Brake Disc Coatings Powder
Table of Contents
Overview
When it comes to brake disc coatings, powder coatings are gaining significant traction in the automotive and industrial sectors. Why? Because they offer exceptional durability, resistance to corrosion, and improved braking performance. But there’s a lot more to these coatings than meets the eye. Let’s dive into the world of brake disc coatings powder, exploring different types, their compositions, properties, applications, and much more.
Types of Brake Disc Coatings Powder
Understanding the different types of brake disc coatings powder is crucial for selecting the right one for your needs. Here are ten specific metal powder models commonly used:
Powder Model | Composition | Properties | Characteristics |
---|---|---|---|
Ceramic Powder | Al2O3, SiO2 | High temperature resistance, low thermal conductivity | Excellent wear resistance, reduced noise |
Graphite Powder | C | High lubrication, good thermal conductivity | Low friction, extended life span |
Tungsten Carbide | WC | Extreme hardness, high density | Superior wear resistance, ideal for heavy-duty braking |
Molybdenum Disulfide | MoS2 | Solid lubricant, high load-carrying capacity | Reduced wear, excellent corrosion resistance |
Nickel-Chromium Alloy | Ni, Cr | High temperature resistance, oxidation resistance | Enhances thermal stability, excellent bonding |
Titanium Powder | Ti | Lightweight, high strength-to-weight ratio | Corrosion resistance, increased performance efficiency |
Aluminum Oxide | Al2O3 | High hardness, electrical insulation | Improved durability, effective heat dissipation |
Zirconium Dioxide | ZrO2 | High melting point, chemical inertness | Excellent thermal barrier, increased toughness |
Copper-Nickel Alloy | Cu, Ni | High electrical and thermal conductivity | Enhanced thermal management, improved braking response |
Iron Phosphate | FePO4 | Excellent adhesion, corrosion resistance | Enhances surface bonding, cost-effective |
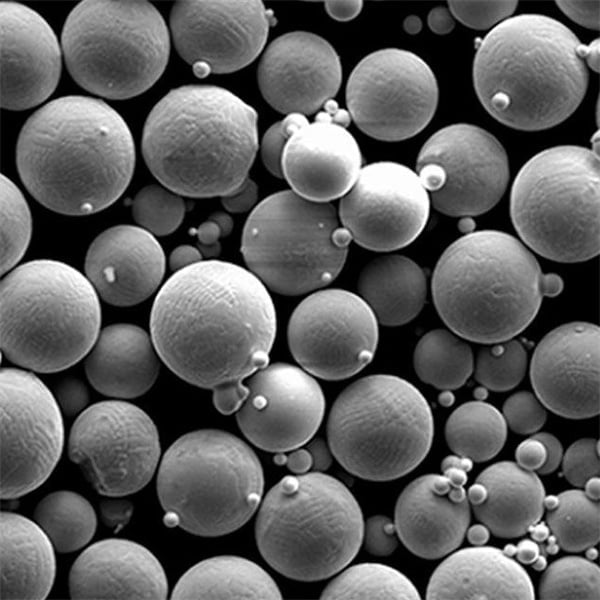
Applications of Brake Disc Coatings Powder
Brake disc coatings powder is used in various applications, tailored to specific performance requirements:
Application | Description |
---|---|
Automotive Industry | Used in passenger cars, trucks, and motorcycles to enhance braking performance and longevity. |
Aerospace | Applied in aircraft brake systems to ensure reliability under extreme conditions. |
Heavy Machinery | Utilized in construction and agricultural equipment for improved wear resistance. |
Railways | Employed in train braking systems to provide consistent performance over long distances. |
Marine Industry | Applied on ships and submarines to prevent corrosion in harsh sea environments. |
Sports Vehicles | Used in racing cars and motorcycles for superior braking performance at high speeds. |
Industrial Equipment | Utilized in manufacturing machines to ensure reliable and safe operation. |
Defense Vehicles | Applied in military vehicles for enhanced durability and performance under tough conditions. |
Electric Vehicles | Used in EVs to improve braking efficiency and extend the lifespan of brake components. |
Bicycles | Employed in high-end bicycles to provide superior stopping power and reduced maintenance. |
Specifications, Sizes, Grades, and Standards
When selecting brake disc coatings powder, knowing the specifications, sizes, grades, and standards is essential:
Specification | Details |
---|---|
Particle Size | Ranges from 10 to 50 microns, depending on the specific application requirements. |
Purity | Typically above 99%, ensuring high performance and reliability. |
Coating Thickness | Varies from 20 to 200 microns, tailored to the desired level of protection and performance. |
Temperature Resistance | Up to 1200°C, depending on the material composition. |
Hardness | Measured in Vickers (HV), typically ranging from 600 to 2000 HV. |
Bond Strength | Generally exceeds 70 MPa, ensuring durability and longevity. |
Standards | ASTM B117, ISO 9227 for corrosion resistance; ASTM E384 for hardness; ISO 2859 for quality assurance. |
Suppliers and Pricing Details
Choosing the right supplier is crucial for obtaining high-quality brake disc coatings powder. Here’s a look at some reputable suppliers and their pricing details:
Supplier | Location | Product Range | Pricing |
---|---|---|---|
PowderTech Coatings | USA | Ceramic, Graphite, Tungsten Carbide | $100 – $300 per kg |
Metallurgic Corp | Germany | Molybdenum Disulfide, Nickel-Chromium Alloy | €150 – €350 per kg |
NanoPowders Ltd | UK | Titanium, Aluminum Oxide | £120 – £280 per kg |
Advanced Materials | Japan | Zirconium Dioxide, Copper-Nickel Alloy | ¥2000 – ¥5000 per kg |
EuroCoat Technologies | France | Iron Phosphate, Ceramic | €100 – €250 per kg |
-
Ti45Nb Powder for Additive Manufacturing
-
Stainless Steel 316L Powder for Metal 3D Printing
-
TiNb Alloy Powder
-
TiNbZrSn Alloy Powder
-
Ti6Al4V Powder Titanium Based Metal Powder for Additive Manufacturing
-
CoCrMoW Powder
-
CPTi Powder
-
TC18 Powder : Unlocking the Power of Titanium Carbide
-
TC11 Powder : A Comprehensive Guide
Pros and Cons of Brake Disc Coatings Powder
Every product has its advantages and limitations. Here’s a comparison of the pros and cons of brake disc coatings powder:
Advantages | Limitations |
---|---|
Enhanced Durability: Significantly extends the lifespan of brake discs. | Cost: High-quality powders can be expensive. |
Corrosion Resistance: Protects against rust and oxidation. | Application Process: Requires specialized equipment and expertise. |
Improved Performance: Reduces noise and improves braking efficiency. | Availability: Some advanced materials may not be readily available. |
Heat Resistance: Maintains performance under high temperatures. | Maintenance: Requires regular inspection to ensure coating integrity. |
Aesthetic Appeal: Provides a clean, professional look to brake components. | Compatibility: Not all powders are suitable for every type of brake disc. |
Advantages of Brake Disc Coatings Powder
Why should you consider using brake disc coatings powder? Here are some compelling advantages:
Enhanced Durability
Brake disc coatings powder significantly enhances the durability of brake discs. By forming a protective layer, these coatings prevent wear and tear, ensuring the components last much longer than uncoated counterparts. Imagine not having to replace your brake discs as frequently—this not only saves money but also reduces downtime.
Corrosion Resistance
One of the standout benefits of using brake disc coatings powder is its exceptional resistance to corrosion. In environments where moisture and road salts are prevalent, this feature is invaluable. The coatings act like a shield, protecting the underlying metal from rust and other corrosive elements. It’s like having a suit of armor for your brakes.
Improved Performance
When it comes to performance, brake disc coatings powder can make a noticeable difference. These coatings reduce noise and vibration, resulting in a smoother and quieter braking experience. Furthermore, they enhance friction, providing better stopping power. It’s akin to upgrading from a standard car to a high-performance vehicle.
Heat Resistance
Brake discs generate a significant amount of heat during operation. Brake disc coatings powder is designed to withstand these high temperatures, maintaining its integrity and performance even under intense conditions. This makes them ideal for applications like racing or heavy-duty machinery, where heat dissipation is crucial.
Aesthetic Appeal
Beyond functionality, brake disc coatings powder also offers aesthetic benefits. The coated brake discs have a clean, professional look that enhances the overall appearance of the vehicle. Whether you’re a car enthusiast or simply want your vehicle to look its best, this is a nice bonus.
Disadvantages of Brake Disc Coatings Powder
While brake disc coatings powder offers numerous benefits, it’s important to consider the potential drawbacks:
Cost
High-quality brake disc coatings powder can be expensive. The initial investment may be higher compared to traditional brake discs. However, considering the extended lifespan and reduced maintenance costs, this can be viewed as a long-term saving.
Application Process
Applying brake disc coatings powder requires specialized equipment and expertise. This means you can’t just do it yourself in your garage unless you have the right tools and training. Professional application ensures the coating is applied evenly and effectively, but it does add to the overall cost.
Availability
Some advanced materials used in brake disc coatings powder might not be readily available in all regions. This can limit your options and potentially lead to higher costs if you need to import the materials.
Maintenance
Although brake disc coatings powder enhances durability, it still requires regular inspection. Over time, the coating may wear off, especially under extreme conditions. Ensuring the integrity of the coating is crucial for maintaining optimal performance.
Compatibility
Not all brake disc coatings powders are suitable for every type of brake disc. It’s essential to choose the right powder for your specific needs, which may require consulting with a specialist.
Technical Parameters and Performance Metrics
Understanding the technical parameters and performance metrics is vital for evaluating brake disc coatings powder:
Parameter | Range/Value | Description |
---|---|---|
Hardness (HV) | 600 – 2000 HV | Indicates the resistance of the coating to indentation and wear. Higher values signify greater hardness and durability. |
Coating Thickness | 20 – 200 microns | The thickness of the applied coating, impacting durability and performance. Thicker coatings offer better protection but may affect dimensional tolerances. |
Temperature Resistance | Up to 1200°C | The maximum temperature the coating can withstand without degrading, crucial for applications in high-temperature environments. |
Bond Strength | > 70 MPa | Measures the adhesion strength between the coating and the substrate. Higher values indicate better bonding and longevity. |
Particle Size | 10 – 50 microns | The size range of powder particles used in coating applications, affecting surface finish and coverage. Smaller particles can provide finer finishes. |
Purity | > 99% | The purity level of the coating material, ensuring consistency and performance reliability. Higher purity reduces the risk of impurities affecting performance. |
Comparing Brake Disc Coatings Powder Options
To help you make an informed decision, here’s a comparison of various brake disc coatings powder options:
Powder Type | Advantages | Disadvantages |
---|---|---|
Ceramic Powder | Excellent wear resistance, reduced noise. | Higher cost, specialized application required. |
Graphite Powder | High lubrication, low friction. | May wear faster under heavy loads. |
Tungsten Carbide | Extreme hardness, ideal for heavy-duty braking. | Expensive, challenging to apply uniformly. |
Molybdenum Disulfide | Solid lubricant, excellent corrosion resistance. | Limited availability, may require reapplication. |
Nickel-Chromium Alloy | High temperature resistance, oxidation resistance. | Costly, requires expertise for application. |
Titanium Powder | Lightweight, corrosion-resistant. | Expensive, limited availability in some regions. |
Aluminum Oxide | High hardness, effective heat dissipation. | Brittle, may crack under extreme conditions. |
Zirconium Dioxide | Superior thermal barrier, increased toughness. | Costly, specialized application needed. |
Copper-Nickel Alloy | High conductivity, enhanced thermal management. | May oxidize over time, maintenance required. |
Iron Phosphate | Excellent adhesion, cost-effective. | Moderate durability, less effective in high-temperature environments. |
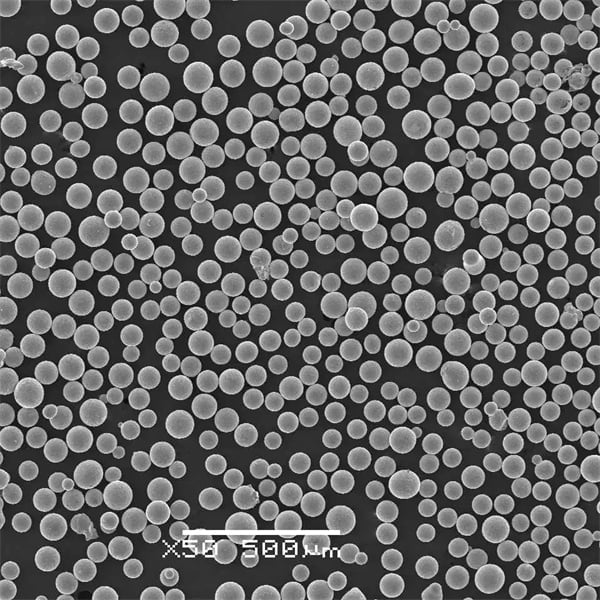
FAQ
What are the primary benefits of using brake disc coatings powder?
Brake disc coatings powder offers enhanced durability, corrosion resistance, improved braking performance, and heat resistance. These coatings also provide aesthetic benefits, enhancing the appearance of brake components.
How do I choose the right brake disc coatings powder for my application?
Consider factors such as required durability, operating conditions (temperature, humidity), application method, and budget. Consulting with suppliers and specialists can help you select the optimal powder for your specific needs.
Are brake disc coatings powder environmentally friendly?
Many modern brake disc coatings powders are formulated to be environmentally friendly, with reduced emissions during application and operation. However, it’s essential to verify specific product claims and certifications.
What maintenance is required for brake disc coatings powder?
Regular inspection is recommended to ensure the integrity of the coating. Depending on usage and environmental conditions, periodic reapplication or touch-ups may be necessary to maintain optimal performance.
Can brake disc coatings powder improve braking performance?
Yes, brake disc coatings powder can enhance braking performance by reducing noise, improving friction characteristics, and ensuring consistent braking efficiency under various operating conditions.
Conclusion
In conclusion, brake disc coatings powder represents a significant advancement in automotive and industrial braking technology. By offering enhanced durability, corrosion resistance, and improved performance, these coatings play a crucial role in extending the lifespan of brake components and enhancing overall vehicle safety. When choosing a brake disc coatings powder, consider factors such as material composition, application method, and specific performance requirements to ensure optimal results. With the right powder, you can achieve superior braking performance and reliability for your vehicles and machinery.
By integrating detailed technical information with practical insights and comparisons, this article aims to guide decision-making and foster a deeper understanding of brake disc coatings powder in various applications. Whether you’re involved in automotive engineering, manufacturing, or maintenance, selecting the right coating can make a significant difference in performance, efficiency, and longevity.
Remember, the choice of brake disc coatings powder should align with your operational needs and performance expectations. For further assistance or inquiries, don’t hesitate to consult with industry experts or suppliers who specialize in brake disc coatings technology.
Share On
MET3DP Technology Co., LTD is a leading provider of additive manufacturing solutions headquartered in Qingdao, China. Our company specializes in 3D printing equipment and high-performance metal powders for industrial applications.
Inquiry to get best price and customized Solution for your business!
Related Articles
About Met3DP
Recent Update
Our Product
CONTACT US
Any questions? Send us message now! We’ll serve your request with a whole team after receiving your message.
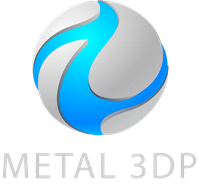
Metal Powders for 3D Printing and Additive Manufacturing