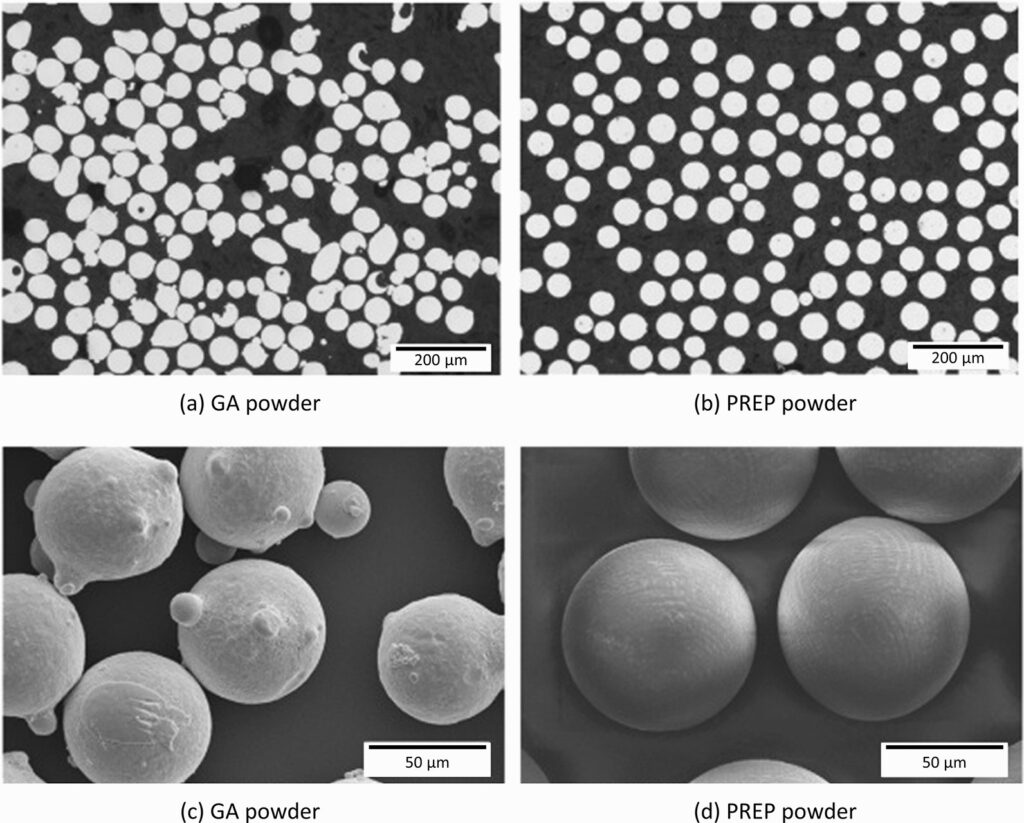
Breakthrough Spherical Titanium Alloy Powder: Unlocking Limitless Possibilities
Low MOQ
Provide low minimum order quantity to meet different needs.
OEM & ODM
Provide customized products and design services to meet unique customer needs.
Adequate Stock
Ensure fast order processing and provide reliable and efficient service.
Customer Satisfaction
Provide high quality products with customer satisfaction at the core.
share this article
Table of Contents
Titanium alloys have long been hailed as the go-to materials for industries demanding strength, lightweight properties, and corrosion resistance. Enter Spherical Titanium Alloy Powder, a cutting-edge material that’s revolutionizing the world of additive manufacturing, aerospace, medical implants, and more. This powdered form of titanium alloy offers incredible versatility, thanks to its spherical shape that enhances flowability and precision in powder-based technologies like 3D printing.
But what makes Spherical Titanium Alloy Powder so special? Why is it the material of choice for demanding applications, and how can it drive innovation in your projects? In this 12,000-word guide, we’ll dive deep into everything you need to know about Spherical Titanium Alloy Powder—from its composition to its real-world applications, pricing, and more.
Overview of Spherical Titanium Alloy Powder
Let’s start with the basics. Spherical Titanium Alloy Powder is produced using advanced techniques such as gas atomization or plasma atomization, which result in perfectly spherical particles. These fine, uniform powders are prized for their excellent consistency and flowability, making them ideal for precision manufacturing processes, especially additive manufacturing.
Key Benefits of Spherical Titanium Alloy Powder:
- Lightweight but strong: Titanium alloys have one of the highest strength-to-weight ratios of any metal, making them a popular choice for aerospace and automotive applications.
- Corrosion-resistant: Whether exposed to seawater, chemicals, or extreme environments, titanium alloys resist corrosion better than most metals.
- Biocompatibility: Titanium is non-reactive with human tissue, making it perfect for medical implants such as bone screws and joint replacements.
- High-temperature performance: Titanium alloys can withstand high temperatures, making them ideal for aerospace applications where heat resistance is critical.
Types, Composition, and Properties of Spherical Titanium Alloy Powder
Not all titanium alloys are created equal. Depending on the intended application, different formulations of Spherical Titanium Alloy Powder offer unique properties. The most common titanium alloy used in powder form is Ti-6Al-4V (Grade 5), but there are other variations tailored for specific uses.
Alloy Type | Composition (Wt%) | Key Properties | Common Applications |
---|---|---|---|
Ti-6Al-4V (Grade 5) | Ti: 90%, Al: 6%, V: 4% | High strength, excellent corrosion resistance, biocompatibility | Aerospace, medical implants, 3D printing |
Ti-6Al-4V ELI (Grade 23) | Ti: 90%, Al: 6%, V: 4% (Extra Low Interstitials) | Enhanced toughness, better fatigue resistance | Biomedical implants, surgical tools |
Ti-5Al-2.5Sn | Ti: 92.5%, Al: 5%, Sn: 2.5% | High creep resistance, good weldability | Aerospace components, high-temperature parts |
Ti-15V-3Cr-3Al-3Sn | Ti: 85%, V: 15%, Cr: 3%, Al: 3%, Sn: 3% | Excellent ductility, good cold formability | Aerospace structures, chemical processing |
Ti-10V-2Fe-3Al | Ti: 85%, V: 10%, Fe: 2%, Al: 3% | High strength, good fatigue resistance | Automotive, aerospace |
Why Composition Matters:
The composition of the alloy directly influences its mechanical properties and performance in different environments. For example, Ti-6Al-4V is the most widely used titanium alloy due to its balanced combination of strength, corrosion resistance, and biocompatibility. Ti-15V-3Cr-3Al-3Sn, on the other hand, is ideal for applications where ductility and cold formability are more critical.
Spherical Titanium Alloy Powder Properties and Characteristics
Understanding the key properties of Spherical Titanium Alloy Powder is essential for selecting the right material for your application. Below are some of the most important characteristics that make it stand out.
Property | Description |
---|---|
Density | Around 4.43 g/cm³ (for Ti-6Al-4V), making it much lighter than steel or nickel alloys. |
Tensile Strength | 900-1200 MPa, depending on the alloy and processing method. |
Corrosion Resistance | Excellent in a wide variety of environments, including seawater and industrial chemicals. |
Melting Point | Approximately 1660°C (for pure titanium), though alloys may have slightly altered melting points. |
Thermal Conductivity | Low thermal conductivity, meaning it retains heat well, which is beneficial in high-temperature environments. |
Flowability | Spherical particles offer excellent flowability, critical for 3D printing and powder metallurgy. |
Biocompatibility | Non-reactive with human tissue, making it a top choice for medical implants. |
Why Flowability is Crucial:
In additive manufacturing and powder metallurgy, flowability refers to how easily the powder moves through the machine. Spherical particles offer better flowability than irregularly shaped particles, ensuring smoother operation and higher-quality final products. Imagine trying to pour sand with jagged rocks mixed in—it’s not going to flow smoothly. The same logic applies to metal powders!
Applications of Spherical Titanium Alloy Powder
So, where is Spherical Titanium Alloy Powder used? Thanks to its versatile properties, it’s found in a wide variety of industries, from aerospace to medical devices.
Industry | Applications |
---|---|
Aerospace | Jet engine components, turbine blades, airframe parts |
Medical | Bone implants, dental implants, surgical instruments |
Automotive | Lightweight performance parts, engine components |
Additive Manufacturing | 3D-printed parts for aerospace, automotive, and medical industries |
Chemical Processing | Corrosion-resistant valves, pumps, and heat exchangers |
Defense | Lightweight armor, missile components, and other high-strength applications |
Why Aerospace Loves Titanium:
In the aerospace industry, every gram counts. The high strength-to-weight ratio of Spherical Titanium Alloy Powder makes it perfect for critical components like jet engine blades. These parts must withstand extreme temperatures while remaining light enough to ensure fuel efficiency. Similarly, in automotive racing, titanium parts can drastically reduce vehicle weight without sacrificing performance, giving racers that all-important edge.
Specifications, Sizes, and Standards for Spherical Titanium Alloy Powder
When selecting Spherical Titanium Alloy Powder for your project, understanding the specifications, particle sizes, and relevant standards is key. The particle size you choose will depend on your specific manufacturing process, whether it’s for additive manufacturing, thermal spraying, or powder metallurgy.
Specification | Details |
---|---|
Particle Size Range | Typically 15-53 μm for additive manufacturing, 45-150 μm for thermal spraying |
Purity | 99.5% minimum for most applications |
Grades | ASTM F136 (medical), ASTM F1472 (aerospace), AMS 4998 (additive manufacturing) |
Manufacturing Process | Gas atomization, Plasma atomization |
Packaging | Available in 5kg, 10kg, and 25kg sealed containers |
Why Particle Size Matters:
The particle size of the powder greatly impacts how the material behaves in different manufacturing processes. For example, in 3D printing, finer powders (15-53 μm) are preferred because they offer better precision and a smoother surface finish. On the other hand, coarser powders (45-150 μm) are used in thermal spraying to create thicker, more durable coatings.
Suppliers and Pricing Details for Spherical Titanium Alloy Powder
The price of Spherical Titanium Alloy Powder can vary depending on the alloy, particle size, and supplier. Below is an overview of some of the most reputable suppliers and their pricing.
Supplier | Product Description | Price (USD) | Comments |
---|---|---|---|
AP&C (GE Additive) | Ti-6Al-4V Spherical Powder, 15-45 μm | $350 – $400 per kg | High-quality powder for additive manufacturing |
Carpenter Additive | Ti-6Al-4V Spherical Powder, 45-105 μm | $300 – $350 per kg | Suitable for aerospace and thermal spraying applications |
Praxair Surface Technologies | Ti-6Al-4V ELI, 15-45 μm, medical grade | $400 – $450 per kg | Premium powder for medical implants |
Höganäs AB | Ti-5Al-2.5Sn, 45-150 μm, aerospace grade | $280 – $320 per kg | Bulk pricing available for large orders |
Pricing Factors:
- Particle Size: Finer powders (15-45 μm) tend to be more expensive due to the additional processing required.
- Purity: Higher purity levels result in higher costs but are essential for applications like medical implants.
- Alloy Type: Specialty alloys like Ti-5Al-2.5Sn or Ti-10V-2Fe-3Al may come at a premium due to their specific properties.
Advantages and Limitations of Spherical Titanium Alloy Powder
While Spherical Titanium Alloy Powder is a fantastic material for many applications, it’s essential to weigh its advantages and limitations before making a decision.
Advantages | Limitations |
---|---|
Excellent strength-to-weight ratio, perfect for lightweight, high-strength components | Higher cost compared to other metals like steel or aluminum |
Outstanding corrosion resistance, ideal for harsh environments | Requires advanced equipment and expertise for processing (e.g., 3D printing) |
Biocompatibility makes it the top choice for medical implants | Limited availability in some regions |
High-temperature performance, ensuring longevity in aerospace and automotive parts | Not as affordable for mass-market consumer products |
Spherical shape ensures excellent flowability for consistent additive manufacturing | Finer powders are more expensive and require more precise handling |
Why the Cost is Worth It:
Sure, Spherical Titanium Alloy Powder isn’t cheap. But when you think about the long-term benefits—durability, weight savings, and biocompatibility—the investment pays off. Whether you’re producing a jet engine component or a hip implant, the reliability and performance of titanium alloys make them worth every penny.
FAQs About Spherical Titanium Alloy Powder
Question | Answer |
---|---|
What makes Spherical Titanium Alloy Powder ideal for 3D printing? | Its spherical shape ensures excellent flowability, which is critical for consistent powder-based additive manufacturing processes. |
How does Spherical Titanium Alloy Powder compare to stainless steel? | Titanium alloys are significantly lighter and offer better corrosion resistance, though they tend to be more expensive than stainless steel. |
What industries use Spherical Titanium Alloy Powder the most? | Aerospace, medical devices, automotive, and defense are the primary industries that rely on titanium alloy powders for their high-performance needs. |
Can Spherical Titanium Alloy Powder be used for medical implants? | Yes, titanium is biocompatible, making it an ideal material for medical implants like bone screws and hip replacements. |
Why is particle size important in titanium alloy powders? | Particle size affects the powder’s flowability and packing density, which are critical factors in applications like 3D printing and thermal spraying. |
Conclusion: Why Spherical Titanium Alloy Powder is a Game-Changer
In summary, Spherical Titanium Alloy Powder is a revolutionary material that offers high strength, lightweight properties, and exceptional corrosion resistance. Whether you’re working in aerospace, medical devices, or additive manufacturing, this material can meet the most demanding requirements.
While it may come with a higher price tag, the benefits—especially in terms of performance and longevity—make it a worthwhile investment. Whether you’re creating jet engine components, medical implants, or lightweight automotive parts, Spherical Titanium Alloy Powder is the material that can take your project to the next level.
So, is Spherical Titanium Alloy Powder the right choice for you? If you need a material that’s strong, durable, and versatile, the answer is likely yes.
Get Latest Price
About Met3DP
Product Category
HOT SALE
CONTACT US
Any questions? Send us message now! We’ll serve your request with a whole team after receiving your message.
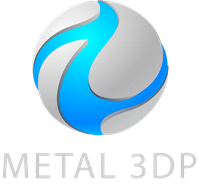
Metal Powders for 3D Printing and Additive Manufacturing