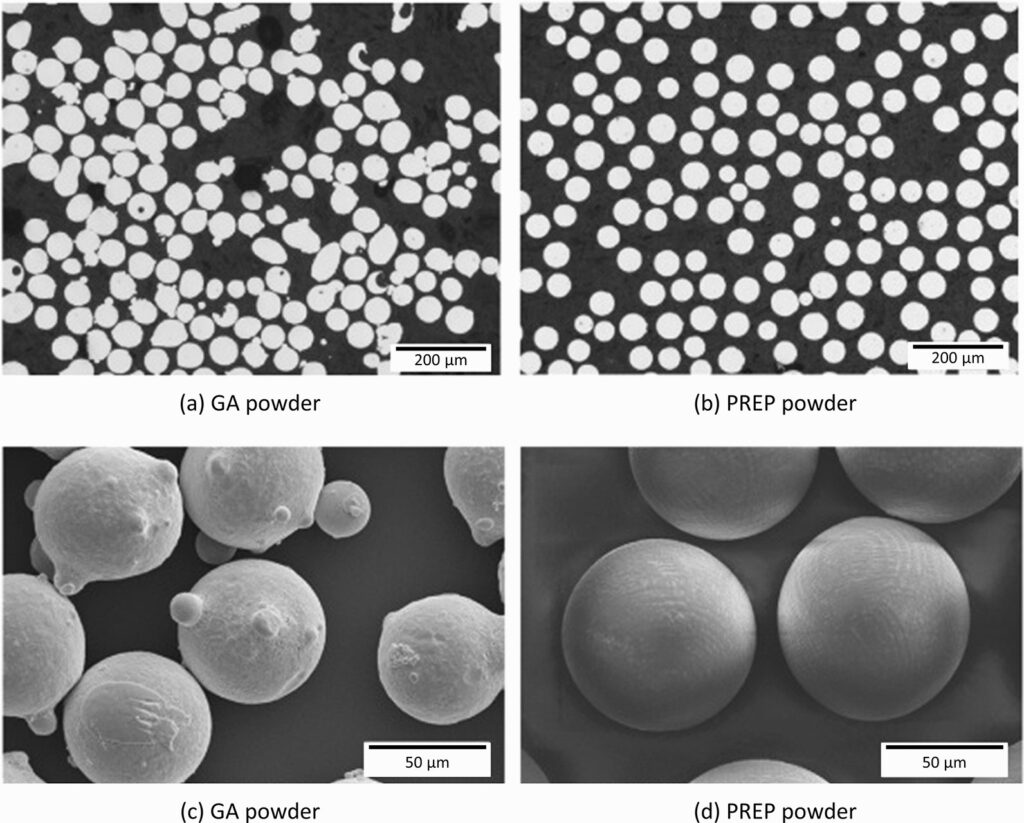
Carbide Cement Pellet: Unmatched Performance for High-Stress Environments
Low MOQ
Provide low minimum order quantity to meet different needs.
OEM & ODM
Provide customized products and design services to meet unique customer needs.
Adequate Stock
Ensure fast order processing and provide reliable and efficient service.
Customer Satisfaction
Provide high quality products with customer satisfaction at the core.
share this article
Table of Contents
Carbide cement pellets may not be the first thing that comes to mind when you think of industrial materials, but to those in the know, they are game-changers. Whether you’re working in mining, oil and gas, or even manufacturing, carbide cement pellets are critical to the success of many applications. These tiny pellets may seem humble, but they pack a punch in terms of durability, wear resistance, and versatility.
So, what exactly are carbide cement pellets, and why are they so important in high-performance industries? In this guide, we’re going to break down everything you need to know. We’ll cover the composition, properties, applications, and pricing of carbide cement pellets, so you can see why they’re the material of choice for many heavy-duty applications.
Let’s dive in.
Overview of Carbide Cement Pellets
What Are Carbide Cement Pellets?
Carbide cement pellets, also known as cemented carbide pellets, are composite materials made by combining tungsten carbide (WC) with a metallic binder, most commonly cobalt. In essence, they are tiny, high-strength pellets engineered to withstand extreme conditions, such as abrasion and impact. The pellets are created through a process called powder metallurgy, where the tungsten carbide powder is mixed with cobalt binder, pressed into pellet form, and then sintered at high temperatures to form a solid, cohesive material.
The result? A material that’s almost as hard as diamond, but with enough toughness to resist chipping or breaking under stress.
But why pellets? The small size of the pellets increases the surface area, making them ideal for applications like drilling, cutting, and grinding, where a high degree of precision and durability is needed. Carbide cement pellets are widely used in industries where wear resistance and strength are critical, such as mining, oil extraction, and metalworking.
Key Characteristics of Carbide Cement Pellets
- Incredible Hardness: Tungsten carbide is one of the hardest materials on earth, second only to diamond.
- Wear Resistance: Carbide cement pellets maintain their integrity even in abrasive environments.
- Toughness: The cobalt binder helps prevent brittleness, so the material doesn’t crack under pressure.
- Thermal Stability: Carbide cement pellets can withstand high temperatures, making them ideal for high-heat applications.
- Corrosion Resistance: The material resists corrosion, offering a longer lifespan in harsh environments.
Composition and Properties
Now that we’ve covered the basics, let’s take a closer look at the composition and properties that make carbide cement pellets such a vital material in industrial applications.
Carbide cement pellets are typically composed of tungsten carbide—a hard, dense material—combined with a metal binder like cobalt or nickel. The ratio of tungsten carbide to the binder plays a significant role in the final properties of the pellets. A higher tungsten carbide content means greater hardness, while a higher binder content improves toughness.
Property | Description |
---|---|
Composition | Typically 85-95% tungsten carbide (WC) and 5-15% cobalt (Co) or nickel (Ni) binder. |
Hardness (Vickers Scale) | Ranges from 1,500 to 2,200 HV, depending on the WC content. |
Density | Around 14-15 g/cm³, making it a dense material suitable for high-impact applications. |
Fracture Toughness | Enhanced by the cobalt binder, with values ranging from 10-15 MPa·m^1/2. |
Compressive Strength | Can withstand pressures up to 6,000 MPa, making it ideal for heavy-duty applications. |
Thermal Conductivity | High thermal conductivity allows it to dissipate heat effectively, even in high-heat environments. |
Melting Point | Tungsten carbide melts at 2,870°C (5,198°F), while cobalt melts at around 1,495°C (2,723°F). |
Corrosion Resistance | Resistant to wear and corrosion, particularly in harsh chemical environments. |
Material Composition Breakdown
The properties of carbide cement pellets can be fine-tuned by adjusting the ratio of tungsten carbide to cobalt or nickel binders. Here’s a quick breakdown:
- High WC content (90-95%) = Greater hardness and wear resistance, but slightly more brittle.
- Higher binder content (10-15%) = Increased toughness, but slightly lower hardness.
This balance is key, and different applications may require different ratios depending on the environment and stresses the pellets will face.
Types of Carbide Cement Pellets
Carbide cement pellets come in different forms, each tailored for specific applications. These variations are based on the composition of the materials, the manufacturing process, and the pellet size. Let’s break down the common types.
Type | Description |
---|---|
Cobalt-Bonded Carbide Cement Pellets | The most common type, using cobalt as a binder for increased toughness and impact resistance. |
Nickel-Bonded Carbide Cement Pellets | Offers better corrosion resistance than cobalt-bonded variants, making them ideal for oil and gas applications. |
Mixed Binder Carbide Cement Pellets | Combines cobalt and nickel for a balance of toughness and corrosion resistance. |
Coated Carbide Cement Pellets | Pellets are coated with materials like titanium carbide to further enhance wear resistance. |
Fine-Grain Carbide Cement Pellets | Smaller grain size for precision applications requiring a high degree of surface finish. |
Coarse-Grain Carbide Cement Pellets | Larger grain size for applications where impact resistance is more critical than surface finish. |
Each of these types has its strengths, making them more suited for different industrial environments.
Applications
Carbide cement pellets are used in a wide variety of industries thanks to their unique combination of hardness, toughness, and wear resistance. Let’s take a look at some of the most common applications.
Industry | Applications |
---|---|
Mining and Drilling | Used in drill bits, rock-cutting tools, and wear parts that encounter highly abrasive materials. |
Oil and Gas | Found in downhole tools, valve seats, and bearings where high pressure and corrosive substances are common. |
Metalworking | Essential in cutting tools, grinding wheels, and dies for machining tough metals like steel and titanium. |
Construction | Used in concrete cutting tools and road milling machines where high wear and impact are daily challenges. |
Aerospace | Applied in jet engine components and turbine blades that require materials resistant to both heat and wear. |
Automotive | Found in engine components, gear tools, and brake systems, where both wear resistance and heat stability are critical. |
Defense and Military | Used in armor-piercing ammunition and protective coatings for military vehicles and equipment. |
Tooling Industry | Key material for cutting blades, saw tips, and drill bits that need to survive in high-stress environments. |
Why Are Carbide Cement Pellets So Popular in These Industries?
It all comes down to the fact that carbide cement pellets can handle extreme conditions. Whether it’s the intense heat of an aerospace engine, the abrasive wear of a mining drill bit, or the corrosive environment of an oil well, carbide cement pellets consistently outperform other materials. They offer longer tool life, which means less downtime for maintenance and replacement, ultimately saving companies time and money. Who wouldn’t want that?
Specifications, Sizes, Grades, and Standards
When selecting carbide cement pellets for a particular application, it’s important to consider the specifications, sizes, grades, and standards that ensure you’re getting the right material for the job. Here’s a breakdown of the key specs to keep in mind.
Specification | Details |
---|---|
Pellet Sizes | Common sizes range from 0.5 mm to 5 mm in diameter, depending on the application. |
Grain Sizes | Available in fine-grain (0.5 – 2 µm) and coarse-grain (2 – 10 µm) options for different applications. |
Grades | Grades are typically classified by ISO standards, with common grades including K10, K20, and K30 for wear resistance and toughness. |
Hardness | Hardness values range from 1,500 to 2,200 HV, depending on the WC content and grain size. |
Density | Typically around 14 to 15 g/cm³, depending on the metal binder and WC content. |
Compressive Strength | Can withstand pressures up to 6,000 MPa, making it suitable for high-pressure environments. |
Standards | Common standards include ISO 9001 for quality management, ASTM B777 for tungsten products, and ISO 513 for cutting tool materials. |
These specifications help ensure that the carbide cement pellets you select meet the rigorous demands of your particular industry or application.
Suppliers and Pricing
If you’re looking to purchase carbide cement pellets, you’ll need to consider factors like supplier reputation, product quality, and of course, pricing. Here’s a look at some key suppliers and their pricing details.
Supplier | Country | Price Per Kg (USD) | Grade Options | Special Features |
---|---|---|---|---|
Kennametal | United States | $80 – $150 | K10, K20, K30 | Leading supplier with a wide range of carbide products for industrial and tooling applications. |
Sandvik | Sweden | $90 – $160 | K10, K20, P15 | Known for high-quality carbide materials for mining and cutting tools. |
Zhuzhou Cemented Carbide Group | China | $50 – $100 | K10, K20, K30 | Affordable pricing with a focus on carbide for mining and drilling industries. |
CERATIZIT | Luxembourg | $100 – $180 | K10, K20, P15 | High-end carbide products for aerospace and high-precision applications. |
Sumitomo Electric Hardmetal | Japan | $110 – $170 | K10, K20 | Specializes in carbide for cutting tools and wear parts, offering premium quality. |
Factors That Influence Carbide Cement Pellet Pricing
Several factors can influence the price of carbide cement pellets, including:
- Tungsten carbide content: Higher WC content typically leads to higher prices due to the cost of raw materials.
- Binder type: Cobalt-bonded pellets tend to be more expensive than nickel-bonded ones, as cobalt is pricier.
- Grain size: Fine-grain pellets are often more expensive due to the additional processing required to achieve a smaller grain size.
- Supplier location: Suppliers from regions with lower production costs, such as China, may offer more competitive pricing.
Advantages and Disadvantages
Like any material, carbide cement pellets come with their own set of advantages and limitations. Understanding these can help you determine whether they’re the right choice for your application.
Advantages | Disadvantages |
---|---|
Superior Hardness: One of the hardest materials available, ideal for wear-intensive applications. | Brittleness: Despite their toughness, carbide cement pellets can be brittle under certain impacts. |
Longer Tool Life: Their wear resistance reduces the need for frequent replacements, saving time and money. | High Cost: Carbide cement pellets are more expensive than many other materials, especially at high WC content. |
Heat Resistance: Maintains integrity at high temperatures, making them suitable for high-heat environments. | Difficult to Machine: Their hardness makes them challenging to machine, requiring specialized tools. |
Corrosion Resistance: Resistant to corrosion, especially in oil and gas applications. | Weight: Tungsten carbide is a dense material, which can be a disadvantage in applications where lightweight materials are preferred. |
In general, carbide cement pellets are a great choice for applications where wear resistance, hardness, and durability are key. However, they may not be the best fit for applications where flexibility or lightweight materials are needed.
Frequently Asked Questions (FAQ)
To make things easier, here are some commonly asked questions about carbide cement pellets.
Question | Answer |
---|---|
What are carbide cement pellets used for? | They are used in a variety of industries, including mining, oil and gas, metalworking, and aerospace, for applications requiring extreme wear resistance. |
How are carbide cement pellets made? | They are produced through powder metallurgy, where tungsten carbide powder is mixed with a metal binder (like cobalt), pressed into pellets, and sintered at high temperatures. |
What is the typical hardness of carbide cement pellets? | The hardness typically ranges from 1,500 to 2,200 HV, depending on the tungsten carbide content and grain size. |
Why are carbide cement pellets so expensive? | Their high cost is due to the price of tungsten carbide and the complex manufacturing process involved in creating them. |
What is the difference between cobalt-bonded and nickel-bonded carbide cement pellets? | Cobalt-bonded pellets offer better toughness, while nickel-bonded pellets provide superior corrosion resistance, especially in harsh environments. |
Can carbide cement pellets be recycled? | Yes, tungsten carbide materials can often be recycled, which helps reduce costs and environmental impact in some industries. |
How do I choose the right grade of carbide cement pellets? | The right grade depends on your application. For wear resistance, choose a higher WC content; for toughness, opt for a higher binder content. |
Conclusion
Carbide cement pellets are a true workhorse in the world of industrial materials. Their incredible hardness, wear resistance, and toughness make them indispensable in industries like mining, oil and gas, aerospace, and metalworking. While they can be expensive, their long lifespan and performance advantages often justify the cost.
Whether you need carbide cement pellets for drill bits, cutting tools, or grinding wheels, understanding the composition, properties, and applications of these pellets will help you make the best decision for your project. With the right supplier and grade, carbide cement pellets can significantly improve the efficiency and durability of your tools and machinery.
So, are carbide cement pellets worth the investment? Absolutely—if you need a material that can stand up to the toughest conditions, carbide cement pellets are the way to go.
Get Latest Price
About Met3DP
Product Category
HOT SALE
CONTACT US
Any questions? Send us message now! We’ll serve your request with a whole team after receiving your message.
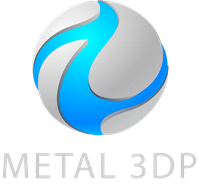
Metal Powders for 3D Printing and Additive Manufacturing