molds, tooling, functional prototypes |
Construction | Architectural models, structural components |
Specifications, Sizes, Grades, and Standards
When selecting materials and processes for Binder Jetting, it’s crucial to understand the specifications, sizes, grades, and standards that apply to ensure optimal performance and compliance.
Material Specifications:
Material | Standard | Size Range (Microns) | Typical Grades |
---|---|---|---|
Stainless Steel 316L | ASTM F3184 | 15-45 | Medical grade |
Inconel 625 | ASTM F3055 | 10-50 | Aerospace grade |
Titanium Ti6Al4V | ASTM F2924 | 20-60 | Grade 23 |
Aluminum AlSi10Mg | ISO 5755 | 10-40 | Automotive grade |
Cobalt-Chrome (CoCr) | ASTM F75 | 10-50 | Medical grade |
Tool Steel H13 | ASTM A681 | 20-60 | Tool grade |
Copper (Cu) | ASTM B170 | 15-45 | Electrical grade |
Bronze | ASTM B22 | 20-50 | Standard grade |
Nickel Alloy 718 | ASTM F3055 | 10-50 | Aerospace grade |
Tungsten (W) | ASTM B777 | 20-50 | Industrial grade |
Suppliers and Pricing Details
Knowing where to source materials and understanding the cost implications are crucial for effective Binder Jetting operations.
Suppliers and Pricing:
Supplier | Material | Price (per kg) | Notes |
---|---|---|---|
Carpenter Technology | Stainless Steel 316L | $150 | High-quality powders |
Praxair Surface Technologies | Inconel 625 | $200 | Wide range of alloys |
AP&C | Titanium Ti6Al4V | $300 | Aerospace and medical |
ECKART | Aluminum AlSi10Mg | $100 | Cost-effective |
Hoganas | Cobalt-Chrome (CoCr) | $250 | Medical applications |
Sandvik Osprey | Tool Steel H13 | $180 | Industrial use |
Global Tungsten & Powders | Copper (Cu) | $90 | High purity |
Metal Powder and Process Ltd | Bronze | $120 | Custom formulations |
Advanced Powders & Coatings | Nickel Alloy 718 | $220 | High-performance |
H.C. Starck | Tungsten (W) | $400 | Specialty applications |
Advantages of Binder Jetting Additive Manufacturing
Binder Jetting offers several compelling advantages that make it a preferred choice for various manufacturing needs.
Speed and Efficiency
Binder Jetting can produce parts quickly and efficiently. Unlike some other additive manufacturing methods, Binder Jetting doesn’t require the use of lasers or thermal processes, which significantly speeds up the printing time. This makes it ideal for rapid prototyping and short production runs.
Cost-Effectiveness
The technology is often more cost-effective compared to other 3D printing methods. This is because it uses less energy and can produce parts without the need for expensive support structures. Additionally, the ability to use a wide range of materials, including relatively inexpensive metals, further drives down costs.
Material Versatility
One of the standout features of Binder Jetting is its ability to work with a variety of materials. From metals to ceramics and even composites, Binder Jetting provides manufacturers with the flexibility to choose the best material for their specific application.
Complex Geometries
Binder Jetting excels at producing complex geometries and intricate designs. The layer-by-layer approach allows for the creation of internal structures and fine details that would be challenging or impossible to achieve with traditional manufacturing methods.
Environmental Impact
Binder Jetting is considered to be a more environmentally friendly option. It generates less waste compared to subtractive manufacturing methods and can often use recycled materials, contributing to sustainability efforts.
Advantages Summary:
Advantage | Description |
---|---|
Speed | Rapid production of parts |
Cost-Effective | Lower operational costs |
Material Versatility | Wide range of usable materials |
Complex Geometries | Ability to create intricate designs |
Environmentally Friendly | Reduced waste, sustainable materials |
Disadvantages of Binder Jetting Additive Manufacturing
While Binder Jetting offers numerous benefits, it also has its limitations that must be considered.
Mechanical Properties
Parts produced via Binder Jetting may not always have the same mechanical properties as those made with traditional methods. This is due to the nature of the binding process and the potential need for additional post-processing steps to achieve desired strength and durability.
Surface Finish
The surface finish of Binder Jetting parts can sometimes be rougher compared to other additive manufacturing techniques. This may necessitate additional finishing processes to achieve a smooth surface, adding to the overall production time and cost.
Size Limitations
The build size of Binder Jetting machines can be a limiting factor. Larger parts may require segmentation and subsequent assembly, which can introduce weak points and complicate the manufacturing process.
Binder Selection
The choice of binder can significantly impact the final properties of the part. Some binders may not be suitable for certain applications, requiring careful selection and potentially limiting material compatibility.
Porosity
Binder Jetting can result in porous structures, which may not be suitable for applications requiring airtight or watertight properties. This issue can be mitigated through post-processing techniques, but it adds an extra step to the manufacturing process.
Disadvantages Summary:
Disadvantage | Description |
---|---|
Mechanical Properties | May require post-processing for strength |
Surface Finish | Additional finishing may be needed |
Size Limitations | Build size constraints |
Binder Selection | Impacts material compatibility |
Porosity | Potential for porous structures |
Technical Parameters and Performance Metrics
When evaluating Binder Jetting Additive Manufacturing, it’s important to consider various technical parameters and performance metrics.
Parameter | Description | Typical Values |
---|---|---|
Layer Thickness | Thickness of each printed layer | 50-200 microns |
Build Speed | Rate of part production | Up to 15 mm/hr |
Resolution | Minimum feature size | 50-100 microns |
Binder Type | Type of binding agent used | Various (e.g., aqueous, solvent-based) |
Post-Processing | Additional steps required | Sintering, infiltration |
Material Utilization | Efficiency of material use | Up to 90% |
Comparative Analysis of Binder Jetting Additive Manufacturing
Comparing Binder Jetting with other additive manufacturing methods helps highlight its unique strengths and potential drawbacks.
Parameter | Binder Jetting | SLA (Stereolithography) | SLS (Selective Laser Sintering) |
---|---|---|---|
Speed | High | Moderate | High |
Cost | Moderate | High | Moderate |
Material Range | Broad | Limited | Broad |
Surface Finish | Moderate | High | High |
Complexity | High | High | High |
Post-Processing | Required | Required | Minimal |
Part Strength | Moderate | High | High |
Real-World Examples and Case Studies
Binder Jetting has been successfully implemented in various industries, showcasing its versatility and effectiveness.
Case Studies:
Automotive Industry:
A leading automotive manufacturer used Binder Jetting to produce complex engine components. The technology allowed for rapid prototyping and testing of different designs, significantly reducing the development cycle and costs.
Medical Field:
In the medical field, Binder Jetting was employed to create custom surgical instruments and implants. The ability to produce patient-specific parts with high precision improved surgical outcomes and patient recovery times.
Aerospace Sector:
An aerospace company utilized Binder Jetting to fabricate lightweight yet strong components for aircraft. The technology enabled the production of parts with complex geometries that were both functional and optimized for performance.
Comparative Analysis of Case Studies:
Industry | Application | Outcome |
---|---|---|
Automotive | Engine components | Reduced development time and costs |
Medical | Surgical instruments and implants | Improved precision and patient outcomes |
Aerospace | Aircraft components | Enhanced performance with lightweight structures |
Future Trends and Developments in Binder Jetting
As technology continues to evolve, Binder Jetting is expected to see significant advancements and wider adoption.
Emerging Trends:
- Material Innovation: Development of new materials and binders will expand the range of applications.
- Improved Post-Processing: Advances in post-processing techniques will enhance the mechanical properties and surface finish of parts.
- Larger Build Volumes: Future machines may offer larger build volumes, overcoming current size limitations.
- Integration with Other Technologies: Combining Binder Jetting with other additive manufacturing methods or traditional manufacturing techniques will create hybrid processes with enhanced capabilities.
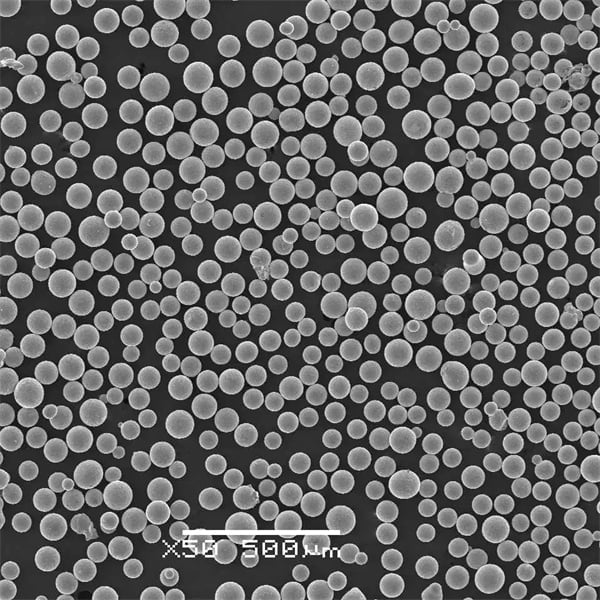
FAQ
Question | Answer |
---|---|
What is Binder Jetting Additive Manufacturing? | Binder Jetting is a 3D printing process that uses a liquid binder to adhere powder particles together to form objects layer by layer. |
What materials can be used in Binder Jetting? | A wide range of materials can be used, including metals, ceramics, and polymers. |
What are the main advantages of Binder Jetting? | Key advantages include high production speed, cost-effectiveness, material versatility, and the ability to create complex geometries. |
Are there any limitations to Binder Jetting? | Yes, limitations include potential issues with mechanical properties, surface finish, size constraints, binder selection, and porosity. |
What industries benefit from Binder Jetting? | Industries such as aerospace, automotive, medical, consumer goods, and construction benefit from Binder Jetting. |
How does Binder Jetting compare to other 3D printing methods? | Binder Jetting offers high speed and material versatility but may require additional post-processing for optimal part strength and finish. |
What are the future trends in Binder Jetting? | Future trends include material innovation, improved post-processing, larger build volumes, and integration with other technologies. |
Is Binder Jetting environmentally friendly? | Binder Jetting is considered more environmentally friendly than some traditional manufacturing methods due to reduced waste and the potential use of recycled materials. |
What post-processing steps are required for Binder Jetting parts? | Common post-processing steps include depowdering, sintering, and infiltration to enhance part properties. |
Can Binder Jetting produce functional parts? | Yes, Binder Jetting can produce functional parts, especially when combined with appropriate post-processing techniques to achieve the desired mechanical properties. |
Binder Jetting Additive Manufacturing continues to push the boundaries of what’s possible in the world of 3D printing, offering exciting opportunities for innovation and efficiency in various industries. As technology advances, the potential applications and benefits of Binder Jetting will only continue to grow.
Share On
MET3DP Technology Co., LTD is a leading provider of additive manufacturing solutions headquartered in Qingdao, China. Our company specializes in 3D printing equipment and high-performance metal powders for industrial applications.
Inquiry to get best price and customized Solution for your business!
Related Articles
About Met3DP
Recent Update
Our Product
CONTACT US
Any questions? Send us message now! We’ll serve your request with a whole team after receiving your message.
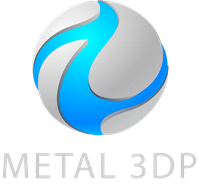
Metal Powders for 3D Printing and Additive Manufacturing