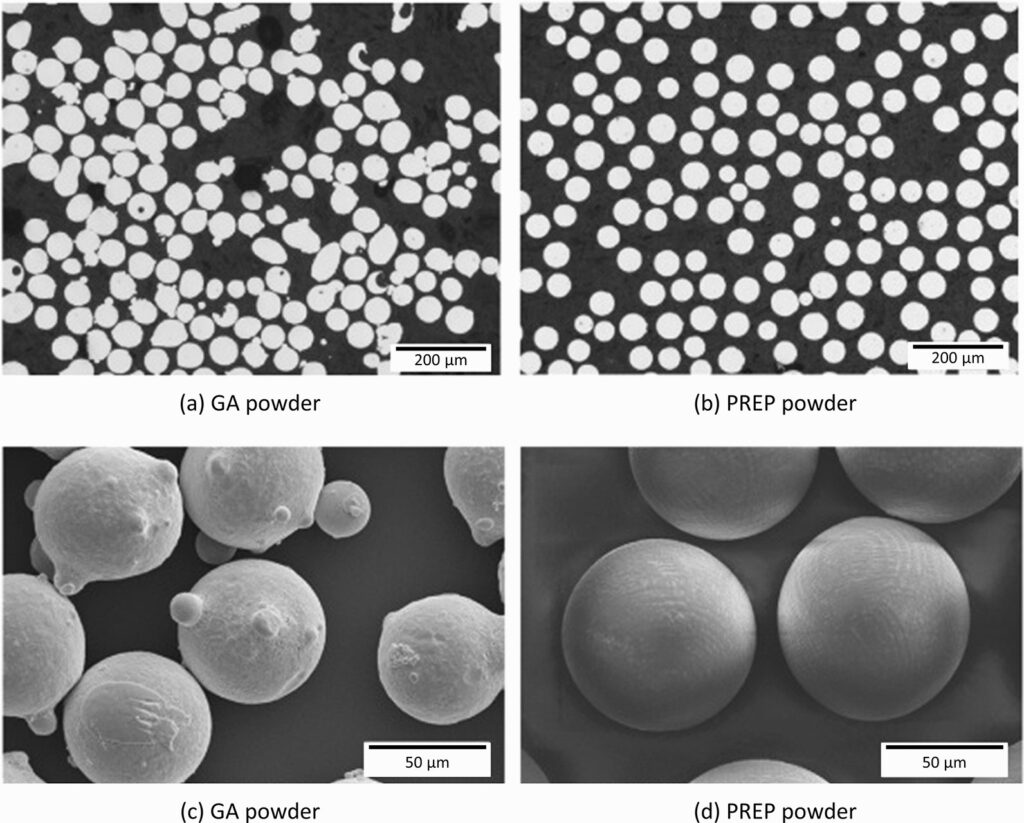
Casting Tungsten Carbide: Your Best Bet for Superior Toughness
Low MOQ
Provide low minimum order quantity to meet different needs.
OEM & ODM
Provide customized products and design services to meet unique customer needs.
Adequate Stock
Ensure fast order processing and provide reliable and efficient service.
Customer Satisfaction
Provide high quality products with customer satisfaction at the core.
share this article
Table of Contents
When it comes to materials known for their hardness, wear resistance, and durability, tungsten carbide is always at the forefront of the conversation. But among the various forms of tungsten carbide, casting tungsten carbide holds a special place. It offers remarkable wear resistance and toughness, making it a go-to material for high-stress applications. Whether you’re in mining, oil and gas, or even the aerospace industry, you’ve probably encountered casting tungsten carbide in some form.
In this comprehensive guide, we’ll explore what makes casting tungsten carbide such a valuable material. From its unique properties and composition to its wide range of applications, we’ll cover everything you need to know. Plus, we’ll dive into specifications, suppliers, pros and cons, and much more to ensure you have a complete understanding of casting tungsten carbide and how it can benefit your operation.
Overview
Casting tungsten carbide is a form of tungsten carbide produced through a specialized casting process. This process involves melting tungsten and carbon at extremely high temperatures and combining them to form a hard, wear-resistant material. Unlike sintered tungsten carbide, which is formed by compressing and heating tungsten carbide powder, casting tungsten carbide offers unique benefits such as superior toughness, better impact resistance, and the ability to withstand extreme conditions.
Its applications are vast, ranging from industrial wear parts to cutting tools, and its properties make it an excellent choice for environments where standard materials would quickly degrade or fail.
Why Choose Casting Tungsten Carbide?
Why settle for materials that can’t handle the heat when you can choose casting tungsten carbide? Imagine a material that’s as tough as nails but can also handle the most abrasive and high-impact environments. That’s what casting tungsten carbide brings to the table. It’s like having armor for your tools and machinery—ensuring they last longer and perform better, even in the harshest conditions.
Composition and Properties
Casting tungsten carbide is made up of two primary elements: tungsten (W) and carbon (C). The typical ratio of these elements is around 94% tungsten and 6% carbon, though slight variations may exist based on specific applications and manufacturing processes. This high tungsten content gives the material its extraordinary hardness and wear resistance.
Let’s break down the key properties of casting tungsten carbide that make it such a valuable material for industrial applications.
Characteristic | Description |
---|---|
Hardness | Casting tungsten carbide can achieve a hardness of 2,500 to 3,500 HV (Vickers hardness). This makes it one of the hardest materials available, second only to diamond. |
Density | The density of casting tungsten carbide is approximately 15.4 g/cm³, making it a relatively dense and compact material. |
Toughness | Exhibits excellent toughness and impact resistance, making it suitable for applications where high-stress or abrasive forces are present. |
Wear Resistance | Exceptional wear resistance makes casting tungsten carbide ideal for use in abrasive environments, especially in mining, drilling, and material handling. |
Thermal Conductivity | Casting tungsten carbide has good thermal conductivity, allowing it to perform well in high-temperature environments without losing its structural integrity. |
Melting Point | With a melting point above 2,870°C (5,198°F), casting tungsten carbide can withstand extreme heat, making it ideal for high-temperature applications. |
Corrosion Resistance | It offers moderate corrosion resistance, especially when properly coated or treated, making it suitable for use in chemically aggressive environments. |
These properties make casting tungsten carbide a material that excels in both durability and performance, ensuring it can handle the most demanding use cases.
Types
Casting tungsten carbide comes in several forms, each tailored for specific applications and performance requirements. The differences between these types often lie in grain size, bonding agents, and production methods. Here’s a breakdown of the most common types:
Type | Description |
---|---|
Macro-Grain Casting Tungsten Carbide | Features larger grain sizes, typically 50-150 µm, making it ideal for applications that require higher toughness and impact resistance, such as drilling and mining tools. |
Micro-Grain Casting Tungsten Carbide | With grain sizes under 1 µm, this type offers higher hardness and wear resistance, making it suitable for cutting tools and precision instruments. |
Coated Casting Tungsten Carbide | Typically coated with materials like cobalt or nickel to improve corrosion resistance and toughness, especially in chemically aggressive environments. |
Spherical Casting Tungsten Carbide | Spherical particles provide a more uniform distribution in composite materials, enhancing wear resistance in coatings and surface treatments. |
Cobalt-Bonded Casting Tungsten Carbide | Uses cobalt as a bonding agent to improve toughness and reduce brittleness, especially in applications that involve impact or shock loading. |
Each type of casting tungsten carbide offers specific advantages based on the intended use. Whether you need improved toughness, wear resistance, or corrosion protection, there’s a type of casting tungsten carbide that can meet your needs.
Applications
Given its exceptional properties, casting tungsten carbide is used in various industries where wear resistance, toughness, and durability are critical. From mining to manufacturing, this material is a key component in many high-stress applications.
Application | Description |
---|---|
Mining and Drilling Tools | Casting tungsten carbide is used in drilling bits, cutting tools, and wear parts in the mining industry due to its ability to withstand abrasive and high-impact conditions. |
Wear-Resistant Coatings | Often used as a coating on surfaces that experience high wear, such as pump impellers, valve seats, and nozzles, to extend the life of these components. |
Cutting Tools | Its extreme hardness and wear resistance make it ideal for cutting tools used in machining, milling, and turning applications, especially for hard materials. |
Aerospace Components | High-temperature stability and wear resistance make casting tungsten carbide a valuable material for components like turbine blades, which operate in extreme conditions. |
Oil and Gas Exploration | Used in downhole tools and other drilling equipment where abrasive forces and high pressures are common, ensuring longer operational life and reduced downtime. |
Industrial Machinery | Casting tungsten carbide is used in gears, bushings, and other machine parts that are subject to high wear, reducing the need for frequent replacements. |
Metal Forming and Stamping | The toughness and wear resistance of casting tungsten carbide make it ideal for dies and punches used in metal forming and stamping operations. |
Defense and Military Equipment | Used in armor-piercing projectiles and other military equipment that require materials capable of withstanding extreme impact forces. |
As you can see, casting tungsten carbide has a wide range of applications, making it an incredibly versatile material. Whether you’re working in mining, aerospace, or manufacturing, casting tungsten carbide offers the durability and performance you need to succeed.
Specifications, Sizes, Grades, and Industry Standards
When selecting casting tungsten carbide for your application, it’s essential to understand the specifications, sizes, grades, and industry standards that apply. This ensures you’re choosing the right material for your specific needs.
Specification | Description |
---|---|
Grain Size | Grain sizes can range from 0.5 µm (micro-grain) to 150 µm (macro-grain), with smaller grains offering higher hardness and larger grains offering better toughness. |
Purity Level | Casting tungsten carbide typically has a purity level of 94-96% tungsten, depending on the application and manufacturing process. |
Bonding Material | Common bonding materials include cobalt and nickel, which are used to enhance toughness, reduce brittleness, and improve corrosion resistance. |
Hardness (Vickers HV) | The hardness of casting tungsten carbide ranges from 2,500 to 3,500 HV, depending on the grain size and composition. |
ISO Standards | Casting tungsten carbide may adhere to standards such as ISO 513 for cutting tools and ISO 9001 for quality management in manufacturing processes. |
ASTM Standards | Standards like ASTM B777 for tungsten and ASTM F288 for aerospace applications provide guidelines on the material’s performance and quality. |
Sintering Temperature | Casting tungsten carbide is typically sintered at temperatures above 1,300°C, depending on the specific grade and application. |
Understanding these specifications ensures that the casting tungsten carbide you choose will meet the performance requirements for your application, whether you’re manufacturing cutting tools or industrial machinery.
Suppliers and Pricing
The global market for casting tungsten carbide includes a wide range of suppliers, each offering different grades, sizes, and pricing. Depending on the purity, grain size, and order volume, prices can vary significantly.
Supplier | Country | Price Per Kg (USD) | Purity Levels Available | Notable Features |
---|---|---|---|---|
Global Tungsten & Powders Corp. | United States | $800 – $1,200 | 94-96% Tungsten | Renowned supplier for high-purity casting tungsten carbide used in aerospace, oil, and gas industries. |
H.C. Starck Tungsten | Germany | $850 – $1,400 | 95-96% Tungsten | Specializes in high-grade casting tungsten carbide powders for industrial wear parts and coatings. |
Buffalo Tungsten | United States | $750 – $1,100 | 94-95% Tungsten | Competitive pricing for bulk orders, primarily serving the mining and oil industries. |
Zhuzhou Cemented Carbide Group | China | $600 – $1,000 | 94-96% Tungsten | Major supplier for mining, drilling, and wear-resistant components. |
ALMT Corp | Japan | $900 – $1,300 | 95-96% Tungsten | Focuses on high-precision casting tungsten carbide for cutting tools and aerospace components. |
Pricing for casting tungsten carbide depends on factors like grain size, purity, and bonding materials. While it may seem expensive, the exceptional performance and extended lifespan of casting tungsten carbide components often justify the higher cost.
Advantages and Limitations
Like any material, casting tungsten carbide has its strengths and weaknesses. Let’s take a look at the pros and cons to help you determine whether it’s the right material for your application.
Advantages | Limitations |
---|---|
Exceptional Hardness: It is one of the hardest materials available, making it ideal for cutting and wear-resistant applications. | High Cost: It is relatively expensive compared to other materials, which may not be suitable for all budgets. |
Superior Wear Resistance: Its ability to withstand abrasive forces makes it perfect for high-wear environments. | Brittleness: Despite its toughness, it can still be brittle in certain applications, particularly under extreme impact. |
Toughness: It offers better toughness than sintered tungsten carbide, making it more resistant to cracking and chipping. | Machining Difficulty: Due to its hardness, machining it requires specialized tools and techniques. |
High-Temperature Stability: It maintains its properties even at high temperatures, making it ideal for applications like aerospace and metalworking. | Limited Flexibility: It is rigid and not ideal for applications that require flexibility or ductility. |
While it offers unparalleled hardness and wear resistance, its high cost and machining challenges may be a consideration for certain projects. However, in applications where performance and durability are paramount, it remains one of the best materials available.
Frequently Asked Questions (FAQ)
Here are some of the most common questions people have about casting tungsten carbide.
Question | Answer |
---|---|
What is it? | It is a form of tungsten carbide produced through a casting process, offering superior toughness and wear resistance. |
How is it different from sintered tungsten carbide? | It is tougher and more impact-resistant than sintered tungsten carbide, which is generally more brittle. |
What are the primary applications? | It’s used in mining, drilling, cutting tools, wear parts, and aerospace components, where high hardness and wear resistance are essential. |
How much does it cost? | Prices typically range from $600 to $1,400 per kilogram, depending on the supplier, grain size, and purity. |
Can it be machined? | Yes, but it requires specialized tools and techniques due to its extreme hardness, making conventional machining difficult. |
Is it resistant to corrosion? | While it offers moderate corrosion resistance, additional coatings or treatments may be needed in highly corrosive environments. |
Conclusion
It represents the pinnacle of toughness, wear resistance, and durability in the world of high-performance materials. Whether you’re in mining, oil and gas, aerospace, or manufacturing, this material offers the resilience and longevity needed to withstand the most challenging conditions.
While casting tungsten carbide can be more expensive and difficult to machine compared to other materials, its benefits far outweigh these limitations in applications where performance, efficiency, and durability are critical. By selecting the right type, specification, and supplier, you can unlock the full potential of casting tungsten carbide for your project.
As industries continue to demand more from their materials, it will undoubtedly remain a key player in pushing the boundaries of what’s possible.
Get Latest Price
About Met3DP
Product Category
HOT SALE
CONTACT US
Any questions? Send us message now! We’ll serve your request with a whole team after receiving your message.
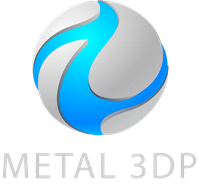
Metal Powders for 3D Printing and Additive Manufacturing